Производство биметаллов
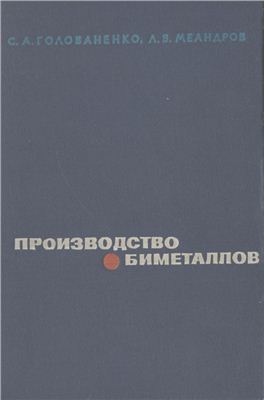
Голованенко С.А., Меандров Л.В.
Металлургия, 1966 г.
МЕТОДЫ ПОЛУЧЕНИЯ БИМЕТАЛЛОВ
В настоящее время существует большое количество различных методов получения биметаллов, что объясняется большим разнообразием биметаллов по их видам и композициям, а также стремлением найти самый рациональный метод получения для каждого вида. В патентной литературе уже зарегистрировано несколько тысяч патентов на способы получения различных видов биметаллов. Производством биметаллов занято большое количество заводов как в СССР, так и за рубежом. Естественно, что на технологию производства биметаллов накладывает отпечаток и состав оборудования завода, на котором организовано его производство.
Несмотря на разнообразие методов получения различных биметаллов, нашедших применение в промышленности, их можно разделить на три группы, причем каждая группа объединяется основным принципом получения заготовки биметалла: а) получение заливкой; б) получение совместной пластической деформацией; в) получение наплавкой, электросваркой или другим методом соединения, не требующим обязательной пластической деформации для создания прочного соединения.
Рассмотрим подробно все перечисленные выше методы производства биметаллов.
1. ПОЛУЧЕНИЕ БИМЕТАЛЛОВ ЗАЛИВКОЙ
Этот метод является самым старым и применяется для получения различных видов биметаллической продукции. В основе метода лежит получение двух- или многослойного слитка заливкой одного или более слоев на твердый слой другого состава. 160
Метод получения биметаллов заливкой применяется как для получения крупных слитков массой (весом) до 13 т, так и для получения небольших слитков массой (весом) в несколько килограмм.
В зависимости от требуемой композиции, формы и массы (веса) слитка этот метод имеет разновидности, которые предусматривают последующую горячую прокатку или иную горячую обработку давлением полученного слойного слитка с интенсивными частными обжатиями и достаточно большим суммарным обжатием. Соединение слоев биметалла может происходить как в процессе заливки, так и в процессе горячей обработки давлением.
Заливка жидким металлом твердой пластины, помещенной в изложницу, применяется для получения многих видов биметаллов различного назначения. В частности, этот способ применяется для получения коррозионностойких листовых биметаллов сталь + нержавеющая сталь, сталь +медь, сталь +медные сплавы, для получения термобиметаллов, у которых один слой является сплавом на основе цветных металлов, для получения проводниковых биметаллов сталь + медь, для получения инструментального биметалла сталь + инструментальная сталь, для получения износостойкого полосового биметалла для отвалов плугов мягкая сталь + твердая сталь, для получения самозатачивающегося профильного биметалла для плужных лемехов сталь - инструментальная сталь, для получения двухслойного круглого проката для изготовления судовых гребных валов.
Наибольшее распространение в СССР этот метод получил в производстве коррозионностойкого толстолистового биметалла для химической промышленности и в производстве износостойкой полосовой трехслойной стали для отвалов плугов.
При изготовлении методом заливки коррозионностойких толстых листов на металлургических заводах СССР (КМК и Комму-нарском) применяется следующий порядок основных технологических операций.
В изложницу для отливки слитка массой (весом) 6,5—13 т помещается специально подготовленный сляб из коррозионностой-кой стали. Подготовка сляба заключается в его строжке с четырех сторон для удаления окислов (окалины) и поверхностных дефектов, в обезжиривании, в приварке ушек и штырей для монтажа сляба в изложнице, в обмазке сляба с двух сторон — с наружной стороны магнезитовым порошком для предотвращения сварки с металлом и с внутренней стороны нашатырем для улучшения сварки с углеродистой сталью.
