Пористость сварных швов и меры борьбы с ней
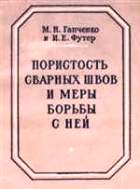
М. Н. Гапченко, И. Е. Футер
Гостехиздат, 1978 г.
ПРОИЗВОДСТВЕННЫЕ МЕРЫ БОРЬБЫ С ПОРИСТОСТЬЮ
МЕРЫ ПРЕДУПРЕЖДЕНИЯ ПОРИСТОСТИ
При изготовлении сварных конструкций борьба с пористостью сварных швов должна начинаться уже с первых стадий технологического процесса. Еще на складе должны быть приняты меры по защите металла от атмосферных осадков. После обработки детали должны быть очищены в местах сварки и вблизи них на расстоянии 20—30 мм от ржавчины, масла, краски и других загрязнений. Литые, подлежащие приварке детали, а также литье в местах дефектов, исправляемых сваркой, должны быть тщательно очищены от литейной корки и формовочной земли. Тонкие слой окалины после горячей прокатки удалять не обязательно, но окалина, остающаяся после нагрева для штамповки или отжига, должна быть удалена.
Производительным способом очистки металла является очистка пескоструйными аппаратами Однако она требует оборудования специальных камер и приводит к запылению производственных помещений. Для очистки мест сварки применяются переносные наждачные круги и электрические щетки. Стационарные наждачные круги применяются для легких деталей, например, для очистки заготовок под наплавку инструмента.
Ржавчина, масло, краска, окалина могут выжигаться. Для этой цели применяются обычные паяльные лампы, горелки для газовой сварки, подогревательное пламя газовых резаков, а также специальные многопламенные горелки. Последние с успехом применяются для очистки краски с металла старых конструкций в ремонтных работах и при очистке окалины с крупных штампованных деталей (например, днищ котлов и цистерн). Ржавчина при этом прокаливается, а менее опасный сухой ее остаток так же, как и окалина, легко отделяется от металла, благодаря различию в коэффициентах линейного расширения.
Серьезное внимание должно быть обращено на упаковку и хранение проволоки, предназначенной для автоматической сварки и изготовления электродов. Ржавчина и другие загрязнения с электродных стержней удаляются в специальных вращающихся барабанах, в которые стержни загружаются вместе с сухим песком или древесными опилками. Опилки применяются для снятия тонкого слоя смазки, которым стержни неизбежно покрываются при правке и рубке проволоки на правильно-рубильных станках. При сильном загрязнении маслом обезжиривание производится бензином или раствором каустической соды с последующей тщательной промывкой в воде и просушкой. Очистка бухт проволоки для автоматической сварки при сильном ее загрязнении значительно сложнее. Очистку можно осуществить травлением в 10%-ном растворе серной кислоты (лучше подогретой) с последующей нейтрализацией в растворе едкого натра, тщательной промывкой в воде и сушкой. Небольшие местные загрязнения можно удалить вручную наждачной бумагой во время перемотки бухт проволоки для зарядки кассет сварочных автоматов. Институтом электросварки разработан» специальная машина для этой цели. Очистку детален в местах сварки лучше всего производить за несколько часов до сборки и сварки конструкции, в особенности, если готовые изделия хранятся в сырых помещениях или на открытом воздухе.
Вне зависимости от того, производилась ли очистка деталей до их сборки, сварщик должен внимательно осмотреть подлежащие сварке места и очистить их от загрязнений, ибо при длительном хранении собранные узлы могут заржаветь и загрязниться маслом. Очистка собранных и прихваченных узлов производится ручными стальными щетками, переносными наждачными кругами и электрическими щетками. Такая очистка менее эффективна, чем очистка отдельных деталей, так как ржавчина забивается в зазоры между деталями и благодаря значительному скоплению в отдельных местах может вызвать сильную пористость. В соединениях внахлестку ржавчина вообще не может быть удалена в месте соприкосновения собранных деталей. Поэтому после очистки необходимо тщательно продуть зачищенные места и зазоры между деталями сжатым воздухом. В собранной конструкции наилучшие результаты дает прокаливание („выжигание") ржавчины пламенем газовой горелки. Им широко пользуются при автоматической сварке на монтаже. Полуавтоматическая сварка тонкой проволокой менее чувствительна к наличию ржавчины на свариваемых кромках и поэтому требует менее тщательной очистки металла. Достаточной оказывается обычная очистка металлической щеткой.
