Переработка шлаков цветной металлургии
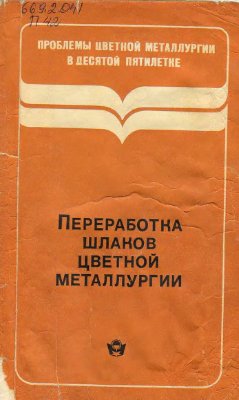
Лакерник М.М., Мазурчук Э.Д., Петкер С.Я., Шабалина Р.И.
Металлургия, 1977 г.
7. ОБЕДНЕНИЕ ШЛАКОВ С ИСПОЛЬЗОВАНИЕМ ПОСТОЯННОГО ТОКА, ЦЕНТРИФУГИРОВАНИЯ И ХЛОРИРОВАНИЯ
Обеднение шлаков с использованием постоянного тока
Ряд исследователей ведут поисковые работы по использованию постоянного тока для переработки шлаков. Этот метод основан на направленном капиллярном движении капель в расплавах при наложении внешнего поля. При этом из шлака выделяются только механические включения штейна и металла, которые, как было показано выше, превалируют над потерями металла в ионизированной форме.
Укрупненные лабораторные испытания процесса непрерывного обеднения шлаков с применением постоянного тока проведены во ВНИИцветмете. Установлены работоспособность устройства и возможность применения его на действующих электропечах. В период испытаний было проплавлено 7,35 т шлака свинцовой плавки и шлака взвешенной плавки медно-цинкового концентрата и получены удовлетворительные результаты.
Осаждение меди из шлаков центрифугированием
Одним из возможных способов снижения содержания цветных металлов в шлаке является метод центрифугирования. Большинство исследований процесса центрифугирования шлака выполнены в лабораторном масштабе, за исключением работы по высокотемпературному центрифугированию шлака, проведенной в Берлинском институте металлургии (ГДР). Л. В. Велюков, а также В. Визе применили метод центрифугировании шлаков в лабораторных условиях с целью ускорения процесса осаждения механически запутавшихся частиц сульфидов меди.
Б. В. Липин и Линденлауб считают, что методом Центрифугирования можно значительно снизить потери металла с отвальными шлаками. Применение этого метода на шлаках Мансфсльдского комбината позволилс получить остаточное содержание меди в шлаке 0,01 % никеля 0,04%, кобальта 0,04%.
Б. В. Липин проводил исследования центрифугирования промышленного отвального шлака медного производства. Были достигнуты следующие показатели по извлечению металлов, %: 30—70 Сu; 40—80 Ni; 20—50 Со; 90 Pb и 10 2п. Степень извлечения металлов не зависела от времени центрифугирования (свыше I мин), но зависела от числа оборотов. Минимальное остаточное содержание металлов в шлаке, соответствующее растворимости сульфидов, составляло, %: 0,053—0,06 Сu; 0,025— 0,03 Ni. 0,018—0,019 Со.
Исследование извлечения ценных составляющих из свинцово-медных шлаков методом высокотемпературного центрифугирования проведено на полупромышленной установке производительностью 2—3 т/ч в Берлинском институте металлургии совместно с Институтом металлургии в Аахене (ФРГ). Испытания проводили как на гранулированном шлаке, который предварительно подвергали плавке в дуговой электропечи, так и на жидком шлаке текущей выдачи. Температура шлака, заливаемого в центрифугу, составляла 1080°С. Испытания показали, что с увеличением числа оборотов центрифуги повышался эффект разделения. Максимальное извлечение металлов получено при скорости центрифуги ~ 1000об/мин.
Необходимо отметить, что вследствие трудностей, связанных с аппаратурным оформлением, нельзя рассматривать в настоящее время центрифугирование шлаков как процесс, пригодный для промышленного внедрения.
Переработка шлаков с добавкой хлорирующих агентов
За последнее время появились сообщения о разработке способов извлечения цветных металлов из шлаков с помощью хлорирования. Нагазуе Хиромиши (Япония) изучал оптимальные условия хлорирующего обжига медных шлаков, в частности температурный режим обжига в пределах от 600 до 1100°С. При обжиге шлака с добавкой 10% СаСl2-2Н2O при температуре 1000°С в течение 2 ч степень извлечения меди достигла 95%. Кроме того, Хиромиши изучал поведение цинка при хлорирующем обжиге.
