Приборы для неразрушающего контроля материалов и изделий. Книга 2
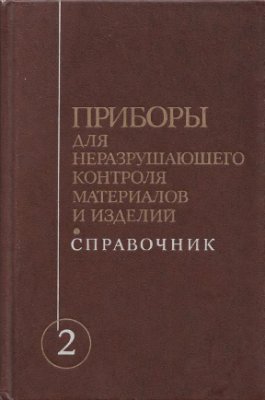
Клюев В.В. (ред.)
Машиностроение, 1976 г.
ПРИБОРЫ И МЕТОДИКА КОНТРОЛЯ МЕТАЛЛОВ
ОБЩИЕ ПРИНЦИПЫ РАЗРАБОТКИ МЕТОДИКИ КОНТРОЛЯ
Разработка методики дефектоскопии или проектирование установки для автоматического контроля начинается с выбора схемы контроля: метода контроля, типа волн, поверхности, через которую вводятся ультразвуковые волны, угла ввода. Для контроля металла применяют в основном эхо-, теневой и зеркально-теневой методы. Предпочтение отдается эхо-методу, как наиболее чувствительному и помехоустойчивому. Теневым методом контролируют тонкие, слоистые (например, паяные) металлы с простой формой поверхности. Как правило, он требует доступа к двум поверхностям изделия. Зеркально-теневой метод применяют при доступе к одной поверхности, когда дефекты не дают эхо-сигнала (например, из-за наличия мертвой зоны или в связи с неблагоприятной ориентацией дефекта), но ослабляют данный сигнал.
Тип ультразвуковых волн выбирают следующим образом. Продольными и поперечными волнами контролируют изделия значительной толщины — в несколько раз большей длины волны. Волны в пластинах применяют для контроля листов, оболочек, труб с толщиной стенки, соизмеримой с длиной волны. Волнами в стержнях проверяют проволоки и прутки, диаметр которых соизмерим с длиной волны. Поверхностными волнами выявляют дефекты на поверхности изделия; чувствительность уменьшается с увеличением глубины и практически достигает нуля на глубине, равной длине волны. Сложная форма поверхности изделия не является препятствием, поскольку поверхностная волна следует за всеми ее изгибами. Для выявления подповерхностных дефектов применяют продольные подповерхностные волны, возникающие при наклонном падении ультразвука на поверхность изделия под углом, равным первому критическому. Эти волны нечувствительны к неровностям и дефектам на поверхности изделия и достигают максимума чувствительности на глубине 5—10 мм от поверхности.
Направление ультразвуковых волн должно быть таким, чтобы обеспечивалось надежное выявление наиболее опасных дефектов. Особо ответственные изделия контролируют несколько раз при различных направлениях ультразвуковых волн.
При контроле эхо-методом выявляемость дефектов в большой степени зависит от направления продольных и поперечных волн. При включении искателей по совмещенной схеме для достижения оптимальной чувствительности к реальным дефектам волны должны падать на плоскость дефекта перпендикулярно или отражаться от дефектов и поверхности, расположенной вблизи них так, чтобы достигалась большая амплитуда обратного эхо-сигнала . Ориентация дефектов значительно меньше влияет на выявляемость при контроле волнами в пластинах и стержнях, в которых одинаково хорошо выявляются поперечные и продольные дефекты. Исключение составляют случаи, когда дефект попадает в область, в которой напряжения равны нулю. В этом случае для получения достаточно большого сигнала от дефекта следует изменить моду волны или частоту, на которой ведется контроль.
Поверхность, через которую вводятся ультразвуковые волны, должна быть относительно ровной, не иметь выступов и выемок, мешающих перемещению искателя, поэтому удобнее контролировать заготовки изделий.
