Получение комплексных ферросплавов из минерального сырья Казахстана
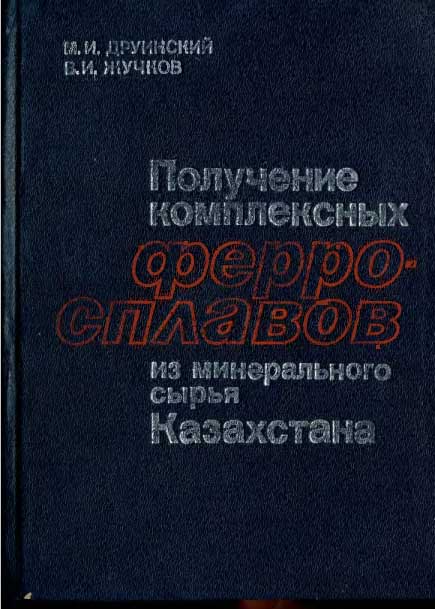
Друинский М.И., Жучков В.И.
Наука, 1988 г.
КАЧЕСТВЕННЫЕ ХАРАКТЕРИСТИКИ КОМПЛЕКСНЫХ
ФЕРРОСПЛАВОВ
1. ОСНОВНЫЕ ЗАДАЧИ ФЕРРОСПЛАВНОГО ПРОИЗВОДСТВА
Металлургия ферросплавов характеризуется большой номенклатурой продукции, связанной с многообразием элементов и композиций, разнообразием технологий и агрегатов для получения ферросплавов, промежуточным положением между сырьевой базой и потребителем, зависимостью от их возможностей и требований.
Основными задачами науки и практики ферросплавного производства на ближайшие годы являются:
— увеличение мощности, совершенствование и разработка новых типов электропечей, в первую очередь руднотермических;
— применение безотходных процессов с максимальным извлечением ведущих элементов;
— использование рациональных приемов подготовки шихтовых материалов к плавке, разливки и сортировки ферросплавов;
— улучшение качественных характеристик и сортамента ферросплавов;
— применение комплексной механизации и автоматизации ферросплавных агрегатов и цехов.
Тенденция увеличения мощности руднотермических ферросплавных печей наблюдалась практически во всех странах, за последние 10 лет единичная мощность печей возросла в 2—3 раза. Средняя мощность электропечи в СССР в 1970 г. составляла всего 12,7 ΜΒА, а вводимых в производство до 2000 г. составит около 40 MBА. Однако при повышении мощности возникают серьезные трудности: рост мощности происходит в основном за счет увеличения силы тока; уменьшается активное сопротивление ванны и увеличивается индуктивность печного контура, что приводит к снижению коэффициента мощности; ухудшаются условия эксплуатации электродов большого диаметра (более 2 м); усложняются условия протекания процесса, приводящие к снижению извлечения ведущих элементов и качества продукции; ужесточаются условия работы печного оборудования.
Повышению эффективности комплексной глубокой переработки сырья в ферросплавном производстве способствуют: применение подготовленной шихты (брикетированных совместно руды и восстановителя, предварительно восстановленной шихты), а также новых видов флюсов, увеличивающих активность элементов в шлаке, например щелочесодержащих флюсов; довосстановление отвальных шлаков; уменьшение механических потерь полезных компонентов при подготовке, транспортировке шихты, разливке и разделке сплавов и т. д.
Мало внимания уделяется подготовке шихты, разливке и сортировке полученных ферросплавов. В нашей стране практически не применяются окускованные материалы. В то же время за рубежом (США, Япония, ЮАР) брикетированную шихту используют для получения хромистых сплавов, ферросилиция. Эксперименты, проведенные советскими исследователями (А. П. Ем, С. И. Хитрик, А. Т. Хвичия и др.), показали эффективность применения брикетированной шихты при производстве ферросилиция, марганцевых и других ферросплавов.
Модернизация разливки поможет не только снизить отходы металла, улучшить качество слитка, но и повысить культуру производства, механизировать ручной труд.
Рациональное потребление ферросплавов, уменьшение их расхода и более стабильное усвоение сталью и чугуном требуют дробления и поставки ферросплавов по классам.
