Предупреждение дефектов листового проката
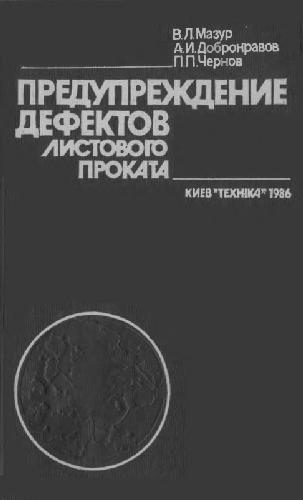
В. Л. Мазур, А. И. Добронравов, П. П. Чернов
Техника, 1986 г.
ПРЕДУПРЕЖДЕНИЕ ДЕФЕКТОВ НА ПОВЕРХНОСТИ ПОЛОС ПРИ ХОЛОДНОЙ ПРОКАТКЕ СТАЛИ
Анализ показателей работы отечественных непрерывных широкополосных станов холодной прокатки свидетельствует, что доля их простоев, обусловленных порывами полос, составляет 20—40 % общего количества аварийных технологических простоев. При этом уменьшение производительности станов из-за названных простоев достигает 10—12 %. Порывы полос являются одной из основных причин получения разнотолщин-ного металла. Длина утолщенных участков полос в местах порывов достигает на станах холодной прокатки 25—30 м, а на станах прокатки жести — 40—50 м. Эти же участки, как правило, имеют повышенную пораженность поверхностными дефектами, обусловленную повреждением полос о проводковую арматуру и увеличением сваривания витков полосы в рулонах при отжиге их в колпаковых печах.
Практика показывает, что основной причиной порывов прокатываемых полос являются дефекты подката (в первую очередь поверхностные). Например, на пятиклетевом стане 1700 холодной прокатки КарМК доля порывов из-за поверхностных дефектов составляет 55 %, а на шестиклетевом стане бесконечной прокатки жести 1400 того же комбината — 80 % общего количества порывов. В то же время одинаковые дефекты поверхности могут в зависимости от технологических режимов холодной прокатки в одних случаях приводить к порывам полос, в других — нет.
Таким образом, исключить порывы можно путем устранения дефектов подката и совершенствования режимов холодной прокатки полос.
Все порывы полос при холодной прокатке в зависимости от вызывающих их причин могут быть условно разделены на три основные группы: порывы из-за дефектов сталеплавильного происхождения, обусловленных нарушениями технологии выплавки, раскисления и разливки стали; порывы из-за дефектов поверхности подката, возникающих при горячей прокатке и травлении полос; порывы, обусловленные нерациональной технологией непосредственно холодной прокатки полос (вследствие неблагоприятных режимов обжатий, натяжений, профи-лировок валков).
Основными дефектами сталеплавильного происхождения, опасными с точки зрения порывов полос, являются раскатанный пузырь, слиточная плена, расслоение, неметаллические включения (волосовины).
Раскатанный пузырь—результат вскрытия при горячей или холодной прокатке несплошностей в местах наличия незаварившихся подкорковых пузырей слитка. Он имеет вид поверхностных вздутий и чешуйчатых отслоений, вытянутых по направлению прокатки. На образцах порывов полос по раскатанному пузырю, как правило, обнаруживаются строчечные сквозные разрывы в местах расположения дефекта.
Дефект слиточная плена на холоднокатаных полосах проявляется в виде единичных крупных отслоений металла. Нижняя поверхность плены загрязнена частицами различных окислов. Порывы полос по пленам имеют вид крупных сквозных разрывов по месту расположения этих дефектов. Порывы полос по раскатанному пузырю и слиточной плене происходят преимущественно при локализации дефектов в прикромочных зонах полос.