При контроле изделий по криволинейной поверхности радиусом 100— 150 мм призму наклонного искателя обрабатывают таким образом, чтобы радиус кривизны ее контактной поверхности был несколько больше радиуса кривизны поверхности изделия. При контроле таких изделий нормальным искателем используют искатели с прямоугольной пьезопластиной, ориентированной вдоль поверхности изделия. При контроле иммерсионным способом применяют фокусировку ультразвука.
Качество поверхности должно обеспечивать достаточно высокую стабильность акустического контакта между искателем и изделием, так чтобы изменения чувствительности не превышали 10%. При контроле контактным способом хорошие результаты получают при обработке по 6-му классу; допустимо снижение до 4-го класса, однако в этом случае рекомендуется применять специальные искатели. Благодаря применению щелевого иммерсионного и бесконтактного способов контроля снижаются требования к поверхности. Во всех случаях недопустимо наличие на поверхности отслаивающейся окалины, грубых неровностей или покрытий, препятствующих прохождению ультразвука.
При контроле контактным методом поверхность изделия покрывают вязкой, хорошо смачивающей жидкостью (машинным или трансформаторным маслом, глицерином, клейстером). В случае контроля иммерсионным и щелевым способами используют воду, освобожденную от пузырьков воздуха путем отстоя. Иногда в нее добавляют вещества (например, спирт) для улучшения смачиваемости поверхности изделия и ингибиторы (например, азотнокислый натрий), предохраняющие от коррозии.
При настройке аппаратуры руководствуются следующими основными рекомендациями.
Частоту ультразвуковых колебаний выбирают более высокой, но с учетом влияния затухания ультразвука в материале. Поэтому с целью достижения максимальной чувствительности частоту снижают с увеличением толщины изделия и повышением затухания ультразвука.
Чувствительность ультразвуковых дефектоскопов обычно выбирают ниже максимально возможного значения. Часто она указывается в технической документации на контроль. В случае необходимости чувствительность устанавливают экспериментально по результатам контроля опытной партии изделий.
В процессе поиска дефектов при ручном (а иногда также при автоматическом) контроле чувствительность увеличивают в 1,5—2 раза но сравнению с требуемым значением (поисковая чувствительность).
Скорость и задержку развертки эхо-дефектоскопа регулируют таким образом, чтобы линия развертки соответствовала всему пути ультразвука в изделии. Изделия большой толщины иногда контролируют но слоям, т. е. изделие по толщине разбивают на несколько зон, которые проверяют последовательно при соответствующей регулировке системы развертки и чувствительности.
КОНТРОЛЬ ЛИТЬЯ
Ультразвуковой контроль литья производится эхо- и зеркально-теневым методами обычно с помощью нормальных искателей [27]. Дефекты литья (поры, раковины, шлаковые включения) имеют объемный характер и могут быть обнаружены при прозвучивании с разных сторон. Поэтому контроль ведут, как правило, в одном направлении по кратчайшему расстоянию от поверхности, удобной для ввода ультразвука. Однако имеются опасные зоны, которые должны быть проверены в направлении, перпендикулярном к плоскости наиболее вероятного развития трещин. Кроме того, в литье встречаются волосовидные дефекты, плохо отражающие ультразвук. О наличии таких дефектов судят по ослаблению донного сигнала.
Ввиду того что поверхность литья шероховатая и сложной формы, целесообразно применять специальные искатели для контроля грубой поверхности. Вогнутые радиусные переходы удобно контролировать искателями с локальной ванной в форме катка.
Ультразвуковому контролю следует подвергать стальное литье после высокотемпературной термической обработки, измельчающей структуру. Частота ультразвуковых колебаний 1—2 МГц. Удовлетворительно контролируются без термообработки изделия (например, трубы), отлитые центробежным способом.
Чувствительность дефектоскопа обычно настраивают по плоскодонным отверстиям площадью 7—80 мм2, в зависимости от технических требований. Иногда для оценки дефекта сравнивают сигнал отражений от дефектов с донным, например допускаются дефекты, высота эхо-сигнала от которых не превышает определенной части донного сигнала в месте расположения дефекта.
