Плавка и литье урана и его сплавов
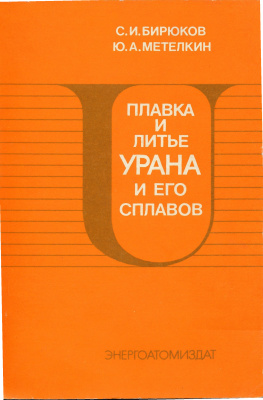
Бирюков С.И., Метелкин Ю.А.
Энергоатомиздат, 1983 г.
6.4. Плавка и литье сплавов урана
При производстве слитков из сплавов U основные трудности связаны с приготовлением сплава, получением слитка с равномерным распределением легирующих компонентов и без литейных дефектов. Эти сложности связаны со значительной разницей плотности урана и большинства легирующих компонентов (Nb, Zr, Ti, Si) и температуры их плавления. Эти факторы способствуют возникновению ликвации уже в тигле и без применения специальных методов воздействия на расплав могут привести к окончательному браку изделия.
Высококачественные однородные слитки урана и урановых сплавов, отвечающие жестким техническим условиям на ядерные материалы, изготавливают в США на заводе Y-12 в Ок-Ридже. Сплавы U, содержащие Ti, Mo, Zr и Nb, производят партиями массой до 800 кг и отливают из них слитки или окончательные изделия. Методы обработки зависят от состава сплава и ограничений по качеству. Нелегированный уран и сплавы, содержащие титан и молибден, как правило, получают вакуумной индукционной плавкой; однако эти сплавы можно также производить вакуумной дуговой плавкой, если необходима высокая степень чистоты. Сплав урана, содержащий по массе 2% Nb, как правило, получают путем индукционной плавки нелегированного урана с ломом сплава U + 6% Nb. Крупные слитки сплавов урана с 6%Nb и U, содержащие по массе 7,5%Nb и 2,5% Zr, обычно получают вакуумно-дуговой плавкой. При необходимости рафинирования материала шихты, такого, как сбрикетированная стружка от механической обработки, желательно использовать электрошлаковую плавку [5].
Методы легирования урана. Наиболее распространенными методами легирования урана являются сплавление урана в вакуумной индукционной печи с легирующими компонентами, вводимыми в чистом виде или в виде лигатур, и совместное восстановление тетрафторида урана и соединений легирующего металла магнием или кальцием.
Приготовление сплавов индукционной плавкой нашло широкое применение при выплавке сплавов с титаном, алюминием, ниобием, молибденом. Выбор способа введения добавок зависит от плотности, удельной площади поверхности, температуры плавления, но общим для этого способа являются следующие условия:
обеспечение контакта между раствором и легирующими компонентами на время, достаточное для растворения легирующих;
создание условий, предотвращающих ликвацию в жидком состоянии;
применение такого материала тигля или покрытия, которые обеспечили бы чистоту сплава по примесям.
Некоторые металлы, например молибден, можно вводить в сплав непосредственно. Сплав урана, содержащий по массе 10% Мо, можно получать совместной плавкой урана и сбрикетированного порошка молибдена. Плавку при этом ведут двумя способами: либо длительное время выдерживают расплав при температуре 1350 °С, либо быстро повышают температуру до 1500 С, выдерживают при ней расплав до полного растворения молибдена и снижают ее до 1350 °С перед разливкой [40].
Для точного определения степени перегрева при растворении определенного количества данного легирующего элемента важное значение имеют такие факторы, как форма, размеры и состояние шихтовых материалов и степень газовыделения в процессе плавки [72]. Так, легирующие добавки в виде губки титана или циркония растворяются при меньшем перегреве и за меньшее время, чем при введении легирующего компонента в виде металлической дроби такого же размера [46].
В Канаде были проведены исследования усвоения легирующих компонентов расплавленным ураном. С этой целью была выплавлена серия сплавов с содержанием их до 9% по массе. Для увеличения реакционной поверхности кремний дробили, а остальные металлы прокатывали в тонкий лист. В тигель в первую очередь загружали легирующие компоненты, а потом на них - куски урана. Плавку вели в вакуумной индукционной печи (см. гл. 2) при остаточном давлении 0,8-1,3 Па, при частоте тока 3000 Гц и мощности 50 кВт. Масса плавки 15-20 кг. Металл перегревали до 1590 °С, выдерживали при этой температуре 8-10 мин, затем охлаждали до 1450°С и разливали в формы. Усвоение различных легирующих компонентов ураном приведено в табл. 23 [бб].
Невысокое усвоение ураном циркония объясняется образованием на поверхности циркониевых пластин оксидов, стойких по отношению к жидкому урану.
Вводят легирующие компоненты при непосредственном сплавлении обычно одним из трех приемов: 1) укладывают их на дно тигля и сверху придавливают кусками урана для предотвращения их всплывают во время плавки; 2) загружают их в емкость с отверстиями (колокольчик), которую после расплавления урана погружают в ванну расплава; 3) подают их из бункера на зеркало ванны расплава (рис. 16).
Для приготовления сплавов урана с некоторыми элементами с успехом можно применять совместное восстановление тетрафторида урана с соединениями (фториды,оксиды) легирующих компонентов. Обычно соединение легирующего металла смешивают с загружаемой в бомбу шихтой из тетрафторида урана и магния. Полученную смесь затем помещают в тигель с футеровкой из фторида кальция. После восстановления слиток извлекают из тигля и его можно использовать в качестве шихты для индукционной плавки.
