Производство проката
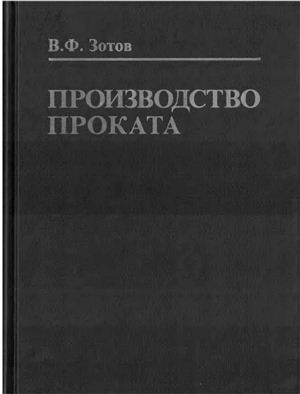
Зотов В.Ф,
Интермет Инжиниринг, 2000 г.
АГРЕГАТЫ И МЕХАНИЗМЫ ГЛАВНОЙ ЛИНИИ ПРОКАТНОГО СТАНА
Процесс деформации осуществляется в валках рабочей клети, вращение которым через шестеренную клеть и редуктор при помощи шпинделей и муфт передается от электродвигателей.
ПРИВОД ВАЛКОВ
Привод валков рабочих клетей прокатных станов осуществляется при помощи электродвигателей переменного и постоянного тока. Электродвигатель, обеспечивающий вращение валко называется главным электроприводом.
Электродвигатели переменного тока используют на станах с постоянной скоростью прокатки — на линейных и непрерывных станах.
Электродвигатели постоянного тока используют, когда необходимо регулировать скорость прокатки — на непрерывных станах, блюмингах, слябингах и др. Электродвигатели должны не только обеспечивать требования технологического процесса прокатки, но и давать возможность выполнять их с необходимой гибкостью. Мощность привода должна быть такова, чтобы удовлетворять требуемым усилиям прокатки и натяжению полосы. Кроме того, электродвигатели должны обеспечивать и необходимый скоростной режим.
Размещают электродвигатели в машинных залах, но иногда и в пролете прокатного стана. Существуют индивидуальный и групповой приводы. При индивидуальном приводе вращение осуществляется в одной клети. Если от одного электродвигателя приводится группа клетей прокатного стана, такой привод называется групповым. В первом случае привод осуществляется через редуктор с коническими шестернями. При индивидуальном приводе редуктор устанавливают с целью повышения скорости вращения двигателя и тем самым уменьшения его мощности.
На некоторых станах применяется привод каждого валка от отдельного электродвигателя. В этом случае шестеренная клеть и редуктор отсутствуют.
Шестеренные клети предназначены для передачи вращения от одного коренного вала двигателя двум, трем или четырем валкам прокатной клети, число шестерен соответствует числу рабочих валков. Шестеренные клети делают открытыми, со съемной крышкой. К подшипникам и зубчатым зацеплениям шестерен непрерывно подается жидкая смазка. Размеры шестерен (диаметр и длина) близки к размерам рабочих валков (рис. 48).
Станины и крышки изготавливают из высокопрочных или модифицированных марок чугуна. Шестерни изготавливают из кованой легированной стали марки 4ХН, а зубья шестерен подвергают поверхностной закалке. В шестеренных клетях применяют роликовые конические подшипники или баббитовые. К подшипникам и зубчатому зацеплению непрерывно подается жидкая смазка.
Размеры шестеренных валков выбираются в зависимости от типа стана, диаметра рабочих валков, высоты подъема и передаваемого крутящего момента. Если частота вращения валков меньше частоты вращения электродвигателя, то между двигателем и шестеренной клетью устанавливается понижающий редуктор. На обжимных реверсивных прокатных станах применяют безредукторный привод.
В зависимости от частоты вращения двигателя и скорости прокатки изготавливают одно-, двух- или трехступенчатые редукторы. Для равномерной нагрузки на подшипники редуктора шестерни устанавливают по возможности симметрично. Передаточное число каждой ступени равно 4—6. В некоторых конструкциях шестеренные клети и редукторы устанавливаются в одном корпусе. Достоинство такой конструкции в ее компактности.
ШПИНДЕЛИ.
Для передачи вращения валкам от шестеренной клети или электродвигателя применяют шпиндели двух типов: универсальные шарнирные и зубчатые. Универсальные шпиндели (рис. 49) позволяют передавать большие крутящие моменты, допуская лри этом значительные вертикальные перемещения валков. В зависимости от величины передаваемого крутящего момента из условия прочности угол наклона шпинделя на обжимных, толстолистовых и заготовочных станах устанавливается в пределах 3—10°, а на листовых до 1—2°, при этом угол наклона нижнего шпинделя несколько меньше наклона верхнего шпинделя из-за более тяжелых условий работы. Шпиндели изготавливают из углеродистой кованой стали 40 или из легированной стали 40Х.