Дефекты расслоение и волосовина образуются при наличии в стали значительного количества крупнозернистых неметаллических включений. Волосовины образуются при залегании включений рассредоточенными группами у поверхности полос. На холоднокатаном металле волосовины имеют вид вытянутых вдоль направления прокатки узких нарушений сплошности поверхности или разнотональных дорожек. В местах порывов полос обнаруживается цепочка сквозных разрывов. Дефекты расслоение образуются при залегании крупных скоплений неметаллических включений на значительной глубине по толщине полос.
Порывы полос по расслоению имеют вид гармошки с крупными сквозными разрывами, расположенными преимущественно на средних по ширине участках полос. В поперечном сечении явно различаются два слоя металла, которые в большинстве случаев расщепляются.
Характерный вид участков полос в местах порывов по основным дефектам сталеплавильного происхождения и микроструктура металла в зоне дефектов показаны на рис. 16.
Причины возникновения и рекомендации по исключению образования дефектов сталеплавильного происхождения в достаточной степени известны [10; 29]. На металлургических предприятиях для предупреждения указанных дефектов при производстве холоднокатаного листа и жести широко используются следующие основные мероприятия: регламентирование температуры и степени окисленности металла при разливке; применение для раскисления металла ферромарганца с нормированным содержанием кремния (менее 2,0 %); разливка металла в изложницы, оборудование манжетами; разливка стали с использованием интенсификатора кипения на основе порошковой окиси железа; отсечка конечного шлака механическим и химическим способами; исключение оплавления и пересижива-ния слитков в нагревательных колодцах слябинга.
Как уже говорилось выше, основными дефектами поверхности, возникающими при горячей прокатке и травлении полос, являются вкатанная окалина, раковины, отпечатки, повреждения, обусловленные повреждением полос при транспортировании и намоточных операциях (риски, царапины, забоины, продиры).
Царапины и продиры на поверхности холоднокатаных листов, а также на листовом прокате другого назначения часто образуются вследствие относительного смещения витков при сматывании и разматывании рулонов протравленных полос.
Эти дефекты не только ухудшают качество поверхности листовой продукции, но и являются причинами порывов полос при холодной прокатке. Исследования, выполненные на Магнитогорском металлургическом комбинате, показали [47], что чем больше толщина подката и выше концентрация поверхностно-активных веществ в смазке, используемой для промасливания горячекатаных полос после травления, тем меньше царапин образуется на поверхности холоднокатаной стали. На Череповецком металлургическом комбинате для уменьшения количества царапин и продиров горячекатанные полосы после травления перед смоткой в рулоны промасливают эмульсией АНСК-50 концентрацией 7—9 %, которая создает на поверхности стали антизадирную пленку. Такое промасливание в несколько раз уменьшает отбраковку холоднокатаных полос из-за дефектов,
связанных с повреждением поверхности металла при относительном смещении витков в рулонах [26]. Аналогичные результаты получены на металлургическом комбинате «Запорожсталь» при использовании в качестве промасливателя эмульсии полимеризованного хлопкового масла [41].
Типичные виды участков металла с зарождающимися очагами разрушений, возникающих из-за наличия на подкате указанных дефектов и приводящих к порывам полос при холодной прокатке*, показаны на рис. 17. Для большинства дефектов данной группы характерно образование и развитие при холодной прокатке микротрещин и надрывов в деформируемом металле, которые являются потенциальными источниками порывов полос.
При прокатке дефектного участка из-за локальной разнотолщинности металла в зоне дефекта деформация его неравномерна по ширине и толщине полосы. Поверхностные объемы металла, имеющего раковины, царапины, продиры и другие аналогичные дефекты, получают меньшую относительную деформацию, в результате чего в них возникают растягивающие напряжения. При достижении растягивающими напряжениями величины предела прочности деформируемого металла на его поверхности в зоне дефекта образуются микротрещины. Если растягивающие напряжения достигают величины предела прочности по всей толщине прокатываемого металла, то в зоне дефекта образуется сквозной разрыв, который в свою очередь является концентратором напряжений и потенциальным источником порыва полосы.