Дефекты литья выявляются радиационным просвечиванием, поэтому целесообразно проводить 100%-ный ультразвуковой контроль, а допустимость выявленных дефектов оценивать по результатам радиографического контроля отмеченных участков.
Чугун проверяется хуже, чем стальное литье. Эхо-методом удается контролировать чугун со сфероидальным графитом при толщине изделий не более 100—200 мм. Для уменьшения затухания ультразвука работают на пониженных частотах (0,5—1,5 МГц).
Эхо-метод применяют для обнаружения грубых дефектов в слитках из различных металлов и сплавов, предназначенных для изготовления ответственных изделий. Простая форма слитка благоприятствует контролю. Однако слитки имеют крупнозернистую структуру, что требует понижения частоты и снижает чувствительность метода контроля. Слитки из углеродистой стали могут быть прозвучены на толщину до 1 м при частоте 0,25—1 МГц. Слитки из легированной стали прозвучиваются значительно хуже. Слитки из титановых и алюминиевых сплавов могут быть проконтролированы на глубину более 1 м при частоте 1—1,5 МГц. Для обеспечения акустического контакта вдоль боковых поверхностей слитка зачищают полосы шириной 50—70 мм от окалины и других неровностей.
Контроль поковок и штамповок
Поковки (типа роторов и дисков турбин, заготовок штампов, станин, валов, детали самолетов, в том числе из легких сплавов, и т. п.) контролируют эхо-методом [5, 7, 11, 27]. В этих изделиях могут быть выявлены флокены, остатки усадочных раковин, инородные включения, окисные плены, ликвационные скопления и другие внутренние дефекты, которые практически невозможно обнаружить просвечиванием. Контроль (ГОСТ 12503—67) ведется при частоте 2—5 МГц. В первую очередь нормальным искателем (рис. 68) контролируют по поверхности, со стороны которой производился последний этап ковки, так как большинство дефектов расположено параллельно этой поверхности. Нормальными искателями проверяют также по другим поверхностям. Наклонными искателями контролируют участки, опасные ввиду возможного возникновения трещин, которые не удается проверить нормальными искателями во всех направлениях. Для удобства поверхность крупных поковок разбивают на участки.
Обычно эквивалентный размер дефектов, подлежащих регистрации, определяется амплитудой отражения от плоскодонного отверстия площадью 0,75— 7 мм2 Недопустимыми считают дефекты с эквивалентным размером 7—20 мм2. Кроме того, накладываются ограничения на условную протяженность дефектов, их количество, расстояние между дефектами.
Контроль штамповок производится эхо-методом продольными волнами при частоте 2—5 МГц. Направление ультразвуковых волн рекомендуется перпендикулярное к направлениям волокон металла. В этом случае эффективно применение иммерсионных установок, в которых искатель автоматически ориентируется в требуемом направлении. Для контроля некоторых типов штамповок (лопаток турбин и компрессоров, камер сгорания турбин) успешно используют волны Релея и Лэмба.
КОНТРОЛЬ ПРОКАТА И ПРОВОЛОКИ
Листы и плиты толщиной более 50—100 мм контролируют эхо-методом. Достаточно высокая производительность контроля обеспечивается применением дефектоскопической установки в виде тележки, которую контролер катит перед собой. На тележке расположены искатели нормального типа на частоту 2—2,5 МГц со щелевым контактом, а также укреплены дефектоскоп и бачок с контактной жидкостью.
Более тонкие листы (5—60 мм) контролируют либо теневым, либо эхо-методом В первом случае лист погружают в ванну с жидкостью. Он проходит между двумя траверсами, на которых укреплены излучающие и приемные искатели.
Контроль листов и плит в горячем состоянии позволяет своевременно выявить часть изделия, подлежащую обрезке. Наиболее перспективным способом контроля при 900—1100° С является способ, при котором искатели расположены в канале специальных валков прокатного стана. Акустический контакт осуществляется за счет прижатия валка к поверхности листа под большим давлением.
