Производство сортовой стали
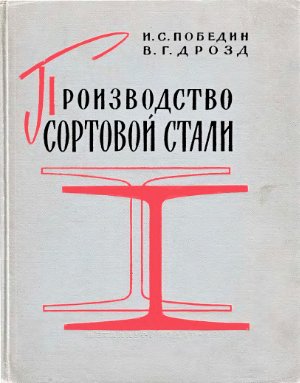
Победин И.С., Дрозд В.Г.
Металлургиздат, 1961 г.
РЕЛЬСОБАЛОЧНЫЕ СТАНЫ ТРИО 800
Схема расположения оборудования стана, изготовленного УЗТМ и установленного на заводе 2, приведена на рис. 9.
Для нагрева заготовок на этом стане используются методические и камерные печи. Более же современным решением печного хозяйства рельсобалочного стана такого типа является установка только методических печей.
Горячие блюмы (700°) от ножниц впереди стоящего блюминга по рольгангам поступают в пролет камерных печей.
С транспортного рольганга блюмы передаются на приемную тележку, встроенную в подводящий рольганг обжимной клети, и с ее помощью подаются к подогревательным камерным печам. Загрузка и выгрузка блюмов производится с помощью шарнирного крана.
Холодные блюмы подаются к методическим печам для нагрева до 600—700° и затем передаются для окончательного нагрева в камерные печи указанным выше способом.
Нагретые до 1150—1180° блюмы вынимаются шарнирным краном, укладываются на ,приемную тележку и транспортируются к подводящему рольгангу обжимной клети.
Дуо-реверсивная обжимная клеть оборудована манипуляторами с обеих сторон и кантователем крюкового типа с передней стороны. Скорость передвижения линеек около 1 м/сек. Ход линеек 2500 мм, скорость кантователя 0,5 м/сек. В обжимной клети обычно число проходов достигает 5—7, затем раскат поступает на вторую линию, состоящую из двух клетей трио и чистовой дуо.
Каждая клеть трио оборудована с обеих сторон подъемно-качающимися столами длиной 12 м. С передней и задней сторон подъемные столы снабжены роликовыми манипуляторами-кантователями. Передача металла от одной клети к другой осуществляется шлепперами.
Общее количество проходов при прокатке различных профилей во всех клетях, включая обжимную, составляет 12—16.
Характеристика этого стана приведена в табл. 2. Технико-экономические показатели этого и других станов см. в табл. 29 (стр. 89).
Из общего количества металла, прокатываемого на этом стане, доля фасонных профилей превышает 50% (балки и швеллеры около 20%, железнодорожные рельсы свыше 30%).
Из чистовой клети прокатанная полоса поступает к салазковым пилам горячей резки (всего имеется шесть пил), где производится порезка на мерные длины. Диаметр диска пилы 1600 мм, толщина 7 мм, окружная скорость диска 100 м/сек. После порезки прокат поступает в отделение отделки.
По сложности и трудоемкости отделки вся продукция стана может быть разделена на три группы:
а) железнодорожные рельсы,
б) балки, швеллеры и другая фасонная сталь,
в) круглые и квадратные профили.
Железнодорожные рельсы после порезки на
пилах горячей резки на мерные длины и горячего клеймения на штемпельной машине подаются на промежуточный холодильник, где охлаждаются до 550—600°. Далее рельсы поступают в печи изотермической выдержки, где выдерживаются при этой температуре в течение двух часов (для предотвращения образования флокенов). Посадка и выдача рельсов ведется поточным методом, т. е. через определенные промежутки времени подается и одновременно выдается по пять-шесть рельсов. Это позволяет получать достаточно идентичные результаты изотермической выдержки, а также обеспечивает равномерную загрузку всего вспомогательного оборудования. Затем рельсы поступают на центральный холодильник, где охлаждаются до 50—60°. На холодильнике производится проверка длин рельсов, торцы коротких рельсов окрашивают краской.
С холодильника рельсы подаются для правки на роликоправильные машины (№ 1 и № 2), при этом подача рельсов новой плавки производится только после окончания правки и уборки со стеллажей за роликоправильными машинами рельсов предыдущей плавки.
Затем рельсы подвергают дополнительной правке, главным образом концы на вертикальных правильных прессах.
После правки короткие рельсы передаются на специальный стеллаж, а основной поток направляется к автоматическим поточным линиям, рельсоотделки. Здесь при помощи канатных шлепперов рельсы укладываются на стеллажи на расстоянии 300 мм друг от друга и далее с помощью клинкеншлепперов — на линию центрователей, которые устанавливают рельс так, чтобы с обеих сторон рельса получить одинаковый припуск на фрезеровку торцов.
Далее с помощью клинкеншлепперов рельсы последовательно подаются к фрезерным станкам, к сверлильным станкам и закалочным кабинам; при этом шлепперы автоматически увеличивают расстояние между рельсами с 300 до 500 мм.
У фрезерного станка рельс автоматически зажимается гидравлическими зажимами и фрезеруется одновременно с обоих концов. При автоматическом возврате зажима в начальное положение происходит передвижение шлеппера на один шаг вперед, рельс автоматически приподнимается над стеллажами подъемниками и гидравлическими вталкивателями подается к сверлильным станкам. Затем рельс зажимается прижимами и в нем просверливают отверстия. После сверления рельсы подаются к закалочным кабинам. Головки рельса длиной до 150 мм подвергают закалке токами высокой частоты.
