Производство и использование порошковых деталей в легкой промышленности
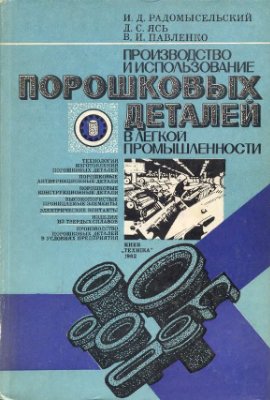
Радомысельский И.Д., Ясь Д.С., Павленко В.И.
К.: Техніка, 1982 г.
ОСОБЕННОСТИ ИЗГОТОВЛЕНИЯ ДЕТАЛЕЙ
Технология изготовления порошковых антифрикционных деталей в основном мало отличается от общей технологии изготовления порошковых деталей и состоит из следующих этапов: приготовления шихты, прессования, спекания, пропитывания маслом, калибрования и, если необходимо, механической обработки.
Приготовление шихты. Чаще всего при изготовлении порошковых подшипников скольжения, втулок, вкладышей, подпятников и т. п. используются порошки железа — марок ПЖ2М2, ПЖЗМ2, ПЖ4М2 и др. (по ГОСТ 9849—74); меди — марок ПМС-1 и ПМС-2 (по ГОСТ 4960—75); олова — марок ПОЭ и ПО-1 (по ГОСТ 9723— 73); никеля — марок ПНЭ1 и ПНК1 (по ГОСТ 9722—71); свинца — марки ПСА (по ГОСТ 16138—70); графита — марок КК, КЛЗ, ЭЗМ (по ГОСТ 4404—72) и ЭУЗ, ЭУТ и ЭУН (по ГОСТ 10274—72).
Порошки в определенных соотношениях смешивают в смесителях различных конструкций, куда для интенсификации процесса вместе с порошками загружают фарфоровые шары, металлические ежи, пружины. Для предотвращения сегрегации порошковой смеси и улучшения перемешивания в шихту добавляют в небольших количествах бензин, стеарат цинка, глицерин или машинное масло (до 2% по массе). Продолжительность процесса смешивания колеблется от 1 до 6 ч.
Прессование. Из всех известных методов формования при изготовлении порошковых антифрикционных деталей чаще всего используется метод холодного прессования в закрытых пресс-формах при давлениях от 0,3 до 0,8 ГПа. Этот метод является наиболее простым и высокопроизводительным. Холодное прессование состоит из операций по дозированию и засыпке шихты в пресс-форму, прессования и выталкивания прессовок из пресс-формы. В зависимости от отношения длины втулки l к ее диаметру d и производят одно- или двустороннее прессование. Так, при соотношении l/d <1 можно ограничиться односторонним прессованием. При соотношении l/d >1 применяют двустороннее прессование. Это связано с необходимостью обеспечения равномерной пористости по всей длине изделия. Втулки с определенной остаточной пористостью (обычно 15—20%) получают либо прессованием по заданному давлению, либо с применением ограничителя высоты (т. е. прессованием до упора). Прессовки должны иметь форму и размеры готовых изделий с учетом их усадки в результате последующего спекания, а также припусков, необходимых для проведения механической обработки.
Спекание. Антифрикционные детали на железной и медной основе спекают в защитной среде (водород, азот, диссоциированный аммиак, конвертированный газ). Оптимальная температура и продолжительность спекания для порошковых изделий из материалов различных составов представлены в табл. 5.
Пропитка маслом. Порошковые пористые антифрикционные детали в большинстве случаев пропитывают маслом. Благодаря этому они приобретают свойства самосмазываемости и коррозионной устойчивости. Пропитку втулок на железной основе рекомендуется производить сразу же после спекания.
Калибрование. Применяют два способа калибрования — раздельный и комбинированный. В соответствии с первым способом (рис. 18, а) сначала калибруется внешняя поверхность (втулка проходит через матрицу), а затем внутренняя (пуансон проходит через внутреннее отверстие втулки). Во втором случае (рис. 18, б) предусматривается одновременное калибрование наружной и внутренней поверхностей. При этом втулка с предварительно вставленным во внутреннее отверстие пуансоном проталкивается через матрицу. Комбинированный способ калибрования для порошковых самосмазывающихся втулок более приемлем, так как в этом случае поры лишь сплющиваются, после этого их объем практически не меняется и сохраняется выход пор на рабочую поверхность изделия [12].
Перед калиброванием детали должны иметь размеры на 0,5— 1,6% больше окончательных. Припуск на калибровку наружных и внутренних поверхностей деталей различен. Для наружных он должен быть больше, так как требуется, чтобы обеспечивалась необходимая прочность посадки и закрытие устьев пор; для внутренних— меньше, в этом случае важно, чтобы выходы пор на поверхность трения оставались открытыми. В табл. 7 приведены значения калибровочных припусков для обработки наружного диаметра втулки, которые обеспечивают максимальную прочность посадки.
Величина усилия калибрования обычно не превышает 20—30% усилия прессования. Предварительная пропитка изделий маслом облегчает процесс калибрования.
