Производство точного проката
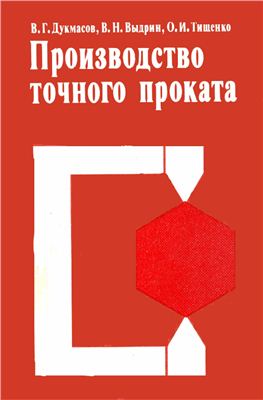
Дукмасов В.Г., Выдрин В.Н., Тищенко О.И.
Металлургия, 1990 г.
Глава 1. ТЕХНОЛОГИЯ И ОБОРУДОВАНИЕ ДЛЯ ПРОИЗВОДСТВА ТОЧНОГО ПРОКАТА
- ПУТИ ПОВЫШЕНИЯ ТОЧНОСТИ ПРОКАТА И ИХ ЭФФЕКТИВНОСТЬ
Повышение точности проката на действующих станах достигается стабилизацией температуры полос, рационализацией калибровки и режима обжатий, более качественной обработкой валков, применением роликовой арматуры. На непрерывных станах с ручным управлением скоростным режимом валков можно поднять точность проката более тщательной настройкой стана и постоянным контролем этой настройки. В отечественном прокатном производстве перечисленные мероприятия позволили на многих станах поднять точность прокатки и организовать сдачу металла по теоретической массе [1 - 4].
Дальнейшее повышение точности проката возможно только путем применения более совершенных рабочих клетей и станов; применения систем регулирования толщины, профиля, натяжения и средств контроля размеров полосы; использования новых технологических процессов.
Совершенствование рабочих клетей позволяет существенно уменьшить разнотолщинность полос за счет увеличения радиальной и осевой жесткости рабочей клети. Заметно уменьшается искажение формы сортовых профилей при снижении величины осевых люфтов рабочих валков. Увеличение жесткости рабочей клети отрицательно сказывается на разнотолщинности полос при использовании валков с радиальным и торцевым биением ручьев валков. Чрезмерное увеличение жесткости рабочей клети неэффективно и приводит к усложнению рабочей клети и снижению ее эксплуатационных показателей.
Системы регулирования толщины полосы, профиля, натяжения и средств контроля размеров полосы позволяют управлять процессом формирования профиля, полосы и достигать наивысших показателей по точности размеров и форме. На непрерывных сортовых станах применяются только система регулирования натяжения полосы и средства контроля размеров ее профиля. Все современные листовые станы оснащены автоматическими системами регулирования толщины, профиля, натяжения и средствами контроля размеров полосы. Применение систем регулирования и контроля наиболее эффективно в сочетании с совершенной конструкцией рабочей клети и прокатного стана.
Для повышения точности сортового проката авторами этой работы предложен [5] новый технологический процесс, получивший название - процесс горячего калибрования. Горячее калибрование выполняется в потоке стана в дополнительной клети или в блоке клетей, содержащих специальную валковую систему. В настоящее время горячее калибрование осуществляется путем применения калибрующей клети с четырехвалковым калибром, калибрующего блока с двумя двухвалковыми калибрами, смещенными по оси прокатки на малое расстояние, или калибрующего блока с тремя трехвалковыми калибрами.
Все схемы горячего калибрования (рис. 1) предусматривают относительное обжатие не более 10 %. Сравнение различных схем горячего калибрования в равных условиях показывает, что наивысшей точностью обладает процесс горячего калибрования в четырехвалковом калибре. Это объясняется почти полным отсутствием уширения по разъемам четырехвалкового калибра. Можно рекомендовать горячее калибрование в четырехвалковом калибре особенно плоских профи-, лей, например, для получения особоточной рессорной стали. Далее следует горячее калибрование в трехвалковых калибрах. Особенно эффективно горячее калибрование шестигранной стали в трехвалковых калибрах. Уширение в двухвалковых калибрах больше, чем в многовалковых калибрах, поэтому горячее калибрование в двухвалковых калибрах обладает меньшей точностью.
1.2. ЗАРУБЕЖНЫЕ СТАНЫ ДЛЯ ПРОИЗВОДСТВА ТОЧНОГО ПРОКАТА
В зарубежном прокатном производстве в последние годы проводятся реконструкции действующих станов с целью их совершенствования. Рассмотрим наиболее интересные примеры.
Фирма «SMS Schloemann - Siemag AG» (ФРГ) модернизировала проволочный стан на заводе фирмы "ARBED Saarstakl" в Neuhrirchen [39]. Стан из трехниточного превращен в однониточный. В черновой и! промежуточных группах увеличено количество клетей. Заготовки; увеличены до квадрата 150 х 150 мм. В чистовой группе установлен десятиклетевой блок с консольными валками. Применение блока обеспечило получение катанки с отклонениями ± 0,2 мм и лучшей поверхностью. Применено охлаждение катанки водой и воздухом на линии типа Стелмор. На стане прокатывают катанку из углеродистых, шарикоподшипниковых, нержавеющей и жаропрочных сталей диам. 5,5 мм со скоростью 100 - ПО м/с. Достигнута скорость 114 м/с, при проектной - 120 м/с. Также фирма реконструировала трехниточный
проволочный стан на заводе Schifflingen фирмы "Arbed - Esch" (Люксембург), превратив его в двухниточный [40]. Характер реконструкции подобен предыдущему стану. Скорость прокатки увеличена с 36 до 100 м/с. После реконструкции на стане прокатывают катанку из углеродистых, подшипниковых и пружинных сталей с узкими допусками и с высоким качеством поверхности и структуры металла.