Для высокоскоростных станов холодной прокатки применяют зубчатые шпиндели с бочкообразным профилем зуба, допускающие рабочие углы перекоса.
МУФТЫ главной линии прокатного стана должны предохранить стан от перегрузки и компенсировать перекос осей валков. В основном применяют зубчатые муфты и гибкие муфты с резиновыми баллонами (рис. 50). Зубчатые муфты могут передавать большие крутящие моменты при радиальном смещении и перекосе валков. Зубчатые муфты постоянно заправляются смазкой. В последнее время все больше используют гибкие муфты. Они просты в изготовлении, бесшумны в работе, не требуют смазки и также допускают смещение и перекос валков.
РАБОЧИЕ КЛЕТИ ПРОКАТНЫХ СТАНОВ
Основой прокатного стана является рабочая клеть, в которой осуществляется собственно прокатка металла. Конструкция, размеры и масса рабочих клетей зависят от назначения и специализации прокатных станов, условий процесса прокатки металла, числа рабочих валков в самой клети, уровня технического прогресса в прокатном производстве.
Рабочая клеть прокатного стана должна удовлетворять следующим требованиям: доступность обслуживания при эксплуатации и ремонте, быстрота смены валков, высокая прочность станины и других элементов клети не только при рабочих давлениях, но и в непредвиденных аварийных случаях. Основными элементами рабочих клетей являются станина, валки, подшипники, подушки, механизмы для установки и уравновешивания валков (рис.51).
СТАНИНЫ рабочей клети относятся к самым ответственным деталям рабочей клети. Две станины, соединенные стяжными болтами или траверсой, образуют основу рабочей клети. Каждая станина состоит (рис. 52) из двух стоек, а также верхней и нижней поперечин. Рабочая клеть крепится к плитовине либо болтами, либо специальными гидравлическими зажимами, которые позволяют быстро производить замену станины. По конструкции станины делят на открытого и закрытого типа. Крышка станины открытого типа крепится с помощью откидных с клиновым соединением болтов к стойкам станины, что облегчает перевалку валков клети.
Станины открытого типа позволяют осуществлять перевалку валков непосредственно краном при снятой крышке. Станины этого типа применяются в клетях сортовых и рельсобалочных станов линейного типа. Станина закрытого типа представляет собой литую жесткую раму. Она более прочна и жестка, и ее применяют в рабочих клетях блюмингов, слябингов, тонколистовых станов горячей и холодной прокатки, а иногда заготовочных и сортовых станов.
Сечение стоек станин обычно изготавливается двутавровым или прямоугольным. Усилия, возникающие при прокатке, главным образом воспринимаются станинами, поэтому при конструировании и изготовлении особое внимание уделяется их прочности и жесткости. Коэффициент запаса прочности принимается равным не менее 10. Станины изготавливаются из литой углеродистой стали с содержанием 0,25—0,35 % С. Размеры станины должны обеспечить размещение в окне станины подушек валков и конца нажимного винта требуемой
Затраты, связанные с эксплуатацией валков, составляют 5-15% всех расходов по прокатному стану.
ПРОКАТНЫЕ ВАЛКИ классифицируют по назначению, форме бочки валка, конструкции, материалу. По назначению валки бывают сортовые и листовые, кантующие, разрезные, правильные и т.д., валки для горячей и холодной прокатки, валки обжимные, черновые, предчистовые и чистовые. По форме бочки валки бывают гладкие или цилиндрические, с калибрами. По конструкции различают валки цельнолитые, цельнокованые и составные. По материалу валки бывают стальные, чугунные и из твердых сплавов.
Основными параметрами прокатного валка являются диаметр Dи длина Lбочки, которые определяют название сортовых и листовых станов.
Рабочий диаметр валков выбирают с учетом "естественного" угла захвата, т.е. без принудительного заталкивания
металла в валки и из условия прочности, а для тонколистовых станов и с учетом жесткости.
Значения диаметров и длины бочек валков определяются по ГОСТу.