Преимущество метода совместного восстановления состоит в получении сплавов с малым содержанием посторонних примесей. В частности, приготовление сплава в бомбе исключает загрязнение углеродом, неизбежное при проведении плавки в графитовых тиглях.
В работе [46] описывается совместное восстановление тетрафторидов урана и циркония для приготовления сплавов с содержанием циркония по массе 0,2—6,0%. Сплавы со средним содержанием циркония от 0,6 до 1,7% обладают хорошей однородностью, а с малым и с высоким (боле 6%) — недостаточно однородны.
Попытки получить уран-ниобиевые сплавы совместным восстановлением магнием в присутствии пятиокисн ниобия не дали положительных результатов. Более положительные результаты получены при использовании соли ниобия Na2NbOF6 [46].
Вследствие летучести соединений молибдена уран-молибденовые сплавы нельзя получить совместным восстановлением галогенов; однако при применении окислов молибдена или чистого металла получаются вполне удовлетворительные результаты.
Фирмой National Lead Co. of Ohio с успехом было применено восстановление урана кальцием в присутствии циркония и молибдена для получения сплавов с 5% Zr или Мо [46].
Уран-кремниевые сплавы, содержащие по массе до 9,5% Si, могут быть получены методом совместного восстановления тетрафторида урана с оксидом кремния. Слитки обладают хорошей однородностью. Необходимым условием достижения этого является полное обезвоживание оксида кремния.
Способы перемешивания расплава в тигле.
Для уменьшения времени растворения легирующих в жидком металле часто применяют перемешивание расплава и легирующих компонентов во время плавки. Это приводит к уменьшению времени плавки, а следовательно, к увеличению производительности оборудования, улучшению качества металла за счет сокращения времени контакта с материалом тигля и повышению однородности выплавляемого сплава.
За рубежом при выплавке сплавов урана нашли применение следующие способы: перемешивание с помощью механической мешалки, электромагнитное перемешивание, перемешивание с помощью продувки нейтральным газом, перемешивание парами металлов с высокой упругостью пара.
Механическое перемешивание нашло применение при проведении небольших плавок массой в несколько килограммов и крупномасштабных плавок массой свыше 1000 кг [53,59]. Во Франции графитовую мешалку применяли при приготовлении сплава урана, содержащего по массе 10% Мо. Ось мешалки была полон, и через нее с помощью оптического пирометра замеряли температуру жидкой ванны. Перемешивание продолжалось около 20 мин, после чего расплав отстаивали в течение 10 мин и сливали в форму. Масса плавки составляла несколько килограммов [59].
При выплавке сплава урана, содержащего по массе 0,75—0,80% Ti, применяли графитовую мешалку с двумя лопастями. Плавку вели в графитовом тигле. Масса расплава при плавке была равна 1000 кг. Шихта состояла из чернового урана, полученного магнийтермическим восстановлением тетрафторида урана, отходов уранового производства и титановой губки, которую загружали на дно тигля. Плавку вели на частоте тока 960 Гц. Характеристика полученного слитка приведена в табл. 25.
В работе [69] для перемешивания расплава рекомендуется применять низкочастотное электромагнитное перемешивание (табл. 26). Расплавление шихты происходило при частоте 10 000 Гц. После необходимого перегрева высокочастотный генератор отключали и к индуктору на 5 мин подводили ток промышленной частоты (60 Гц). Благодаря электромагнитному перемешиванию при плавке сплава урана с 1% Ti (по массе) изменение содержания титана по длине отливки уменьшилось от 0,5 до 0,08%. В работе [78] указывается, что электромагнитное перемешивание целесообразно совмещать с литьем.
В работе [46] указывается на возможность перемешивания расшива парами металлов с высоким давлением пара. Это впервые было обнаружено, когда проводились плавки металлического урана. Магний испарялся, раствор как бы кипел, и шло его активное перемешивание. Этот эффект наблюдался при выплавке сплава урана, содержащего по массе 5% Zr и 1,5% Nb. Магнии в плавку вводили с магнийтермическим ураном и циркониевой губкой. Плавку вели на частоте тока 3000 Гц в графитовом тигле, покрытом цирконатом магния или двуокендом тория. Для предотвращения конденсации паров магния в изложнице литниковые каналы перекрывали урановой фольгой.
В связи с тем, что наличие паров магния в печном пространстве могло привести к возникновению разряда между витками индуктора и к его пробою, был применен тип печи с индуктором, вынесенным во внепечное пространство.
Особенно бурное перемешивание происходит при температуре 1300°С, когда начинается растворение циркония. При температуре 1500 °С иногда образуется пена и уровень расплава начинает повышаться. В этом случае отсоединяется вакуумная система, в печь подается аргон до давления 300 — 400 Па и пена пропадает. После этого печь снова откачивают до давления 1—2 Па. Для обеспечения полного растворения ниобия и циркония температуру расплава во время плавки поддерживают равной 1550 -1600°С.
При продувке расплава нейтральным газом происходит интенсивное перемешивание металла, что ускоряет процесс растворения легирующих компонентов. Нейтральный газ вдувают через полую штангу, на одном конце которой имеется наконечник из пористой керамики или графита, а другой конец присоединен к магистрали инертного газа. Критичным для материала наконечника являются поры размером не более 30 мкм. Штанга опускается на дно тигля и во время подачи нейтрального газа перемешивает расплав, совершая возвратно-поступательное движение. Этот процесс позволяет не только ускорить растворение легирующих компонентов, но и провести дегазацию металла от летучих примесей, например водорода [36].