Производство рельсов на Кузнецком металлургическом комбинате
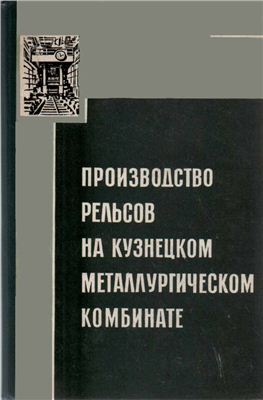
Михайлец Н.С., Горелкина А.Е., Кошкин В.А., Никулин Н.Г., Дарушин Р.А., Сахарова Н.А., Лымарь А.И., Лоскутова Л.В., Руднева Р.С.
Металлургия, 1964 г.
РЕЛЬСЫ ИЗ ЛЕГИРОВАННОЙ И СПЕЦИАЛЬНОЙ СТАЛИ
Элементы, применяемые для легирования рельсовой стали, должны быть доступными и дешевыми. Такими элементами являются хром, марганец и кремний. Химический состав легированной стали должен обеспечить высокую прочность, упругость и ударную вязкость при нормальных и низких температурах. В то же время сталь должна обладать высоким сопротивлением истиранию и смятию, а также высокой прокаливаемостью, чтобы повышенная прочность металла после термической обработки распространялась на значительную глубину под поверхностью катания рельсов. Состав, стали должен быть близким к принятым в промышленности маркам конструкционных сталей, свойства которых достаточно изучены. Однако от существующих марок конструкционных сталей рельсовая легированная сталь будет отличаться повышенным содержанием углерода, без чего невозможно получить высокое сопротивление истиранию и смятию (табл. 52).
1. ХРОМИСТЫЕ РЕЛЬСЫ
Рельсы прокатывали из стали, содержащей 1—3%% Сr (см. табл. 52).
Технология «производства рельсов Р-65 из стали, содержащей 0,56—0,92% Сr, не отличается особыми затруднениями. Продолжительность выплавки в 400-т мартеновских печах увеличилась на 1 час. 15 мин. (по сравнению с плавками углеродистой стали), продолжительность нагрева слитков в колодцах — на 25 мин. (вследствие медленного нагрева в первом периоде). Замедленное охлаждение в коробах в течение 10 час. (вместо 8 час. для углеродистых рельсов) гарантировало отсутствие флокенов.
Механические свойства хромистой стали с содержанием 1 % Сr после замедленного охлаждения несколько выше, чем углеродистой (см. табл. 52): предел прочности на 7%, предел текучести на 9%, твердость на 20ΗΒ. Ударная вязкость оказалась такой же, как и для углеродистой стали; при понижении температуры испытания она плавно уменьшается с 1,63 кГм/см2 при +20° С до 0,9 кГм/см2 при —60° С.
Рельсовая сталь с содержанием 0,56—0,92% Сr при вылеживании стареет, увеличивая пластические свойства. После выдержки 8—23 дня относительное удлинение увеличивается в < 1,5 раза, а сужение сечения примерно в два раза.
Таким образом, хромистая рельсовая сталь с содержанием 1%Сr, не подвергнутая термической обработке, обладает лишь несколько лучшими свойствами, чем углеродистая.
Для получения рельсов, обладающих более высокими свойствами без термической обработки, была использована сталь, содержащая 2—3% Сr. Образование в ней достаточно твердого кубического карбида хрома придает ей высокую износоустойчивость. Необходимая твердость и сорбитная структура могут быть получены по всему сечению головки рельса простым охлаждением на воздухе.
Сталь, содержащую 2 и 3% Сr, выплавляли в мартеновских печах емкостью 30 и 185 т. Изготовление рельсов из этой стали сопровождалось рядом затруднений. Особенно трудоемкими и требующими специального оборудования оказались операции отделки.
Замедленное охлаждение в коробах (в час.) проводили с 360°С. При более высоких температурах рельсы нельзя было загрузить в короба, так как сталь не обладала магнитными свойствами.