Двухниточный проволочный стан фирмы "Morgan Conctruction" введен в эксплуатацию в 1980 г. на заводе фирмы "Raritan river SteeV в Перт-Эмбое, США [41]. На этом стане, впервые в США, применено сочетание предчистовых клетей с консольными валками, десятиклете-вых блоков и системы регулируемого охлаждения Стелмор. Стан предназначен для прокатки катанки диам. 5,5 - 13,1 мм из углеродистых и низколегированных сталей в мотки массой до 2000 кг. Проектная скорость прокатки составляет 76 м/с, привод позволяет повысить ее до 93 м/с. Каждая предчистовая группа включает четыре клети с консольными валками диам. 240 мм. Горизонтальные и вертикальные клети имеют индивидуальный привод валков. Вертикальные петле-образователи между клетями обеспечивают прокатку без натяжения полосы. Каждый чистовой блок содержит десять пар консольных валков, расположенных под углом 45° к оси прокатки. Чистовые блоки оснащены роликовыми проводками с оптической центровкой по оси прокатки [42].
На заводе Siegen фирмы "Krupp Siidwestfalen" (ФРГ) к имевшемуся мелкосортному стану добавили чистовую линию, предназначенную для прокатки прутков 15 - 55 мм из легированных и специальных сталей. Бывшие в эксплуатации черновая линия с клетью трио 580 и промежуточная линия 430 остались без изменений [43].
Чистовая линия содержит семиклетевую группу 500, семиклетевую группу 370 и калибрующий блок 370 с тремя клетями. Все клети чистовой линии имеют трехвалковые калибры. Между группами 500 и 370 установлен вертикальный петлеобразователь. Первые пять клетей в группах 500 и 370 имеют групповой привод от электродвигателя постоянного тока, а две последние клети в каждой группе имеют индивидуальный привод постоянного тока. Все три клети калибрующего блока 370 приводятся от группового привода постоянного тока, две последние клети снабжены обгонными муфтами. Замена клетей чистовой линии полностью механизирована.
Валки клетей изготовлены в виде колец из легированного чугуна. Переточка валков осуществляется без разборки клети на вальцетокарных станках. Переточка валков и подготовка клетей к прокатке осуществляется в мастерской, расположенной в соседнем пролете. Стан имеет управляющую ЭВМ. Достигнута скорость прокатки 19 м/с. Использование трехвалковых калибров, обладающих известными преимуществами перед двухвалковыми калибрами, и применение калибрующего блока с обжатиями 2 - 11 % позволили получить прутки диаметром 15-55 мм с отклонениями диаметра не более ± 0,2 мм.
Приведем несколько примеров производства точного листового проката.
На заводе бразильской фирмы "ЮЗИМИНАС" введен в эксплуатацию современный толстолистовой прокатный стан с электрогидравлической САРТ. В четырехвалковой клети 4100 диаметр рабочих валков 1100, опорных 2000 мм, допустимое усилие прокатки 70 мн. В сортамент стана входят листы толщиной 4,5 - 150 мм при ширине 900 - 3900 мм и максимальной длине 25 мм. Максимальные отклонения толщины по всему сортаменту проката составили ± 0,05 мм [44].
На толстолистовом стане 5530 фирмы "Jshikawajima Harima Heavy Industries Co., Япония в четырехвалковой клети с рабочими валками диаметром 1200, опорными 2400 мм установлена электрогидравлическая САРТ. Максимальное усилие прокатки 90 МН.
Сервоклапаны системы обеспечивают высокую чувствительность и быстроту срабатывания до 25 Гц [45].
Электрогидравлическая САРТ, установленная на действующем толстолистовом стане 2800 завода Burns Harbon Plant фирмы Bethlehem Steel Corporeishen (США) позволила более чем в два раза повысить точность прокатки листов [46].
Фирма "Britich Steel Corp." установила электрогидравлическую САРТ полосы на трех станах холодной прокатки углеродистых сталей на заводе Whitehead. Применение новой системы позволило на 10 % увеличить производительность, в два раза снизить продольную раз-нотолщинность на 98 % длины полосы, увеличить скорость прокатки и снизить расход валков на 10 % [47].
На заводе "Kakogawa Works, Япония, на пятиклетевом стане холодной прокатки установлена САРТ полосы, действующая на всех режимах работы стана. Стан прокатывает полосы толщиной 0,15 - 3,2, шириной 600 - 1600 мм в рулонах массой до 50 т. Для управления станом установлены две ЭВМ, которые связаны с центральной ЭВМ. Информация о процессе прокатки поступает с датчиков натяжения, установленных между клетями и между пятой клетью и моталкой, двух рентгеновских толщиномеров, один из которых установлен между второй и третьей клетями, а второй - между пятой клетью и моталкой. Система позволяет устранить разнотолщинность полос, вызванную эксцентриситетом валков [48].
На действующем пятиклетевом стане холодной прокатки низкоуглеродистых сталей толщиной 0,2 - 2,3 мм установлена САРТ полосы с компенсацией эксцентриситета опорных валков. Для компенсации эксцентриситета измеряется биение сведенных при нагрузке валков.
Сигнал биения запоминается и при прокатке вычитается из сигнала усилия прокатки в соответствии с алгоритмом. Использование компенсации эксцентриситета валков снизило разнотолщинность полос толщиной 0,4 - 0,9 мм на 42 - 23 % [49].
В Японии на заводе Нагая фирмы "Синниппон сэйтцу" на пятиклетевом непрерывном стане холодной прокатки установлена система компенсации биения опорных валков. Работа системы основана на выделении в спектре сигналов измерителей усилия прокатки первой и второй клетей составляющих, связанных с биением валков.
Эффективность системы компесации эксцентриситета в первой клети выше, чем в пятой клети. В первой клети разнотолщинность полосы снижается с 50 до 5 мк [50].