Механическая обработка. Более высокие требования к точности размеров деталей, усложнение геометрической формы вызывают в отдельных случаях необходимость применения дополнительной механической обработки резанием. Такая обработка применяется при изготовлении подшипников, имеющих несколько переходов (буртов, выточек, каналов и т. д.) в направлении прессования;
7. Калибровочные припуски для обработки наружного диаметра втулки, %
Материал | Пористость, % | Минимальный | Средний | Максимальный | Материал | Пористость, % | Минимальный | Средний | Максимальный |
Железо- графит
| 15 | 0,5 | 0,8 | 0,8 | Железо | 15 | 0,6 | 0,8 | 0,9 |
25 | 0,8 | 1.0 | 1.2 | 25 | 0,9 | 1,2 | 1,3 | ||
30 | 1,0 | 1,2 | 1.5 | 30 | 1,2 | 1,4 | 1,6 |
отверстия, расположенные перпендикулярно или под углом к направлению прессования; резьбу, канавки, конусность.
По описанной выше технологии изготавливается большинство порошковых антифрикционных материалов на основе железа и меди. При этом порошковые материалы на основе железа содержат графита — до 3%, меди — до 5%; на основе меди — графита — до 4%, олова — 8—10%. Пористость антифрикционных материалов — от 15 до 30%.
Свои особенности и отличия имеют технологические процессы изготовления сульфидированных самосмазывающихся материалов, металлографитовых материалов с повышенным содержанием графита и металлопластмассовых материалов.
Сульфидированные пористое железо и железографит. В состав сульфидированных антифрикционных материалов на железной основе помимо железа или железа и графита входит сера. Количество серы при этом составляет 0,8—1%. В ряде случаев в состав железографитовых материалов вводятся сульфиды металлов: сульфид цинка — до 4%, сульфид меди — до 3,5%. При изготовлении антифрикционных изделий применяются в основном следующие методы сульфидирования: введение серы или сернистых металлов (сульфидов) в шихту; газовое сульфидирование в сероорганических соединениях; пропитка пористых изделий жидкой серой.
В целом технология изготовления сульфидированных порошковых материалов и деталей состоит из процессов, входящих в общую технологию изготовления порошковых изделий с добавлением операции сульфидирования. Следует отметить, что в процессе спекания вводимая в состав материалов сера, в зависимости от температуры процесса и состава защитной среды, может в определенной степени выгорать. Поэтому в процессе приготовления шихты сера должна вводиться с учетом ожидаемого выгорания.
Металлографитовые антифрикционные материалы с повышенным содержанием графита. В состав указанных материалов помимо металлов входит графит, при этом его содержание колеблется в пределах 8—12% по массе.
Известно [10], что с повышением содержания графита антифрикционные свойства металлографитовых материалов улучшаются. Однако при содержании графита в их составе, превышающем 5—7% по массе, резко снижаются прочностные характеристики, а также тепло- и электропроводность материалов. Ввиду этого содержание графита в стандартных медно- и бронзографитовых материалах не превышает 2—4% по массе. Такого количества его явно мало для обеспечения нормальной работы подшипников в режиме сухого трения. Для образования сухой смазывающейся пленки материал должен содержать более 10—15% по массе графита, что весьма сложно обеспечить, применяя обычные методы порошковой металлургии. Связано это с тем, что в процессе смешивания порошков металла и графита и дальнейшего прессования полученной смеси металлические частицы обволакиваются графитовой пленкой, обусловливающей значительное снижение числа металлических контактов и торможение процесса спекания.
Результатом исследований новых способов получения антифрикционных металлографитовых материалов с повышенным содержанием графита стало появление методов, к которым прежде всего следует отнести: метод горячего прессования; метод прессования и дальнейшего спекания в присутствии жидкой фазы, с применением вводимых в шихту поверхностно-активных добавок.
С использованием метода горячего прессования были получены бронзографитовые антифрикционные материалы с повышенной износостойкостью. Пористость этих материалов минимальная (5— 10%), содержание графита колеблется от 4 до 12% по массе [19].
Несмотря на преимущества бронзографитовых материалов, полученных горячим прессованием, указанный метод не нашел широкого распространения ввиду сложности, высокой стоимости и низкой производительности применяемого оборудования.
Метод прессования и дальнейшего спекания прессовок в присутствии жидкой фазы с применением вводимых в шихту поверхностно-активных добавок позволил получить материалы с высоким содержанием графита (до 90% по объему). Действие поверхностно-активных добавок заключается в улучшении смачиваемости поерхности графита жидким металлом. В результате металл растекается по поверхности частиц графита, изолируя их и образуя непрерывную металлическую матрицу. Таким образом, выполняется условие, обеспечивающее получение материалов с высоким содержанием графита, хорошей тепло- и электропроводностью и достаточной механической прочностью. Промышленному внедрению вышеописанного метода препятствует необходимость использования высоких температур, специальной оснастки при спекании прессовок.