Поверхность слитков и готовых рельсов имела много плен и трещин. Рельсы были очень чувствительны к неравномерному охлаждению и еще до укладки в короба имели коробление не только в вертикальной, но и в горизонтальной плоскостях.
Рельсы после замедленного охлаждения были очень прочными и твердыми (400—410Я5). Даже после отпуска при 300° С в течение 8 час. -их не удавалось выправить в роликолравильной машине. Дополнительную правку производили .на штемпельных прессах. Выход первого сорта составил только 22%.
Сталь обладает высокой прочностью и достаточной пластичностью, кроме стали плавки, содержащей 3,38% Сr, у которой пластические свойства были очень низкими. После отпуска при 600° С сталь этой .плавки приобрела следующие свойства: предел текучести 69—73 кГ/мм2, предел прочности 94—96 кГ/мм2, относительиое удлинение 10—11%, сужение сечения 57—59% и твердость 300HB.
Ударная вязкость рельсовой стали с содержанием 2—3% Сг не отличается от ударной вязкости углеродистой.
2. ХРОМОНИКЕЛЕВЫЕ РЕЛЬСЫ
В 30-т мартеновской печи была выплавлена сталь, содержащая 0,31% Сr и 0,34% Ni. Небольшое содержание легирующих не вызывало затруднений в. технологии производства и позволяло рассчитывать на улучшение служебных свойств рельсов без термической обработки.
Вторая опытная партия хромоникелевых рельсов была прокатана из стали Орско-Халиловекого комбината. Сталь выплавляли в мартеновских печах из природнолегированного чугуна, но с добавками хрома и никеля для получения более высоких механических свойств .
Выплавка, прокатка и отделка рельсов из такой стали не вызывает никаких затруднений. Хромоникелевая сталь обладает повышенной флокеночувствительностью. Флокены были обнаружены во всех пробах, отрезанных при резке полос на мерные длины. Замедленное охлаждение в коробах (проводили по более мягкому режиму (10 час); ни в одной из проб после охлаждения в коробах флокены не были обнаружены.
Плены и трещины снизили выход рельсов первого сорта примерно до 80%.
Прочностные свойства хромоникелевой стали, не подвергнутой термической обработке, незначительно отличаются от свойств углеродистой стали. Пластические свойства и ударная вязкость выше примерно в 1,5 раза. По предварительным результатам, служебные свойства рельсов из хромоникелевой стали значительно лучше свойств из углеродистой стали. При этом одинаково хорошо служат рельсы как из стали с небольшими добавками легирующих, так и из стали Орско-Халиловокого комбината.
3. КРЕМНИСТЫЕ РЕЛЬСЫ
Увеличение содержания кремния в углеродистой стали повышает прочность и упругость феррита и улучшает стойкость рельсов против контактных разрушений. Это было подтверждено испытаниями рельсов на машине с катящейся нагрузкой и при эксплуатации их.
Сталь для опытных «партий рельсов, содержащую 0,45— 0,65% Si, выплавляли в 400-т мартеновских печах. Нагрев, прокатку и отделку рельсов проводили по технологии, принятой для углеродистой стали.
Испытания показали, что механические свойства кремнистой стали мало отличаются от свойств углеродистой стали.
4. СРЕДНЕМАРГАНЦОВИСТЫЕ РЕЛЬСЫ
Опытные рельсы, изготовленные из среднемарганцовистой (1,54% Μn) и кремлемаргандовистой (1,34% Μn и 0,52% Si) стали, по механическим свойствам не отличаются от обычных углеродистых рельсов.
Среднемарганцовистая сталь и хромистая с содержанием 1% Сг обладали магнитными свойствами при температуре загрузки рельсов в короба замедленного охлаждения. В остальных марках легированных сталей наблюдалось понижение критических точек магнитных превращений при охлаждении. Это вынуждало охлаждать рельсы перед загрузкой в короба до более низких температур, что увеличивало их кривизну и затрудняло как загрузку в короба, так и правку на роликоправйльных машинах.
