Прокатка циркониевых труб
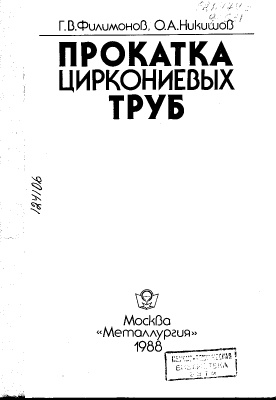
Филимонов Г.В., Никишов О.А.
Металлургия, 1988 г.
Глава II. ОБОРУДОВАНИЕ И РЕЖИМЫ ПРОКАТКИ
Технология изготовления циркониевых труб сложна и очень трудоемка. Ведутся исследовательские работы с целью определения оптимальной технологии, выяснения влияния способов обработки на свойства труб, особенно на попучение структуры. Автор работы 13] исследовал влияние многоцикличной холодной прокатки, справочного волочения, волочения через шариковую обойму и ковки труб из сплава циркалой-4 с начального размера 38X6,5 мм на конечный 15X1 мм. После каждого перехода холодной деформации трубы подвергали вакуумному отжигу. Было установлено, что вид холодной деформации влияет на характер и интенсивность структуры. Наибольшее влияние на структурную неравномерность оказывает степень обжатия по сечению и по внутреннему метру. Согласно данным работы [1], трубы между отжигами необходимо прокатывать на цилиндрических оправках с обжатием не более 50-80 % при минимальном изменении внутреннего диаметра.
Наиболее оптимальной в настоящее время является такая технология, когда основную деформацию после прессования заготовки осуществляют способом холодной прокатки [13, 16].
На заводе фирмы "Mannesmannrohren-Werke AG из слитков после ковки сверления, расточки и обточки прессуют гильзы диаметром до 60 мм которые подвергают затем многократной холодной прокатке с промежуточными отжигами. Холодную прокатку проводят на станах "ХПТ 2 1/2" и KPW25VMP фирмы "Mannesmann-Meer AG , которые оснащены кольцевыми калибрами. Короткоходовые станы KPW25 имеют до 240 двойных ходов рабочей клети в 1 мин; их производительность при подаче 2-3 мм и коэффициенте вытяжки 2,0-3,5 достигает 60—80 м/ч.
Аналогичные режимы технологии используют при производстве труб из сплавов Zr — 1 % Nb и Zr — 2,5 % Nb [16—18].
Большое внимание исследователи уделяют изысканию режимов термообработки циркониевых сплавов [19—21]. Это объясняется тем, что режимы термообработки наравне с режимами деформации, определяют механические и, следовательно, эксплуатационные свойства [22, 23]. При этом необходимо учитывать, что закалке подвергают термоупрочннемые сплавы В большинстве случаев используются промежуточные и окончательные отжиги [24]. Однако известны способы изготовления труб без окончательного отжига (в том числе и труб из высоколегированных сплавов) завершающая деформация которых не превышает 20 %,
1- Валковые станы холодной прокатки труб
Общая особенность холодной прокатки труб на станах валкового типа - возможность достижения за один проход прокатки уменьшения сечения заготовки на 75—85 %, так как в этом случае условия деформирования металла более благоприятны, чем, например, при волочении. Это обстоятельство объясняется, во-первых, тем ,что схема напряженного состояния металла близка к схеме трехосного сжатия (рис. 14) - наиболее благоприятной схеме деформации металла и, во-вторых, высоким коэффициентом дробности деформации, т.е. количеством рабочих циклов, за которое получается конечное сечение трубы. Качество поверхности и точность размеров готовых холоднокатаных труб очень высоки и отвечают жестким требованиям
В зависимости от сортамента прокатываемых труб используют станы различных типов и размеров. В табл. 3 указаны основные параметры отечественных и зарубежных станов холодной прокатки труб [26].
Схема валковой прокатки и выбор деформационных параметров
На рис. 15 приведена схема процесса прокатки труб на стане ХПТ валкового типа.
Деформация заготовки 3 осуществляется обжатием ее между калибрами 1, закрепленными в вырезах валков 2, и неподвижной конической оправкой 5, ввернутой в стержень 4. По окружности калибры имеют вырезы переменного сечения (ручьи), исходный размер которых соответствует наружному диаметру заготовки, а конечный размер — наружному диаметру готовой трубы. При помощи кривошипно-шатунного механизма рабочей клети сообщается возвратно-поступательное движение. При этом валки, установленные в клети на опорах, вращаются вокруг своих осей.
Вращение валков осуществляется при помощи насаженных на их шейки шестерен, крайние из которых на нижнем валке находятся в зацеплении с зубчатыми рейками, закрепленными на боковых стенках станины. При движении клети вперед и перекатывании при этом калибров сечение их ручьев в осевой плоскости валков постепенно уменьшается, что, естественно, приводит и к уменьшению диаметра заготовки до соответствующих размеров.
При соприкосновении внутренней поверхности заготовки с оправкой, помимо ее обжатия по диаметру, происходит деформация по стенке, так как зазор между калибрами и оправкой уменьшается по длине хода валков, При достижении клетью крайнего переднего положения деформированный участок заготовки (рабочий конус) освобождается от соприкосновения с калибрами и труба-заготовка вместе с оправкой поворачивается на определенный угол (обычно 60— 90 град). При обратном ходе клети происходит дальнейшее обжатие по диаметру и стенке, а также раскат более утолщенной части рабочего конуса, которая образуется в выпусках калибров, предусмотренных калибровкой. Очередной цикл прокатки начинается с продвижения заготовки вперед на определенную величину, называемую подачей.
Процесс холодной прокатки труб отличается от процесса продольной прокатки. При холодной периодической прокатке труб изменяются геометрические размеры очага деформации, абсолютное и относительное обжатие по ходу движения трубы.
Участок трубы, который деформируется за один цикл прокатки, называют полным очагом деформации или рабочим конусом (см. рис. 15). Объем металла, который деформируется в данный момент, называют мгновенным очагом деформации. Размеры мгновенного очага деформации меняются по ходу движения рабочей клети.
Во время подачи заготовки внутренняя поверхность рабочего конуса отходит от оправки, образуя зазор. При повороте калибров происходит редуцирование рабочего конуса до соприкосновения его внутренней поверхности с оправкой, после чего обжатие по диаметру сопровождается обжатием по стенке.
Центральные углы, ограничивающие участки редуцирования и обжатия, называются соответственно углом редуцирования и углом обжатия; в сумме они образуют угол захвата. Величина угла захвата меняется по ходу движения рабочей клети, при этом изменяется и величина мгновенного очага деформации.
При прокатке труб на станах ХПТ необходимо учитывать ряд факторов, от которых зависит качество готовых труб, стабильность процесса прокатки и условия работы оборудования [26].
Применительно к сплавам циркония наиболее важными из этих факторов являются следующие:
- установление допустимых и оптимальных степеней деформации за один проход;
- выбор смазок и покрытий;
- выбор допустимых скоростей движения рабочей клети стана и подач металла;
- рациональная калибровка рабочего инструмента.
Как указано выше, при прокатке труб из чистого циркония на станах ХПТ достигались деформации до 85 % за один проход без ухудшения качества готовых труб [27]. Авторы этой работы установили, что суммарное содержание легирующих элементов — олова, железа, никеля, ниобия до 1,5 % не оказывает существенного влияния на величину Максимального обжатия. Для сплавов с более высоким содержанием легирующих элементов целесообразно несколько снижать суммарное обжатие между промежуточными отжигами.