При отделке рельсов длиной 12,5 м в работе находятся все станки, расположенные в два ряда на каждой отделочной линии, при отделке рельсов длиной 25 м средние станки убираются, а станки крайних рядов сдвигаются на 2 м с каждой стороны и устанавливаются на заранее подготовленные плиты.
В дальнейшем рельсы передаются на инспекторские стеллажи, а после приемки инспектором МПС — на склад.
Балки после порезки на пилах горячей резки поступают на центральный холодильник. Затем после охлаждения проходят правку на роликоправильной машине (№ 3) и поступают в пролет отделки, где в поточных линиях проходят дополнительную правку на горизонтальных правильных прессах, резку на пиле холодной резки и далее поступают на склад готовой продукции.
В основном по этой же схеме отделку проходят и другие фасонные и простые профили.
По степени механизации и автоматизации, а также достигнутой производительности этот стан является одним из лучших современных рельсобалочных станов.
На рис. 10 приведена схема современного рельсобалочного стана трио завода 3 с расположением основного оборудования в две линии.
Характеристика этого стана приведена в табл. 2.
Характерной особенностью технологического процесса изготовления рельсов на этом стане является применение колодцев замедленного охлаждения вместо печей изотермического отжига. Применение колодцев удешевляет себестоимость рельсов..
Всего имеется 16 колодцев шириной 4,4 м, длиной 29,1 м и объемом 161,5 м2, каждый. Максимальная емкость одного колодца около 180 т.
Колодцы рассчитаны на охлаждение рельсов длиной до 25 м. При охлаждении рельсов длиной 12,5 м в середине колодца устанавливаются съемные перегородки.
Загрузка и выгрузка производится с помощью электромагнитных мостовых кранов. Горячие рельсы краном подают с разгрузочной части холодильника и рядами укладывают в колодцы. Каждый ряд рельсов по длине разделяется 3—4 немагнитными полосами толщиной примерно 40 мм. Эти полосы создают проходы для циркуляции воздуха и не позволяют электромагниту захватывать при разгрузке колодцев более одного ряда рельсов. По ширине колодца укладывается 10 рельсов, по высоте — 12 рядов. Колодцы закрывают крышками.
Замедленное охлаждение длится 7—8 час. Затем крышки снимают и рельсы охлаждаются еще один час.
Далее рельсы передают на загрузочную часть холодильника, правят на роликоправильной машине № 1 и передают для отделки. Здесь рельсы проходят доправку, фрезеровку торцов, сверление отверстий и закалку концов с помощью токов высокой частоты.
Время нагрева головки под закалку на длину 75 мм до температуры 850—900° составляет 43—45 сек. Закалка производится конденсированной водой, температура которой 45—50°.
КРУПНОСОРТНЫЙ СТАН 650
Схема расположения оборудования этого стана, созданного ЭЗТМ при участии Гипромеза и ВНИИМЕТМАШ, приведена на рис. 11.
Исходной заготовкой для прокатки являются блюмы, подача которых на загрузочные решетки осуществляется мостовыми кранами.
С загрузочной решетки блюмы сталкиваются на подводящий рольганг печи. Конструкция загрузочной решетки предусматривает возможность сталкивания на рольганг одного, двух, либо пачки блюмов. Кроме этого, предусмотрена возможность кантовки блюмов: Последняя необходима для облегчения транспортировки их, если заусенец, образующийся при резке блюмов на ножницах, находится с нижней стороны, а также во избежание выпучивания прямоугольных блюмов при проталкивании их в нагревательной печи. При проталкивании садки прямоугольных блюмов необходимо хотя бы через один ставить блюмы на меньшую сторону.
Нагрев блюмов осуществляется в трех методических рекуперативных печах (подогревается воздух) шириной 6,7 м и длиной 2.6 м каждая. Производительность одной печи при холодном всаде 60 т/час.
После нагрева блюмы подают к обжимной дуо-реверсивной клети 800. Получаемая в этой клети за 5—7 проходов заготовка подается на вторую линию стана, состоящую из трех клетей 650. Первые две клети — трехвалковые, чистовая — двухвалковая. В зависимости от профиля прокатку на второй линии ведут в 7—9 проходов (в чистовой клети дается один проход).
Обжимная клеть оборудована манипуляторами с передней и задней стороны и кантователем с передней стороны. Каждая линейка перемещается с регулируемой скоростью от 0,6 до 1,2 м/сек, мощность электродвигателя линейки 100 кет.
Трехвалковые клети оборудованы с обеих сторон качающимися столами, шлепперами для передачи раската от клети к клети, исчезающими кантователями клещевого типа и вильчатыми манипуляторами с гидравлическими приводами. Для поперечного перемещения манипуляторов и кантователей применены реечные устройства. Перед чистовой клетью установлена кантующая шайба.
Все валки имеют текстолитовые подшипники-с водяным охлаждением. Перевалка на чистовой линии производится клетями. Готовые полосы разрезаются на мерные длины на пилах горячей резки и передаются на холодильник.
Характеристика стана приведена в табл. 3.
Стан оборудован шестью передвижными пилами для горячей резки прокатанного металла с диаметром 1800 мм и толщиной 10 мм при окружной скорости 100 м/сек.
Кроме этого, за обжимной клетью установлена еще одна такая пила, которая используется для делительной резки при прокатке малых сечений. Установка этой пилы вызвана малым расстоянием между обжимной и первой черновой клетями.
За пилами горячей резки установлены две клеймовочные машины, работающие по принципу катящегося диска с выступающими цифрами.