Кроме опытных партий, была изготовлена большая промышленная партия рельсов из стали, содержащей 0,47—0,60% С 0,95—1,25% Μn, 0,07—0,25% Si, 0,06% S и 0,05% Р. Механические свойства этой стали были следующими: предел текучести 41—57 кГ/мм2 предел прочности 73—85 кГ/мм2, относительное удлинение 14—19%; сужение сечения 17—34%; стрела прогиба при копровых испытаниях 59—78 мм.
Эта сталь отличалась от всех остальных небольшим изменением пластических свойств при естественном старении. После выдержки образцов в течение двух месяцев относительное удлинение практически не изменилось,, а сужение сечения увеличилось только в 1,5 раза (в среднем с 24 до 36%).
5. ВЫСОКОМАРГАНЦОВИСТЫЕ РЕЛЬСЫ
Сталь марки Г13 выплавляли в 12-т электропечи (переплав высокомарганцовистого скрапа) и разливали в слитки весом 1,3 и 6 т [356]. Для повышения пластичности литой стали слитки ее перед прокаткой были подвергнуты гомогенизирующему отжигу (1050—1100° С) дли растворения карбидов.
Нагрев и прокатка слитков были сопряжены с большими затруднениями. Лучшие результаты получаются при охлаждении слитков до 700—800° С, последующем нагреве до 1000—1100° С, выдержке при этой температуре и дальнейшем нагреве для про-, катки. Большие холодные слитки следует. нагревать до 800° С медленно (скорость 30—40°С в час), выдержать при этой температуре 1 —1,5 часа и вести дальнейший нагрев со скоростью 60—80° С в час.
При прокатке слитков в первых проходах допустимы обжатия 30—40 мм, а в последних до 50—60 мм. Особенно затруднительными являются операции отделки рельсов — фрезерование торцов и сверление отверстий.
Стрела прогиба рельсов из стали марки Г13 оказалась примерно в два раза больше, чем для углеродистых рельсов, а твердость поверхности катания выше, чем в центре головки.
Сталь, содержащая 0,93% С, 12,02% Μη, 0,24% Si, 0,09% P. 0,021% S, 0,05% Сr, 0,13% Ni и 0,14% Си, обладала следующими свойствами: предел текучести 30—32 кГ/мм2, предел прочности 70—73 кГ/мм2, относительное удлинение 20—22% и сужение сечения 19—20%.
Структура металла при охлаждении образцов в воде и на воздухе состояла из полиэдров аустенита без карбидной фазы. На этом основании был сделан вывод о возможности укладки высокомарганцовистых рельсов на полотно без дополнительной термической обработки. Однако опыт не .подтвердил этого вывода: уже после пропуска 15—20 млн. г груза в рельсах появились поперечные трещины. По-видимому, только термическая обработка рельсов из стали марки Г13 может обеспечить те высокие служебные качества, которыми обладают стрелочные переводы, изготовленные из этой стали.
6. РЕЛЬСЫ ИЗ СЛ0ЖН0ЛЕГИРОВАНН0Й СТАЛИ
Хромованадиевая сталь (0,46% С, 1,08% Сr и 0,23% V) отличается хорошим сочетанием прочностных и пластических свойств. Это обстоятельство было учтено при выборе состава стали, способной обеспечить высокие служебные свойства без термической обработки. После изучения свойств стали различных составов, выплавленных в лабораторной печи, были отобраны три состава для выплавки стали в 30-г мартеновской печи. Сталь двух плавок легировали хромом, кремнием и ванадием и сталь одной плавки — хромом, кремнием и титаном.
Выплавку производили по технологической инструкции для легированной стали. Предварительное раскисление в печи производили бедным ферросилицием (8—12 кг/т), ферромарганцем (14 кг/т ) или силикомарганцем (5—7 кг/т). Феррохром вводили после доменного ферросилиция и силикомарганца за 15— 20 мин. до выпуска металла. Окончательное раскисление производили в ковше 45- или 75%-ным ферросилицием и алюминием. При раскислении хромокремнетитанистой стали алюминий не применяли.