Плазменная резка
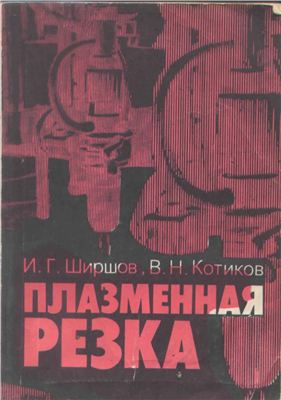
Ширшов И.Г., Котиков В.Н.
Машиностроение, 1987 г.
РЕЗКА ЛИСТОВОГО ПРОКАТА
Листовой прокат из стали всех марок, алюминия и его сплавов может разрезаться методом плазменной резки с использованием ручных резаков, переносных машин, а также на стационарных машинах с цифровым, фотоэлектронным и линейным управлением. Резка производится дугой прямого действия при прямой полярности.
Перед началом плазменной машинной резки необходимо проверить состояние оборудования и убедиться в его исправности. Установить расход плазмообразующей среды по таблице режимов. Проверить действие системы охлаждения плазменного резака. Задать необходимую скорость резки по таблице режимов и программу резки. Прежде чем приступить к вырезке деталей, следует проверить режимы резки на пробной планке из того же металла и той же толщины, что и разрезаемый металл.
При использовании в качестве плазмообразующей среды воздуха, азота, воздуха с водой, кислорода и кислорода с водой следует применять плазменные резаки с вихревой стабилизацией дуги, а при использовании аргона с водородом — плазменные резаки с осевой стабилизацией.
Во всех случаях процесс резки листа может начинаться или с кромки, или с середины листа.
Резка с середины листа, в свою очередь, может производиться, начиная с кромки предварительно просверленного отверстия, диаметр которого не должен быть менее 6 мм, или после пробивки металла непосредственно плазменной дугой. Предварительное сверление отверстий применяется лишь при резке металла большой толщины, когда невозможно пробить металл плазменной дугой, так как сверление отверстий связано с потерями времени и с неудобством выполнения работы, особенно при резке на стационарных машинах. При ручной резке стали, меди и сплавов на медной основе сверление отверстий обычно применяют при толщине более 40 мм, а при резке алюминиевых сплавов — более 50 мм. При резке переносными машинами и на стационарных машинах предварительное сверление отверстий производится при толщине разрезаемого металла более 28 мм для всех металлов.
Пробивка металла плазменной дугой является наиболее сложной операцией плазменной резки.
Капли расплавленного металла в момент пробивки выдуваются режущей струей из кратера, образующегося в листе, и загрязняют наружную поверхность сопла и кожуха резака. В некоторых случаях они могут создать сплошной мостик между соплом и разрезаемым листом, что приводит к образованию двойной дуги. Для предотвращения этого явления резак в момент пробивки должен быть поднят над листом на 20—25 мм, т. е. значительно выше, чем при резке. С другой стороны, для надежного соприкосновения с разрезаемым листом факела вспомогательной дуги, обеспечивающего возбуждение режущей дуги, резак должен быть удален от листа перед началом резки на 10—12 мм. В связи с этим приходится возбуждать дугу при опущенном резаке, а затем приподнимать его после возникновения прямой дуги и вновь опускать в рабочее положение после того, как металл будет пробит струей плазмы насквозь.
При ручной резке и резке переносными машинами приподнимание резака для пробивки производится вручную, а момент окончания пробивки и начала опускания резака определяется визуально по появлению сквозного отверстия. При резке на стационарных машинах приподнимание и опускание резака на время пробивки металла может также производиться оператором машины вручную путем нажатия кнопок на пульте управления машины, а момент окончания пробивки определяется визуально. Однако современные стационарные машины имеют несложные реле времени, при помощи которых резак автоматически приподнимается для осуществления процесса пробивки и опускается в рабочее положение для начала перемещения по траектории резания.