Бесшовные трубы из сталей, сплавов и цветных металлов проверяют эхо-методом в соответствии с ГОСТ 17410—72. Для контроля применяют автоматические иммерсионные установки. Труба проходит через локальную ванну с сальниками, в которой в нее вводят ультразвуковые колебания. Трубы диаметром менее 50—100 мм обычно проверяют фокусирующими искателями.
Для надежного выявления различно ориентированных дефектов трубы наиболее ответственного назначения контролируют волнами, посылаемыми в четырех различных направлениях: в двух по окружности и двух вдоль оси трубы.
Углы наклона искателей выбирают экспериментально. Они соответствуют наилучшей выявляемости внутренних или наружных искусственных дефектов (а иногда обоих одновременно). В качестве искусственных дефектов используют риски прямоугольного или треугольного сечения. В зависимости от технических требовании к качеству труб глубина рисок составляет 3—15% от толщины стенки трубы, а длина 1—50 мм. Браковочным признаком является превышение амплитудой сигнала от дефекта амплитуды сигнала от риски, но которой настраивают аппаратуру. В трубах большого диаметра (100—500 мм) нормальным искателем выявляют дефекты типа расслоения.
Для проверки всего металла трубы необходимо обеспечить взаимное перемещение искателя и трубы по винтовой линии. Более производительным является способ, при котором искатели вращаются вокруг поступательно движущейся трубы. Установка, в которой труба совершает одновременно вращательное и поступательное движения менее производительна, но позволяет проверять трубы в более широком диапазоне диаметров.
Установки для контроля труб могут быть использованы для дефектоскопии прутков. При этом искатели располагают так, чтобы обеспечить нормальный к поверхности ввод лучей. Поверхностные дефекты прутков целесообразно выявлять поверхностными волнами.
Основная часть дефектов прутка (остатки усадочной раковины, трещины) располагается в его центральной части. Для их надежного выявления независимо от положения в ультразвуковых установках три искателя располагают вокруг прутка так, чтобы их оси сходились в центре прутка. Угол между осями 60°. При этом пруток движется поступательно.
Прутки диаметром 10—50 мм проверяют на установках типа УДЦ-25 с локальной иммерсионной ванной. Для сокращения мертвой зоны в установке применены раздельно-совмещенные искатели.
Трубные заготовки диаметров 50—250 мм контролируются на установке типа УДЦ-18ТЗ, которая монтируется на обдирочном станке. Она содержит три лыжи с искателями, прижимаемыми пружинами к поверхности заготовки. Акустический контакт осуществляется через щель, заполняемую эмульсией, питающей обдирочный станок.
Для контроля проволоки применяются волны стержневого типа. Проволока, перематываясь между двумя катушками, проходит через локальную иммерсионную ванну, в которой проверяется теневым или эхо-методом с производительностью 0,5-1 м/с.
Прокат со сложным профилем поперечного сечения контролируют эхо-методом теневым и зеркально-теневым методами при частоте 2,5—5 МГц. Акустический контакт осуществляется иммерсионным или щелевым способом. Искатели располагают так, чтобы обеспечить выявление наиболее опасных или чаще встречающихся дефектов, например трещин и закатов в радиусных и галтельных переходах. Система искателей и изделие движутся относительно друг друга поступательно. Поперечное движение искателей обычно не предусматривается.
Прокатом сложного профиля являются рельсы. В соответствии с ГОСТ 18576—73 их контролируют зеркально-теневым и эхо-методами. Ультразвук вводится со стороны поверхности катания головки рельса .
Как правило, дефекты в шейке рельса и вблизи мест ее перехода в головку и подошву — вертикальные и горизонтальные трещины и расслоения. Их выявляют зеркально-теневым методом с помощью прямого искателя по первому и второму донным импульсам или по их отношению.