Плазменная плавка
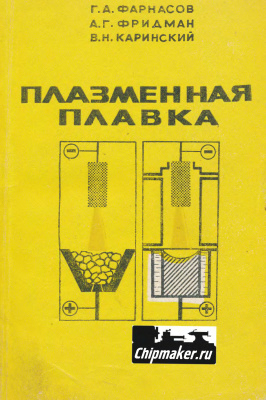
Фарнасов Г.А. и др.
Металлургия, 1968 г.
ИСПОЛЬЗОВАНИЕ ПЛАЗМЕННОГО НАГРЕВА В МЕТАЛЛУРГИИ
Трудно указать такую отрасль современной металлургии, где применение плазменного нагрева не сопровождалось бы интенсификацией технологических процессов или значительным повышением качества выпускаемого металла. Рудовосстановительные процессы и получение высокоогнеупорных изделий из тугоплавких окислов, повышение температурного уровня мартеновской плавки и выплавка специальных сталей и сплавов, рафинирование тугоплавких металлов и ускоренная резка и зачистка проката — вот далеко не полный перечень тех областей, в которых плазма могла бы быть широко использована металлургами.
Наиболее простым и удобным способом применения низкотемпературной плазмы в металлургии является нагрев плазменной дугой и плазменной струей. К. п. д. плазмотронов небольшой мощности составляет в первом случае 10—15%, во втором — всего 2—3%. Однако с ростом мощности плазмотронов их к. п. д. возрастает. Кроме того, в ряде случаев приходится отдавать предпочтение нагреву плазменной струей, поскольку плазменная струя представляет собой более рассредоточенный, объемный источник тепла, обеспечивающий мягкий нагрев больших масс материала независимо от его электропроводности.
Все разнообразие применения плазменного нагрева для металлургической обработки материалов можно свести к нескольким основным схемам.
Обработка рудного сырья может производиться двумя методами. По одной схеме (рис. 74,а) подлежащий
обработке порошок смешивается с таким количеством графита, которое обеспечивает достаточную электропроводность стержней, получаемых прессованием этой смеси. Прессованные стержни в дальнейшем используют в качестве расходуемых анодов в плазменнодуговых устройствах интенсивного действия. Благодаря высокой температуре плазменной дуги материал анода испаряется, диссоциируя на более простые окислы, а при наличии в атмосфере дуги восстановителя в достаточном количестве может происходить восстановление рудного материала до металла или карбида.
По другой схеме (рис. 74,6) обрабатываемый рудный материал в виде порошка подается в плазменную струю, где он сильно нагревается и диссоциирует на более простые окислы или, взаимодействуя с плазмообразующим газом, в качестве которого наряду с нейтральным аргоном или азотом можно использовать хлор или водород, переходит в свободное состояние или в соединения, из которых чистый металл может быть легко извлечен известными методами.
Третья схема предполагает использование плазменного нагрева для плавления металлической шихты на огнеупорной подине. Поскольку здесь речь идет уже об обработке электропроводных материалов, в данном случае выгоднее применять плазмотроны, работающие в. режиме плазменной дуги. С этой целью приходится зафутеровывать в подину электрод, срок службы которого в условиях длительного контакта с жидким металлом вряд ли может быть большим. Для подогрева и плавления металлической шихты можно применять и плазмен^ ную струю.
Наиболее эффективной является четвертая схема: стержень из перерабатываемого материала оплавляется плазмой, а жидкий металл собирается в водоохлаждаемом кристаллизаторе, где происходит формирование слитка. Оплавление расходуемого стержня может происходить как плазменной струей, так и плазменной дугой, что предпочтительнее. Анодом может служить в первом случае сопло плазменнодуговой горелки, а во втором — ванна жидкого металла в кристаллизаторе. Одновременно промежуточный потенциал может быть подан на расходуемый стержень. Важно, что при переплавке по такой схеме скорость плавки и степень перегрева жидкой ванны могут регулироваться раздельно.
Выплавка металла в плазменнодуговых печах с огнеупорной футеровкой
Другим направлением использования низкотемпера турной плазмы в металлургии является выплавка и рафинирование сталей и сплавов в печах с плазменнодуговыми нагревателями. Развитие плазменной плавки в этом направлении может дать следующие преимущества [181]:
- Исключается загрязнение металла нежелательными примесями — углеродом из графитированных электродов, применяемых в обычных дуговых элеткропечах, азотом и водородом из атмосферы печи.
- Плазменная струя может состоять из любой необходимой смеси газов, что позволяет поддерживать в печи любую атмосферу — окислительную, восстановительную, нейтральную.
- Условия дегазации жидкого металла в плазменной печи с нейтральной атмосферой приближаются к условиям дегазации при плавке в оборудованных дорогостоящими откачными системами вакуумных печах, так как парциальные давления кислорода, водорода и азота в атмосфере плазменной печи с горелкой, работающей на инертном газе, невелики. Например, плавка в атмосфере нейтрального газа, содержащего —'0,05% активных газовых примесей, термодинамически эквивалентна осуществлению процесса в вакууме~57 н/м2 (0,5 мм рт. ст.).
- Плавка в плазменных печах в отличие от вакуумной индукционной, дуговой и электроннолучевой плавки благодаря наличию атмосферного давления над ванной сопровождается меньшим испарением основных компонентов расплава.
- При помощи плазменных горелок можно достичь высоких и легко регулируемых температур, а стабильность процесса упрощает проблему его регулирования.
- Высокая концентрация энергии в малом объеме, значительная скорость потока плазмы и очень быстрая передача тепла нагреваемым материалам при сравнительно небольшой потере энергии на излучение обусловливают весьма высокие скорости плавления в плазменных печах.
- Простота плазменных печей по сравнению с вакуумными облегчает выполнение в них таких технологических операций, как наводка шлака, продувка металла и т. д.
Плазменнодуговые печи различного назначения и размера в США проектирует и поставляет фирма Лин
де [132, 182—184]. Для прецизионного литья изготовляют небольшие печи емкостью до 12 кг, мощностью 40 квт\ скорость плавления составляет 1,2 кг\мин\ длительность загрузки, доводки и выпуска металла такая же, как в индукционой печи; срок службы огнеупорного тигля 200 плавок. Для выплавки качественных высокопрочных сталей и специальных сплавов, отливаемых в изложницы или в литейные формы и предназначенных для новейших отраслей промышленности, фирма поставляет печи емкостью от 25 кг до 1,8 г (рис. 77). Мощность печи емкостью 140 кг составляет 120 кет. Печь емкостью 0,9 т оборудована одним плазмотроном, а печи большей емкости (фирма проектирует серию печей емкостью до 90 т) будут снабжены несколькими плазмотронами. Плазменнодуговую печь емкостью 9 т фирма предполагает снабдить четырьмя плазмотронами с тем, чтобы длительность плавки в этой печи была около 2 ч. Это несколько меньше, чем в обычной дуговой электропечи той же емкости, однако специалисты фирмы Линде предполагают, что с увеличением емкости плазменнодуговых печей вряд ли удастся сохранить столь высокие значения скорости плавки. Стоимость плазменнодуговой печи фирмы Линде близка к стоимости обычной дуговой печи такой же емкости.
На рис. 78 изображена схема плазменнодуговой печи конструкции Линде емкостью 140 кг, установленной на заводе фирмы Юнион Карбайд оф Кэнада в Торонто.