Несмотря на то что ферросплавы не применяются в качестве металлоизделий, от их состава и свойств (в основном потребительских) в значительной мере зависит качество основных конструкционных материалов — стали и чугуна.
В последние годы развитие конвертерного производства и связанного с ним ковшевого легирования, раскисления и модифицирования стали, выпуск высокопрочного чугуна вызвали во всем мире необходимость получения специальных комплексных ферросплавов. Однако в нашей стране их производство в промышленных масштабах не достигло нужного объема.
Механизация и автоматизация ферросплавного производства позволяют не только избавляться от тяжелых операций, но и увеличивать производительность агрегатов. Автоматизация только плавильных агрегатов может увеличить их производительность и снизить удельный расход электроэнергии за счет более ровного хода печи, устойчивого электрического режима до 10%.
2. КОМПЛЕКСНЫЕ ФЕРРОСПЛАВЫ
Качественные характеристики ферросплавов их сортамент и методы определения оптимального состава тесно связаны с качеством продукции черной металлургии и литейного производства, которые определяют требования к ферросплавам.
Наращивать производство стали предполагается путем развития кислородно-конвертерного и электросталеплавильного способов, расширения методов специального переплава и внепечной обработки металла. Проблема качества стали на стадии ее получения будет решаться путем выпуска массовых видов продукции с повышенным уровнем свойств за счет не только традиционного легирования, но и модифицирования редкоземельными и щелочноземельными металлами (ЩЗМ), повышения однородности и чистоты металла по вредным примесям [1].
При выплавке стали в кислородных конвертерах раскисление и легирование металла стремятся производить полностью в ковше, поскольку это уменьшает угар легирующих элементов и повышает производительность конвертера. Перенесение присадки ферросплавов из печи в ковш при выплавке углеродистой и низколегированной стали в мартеновских и электродуговых печах сопровождается повышением их производительности на 2—10%, понижением угара марганца π хрома в 1,5—2 раза, снижением содержания водорода и фосфора, улучшением макроструктуры, повышением пластичности и ударной вязкости стали [2]. Однако максимальное количество вводимых в ковш твердых ферросплавов может составлять не более 2—4% от массы стали из-за длительного растворения и неравномерного распределения элементов сплава в ковше, вызванного дефицитом тепла, необходимого для нагрева, расплавления и растворения ферросплавов. В связи с этим требуются ферросплавы, пригодные по своим служебным характеристикам для обработки жидкой стали в ковше.
В XII пятилетке и в последующие годы планируется увеличение выпуска литых деталей из чугуна и стали. Самое большое внимание будет уделяться качеству литья, проблеме снижения массы отливок, утоньшения их стенок. Однако постоянный дефицит кондиционных шихтовых материалов, переход на синтетический литейный чугун (из передельного с обработкой ферросилицием) и ряд других негативных причин затрудняют решение этих важных задач. Следует отметить, что до настоящего времени чугуна высокого качества, особенно высокопрочного (ВЧ), в нашей стране выпускается недостаточно.
Одним из основных путей увеличения выпуска чугуна высокого качества является расширение его модифицирования, для чего необходим выпуск достаточного количества ферросплавов-модификаторов, оптимального для каждой группы чугунов состава.
Таким образом, для коренного улучшения качества стали и чугуна необходимо иметь специальные ферросплавы, в первую очередь комплексные, обладающие необходимыми служебными характеристиками.
Комплексные (многокомпонентные) ферросплавы могут быть или только раскислителем (модификатором, легирующим сплавом), или совокупностью раскислителя и легирующего сплава, модификатора и раскислителя и т. д. Основу комплексных сплавов составляют железо, кремний, никель, алюминий и др.
С увеличением числа элементов в сплавах последние утрачивают универсализм. В то же время повышенное число компонентов позволяет легче получить требуемые служебные характеристики, снизить число присаживаемых марок сплавов.
Процесс получения комплексных сплавов имеет положительные и отрицательные стороны: расширяется рудная база их производства, поскольку в него могут вовлекаться более бедные и комплексные руды, появляется возможность более гибкого регулирования технологических параметров процесса (подбор вязкости, температуры плавления шлака и сплава, электросопротивления шихты и т. д.), однако ограничено количество теоретических и экспериментальных данных о физико-химических свойствах многокомпонентных металлических и оксидных систем, механизме и кинетике восстановления сложных шихт, затрудняется организация промышленного производства (хранение, дозировка повышенного количества компонентов шихты, ее расчетов) и т. д.
