Порошковая металлургия и напыленные покрытия
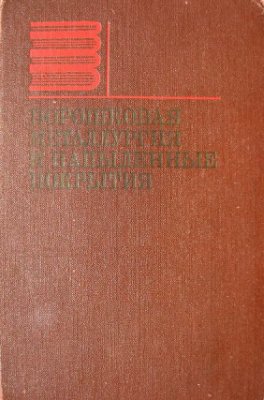
Анциферов В.Н., Бобров Г.В., Дружинин Л.К.
Металлургия, 1987 г.
ПОРОШКОВАЯ БЫСТРОРЕЖУЩАЯ СТАЛЬ
Применение метода порошковой металлургии к получению изделий из быстрорежущей стали позволяет избежать характерных для этой стали явлений карбидной неоднородности, использовать специфическое неравновесное состояние металла.
Использование порошковой быстрорежущей стали открывает широкие перспективы дальнейшего повышения качества инструментальных сталей и стойкости режущего инструмента. Порошковые быстрорежущие стали имеют перед сталями обычной металлургической технологии целый ряд преимуществ, главными из которых являются пониженная склонность к росту зерна, равномерное распределение и дисперсность карбидной фазы, повышенная шлифуемость, более высокий уровень механических и эксплуатационных характеристик. Существуют различные схемы производства порошковых материалов, однако применительно к быстрорежущим сталям наибольшее распространение получила технология, предусматривающая распыление жидкой стали инертным газом (азотом высокой чистоты) с последующим компактированием порошка крупностью 800—0 мкм в плотные заготовки.
Для получения порошка быстрорежущей стали ее расплавляют в индукционной печи при температуре 1600—1650 °С и через приемную воронку и форсуночное устройство сливают в камеру распыления. Кристаллизация капель жидкого металла происходит со скоростью 103—104 °С/с. В таких условиях в частицах порошка формируется высокодисперсная микроструктура. Исследование порошковых частиц на растровом микроскопе после того, как в них была растворена металлическая составляющая, показало, что карбидная фаза представляет собой своеобразный каркас, сохраняющий форму частиц порошка. Распыленные порошки быстрорежущей стали имеют низкую прессуемость. Известные способы получения заготовок из порошковых материалов даже при значительных давлениях (1,2—2,0 ГПа) и высокой температуре спекания (1200 °С) оказались неприемлемыми для получения качественных заготовок (пористость достигала 10—15 %). Компактные заготовки порошковой быстрорежущей стали получают методом горячего изостатического прессования с последующей горячей экструзией. При использовании только горячего изостатического прессования структура стали отличается неоднородностью: четко видны отдельные частицы, сохраняется карбидная сетка и т. д. Механические свойства стали остаются достаточно низкими, так, для стали Р6М5К5 предел прочности при изгибе составляет 1500—1800 МПа, а ударная вязкость равна 0,05— 0,08 МДж/м2. Последующая горячая пластическая деформация (ковка, пропитка, экструзия) обеспечивает однородность микроструктуры и высокий уровень механических свойств. При этом общий коэффициент вытяжки должен быть не менее 10, иначе в микроструктуре стали сохранятся отдельные вытянутые частицы порошка с недостаточно разбитой исходной карбидной сеткой.
Микроструктура порошковой быстрорежущей стали, полученной методами ГИП, ГГП и последующей горячей деформацией, характеризуется высокой дисперсностью и однородностью распределения карбидной фазы, что недостижимо в металле обычней металлургической технологии. Средний размер карбидов составляет 0,6—0,8 мкм, а максимальный не превышает 2—3 мкм. Мелкие равномерно распределенные карбиды снижают склонность порошковой быстрорежущей стали к росту зерна. При правильно выбранном режиме закалки зерно аустенита получается не крупнее № 11—12 по ГОСТ 5639—82.
Испытания эксплуатационных свойств в производственных условиях показали, что стойкость инструмента из порошковой быстрорежущей стали в 1,5—3 раза выше, чем у инструмента из той же стали обычной выплавки. Наибольший эффект достигнут при резании труднообрабатываемых материалов.
Для реализации преимуществ порошковой быстрорежущейстали, т. е. получения металла с более высокими механическими, технологическими и эксплуатационными свойствами, чем у обычного металлургического производства, новая технологиядолжна обеспечивать отсутствие или минимальное развитие и
специфических дефектов металла, свойственных методу порошковой металлургии.
Одним из основных условий получения высококачественной порошковой быстрорежущей стали является высокое качество исходного порошка. Порошок должен обладать однородным химическим составом, достаточно высокими значениями насыпной плотности и текучести, минимальным содержанием кислорода, неметаллических включений. Показатели качества зависят от метода получения порошка распылением жидкого металла и технологических параметров выплавки и распыления.
Кроме высокого качества исходного порошка, технология производства порошковой быстрорежущей стали должна обеспечивать отсутствие дефектов, связанных с подготовкой капсул для горячего изостатического прессования и компактированием материала. К этим дефектам относятся слоистость, ликвация серы в микроструктуре, оксидные пленки по границам частиц порошка, а также поры.
Слоистость в микроструктуре порошковой быстрорежущей стали выражается в появлении четко выраженных концентрических слоев с различной травимостью металла. Дефект образуется, в результате разделения порошка на крупные и мелкие фракции в процессе заполнения и виброуплотнения капсулы. На микрошлифах заготовок из капсул с таким расслоением зоны крупного порошка характеризуются большей травимостью, чем зоны мелкого порошка. Для устранения дефекта необходимо не допускать разделения порошка на фракции.
Ликвация серы проявляется в виде локальных растравов поверхности микрошлифов. Иногда локальные растравы имеют вид изогнутых линий, иногда сходны с трещинами. Изучение природы дефекта показало, что локальный растрав поверхности происходит по участкам скоплений тонких сульфидных включений, выделившихся по границам частиц порошка.