Были проведены исследования возможности применения хлородовозгонки для извлечения цветных металлов из шлаков Балхашского комбината [36]. При температуре 900 -1000°С в возгоны извлекали 80—90% РЬ, 60— 80% Zn и 40—60% Сu. Для предотвращения оплавления гранул в состав шихты вводили добавки кремнезема и глинозема, что позволяло весгн процесс при более высоких температурах,
8. ГИДРОМЕТАЛЛУРГИЧЕСКИЕ СПОСОБЫ ПЕРЕРАБОТКИ ШЛАКОВ
Ряд исследователей работает над вопросами переработки отвальных шлаков гидромсталлургическими способами. Так, опыты по переработке шлаков отражательной плавки гидрометаллургическпм способом были проведены И. Л. Баркером и др. на заводе «Ля Ороня» (Перу). Исследовали следующие схемы переработки шлаков: выщелачивание шлаков растворами серной кислоты и сульфата железа; автоклавное аммиачно-карбонатное выщелачивание шлаков в окислительной среде; автоклавное сернокислотное выщелачивание. Извлечение меди составило более 90%.
Г. Бёрлинг и Г. Кол та .[37] проводили автоклавное азотнокислое выщелачивание шлаков отражательной и шахтной плавок. Лучшие результаты были получены при температуре 120°С и давлении кислорода, равном 1 ат. При разложении фаялита кремний гидратировался, что приводило к затруднениям при фильтрации.
Были проведены исследования по бактериальному выщелачиванию шлака отражательной плавки, которые показали, что извлечение меди в раствор повышается в случае применения бактерии с 12 до 62%.
Т. Р. Шелли [38] исследована возможность выщелачивания отвальных шлаков растворами серной кислоты и сульфата железа, а также аммиачно-карбонатными растворами. Исходный шлак содержал 0,55% Си. Выщелачивание растворами серной кислоты и сульфата железа осуществляли при рН —0,5. При увеличении содержания трехвалентного железа в растворе с 2 до 32 г/л степень извлечения меди возрастала с 13 до 50%. Оптимальная степень измельчения составляла 100%—0,074 мм. Опыты но выщелачиванию аммиачно-карбонатными растворами показали, что максимальное извлечение меди превышает 50%.
Сопоставление процессов выщелачивания двумя тоннами растворителей показывает, что в случае применении аммиачно-карбонатных растворов процесс протекает более эффективно, чем при использовании растворов сер пой кислоты и сульфата железа. Аммиачно-карбонатно выщелачивание рекомендуют для переработки измельченного шлака с содержанием меди менее 1%. Медь и аммиачного раствора можно извлекать жидкостной экстрацией с последующей реэкстракцией и электролизом.
Г. Вильсон запатентовал ряд гидрометаллургически: схем выщелачивания отвальных шлаков отражательной плавки следующего состава, %: 0,3—0,5 Сu; 0,5 РЪ;2—с 2п; 28-32 Ре; 32 -38 5Ю2; 8—10 СаО.
Измельченный шлак (90%—0,074 мм) подвергали выщелачиванию растворами соляной или азотной кислоты
9. ИЗВЛЕЧЕНИЕ ИЗ ШЛАКОВ ЖЕЛЕЗА
Способы переработки шлаков, рассмотренные выше имеют различную степень достоверности, так как проверены в лабораторном, укрупненном и полупромышленном масштабах, но ни один из них не подготовлен к промышленному использованию. Наиболее проверены различные электротермические способы, которые, вероятно, и явятся основой способа комплексной переработки шлаков.
Наиболее сложной является проблема извлечения из шлаков железа, притом в таком виде, чтобы оно могло быть использовано в промышленности.
Во всех случаях железо получается сернистым и медистым. Удаление серы является освоенной операцией. Удаление меди — намного сложнее. Поэтому В. И. Смирнов справедливо указывал на необходимость максимального извлечения меди из шлака до проведения глубокого восстановления железа, так как, не удаляя медь, невозможно получить в восстановленном продукте необходимое соотношение Рb/Cu.
Показательным является опыт переработки шлаков свинцовой плавки, описанный И. М. Малкиным с сотрудниками. Шлак свинцовой плавки Лениногорского завода подвергали переработке в электропечи с коксовой проводимостью, получая чугун, отвальный шлак и возгоны.