Производство огнеупоров полусухим способом
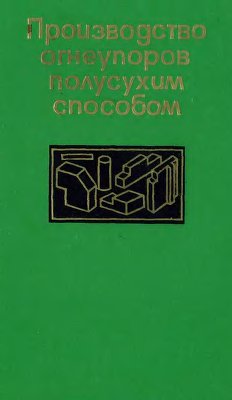
Карклит А.К., Ларин А.П., Лосев С.А., Берниковский В.Е.
Металлургия, 1981 г.
СМЕШИВАНИЕ ОГНЕУПОРНЫХ МАСС И СМЕСИТЕЛЬНОЕ ОБОРУДОВАНИЕ
Общие сведения о процессе смешивания
В огнеупорной промышленности применяется более 100 различных полусухих масс, различающихся по вещественному, зерновому составу и влажности. К наиболее распространенным видам масс относятся:
1) шамотные и высокоглиноземистые крупностью до 2—3 мм, влажностью до 10%;
2) магнезиальные крупностью до 2 мм, влажностью до 4%;
3) динасовые крупностью до 3 мм, влажностью 5— 6%;
4) карбидкремниевые крупностью до 1—2 мм, влажностью до 4 %;
5) корундовые массы влажностью 3—4,5%;
6) смолодоломитовые и смоломагнезитовые крупно-стью8—10 мм, с 5—6% каменноугольной смолы или пека. Характерными для всех видов масс являются слабая подвижность, ухудшающаяся при снижении окружающей температуры; прилипание к рабочим поверхностям смесителей (в особенности смолусодержащнх масс); склонность к самоуплотнению и сводообразованию при хранении в емкостях (в табл. 33 приведены углы откосов для некоторых огнеупорных масс); абразивность, вызывающая быстрый износ облицовочных деталей смесителей и прессформ. Специфической особенностью большинства масс, особенно шамотных, динасовых и магнезиальных, является склонность к расслаиванию (расфракционированию) при транспортировании, в перегрузочных узлах и бункерах, ведущая к нарушению однородности изделий.Сухие компоненты и высохшие массы пылят при перемещении. Различные массы имеют свои особенности: карбидкремниевая масса с большим количеством с.с. б. быстро подсыхает и твердеет; горячие смолодоломитовые массы при остывании до 60°С прилипают к рабочим поверхностям машин и при 40—50° С приобретают вязкость, затрудняющую работу засыпных устройств. Все эти свойства должны учитываться при выборе смесителей и параметров процесса смешивания.
Изделия из разных масс
Растущие требования к ассортименту огнеупоров привели к появлению новых полусухих масс в огнеупорном производстве. Корундографитовые шихты из 55% электрокорунда № 10, 20% тигельного графита, 7% карбида кремния № 12, 3% тонкомолотого кремния и 15% спекающейся глины применяют для изостатического формования сложных по форме погружаемых сталсразливочных стаканов под давлением от40 до 100 МПа [37, 38]. Широко применяют гидростатические установки при сравнительно небольших давлениях (20— 30 МПа) для формования изложниц, тиглей и других изделий из графитсодержащих масс. Под изостатическим давлением 100 МПа формуют блоки из порошка оксида хрома фракции 6—10 мкм и менее на связке из ме-тилцеллюлозы или декстрина с с. д. б. [39J. Для предотвращения трещин от запрессованного воздуха иногда на таких установках применяют замедленное снижение давления. Цирконовые изделия формуют из гранулированных порошков, полученных на распылительной сушилке [40], На гидропрессах из полусухих масс изготовляют цирконографитовые стаканы. Накоплен большой опыт формования полусухим способом карбидкремниевых огнеупоров, в том числе на гидравлических прессах и виброустановках. В опытном порядке испытан способ импульсного прессования кремнеземных масс [41], Изучается применение высоких давлений, оказывающих влияние не только на плотность, но и на количество и размер пор изделий [42—44]. Таким образом, полусухой способ формования становится все более универсальным в огнеупорном производстве.
ПОДГОТОВКА ПОРОШКОВЫХ КОМПОНЕНТОВ ОГНЕУПОРНЫХ МАСС
Для подготовки огнеупорных порошков материал проходит обычные процессы дробления, измельчения, помола и сортировки. Оборудование для этих процессов описано в литературе [45—54] и выпускается серийно. Ниже приведены краткие сведения о характере работы и расчеты производительности оборудования по подготовке порошков огнеупорного производства.
Дробление
При дроблении материалов существенное значение имеют их кажущаяся плотность и прочность. Свойства некоторых огнеупорных материалов приведены в табл. 13. В зависимости от крупности исходного и дробленого материала различают три стадии дробления: крупное или первичное (от 1500—300 до 300—100 мм), среднее (от 350—100 до 100—40 мм) и мелкое (от 100—40 до 30—5 мм). Последующую операцию для получения зерна 5—0,09 мм называют измельчением, а для получения фракции <0»09 мм — помолом. Для дробления применяют дробилки, а для измельчения и помола — мельницы. Каждая машина наиболее эффективно работает только при определенных степенях измельчения, поэтому рационально дробить и измельчать материал от исходной крупности до требуемого размера в комплексе последовательно работающих машин.
Материал можно дробить и размалывать в открытых или замкнутых циклах. В открытом цикле крупная часть материала вторично в дробилку не возвращается. При замкнутом цикле дробленый продукт поступает на классификацию и отделяемые более крупные куски направляются для дополнительного дробления. Материал, направленный вторично на дробление, называется циркуляционным и создает циркуляционную нагрузку. Отношение размеров кусков или зерен исходного материала перед дроблением и измельчением к размеру кусков или зерен выходящего продукта называют степенью дробления или измельчения.