Совершенно очевидно, что преимущества комплексных ферросплавов существеннее их слабых сторон, о чем говорит и длительная практика их получения и применения. Продукция ферросплавного производства должна иметь оптимальное соотношение между двухкомпонентными ферросплавами (Fe—Si, Fe—Мn, Fe—Сr и др.) и комплексными сплавами.
Несмотря на значительную потребность в комплексных ферросплавах, они не получили широкого промышленного внедрения. Это связано в первую очередь с отсутствием обоснованного метода определения рационального состава комплексных и простых ферросплавов, критериев, по которым он находится, эффективной технологии получения сплавов.
Изучением физико-химических характеристик ферросплавов занимались многие авторы —И. П. Казачков, Б. М. Лепинских, М. И. Гаснк и др. [2—8].
Большинство исследователей при выборе оптимального состава ферросплавов исходят из их действия на качество и свойства обрабатываемого металла. По мнению [2], для выбора состава лигатур кроме сведений о механических и технологических свойствах стали представляют интерес данные о раскислительной способности лигатур. Есть мнение, что при разработке составов комплексных модификаторов необходимо учитывать особенности влияния входящих в них элементов на процессы структурообразования обрабатываемого металла, обусловленные различным сродством модификаторов к кислороду, сере, отличием в термодинамической активности на литую структуру, жидкотекучесть, физико-механические и другие свойства металла.
Ряд авторов при определении состава ферросплавов учитывают следующее: температуру плавления, плотность, технологические особенности и экономичность их получения, рассыпаемость, токсичность.
Предлагается и комплексный подход к выбору состава ферросплавов. Так, для определения эффективности воздействия активных элементов (ЩЗМ, Al, Si) А. С. Дубровин использовал величины упругости их паров и тепловых эффектов взаимодействия с другими элементами наряду с данными о технологических, экономических и экологических характеристиках. Ю. Я. Скок и др. об эффективности состава ферросплава судили по его влиянию на качество поверхности и макроструктуру заготовок, выход годной продукции, неметаллические включения, механические свойства стали, остаточное содержание в ней элементов сплава и примесей. Учитывались также плотность сплава, усвоение основных компонентов, методы введения в сталь. В. Е. Власенко считает, что при разработке новых марок ферросплавов кроме известных физико-химических характеристик сплава (температуры плавления, плотности) следует учитывать такие факторы, как экономическая эффективность и технологичность выплавки, потребность в сплаве, его усвоение, раскислительная способность, тенденция развития сталеплавильных процессов и др. По мнению [3], выбор оптимального состава комплексных сплавов возможен с учетом поведения составляющих сплава в жидком металле, степени их сродства к кислороду и другим элементам, распределения продуктов окисления и снижения температуры жидкой стали. Наиболее разносторонний и глубокий подход к выбору новых марок комплексных сплавов содержится в работах И. П. Казачкова [4], который учитывает тепловой эффект присадки ферросплавов в сталь, скорость их плавления в ковше, температуру плавления и плотность сплавов, их химическое взаимодействие с кислородом и азотом и очищение стали от неметаллических включений.
Комплексный подход при выборе состава ферросплава, безусловно, является наиболее целесообразным. Однако такой подход, за редким исключением, не использовался на практике из-за отсутствия общепринятой схемы и трудности определения некоторых физико-химических характеристик.
3. ТРЕБОВАНИЯ, ПРЕДЪЯВЛЯЕМЫЕ К ФЕРРОСПЛАВАМ
Специфика получения и использования ферросплавов предъявляет к их качеству определенные требования.
Влитературе отсутствует перечень требований, которыми должны обладать ферросплавы по условиям плавки и разливки. В отдельных случаях упоминается о необходимости иметь плотность ферросплава более высокую, чем у шлака, а также минимальную ликвацию элементов при остывании и кристаллизации сплава.
