Плавка и литье жаропрочных сплавов и сталей в вакууме
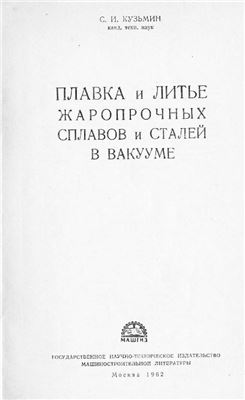
Кузьмин С.И.
Машгиз, 1962 г.
Согласно исследованиям жаропрочных сплавов на никельхромовой основе, легированных алюминием и титаном, проведенным Э. В. Поляк и автором, макро- и микроструктура этих сплавов значительно отличается от структуры аналогичных сплавов, выплавленных в атмосфере воздуха.
В первую очередь обращает на себя внимание различие в макроструктуре. Величина макрозерна сплава, выплавленного и отлитого в вакууме, заметно больше зерна сплава, выплавленного и отлитого в атмосфере воздуха (при равных условиях заливки). Разница в атмосфере зерен увеличивается с увеличением степени вакуума. Чем меньше остаточное давление, при котором выплавлялся сплав, тем крупнее получается зерно в отливке.
На фиг. 11, а, б, в показано, как изменяется макроструктура сплава в зависимости от степени разрежения. В вакууме 10-3 мм рт. ст. зерно курпнее, чем у сплава, отлитого при атмосферном давлении, а в вакууме 10-6 мм рт. ст. размер его еще больше возрастает. Изменение величины зерна в зависимости от глубины вакуума обусловлено скоростью охлаждения сплава в процессе кристаллизации. Чем выше вакуум, тем меньше теплоотдача; сплав охлаждается медленно, и в процессе кристаллизации зерно получается крупнее.
Рост зерна с повышением степени вакуума вызван также удалением из сплава различных примесей. О более высокой чистоте сплава, выплавленного в вакууме, свидетельствует дендритная структура и структура границ зерен. У сплава, выплавленного и отлитого в вакууме, дендриты имеют более тонкое строение, чем дендриты сплава, выплавленного в атмосфере воздуха (фиг. 12).
По границам зерен сплава, выплавленного и отлитого в вакууме, располагаются более тонкие выделения, чем у сплава, выплавленного и отлитого в атмосфере воздуха (фиг. 13 и 13а). У сплава, выплавленного в вакууме, мелкие карбиды располагаются по границам зерен в виде прерывистых цепочек; у сплава же, выплавленного в атмосфере воздуха, на границах зерен часто встречаются крупные карбиды и карбонитриды и другие грубые выделения.
Различие в состоянии границ зерен и дендритного строения является наиболее важной структурной особенностью для сплавов, выплавленных в вакуумных печах, так как время до разрушения и пластические свойства жаропрочных сплавов при воздействии высоких температур и растягивающих напряжении в значительной мере определяются состоянием границ зерен, ибо разрушение при длительной работе происходит во времени по границам зерен. Следовательно, состояние границ зерен является одним из основных факторов, определяющих жаропрочные и пластические свойства сплава.
Сопоставление строения и дисперсности упрочняющей ннтерметаллидной α'-фазы в сплаве, выплавленном в вакууме и на воздухе, не дает существенного различия (фиг. 14). Дисперсность и форма α'-фазы при данном легировании зависит, как известно, не от условий плавки, а от скорости охлаждения после закалки. Поскольку режим термической обработки был одинаков для сплавов, выплавленных в вакууме и в атмосфере воздуха, то и в строении α-фазы разницы не наблюдается.
Исследование с помощью электронного микроскопа структурных изменений, происходящих при испытании на длительную прочность, позволяет косвенно оцепить сравнительную скорость диффузионных процессов в сплавах, выплавленных в атмосфере воздуха и в вакууме.
В структуре сплава, выплавленного в вакууме, во времени происходит ориентированный рост α'-фазы и вытягивание ее в длинные параллельные пластины.
Сопоставление структурных изменений сплава, выплавленного в вакууме, со структурными изменениями сплава, выплавленного в атмосфере воздуха, показывает, что коагуляция и вытягивание α'-фазы у сплава, выплавленного в атмосфере воздуха, происходит за более короткое время; причем эти структурные изменения протекают неравномерно: в зоне разрыва под влиянием максимальных растягивающих напряжений α'-фаза вытягивается сильно, тогда как вблизи головки образца α'-фаза имеет форму правильных кубиков. После испытания на длительную прочность границы зерен сплава, выплавленного в атмосфере воздуха, имеют значительно более грубее строение, чем у сплава, выплавленного в вакууме (фиг. 15). Устранение при плавке в вакуумных печах растворенных в сплаве газов, воздуха и восстановление окисных плен создает более- благоприятные условия для лучшего смачивания растущих в жидком металле кристаллов и для получения более плотного металла, что по-видимому, способствует снижению скорости диффузионных процессов в сплаве.
