Пособие мастеру цеха гальванических покрытий
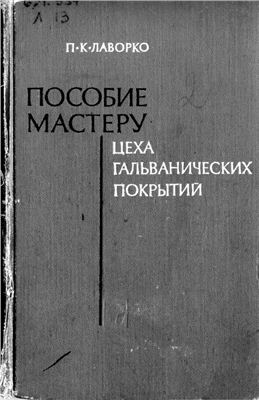
Лаворко П.К.
Машиностроение, 1969 г.
МЕТОДЫ ЭЛЕКТРОЛИТИЧЕСКОГО ОСАЖДЕНИЯ МЕТАЛЛОВ
ЦИНКОВАНИЕ
Цинк — металл серебристо-белого цвета, в сухом воздухе почти не изменяется, во влажном воздухе с содержанием углекислоты и в воде он окисляется и покрывается пленкой из основной углекислой соли, которая защищает цинк от дальнейшего разрушения. Удельный вес цинка 7,1 г/см3, атомный вес 65,4, температура плавления 419° С, электрохимический эквивалент 1,22 Г/а-ч. Цинк очень легко растворяется во всех кислотах и едких щелочах.
Цинковые покрытия относятся к защитным покрытиям, они хорошо защищают железоуглеродистые сплавы (сталь и чугун) от коррозии, потому что цинк — металл более электроотрицательный, чем железо. Нормальный потенциал цинка — 0,76 в. Поэтому в гальванической паре железо—цинк в присутствии влаги цинк, будучи анодом, растворяется, защищая этим самым основной металл.
Однако цинковые покрытия, защищая сталь, сами подвергаются коррозии, переходя в различные химические соединения цинка, не дающие хорошей защиты от коррозии. Поэтому, чем большую толщину будет иметь цинковое покрытие, тем оно даст более надежную и длительную защиту от коррозии.
Наилучшим видом подготовки поверхности при покрытии цинком является пескоструйная очистка, хотя может быть применено и травление или какая-либо механическая обработка, дающая чистую матовую поверхность (крацевание).
Цинковые покрытия широко применяются для защиты изделий из черных металлов от коррозии в различных климатических зонах и в атмосфере, загрязненной промышленными газами, для защиты от непосредственного влияния
пресной воды и от коррозионного воздействия керосина, бензина и других нефтяных продуктов и масел.
В среде, насыщенной морскими испарениями, покрытия цинком не стойки.
Для повышения защитных свойств цинковых покрытий применяется пассивирование в растворах хромовокислых солей или хромового ангидрида — так называемое хроматирование, а также фосфатирование и дополнительная окраска лаками и эмалями. После хроматирования покрытия приобретают желтоватый, радужный оттенок с цветами побежалости.
Цинковые покрытия хорошо выдерживают изгибы, развальцовку и плохо — запрессовку; при температуре выше 250° С и ниже минус 70° С они становятся хрупкими.
Толщина цинковых покрытий назначается в зависимости от условий эксплуатации изделий.
Так, при службе изделий в условиях сухих, отапливаемых помещений толщина покрытия должна быть 6—9 мк, для эксплуатации под навесом и в помещениях с переменной температурой и влажностью 15—18 мк, для защиты от коррозии в атмосферных условиях 24— 30 мк, для особо жестких условий толщину покрытий увеличивают до 36—42 мк.
Для резьбовых и крепежных деталей толщину слоя цинка назначают в пределах 3—12 мк в зависимости от их диаметра, шага резьбы и класса точности.
Для защиты стальных деталей, эксплуатируемых в атмосферных условиях с повышенной влажностью и в морском климате, применяют цинкование с последующим фосфатированием и лакокрасочным покрытием, толщина слоя цинка в этом случае 6—9 мк.
Цинкование производится в электролитах разных типов: кислых, цианистых, щелочных, так называемых цинкатных, аммиакатных и др. Для цинкования применяются прокатанные цинковые аноды марок Ц0, Ц1 и Ц2 (ГОСТ 3640—65).
При цинковании в кислых электролитах можно применять токи высокой плотности и получать высокий (до 100%) выход металла по току, однако рассеивающая способность их несколько мала.
Цинковые покрытия, полученные в кислых электролитах, имеют светлый цвет, характеризуются пластичностью и прочным сцеплением с основным металлом и могут выдержать различную механическую обработку. Поэтому для покрытия малорельефных изделий, а также полуфабрикатов — листов, проволоки, полос и др., подвергающихся в дальнейшем механической обработке, следует применять для цинкования кислые электролиты.
Цианистые электролиты отличаются хорошей рассеивающей способностью и осадки из них обладают более высокой антикоррозионной стойкостью. Однако цианистые электролиты не позволяют применять относительно высоких плотностей тока и дают низкий выход по току, не превышающий 70—75%. Недостатком цианистых электролитов является то, что они весьма ядовиты и состав их не постоянен вследствие разложения цианистых соединений в процессе работы. Цианистые электролиты применяют главным образом для покрытия изделий с глубоким рельефом, требующих особо надежной противокоррозионной защиты. Детали, имеющие сварные швы, также следует покрывать в цианистых электролитах.
Щелочные нецианистые электролиты (цинкатные) обладают более низкой рассеивающей способностью, чем цианистые.
Плотность тока при работе в этих электролитах приходится регулировать в сравнительно небольших пределах; кроме того, цинкатные электролиты склонны к образованию губчатых осадков и требуют подогрева электролита.
Кислые электролиты.
Основной солью для кислых ванн является сернокислый цинк, обладающий высокой растворимостью.
Для улучшения качества отложений в состав электролита вводятся соли, повышающие электропроводность раствора, например сернокислый натрий, сернокислый алюминий, иногда и хлористые соли — хлористый цинк, хлористый аммоний и др. Введение добавок сернокислого алюминия или алюмокалиевых квасцов способствует осаждению более светлого и блестящего цинка; кроме того, это соединение играет роль буферного вещества, регулируя изменение кислотности.
Применение сернокислого алюминия или квасцов имеет то преимущество, что при защелачивании и увеличении рН электролита выше 4,0—4,5 выпадает хлопьевидный осадок гидрата окиси алюминия, весьма заметный в растворе и сигнализирующий необходимость подкисления электролита.