Отжигальщик
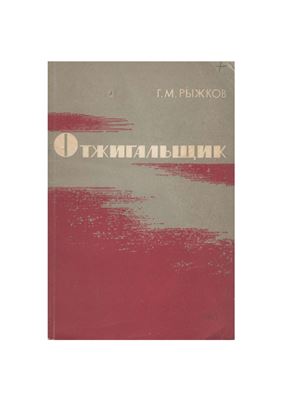
Рыжков Г.М.
Металлургиздат, 1963 г.
БРАК ТЕРМООБРАБОТКИ
45. Брак по твердости
Металл, после отжига не удовлетворяющий требованиям ГОСТ и ТУ вследствие завышенной твердости, должен подвергаться повторному отжигу по прежнему режиму. Допускается незначительное (на 10°) понижение температуры или сокращение выдержки примерно на 10—15%.
Установленные на заводах методы контроля изделий после термообработки не могут обеспечить 100% проверки изделий. Обычно подвергается контролю 2—3% изделий. Поэтому, чем хуже качество отжига, тем больше возможности пропустить брак в дальнейшую обработку.
Если металл с повышенной твердостью не задерживается на участке отжига, то при дальнейшей его обработке наблюдается ряд осложнений. Особенно пагубно влияет повышенная твердость на работу поточных автоматических линий. Если- металл назначается после термообработки в холодное волочение, то завышенная твердость ведет к повышенному износу волок и даже к трещинам на протягиваемом металле.
Восновномтвердыйметаллявляетсяследствиемнедогреваприотжиге. Причины недогрева следующие:
1) неправильные показания приборов, которые завышают температуру;
2) неправильная погрузка: металл данной марки стали погружен с металлом, режим термообработки которого предусматривает более низкую температуру;
3) нарушение формы садки; при этом перекрываются огневые каналы, движение газа по ним затрудняется или прекращается совсем, и отдельные участки садки недогреваются;
4) неправильное ведение режима давления: в печи в период выдержки имеется разрежение;
5) неправильный режим горения форсунок, в результате чего металл прогревается неравномерно.
Ускоренное охлаждение тоже может стать причиной получения твердого металла. Ускоренное охлаждение происходит при:
1) преждевременном открытии печи;
2) преждевременном замачивании в воде металла с целью удаления окалины;
3) попадании воздуха из форсунок на садку.
При перекрытии мазута необходимо, чтобы воздух тоже был перекрыт. Из-за неисправности дроссель воздухопровода может оказаться открытым при остановке печи на охлаждение. Попадая на металл, воздух резко охлаждает участок садки, что вызывает повышение твердости.
Перегрев металла также может быть причиной брака по твердости. Значительный перегрев (30—40°) при отжиге углеродистых инструментальных и шарикоподшипниковых марок стали приводит к получению грубо-пластинчатой структуры, часто с повышенной твердостью. Превышение температуры при высоком отпуске выше точки Aci может привести к образованию аустенита, а так как после отпуска металл охлаждается на воздухе или в воде, то происходит частичная закалка.
Превышение температуры во время высокого отпуска преобладающего большинства марок стали не приводит к браку по твердости, если садку охладить медленно, с печью. В этом случае произойдет вынужденная замена высокого отпуска отжигом. Но некоторые стали марок 18ХНВА, 25ХНВА, Х17Н2, нагретые до температур выше критических точек, будут твердыми даже при медленном охлаждении.
Отжигальщику следует знать трудно умягчающиеся при отжиге марки стали и обращать особое внимание на точность выполнения режима при их термообработке. Основные из этих марок: Р18, Р18М, ЭИ107 (Х10С2М), ШХ15СГ, У7, У8, 18ХНВА, 25ХНВА. Х17Н2, ЭИ736, ЭИ992. ЭИ474, 45ХНМФА. Для последних семи марок зачастую по технологии предусматривается двухкратный отпуск.
46. Брак по структуре
Для многих марок стали, например для инструментальных, шарикоподшипниковых и др., важно получить после термообработки не только низкую твердость, но и структуру зернистого перлита. Достигнуть этого труднее, так как не всегда при хорошей твердости сталь имеет хорошую структуру. Все те отклонения от технологии, которые являются причиной получения твердого металла, влекут за собой появление неудовлетворительной структуры.
При недогреве сталь в основном сохраняет структуру, образовавшуюся при охлаждении после прокатки.
При перегреве получается грубопластинчатая структура высокотемпературного отжига. При ускоренном охлаждении получается сорбит (структура чрезвычайно мелкопластинчатого перлита). Эти виды структур являются неудовлетворительными. Исправление структуры производится повторным отжигом по обычному режиму.
При сильном перегреве стали образуется крупнозернистая структура, хорошо видимая в изломе невооруженным глазом. Это — более серьезный брак, исправить его обычным отжигом уже невозможно. Для этого необходимо осуществить нормализацию и повторный отжиг.