3. СТРУКТУРА И ПЛОТНОСТЬ ОТЛИВОК В ЗАВИСИМОСТИ ОТ УСЛОВИЙ ПЛАВКИ И РАЗЛИВКИ В ВАКУУМЕ
Плавка жаропрочных сплавов и отливка деталей в вакууме может производиться при различных условиях: в вакууме, в среде нейтрального газа и в вакууме с последующей кристаллизацией отливки в атмосфере окружающего воздуха.
По первому способу весь процесс плавки, разливки и кристаллизации осуществляют в вакууме; во втором случае расплавление металла происходит в вакууме, а разливка в среде нейтрального газа. Третий вариант состоит из плавки и разливки в вакууме с последующим быстрым заполнением вакуум-камеры плавильной печи атмосферным воздухом. В последнем случае еще не успевший затвердеть жидкий металл кристаллизуется в форме под давлением окружающего воздуха. Условия плавки и литья в вакууме выбираются в зависимости от требований, предъявляемых к деталям.
Плавки по первому варианту проводятся как с отключением насосов перед сливом металла, так и с работающими насосами во время слива и кристаллизации металла. В первом случае плавки проводятся по системе: металл расплавляют в вакууме и дают выдержку при определенной величине вакуума. По окончании выдержки насосы отключают и сливают металл в форму; при этом после отключения насосов вакуум падает за счет выделения газов
По второму варианту после расплавления металла и выдержки его в вакууме насосы отключают и заполняют вакуум-камеру аргоном или гелием до определенного давления. Слив металла и кристаллизация осуществляются уже в нейтральной атмосфере.
В третьем варианте после расплавления металла и выдержки его под вакуумом при работающих насосах заливают металл в форму. После этого быстро перекрывают насосы и в вакуум-камеру напускают воздух до давления одной атмосферы. В этом случае заливка металла осуществляется в вакууме, а кристаллизация его происходит в смеси воздуха с газами, выделяемыми формой, металлом и тиглем. Совершенно очевидно, что качество детали будет зависеть от разобранных вариантов проведения плавки и заливки в вакуумной печи.
Исследования, проведенные Э. В. Поляк и автором, свидетельствуют о том, что структура сплава также изменяется в зависимости от условий плавки, заливки и кристаллизации.
На фиг. 16 сопоставлена дендритная структура сплава, выплавленного на воздухе и в вакууме с различными способами разливки. Наиболее тонкая дендритная структура образуется при плавке и разливке в вакууме, а наиболее грубая — при плавке и разливке на воздухе. Промежуточное положение занимает разливка в среде нейтрального газа и разливка в вакууме с кристаллизацией в атмосфере воздуха. На фиг. 17 сопоставлена микроструктура сплава, выплавленного в вакууме при различных условиях заливки и в атмосфере воздуха. В сплаве, выплавленном и разлитом в вакууме, по границам зерен видны мелкие карбидные выделения, расположенные прерывистой цепочкой. Примерно такой же формы карбидные выделения наблюдаются на границах зерен сплава при плавке в вакууме и заливке в среде нейтрального газа. При плавке и разливке в вакууме, но с кристаллизацией на воздухе выделения по границам зерен утолщаются. Наконец, наиболее грубые выделения наблюдаются па границах зерен у сплава, выплавленного и отлитого в атмосфере воздуха. По границам зерен располагаются крупные карбидные и карбонитридные соединения.
Одной из трудных задач при литье в вакууме является вопрос получения плотной отливки. Как бы тщательно при плавке в вакууме не производилось удаление газов из металла, практически невозможно их удалить полностью. Поэтому в случае заливки формы в вакууме оставшиеся газы продолжают выделяться и образуют газовую пористость при кристаллизации отливки. Кроме того, отсутствие атмосферного давления затрудняет питание отливки, что ведет к образованию усадочной рыхлости. Таким образом, при плавке металла и заливке детали непосредственно в вакууме трудно добиться плотной отливки. Более выгодные условия для кристаллизации отливки создаются в случае расплавления металла в вакууме, а заливки в среде нейтрального газа давлением 1ат, В этом случае отливка получается наиболее плотной.