Прокаливаемость стали
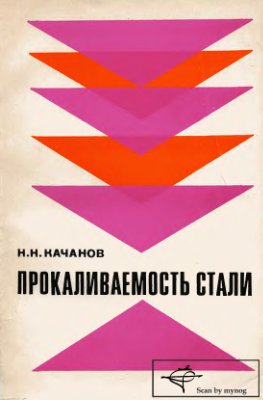
Качанов Н.Н.
Металлургия, 1978 г.
ФАКТОРЫ, ВЛИЯЮЩИЕ НА ПРОКАЛИВАЕМОСТЬ
Накопленные к настоящему времени данные свидетельствуют о том, что на прокаливаемость стали оказывают влияние следующие факторы: химический состав стали; величина зерна аустенита; скорость кристаллизации стали; условия прокатки стали;
исходная структура; условия термической обработки (температура нагрева, продолжительность, условия охлаждения — природа охлаждающей среды и скорость ее перемешивания), химическая микронеоднородность твердого раствора, определяемая дендритной ликвацией, внутренней адсорбцией в твердых растворах, характером взаимодействия растворенных атомов между собой, процессом образования и растворения карбидной фазы и присутствующими в сталях несовершенствами кристаллической решетки.
ХИМИЧЕСКИЙ СОСТАВ. Прокаливаемость стали при переходе от марки к марке меняется. Однако эффективность влияния того или иного элемента на прокаливаемость определяется природой других элементов, присутствующих в данной стали. С этой точки зрения, по-видимому, нельзя признать, что химический состав конструкционных сталей во всех случаях строго обоснован, поэтому работы в данном направлении следует считать необходимыми.
Влияние химического состава в пределах марки стали проявляется, как правило, слабо, а в отдельных случаях вообще не проявляется. Выше приводились примеры, когда плавки стали, менее легированные, имели прокаливаемость более глубокую, чем плавки той же стали, но более легированные. Очевидно, в этих случаях действовали другие, более сильные факторы, которые затушевывали влияние колебаний химического состава, а в ряде случаев просто перекрывали его.
ВЕЛИЧИНА ЗЕРНА АУСТЕНИТА. Применяемые в настоящее время конструкционные стали, как правило, мелкозернистые. При этом колебания величины зерна не превосходят двух (редко трех) баллов. Эти колебания практически не оказывают заметного влияния на прокаливаемость.
СКОРОСТЬ КРИСТАЛЛИЗАЦИИ. Как показано выше, этот фактор оказывает влияние на прокаливаемость. Однако это влияние проявляется через химическую микронеоднородность ликвационного происхождения. Поэтому роль скорости кристаллизации стали будет рассматриваться при обсуждении роли химической микронеоднородности твердого раствора. Одновременно будет рассмотрена также роль прокатки стали и в особенности роль условий охлаждения после окончания прокатки стали.
УСЛОВИЯ ТЕРМИЧЕСКОЙ ОБРАБОТКИ. Рассматривая вопрос о роли условий термической обработки на прокаливаемость стали, следует иметь в виду два момента: 1) температуру и продолжительность нагрева; 2) скорость охлаждения.
С повышением температуры нагрева под закалку и увеличением продолжительности выдержки прокаливаемость стали, как правило, увеличивается, хотя и неравномерно для различных плавок одной и той же стали.
Однако повышение температуры и удлинение выдержки ограничиваются опасностью получения крупноигольчатого мартенсита, что отрицательно сказывается на свойствах термически обработанной стали. Поэтому для каждой стали всегда определяют оптимальные температуры закалки и длительности нагрева.
Необходимо, однако, отметить следующее. Выбор строго постоянной температуры закалки для всех плавок стали той или иной марки нельзя считать строго оправданным. Нежелательно использование плавок, расположенных у левой границы полосы прокаливаемости, из-за их недостаточной прокаливаемости, а плавок, расположенных у правой границы этой полосы, — из-за того, что сталь этих плавок более склонна к образованию трещин при закалке.
Указанные явления, по нашему мнению, объясняются следующим.
Все плавки одной стали независимо от их фактической прокаливаемости подвергают закалке с одной температуры. В этих условиях плавки с пониженной прокаливаемостью заведомо несколько недогревают, а плавки с повышенной прокаливаемостью несколько перегревают, что естественно привести к образованию трещин при закалке.
Было бы более целесообразно плавки с пониженной прокаливаемостью подвергать закалке с температуры, превышающей принятую для данной марки, а плавки с повышенной прокаливаемостью — с более низкой температуры.
Схематически это показано на рис. 96 для стали 40ХГМ. Линия а—а отвечает температуре закалки, принятой для стали марки 40ХГМ, линия b—Ь характеризует более правильное изменение температуры закалки в зависимости от фактической прокаливаемости стали плавок, включенных в полосу. Разумеется, пределы колебания температуры закалки должны устанавливаться экспериментально. Для этого сталь должна проходить поплавочный контроль прокаливаемости.
Практика и приведенные выше данные показывают, что закалочная среда и скорость ее перемешивания оказывают значительное влияние на глубину закалки деталей.
На выбор закалочной среды в основном влияют величина изменения* линейных размеров при закалке, величина остаточных напряжений и склонность стали к трещинообразованию. В свою очередь закалочная среда определенным образом обусловливает выбор стали.
Углеродистые стали при сечениях более 12,0—13,0 мм, как правило, закаливают в воде. По этой причине из них чаще всего изготовляют детали, для которых допустимы достаточно большие изменения размеров и которые можно закаливать с большими
Таким образом, для управления прокаливаемостью необходим выбор оптимальной степени обжатия.
Как уже отмечалось, прокаливаемость высокоуглеродистой стали заметно повышается при применении непрерывной разливки. Можно полагать, что непрерывная разливка повысит прокаливаемость также конструкционных сталей. Поэтому целесообразно создание оптимальной технологии непрерывной разливки сталей различных марок.
Заслуживает внимания и разработка оптимальных режимов гомогенизации стали в процессе прокатки. Это позволит существенно повысить не только прокаливаемость стали, но, что не менее важно, ее контактную и, по-видимому, усталостную прочность.
Большое значение для управления прокаливаемостью имеет также дальнейшее развитие работ по комплексному легированию сталей.
ИСХОДНАЯ СТРУКТУРА.Одним из важных факторов, определяющих прокаливаемость, является структурное состояние стали . перед закалкой, в частности дисперсность карбидной фазы.
Существующая точка зрения, согласно которой прокаливаемость тем глубже, чем дисперснее карбидная фаза, должна быть серьезно скорректирована. Для подшипниковых сталей ШХ15 и ШХ15СГ существует оптимальная дисперсность карбидной фазы, при которой обеспечивается максимальная прокаливаемость. Можно полагать, что и для сталей других марок справедливо это положение. Для подтверждения его необходимы дальнейшие эксперименты.
Желательно установление единых оптимальных режимов отжига стали, поскольку, как показывает опыт, они весьма существенно различаются (даже при термической обработке стали одной марки на разных заводах).
Из приведенных выше данных об экономике прокаливаемости вытекает значение такого мероприятия, как нормирование прокаливаемости стали всех марок. Оно позволит добиться стабильности технологии термической обработки стальных деталей, исключить брак по неполной закалке, повысить долговечность и надежность изделий.