Пресс-формы для литья под давлением. Справочное пособие
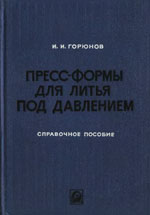
Горюнов И. И.
Машиностроение, 1973 г.
КОНСТРУКЦИИ, ПРОЕКТИРОВАНИЕ И ИЗГОТОВЛЕНИЕ ПРЕСС-ФОРМ
КЛАССИФИКАЦИЯ ПРЕСС - ФОРМ
Пресс-формы, применяемые при литье под давлением для изготовления отливок, можно разделить на два класса: 1) неунифицированные и ненормализованные или обычные; 2) унифицированные и нормализованные. На нормализованные детали, узлы, механизмы и конструкции пресс-форм составляются заводские или отраслевые нормали, а на унифицированные — разные другие технические документы.
Простейшие неунифицированные (обычные) пресс-формы состоят из вкладышей матриц и пуансонов и направляющих колонок. Вкладыши имеют заплечики для крепления их специальными болтами или крепежными планками специального профиля. Выталкивание отливок в них осуществляется поршнем плунжера. Наряду с простейшими изготовляются пресс-формы различной степени сложности вплоть до уникальных, имеющих большое количество стержней, расположенных параллельно и перпендикулярно плоскости разъема пресс-форм, механизмы автоматического регулирования температуры и другие механизмы. Трудоемкость изготовления и стоимость таких пресс-форм очень высоки.
Унифицированные и нормализованные пресс-формы более экономичны и производительны, поэтому они постепенно вытесняют обычные неунифицированные. Унифицированные и нормализованные пресс-формы применяются при массовом и мелкосерийном производствах, где в одном блоке отливается несколько наименований деталей, для каждой из которых изготовляются свои вкладыши или пакеты; по мере их износа они заменяются дублерами.
Унификация и нормализация пресс-форм производится практически на всех заводах, занимающихся литьем под давлением, поэтому существует несколько направлений по конструктивному их оформлению и по терминологии. По имеющейся классификации можно выделить следующие группы пресс-форм:
1) состоящие из унифицированных или нормализованных вкладышей или пакетов и блоков к ним, которые называют блок-формой и формоблоком;
2) состоящие из нормализованных или унифицированных пакетов и унифицированных постаментов к ним;
3) изготовляемые из универсальных сборных узлов (УСФ).
В зависимости от конструкции отливок различают пресс-формы для изготовления деталей с резьбой, армированных деталей, крышек и т. д. Например, пресс-формы для изготовления деталей, имеющих резьбу, можно классифицировать по следующим признакам:
а) по расположению резьбы — на пресс-формы для отливки деталей с наружной резьбой, с внутренней резьбой и с наружной и внутренней резьбой;
б) по величине резьбовой поверхности — на пресс-формы для отливки деталей с резьбой по всей окружности и с резьбой по полуокружности;
в) по способу оформления резьбы — на пресс-формы для получения отливок с резьбой в неразъемных и в разъемных резьбообразующих элементах;
г) по способу вывинчивания отливок из резьбообразующих элементов — на пресс-формы с вывинчиванием отливок из резьбообразующих элементов и с вывинчиванием резьбообразующих элементов из отливок (вывинчивание производится как на машине, так и вне машины).
Пресс-формы для изготовления армированных отливок можно классифицировать по следующим признакам;
1) по материалу, применяемому в качестве армирующего элемента (цветные и черные металлы, специальные сплавы, пластмассы, керамика, дерево, фибра и другие материалы);
2) по количеству армирующих элементов (один или несколько) (в п. 4 приводился пример отливки весом 75 кг, имеющей 50 вес. % армирующих элементов) ;
3) по расположению армирующих элементов в рабочей полости: параллельно, перпендикулярно плоскости разъема и под углом;
4) по форме армирующих элементов (элементы типа штифтов, шпилек, болтов, осей, втулок, гаек, гладких втулок, подшипников и других фигур различных сложных конфигураций).
Пресс-формы для изготовления деталей при мелкосерийном производстве при групповой технологии разделяются по габаритам — площади проекции отливки на поверхность разъема пресс-формы; по подводу литника к отливке; по типу съема отливки из пресс-формы; по поверхности разъема отливки.
Пресс-формы классифицируются также в зависимости от конструкции и мощности машин, габаритных размеров плит для их крепления, хода подвижной плиты.