О требованиях к ферросплавам со стороны потребителей сведения в литературе достаточно многочисленны. В первую очередь, они относятся к химическому составу ферросплавов по содержанию сопутствующих примесей и пределам ведущих элементов. А. Н. Морозов и С. И. Хитрик [5] справедливо отмечают, что пределы содержания сопутствующих примесей в ферросплаве каждого сорта должны быть в соответствии с его технологическим назначением и экономическими соображениями. Содержание ведущего элемента следует выдерживать стабильным, регламентируемыми сопутствующими примесями являются углерод, сера, фосфор, азот, цветные металлы (Zn, Sri, Си, Bi, Sb, Pb, As), дополнительные требования относятся к содержанию неметаллических включений, кислорода и водорода.
Физико-механическим характеристикам ферросплавов стали уделять внимание в связи с применением сортированных и порошкообразных ферросплавов, их дроблением, гранулированием [6].
Другие требования к ферросплавам можно свести к следующему:
1) содержание основного (ведущего) элемента необходимо иметь максимальным [7];
2) легирующие элементы должны иметь минимальное, а элементы-раскислители — максимальное сродство к кислороду [7], в комплексных раскислителях следует иметь элементы, обладающие разным сродством к кислороду [3, 4];
3) температуру плавления ферросплава рационально принимать ниже температуры кристаллизации обрабатываемого металла или ниже, чем температура стали в ковше [3, 4];
4) плотность ферросплава должна быть равной [4, 7] или более высокой [3], чем у обрабатываемого металла;
5) тепловой эффект взаимодействия ферросплавов с жидкой сталью не должен приводить к значительному охлаждению последней [3, 4];
6) продолжительность растворения составляющих сплава в жидком металле должна быть минимальной [3, 4].
Большинство приведенных требований основаны на длительной практике использования ферросплавов, и с ними следует согласиться. Однако в литературе отсутствуют сведения о некоторых характеристиках, в ряде случаев данные разноречивы (п. 2—4) или спорны (п. 1).
Нельзя согласиться с распространенной рекомендацией о необходимости иметь в сплаве максимальное содержание основного элемента, предполагающей снижение затрат тепла на расплавление ферросплава и содержания в стали других элементов. Однако снизить затраты тепла на усвоение ферросплава можно введением в его состав кремния, алюминия, титана. Кроме того, при вводе элемента, содержание которого в стали мало (например, при микролегировании), целесообразнее применять сплавы с пониженной концентрацией этого элемента, поскольку увеличится количество вводимого ферросплава и создадутся условия для более равномерного и стабильного растворения элемента. Это положение подтвердилось на практике, например для сплавов с бором и ниобием.
Исходя из результатов наших исследований и литературных данных были сформулированы основные требования к ферросплавам с точки зрения их получения и использования [8]:
1. Оптимальная температура плавления (начала кристаллизации) ферросплавов, предназначенных для обработки стали,— 1350—1400°С, для обработки чугуна — 1150—1200.
2. Оптимальная плотность промышленных ферросплавов — от 5000 до 7000 кг/м3.
3. Ведущие элементы для лучшего усвоения должны слабо окисляться кислородом воздуха, для этого в комплексном ферросплаве желательно иметь недорогие элементы с большей окисляемостью и поверхностной активностью, чем у основных компонентов сплава.
4. В сплаве, предназначенном для микролегирования, целесообразно снижать содержание ведущего элемента до 10—25%, а в отдельных случаях — до 2—5.
5. Время плавления и растворения ферросплава в обрабатываемом металле должно быть минимальным.
6. В комплексных раскислителях следует иметь элементы, обладающие разным сродством к кислороду и обеспечивающие максимальное удаление, измельчение и глобуляризацию неметаллических включений.
7. Тепловой эффект взаимодействия ферросплава с жидким металлом должен приводить к минимальному охлаждению последнего.
8. Необходимо, чтобы ферросплавы обладали механической прочностью, обеспечивающей удовлетворительную дробимость при образовании минимума мелких фракций, низкими значениями пористости, рассыпаемости и ликвации элементов в слитке, удовлетворяющими потребителя гранулометрическим составом и внешним видом,
9. Ферросплавы обязаны отвечать требованиям санитарной и пожаро- и взрывобезонасности.
10. Состав ферросплава должен находиться в соответствии с экономической эффективностью и технологическими особенностями его получения и использования.