В процессе эксплуатации валки изнашиваются. С целью продления периода эксплуатации валков их перетачивают, в результате чего диаметр их уменьшается и снижается их прочность.
Параметры шеек валков выбираются исходя из условий прочности валков, мощности привода и других факторов. Для увеличения прочности стремятся изготавливать шейки валков большего диаметра, чтобы давление при прокатке распределить на большую площадь и тем самым уменьшить усилие на единицу поверхности. Диаметр шейки валков, имеющих подшипники скольжения открытого типа, устанавливается по условию прочности в зависимости от диаметра бочки валка:
для обжимных и сортовых станов dm= (0,55—0,63)Z); для листовых станов дуо и трио dw= (0,7-0,75)1).
Длину шейки обычно принимают равной ее диаметру, а диаметр концевых частей валков на 10—15 мм меньше диаметра шейки.
Материал валков должен обеспечивать возможность прокатки в течение длительного времени без поломок и при минимальном износе поверхности.
Валки изготавливают из чугуна и сталей, легированных различными элементами (Сr, Ni, Moи др.). Для обжимных и заготовочных станов, где валки испытывают большие динамические нагрузки и находятся в весьма тяжелых температурных условиях, применяются незакаленные валки — мягкие или полутвердые, изготавливаемые из незакаленной стали, серого или полузакаленного чугуна.
Для листовых и сортовых станов, валки которых должны быть прочны и отличаться высокой твердостью поверхности, применяют валки с мягкой сердцевиной, хорошо сопротивляющейся изгибу и твердой поверхности. Такие валки делают из закаленной стали или чугуна. Для холодной прокатки тонких листов и лент применяют и особотвердые валки из специальных марок сталей и сверхтвердые, изготавливаемые из твердых металлокерамических сплавов на основе карбида вольфрама.
Чугунные валки применяют во всех случаях, когда они обеспечивают необходимую прочность. Необходимую твердость бочки получают при отливке путем использования различных материалов для изготовления форм, в которые производится отливка. Балки высокой твердости изготавливают двухслойными: наружный слой из высоколегированного чугуна, а сердцевина — из чугуна более прочного при работе на изгиб, например, серого. Твердость валков может быть увеличена не только при отливке. Эффективным способом является поверхностная закалка.
Твердые чугунные валки отливают в металлические формы и на их поверхности образуется твердый отбеленный слой. Толщина отбеленного слоя определяет срок службы валка, т.е. допустимое число переточек, и составляет 15-60 мм, но не более 0,1 D.
Стальные валки применяют в тех случаях, когда прочность чугунных валков недостаточна. Мягкие валки изготавливают из литой и кованой углеродистой стали с содержанием углерода 0,4—0,8 %. Твердые и полутвердые валки изготавливают из легированной стали 60ХН, 50ХН, 60ХГН, 60ХГ, 9Х и др. Для получения высокой твердости применяют поверхностную закалку.
ВАЛКИ ДЛЯ СТАНОВ ХОЛОДНОЙ ПРОКАТКИ, для которых требуется высокая твердость поверхности бочки, изготавливают коваными из хромистой стали. Высокая твердость бочки обеспечивается индукционной закалкой токами промышленной частоты, при этом твердость поверхности шеек в 2—3 раза выше твердости бочки, глубина закаленного слоя должна быть не менее 3 % от радиуса валка, но не менее 5 мм. Для валков диаметром менее 300 мм применяют хромистую и хромованадиевую сталь марок 9Х и 9ХФ, а для валков диаметром более 300 мм — сталь с повышенным содержанием хрома марок 9X2, 9Х2МФ, 9Х2В.
Кроме цельных чугунных и стальных листовых и сортовых валков, на прокатных станах применяются составные или бандажированные валки. Применение таких валков не только дает оптимальное соотношение механических свойств бочки и средней части валков, но и экономит легированную сталь, так как при большом износе его меняют только бандажи. На рис. 54 приведена конструкция бандажированного валка.
ПРОФИЛИРОВКА ВАЛКОВ. Валки листопрокатных станов должны иметь бочку такой формы, чтобы при прокатке образовывалась межвалковая щель с параллельными сторонами, что обеспечивает получение высококачественного проката без поперечной разнотолщинности.