По линии разъема различают пресс-формы с вертикальным разъемом для машин с вертикальным расположением плит и пресс-формы с горизонтальным разъемом — для машин с горизонтальным расположением плит. Указанные пресс-формы могут быть одноразъемные и многоразъемные. Машины с горизонтальным расположением крепежных плит очень неудобны для эксплуатации пресс-форм и поэтому они применяются в ограниченном количестве.
По габаритным размерам и весу пресс-формы подразделяются на мало-, средне- и крупногабаритные. По высоте и ширине пресс-формы изготовляются с размерами до 4000X4000 мм, третий размер зависит от допустимого хода машины и размера отливки в этом направлении. Максимальный вес отливок, получаемых литьем под давлением, находится в пределах 25—45 кг, но, как указывалось выше, известны и более тяжелые армированные отливки, вес которых за счет арматуры достигает 75 кг. Так, на заводе им. Егорова (Ленинград) изготовлялись отливки из сплава АЛ9В с размерами 1108Х962Х 18 мми весом 5 кг, для которых пресс-форма имела размеры 1310X 1170X340 мм и вес 4800 кг. На этом же заводе для крупногабаритной отливки из сплава АЛ2 с размерами 1225x580X 15 мми весом 6 кгбыла изготовлена и эксплуатировалась пресс-форма размерами 1700X580X545 мм и весом 4500 кг. Самая крупная пресс-форма размерами 3700Х3680Х 1070 мми весом 30 000 кгбыла изготовлена в США для отливки блока 6-цилиндрового двигателя.
Пресс-формы в зависимости от количества отливок, изготовляемых в ней, разделяются на одногнездные и многогнездные (в некоторых пресс-формах изготовляется до 50 и более мелких отливок). В зависимости от способа подогрева и охлаждения пресс-формы изготовляются как с регулированием температуры (автоматическим и полуавтоматическим), так и без регулирования температуры. Автоматическое регулирование температуры пресс-форм возможно при использовании жидких теплоносителей, в том числе и металлических, или электрических нагревателей, применяемых совместно с водяным охлаждением. Полуавтоматическое регулирование температуры осуществляется с помощью электрических и других нагревателей.
Пресс-формы изготовляются с автоматическим, полуавтоматическим или ручным приводами для съема отливок и извлечения стержней из отливки. Автоматический привод, использующий ход машины, применяется для съема отливок плитой или выталкивателями. Для крепления подвижной части пресс-формы и фиксации системы выталкивателей иногда используются постаменты.
Автоматические приводы для съема стержней подразделяются на механические и гидравлические. Механические приводы могут быть с наклонным клином, наклонным плоским клином, изогнутыми штырями, копирующими устройствами и другими механизмами. Полуавтоматический гидравлический привод предусматривает ручное управление. В качестве ручных применяются винтовые, рычажные, эксцентриковые, с зубчатыми колесами и другие приводы.
Пресс-формы в зависимости от основы сплавов, применяемых для изготовления отливок, имеют особенности в оформлении рабочей полости и в конструкции приводов выталкивателей и стержней.
По способу изготовления вкладышей, оформляющих внешние контуры отливки, пресс-формы очень разнообразны. Вкладыши изготовляются преимущественно механической обработкой из проката или поковок, но в последние годы применяются вкладыши, изготовляемые также другими способами: холодным выдавливанием, литьем по выплавляемым моделям, литьем под давлением и др.
По расположению рабочей полости для оформления внешних контуров отливки различают пресс-формы с расположением отливок только в матрице, только в пуансоне или в пуансоне и матрице.
В последнее время внедряются пресс-формы с удалением литников и облоя в процессе съема отливки, с автоматической очисткой рабочей полости и автоматическим нанесением на нее смазки.
Детали пресс-формы по их назначению можно разделить на следующие группы.
Группа I. Детали, формообразующие рабочую полость пресс-формы: вкладыши матриц и пуансонов, вставки или куски, стержни и выталкиватели.
Группа II. Детали металлопровода: стакан, втулка, наконечник прессующего плунжера, пятка и рассекатель.
«Группа III. Детали конструктивного назначения: плиты или обоймы матриц и пуансонов, плиты толкателей, опорные и подкладные, направляющие колонки и втулки, упоры, различные детали узлов и механизмов. Эта группа содержит очень много различных наименований деталей, и чем сложнее пресс-форма, тем их больше.
Детали группы I определяют стойкость пресс-форм и качество отливок по чистоте и точности размеров. Детали групп II и III определяют работоспособность пресс-форм. Конструкции этих деталей и качеству материалов, применяемых для их изготовления, необходимо уделять самое большое внимание.