При автоматической пробивке ее осуществление контролируется не визуально, а по времени, затрачиваемом на пробивку металла определенной толщины. При этом под временем пробивки понимается промежуток времени от начала возбуждения режущей дуги до начала движения резака по заданной траектории.
В этом промежутке с помощью автоматики машина осуществляет возбуждение режущей дуги, приподнимание резака в начале пробивки отверстия и опускание его после окончания пробивки. Продолжительность остановки резака при пробивке металла задается в зависимости от толщины разрезаемого металла.
В случае выполнения пробивки непосредственно на линии контура детали при машинной резке требуется очень точная регулировка времени пробивки. При недостаточной выдержке металл не пробивается на всю толщину и прорезается уже в процессе движения резака. В результате этого в начале реза у нижней кромки остается участок непрорезанного металла. При чрезмерно продолжительной остановке резака диаметр пробитого отверстия превышает ширину реза. На кромке детали остается выхват, ухудшающий внешний вид и затрудняющий последующую сварку.
Подбор оптимальной продолжительности времени пробивки для каждой толщины листа значительно усложняет процесс регулирования системы управления дугой перед резкой. Кроме того, незначительное изменение внешних условий, например изменение напряжения питающей сети, давления сжатого воздуха, расстояния между резаком и металлом, приводит к тому, что ранее установленная выдержка оказывается для данных условий неправильной и в точке пробивки образуется или непрорез, или слишком большое отверстие. В связи с этим рекомендуется продолжительность пробивки устанавливать таким образом, чтобы обеспечить надежное проплавление металла, а пробивку производить в стороне от контура вырезаемой детали (на отходе). Практически при резке стали толщиной 6—20 мм можно использовать одну выдержку времени, равную приблизительно 2 с; расстояние от места пробивки до контура вырезаемой детали при плазменной резке зависит от толщины детали следующим образом:
Толщина разрезаемого металла, мм..... 15 16—20 21—30 31—50
Расстояние от места пробивки, мм...... 5—6 6—7 7— 8 20—25
Однако и в данных условиях продолжительность пробивки не следует делать слишком долгой, так как отверстие становится настолько большим, что для обеспечения контакта между металлом и столбом плазменной дуги последний должен сильно искривиться. Это приводит к соприкосновению столба дуги со стенкой сопла, в результате чего происходит либо срабатывание системы автоматической защиты сопла, либо оплавление его стенок, либо отрыв дуги.
Плазменную резку алюминия и его сплавов следует выполнять в среде аргона с водородом. Допускается резка в среде азота, воздуха, воздуха с водой и кислорода с водой.
Большим преимуществом аргона является способность устойчиво поддерживать плазменную дугу при небольших напряжениях и малом токе. В связи с этим аргон применяется, главным образом, при ручной резке листов из алюминиевых сплавов сравнительно небольшой толщины (до 12— 20 мм). Недостатком аргона является относительно малая проплавляющая способность плазменной струи и, как следствие, наименьшая по сравнению со всеми другими газами скорость резки. Однако при ручной резке физиологические возможности резчика ограничивают скорость ведения процесса. В связи с этим при резке тонколистового алюминия малая проплавляющаяся способность аргоновой плазмы практически не оказывает влияния на производительность резки.
Добавка к аргону водорода резко повышает скорость резки. Однако водород, диссоциируя на атомы в приэлектродной области, отнимает у электрода значительное количество теплоты, т. е. оказывает на дугу гасящее действие. Он может охладить катодное пятно настолько, что термоэлектронная эмиссия прекратится и дуга прервется. Зажечь плазменную дугу в атмосфере водорода при тех же напряжениях и токе вспомогательной дуги, которые применяются в существующих установках, не удается. В связи с этим возбуждение дуги производят в среде аргона и только после получения режущей дуги добавляют к аргону водород. Соотношение между аргоном и водородом зависит от вида резки и толщины разрезаемого металла.