Сталь с неудовлетворительной структурой бракуется потому, что при механической обработке ее затрачивается больше усилий. Кроме того, поверхность стали с пластинчатой структурой не может быть обработана с высокой точностью. Детали из стали с исходной структурой пластинчатого перлита после закалки имеют повышенную хрупкость. Наиболее трудно получить хорошую структуру на стали марок У7, У8, ШХ15.
47. Брак по карбидной сетке
Как известно, карбидная сетка образуется по границам аустенитного зерна при медленном охлаждении в интервале температур от Ас1 до Α1 заэвтектоидных сталей. Температура отжига находится значительно ниже Аст, поэтому при отжиге карбидная сетка образоваться не может. Карбидная сетка в структуре стали является результатом медленного охлаждения от температур прокатки.
При наличии карбидной сетки резко возрастает хрупкость закаленной стали, поэтому применять для изготовления деталей и инструмента сталь с карбидной сеткой нельзя.
Отжиг не устраняет карбидную сетку. Поскольку температура выдержки при отжиге значительно ниже Аст, растворение карбидной сетки при этом происходит очень слабо. Опыты показывают, что даже отжиг большой продолжительности (до 60 час.) снижает балл карбидной сетки всего лишь на 0,5. Устранить карбидную сетку можно лишь нормализацией с последующим отжигом. Однако далеко не на всех предприятиях имеются специальные печи для нормализации, а применение для нее обычных отжигательных печей далеко не всегда дает положительные результаты. Кроме того, нормализация с отпуском после неудовлетворительных результатов отжига часто приводит к недопустимому уменьшению размеров изделия, так как происходит окалинообразование. Для многих видов изделий этот способ вообще неприменим. Лучше всего не допускать образования карбидной сетки. Для этого необходимо от температур ковки и прокатки охлаждать сталь до 650—700° замачиванием в воде или в струе воздуха.
Охлаждение до более низких температур приводит к растрескиванию изделий крупных размеров.
Наличие карбидной сетки проверяется под микроскопом на закаленных шлифах. Инструментальная и шарикоподшипниковая сталь не должна иметь балл карбидной сетки более 3.
48. Брак по обезуглероженному слою
Обезуглероженный слой является самым опасным видом брака при термообработке, так как он влечет за собой тяжелые последствия и трудноисправим.
Обеднение углеродом поверхностного слоя стали или полное обезуглероживание его приводит к тому, что поверхность закаленной стали получается пониженной твердости. Инструмент из такой стали настолько быстро затупляется, что не может применяться при резании.
На шариковых и роликовых подшипниках с обезуглероженным слоем легко получаются вмятины на поверхности, и подшипники выходят из строя. На трущихся деталях машин из металла с обезуглероженным слоем легко получаются задиры, что ведет к поломке механизма. Из перечисленного ясно, что обезуглероженный слой в готовых изделиях может быть причиной крупных поломок и аварий.
Исправить обезуглероженный слой невозможно. Можно сделать металл годным, лишь удалив обезуглероженный слой. Это возможно в том случае, когда заготовка имеет необходимый припуск, и удаление слоя металла с обезуглероживанием не нарушит размеров готового изделия. Удаление обезуглероженного слоя производится окислением и механическим путем.
Окислением обезуглероженный слой переводится в окалину при отжиге. Этот специальный отжиг производится при пониженных на 20—30° температурах с большим избытком воздуха. Температуру понижают для того, чтобы в процессе сжигания уже имеющегося обезуглероженного слоя не получить новый. Такой способ приемлем далеко не для всех марок стали и не всегда дает положительные результаты. Нет смысла делать окислительный отжиг на стали марок 40ХН, 50ХН, 55СМА; 60С2А, У7 — У8, 9ХС.
Снятие металла с обезуглероженным слоем механическим путем производится обточкой, наждачной чисткой, шлифованием.
На получение обезуглероженного слоя при термообработке влияет температура, продолжительность выдержки, состав газовой среды. Чем выше температура, тем быстрее происходит
обезуглероживание поверхности. Начинаются процессы обезуглероживания в пламенных печах без защитной атмосферы при температуре 720—730°. Наиболее резко возрастает обезуглероживание при температурах выше 800°. При этом нельзя забывать, что стали разных марок по-разному реагируют на повышение температуры.
Чем длиннее выдержка, тем на большую глубину успевает проникнуть обезуглероживание. Правда, с течением времени скорость обезуглероживания уменьшается вследствие образования окалины, препятствующей проникновению обезуглероживающих газов в глубь металла. Влияние газовой среды зависит от температуры, взаимодействия различных составляющих газовой смеси и содержания углерода в обрабатываемом изделии, а также от присутствия различного рода катализаторов. Регулирование состава и контроль газа в печах без специальной атмосферы невозможны. Поэтому для предотвращения обезуглероживания отжигальщик должен строго соблюдать температуру и время выдержки.
Наиболее склонны к обезуглероживанию стали 40ХН, 50ХН. 55СМА, 60С2А, У7А, У8А, У10А, 9ХС, Р9, Р18, РЭМ, ΡΙ8Μ.