В изложницу с помещенной в нее плитой производится сифонная заливка жидкой углеродистой или низкоуглеродистой стали основного слоя из мартеновской печи (рис. 80, а). Заливаемый металл образует защитный слой — подливку — толщиной 50— 65ммдля защиты поверхности нержавеющего сляба от окисления.
Заливка может производиться и для получения этим методом трехслойного биметалла. В этом случае в изложницу помещаются два одинаковых сляба у двух противоположных стенок изложницы или один сляб в центре изложницы (рис. 80, в, г).
Известен также способ, при котором в центр изложницы помещаются два сляба, сваренных между собой по периметру электросваркой [99]. Плоскости соприкосновения этих слябов между собой смазаны специальным составом для предотвращения сваривания их друг с другом. В качестве такого состава применяют мелко молотый шамот или хромомагнезит. Из такого слитка после прокатки получаются два двухслойных листа. Однако ввиду сложности этот способ не получил широкого распространения в промышленности.
После охлаждения и извлечения из изложницы биметаллический слиток нагревается в колодцах до температуры прокатки, которая определяется химическим составом основного и плакирующего слоев. Нагретые слитки прокатываются на блюминге на сляб с максимально возможными частными обжатиями. Размеры сляба определяются размерами прокатываемых из него листов с учетом раскроя металла.
После охлаждения со слябов автогенным резаком удаляется подливка. Слябы зачищаются и затем нагреваются в методических печах и прокатываются на толстолистовых станах на требуемую толщину. Прокатанные листы после правки и обрезки подвергаются термической обработке, повторной правке, травлению и окончательной отделке.
Такой метод имеет тот недостаток, что между плитами коррозионностойкой стали и углеродистой сталью может образовываться пленка окислов, препятствующая надлежащей связи разнородных металлов при прокатке.
Предложен метод, по которому изложница с вставленным в нее слябом из коррозионностойкой стали помещается в вакуумную
камеру с заливкой жидкого металла через отверстие, предварительно закрытое алюминиевой пластинкой 1100], которая расплавляется при ударе струи жидкой стали. В процессе разливки в камере поддерживается вакуум.
По другой схеме предложено в вакуумную камеру помещать и качающуюся печь. Этот метод хотя, по всей вероятности, и может существенно улучшить прочность соединения слоев, однако его сложно применить при получении многотонных биметаллических слитков для получения толстолистового биметалла. Ввиду этого он может получить лишь ограниченное применение для получения малых отливок из специальных сплавов.
Метод заливки был опробован на Кузнецком металлургическом комбинате и для получения фасонного биметаллического проката [6].
На рис. 81 приведен чертеж изложницы для слитка массой (весом) 6 т, в который точно на оси устанавливался квадратный сердечник стали ХНЗМ размерами 475 X 475 X 1950 мм со скошенными углами. В изложницу заливали сталь Х18Н9Т сифонным способом. Слитки после соответствующей выдержки для затвердевания передавались к нагревательным колодцам, где нагревались до температуры 1270—1280° С.
Слитки прокатывали сначала на блюминге 1100, а затем без промежуточного нагрева на блюминге 900 на блюмы сечением
210 X 210 и 180 х 180 мм для последующей прокатки на круг диаметром 130—140 и 90 мм. Прокатка на готовые профили круглого сечения производилась на крупносортном девяти клетевом стане 500.
В процессе производства круглой биметаллической стали главная трудность заключается в том, что сердечник в круглом готовом профиле имеет форму, отличающуюся от правильной окружности. На рис. 82 приведены обводки темплетов круглых биметаллических профилей, полученных на КМК. Отличие от окружности получается больше, если в слиток залить сердечник круглой формы. Это объясняется тем, что при прокатке с кантовкой на 90° между отдельными проходами деформация осуществляется в двух взаимно перпендикулярных плоскостях.
Некоторое улучшение формы сердечника может быть достигнуто, если вместо ящичной системы калибровки применять калибровку по системе овал—круг.