Применение двухслойной автоматической сварки, при которой первый слой шва, с целью выжигания ржавчины, сваривается на большой скорости, причем получается пористым, а второй слой дает окончательное сечение шва, нужно признать нерациональным, так как это резко снижает эффективность автоматической сварки, лишая ее одного из преимуществ — возможности однопроходной сварки швов больших сечений. Этот метод может быть оправдан в том случае, если на отдельных участках шва из-за повышенного зазора сварка производится первоначально на большой скорости, причем шов получается пористый.
Необходимо обратить внимание на контроль обмазок и флюсов согласно техническим условиям. Влажность флюсов не должна превышать 0,1%. Многие электродные обмазки обладаютповышенной гигроскопичностью. Флюсы также поглощают влагу из воздуха. Поэтому их надо хранить и теплых сухих помещениях. Полезно иметь непосредственно в сварочных цехах небольшие электрические печи сопротивления для просушки электродов и флюсов перед их применением. При работе в полевых условиях сушку электродов и флюсов производят на жаровне, а также используют тепло выхлопных газов двигателей внутреннего сгорания передвижных сварочных агрегатов. Для этой цели на выхлопную трубу двигателя надевается специальное устройство. При изготовлении электродов необходимо, чтобы толщина слоя покрытия находилась в пределах допусков, так как недостаточное количество расплавленного шлака на шве не только не обеспечивает полноты протекания необходимых химических реакций между металлом и шлаком, но ведет также к ускоренному охлаждению шва. Необходимо строго контролировать температуру прокалки электродов.
Прихватка при сборке под автоматическую сварку должна производиться электродами марки Э-42, Э-42А, Э-50. Даже при сборке под ручную сварку прихватки необходимо выполнять электродами той же марки, которыми будут свариваться швы. Автоматическая сварка по ручной подварке электродами марки Э-34 во всех случаях, когда автоматный шов может частично переплавить металл ручного шва, недопустима.
При сварке для каждого материала должны применяться электроды, флюсы и проволока проверенных типов, а режимы сварки должны быть тщательно отработаны. Хорошо поставленный технический контроль основных и вспомогательных материалов способствует получению беспористых швов. В процессе сварки необходимо создать условия, обеспечивающие максимальное выделение газов из жидкого металла сварочной ванны до затвердевания металла шва. Это может 43ыть достигнуто посредством замедления затвердевания жидкого металла и поддержания металла возможно» больше времени в жидком состоянии. Последнее можно осуществить достаточным прогревом основного металла. Для этого в большинстве случаев достаточна правильная техника сварки — соответствующие манипуляции концом электрода или горелкой, при которых получается хороший прогрев и провар кромок, подогрев затвердевающей части сварочной ванны, перемешивание металла в ванне.
Предварительный подогрев, проводимый при сварке и наплавке некоторых специальных, а также средне- и высокоуглеродистых сталей и при заварке дефектов стального и чугунного литья, наряду с предупреждением получения резких закалочных структур и образования трещин, способствует получению плотных швов. При наплавке инструмента и заварке дефектов литья рекомендуется применять ванный способ сварки, обеспечивающий получение плотных наплавок. При ручной сварке нужно следить за равномерным отложением шлака на шве. При автоматической сварке должна быть обеспечена равномерная засыпка флюса вдоль линии шва, так как при недостатке флюса дуга прорывается наружу, и шов становится пористым.
При дуговой сварке должна поддерживаться оптимальная для данной работы длина дуги, которая контролируется измерением напряжения на дуге. При газовой сварке должен поддерживаться требуемый характер пламени. При сварке в среде инертных газов, весьма важным является контроль чистоты применяемых газов, их расхода и техники сварки.