Основы технологии производства стали: Учебное пособие для вузов
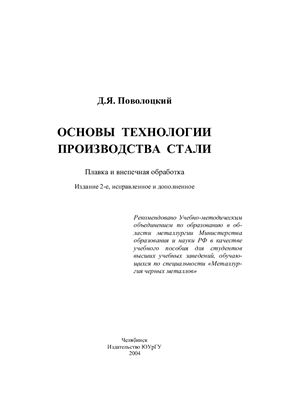
Поволоцкий Д.Я.
Челябинск: Изд-во ЮУрГУ, 2004 г.
Вторая половина XX в., уже с первых лет, ознаменовалась коренным изменением структуры и технологии сталеплавильного производства, существовавших в течение всей первой половины этого столетия. Началось это изменение в 1952 г., когда в Линце (Австрия) был осуществлен первый кислородно-конвертерный процесс – процесс LD (Linz Düssenstahl – нем.). К этому времени примерно 75 % мирового производства стали приходилось на мартеновский процесс, 10 % – на плавку в дуговых электрических печах (ДСП) и 15 % на конвертерные процессы – томасовский и бессемеровский. В США и СССР, в то время главных производителей стали, на долю мартеновского процесса приходилось 85–88 % ее производства. Значительно развито было томасовское производство в ФРГ (44 % всей стали), Франции (более 60 %) и других странах западной Европы, где используются высокофосфористые чугуны (P 1,4–2,2 %).
Кислородно-конвертерный процесс оказался весьма эффективным и имеет ряд преимуществ по сравнению с мартеновским: значительно большая производительность, меньшие капитальные затраты, гибкость в разнообразии выбора технологий, легкость управления процессом, возможность автоматизации плавки, улучшение экологической обстановки. По сравнению с бессемеровским и томасовским процессами кислородно-конвертерный процесс также имеет преимущества: низкое содержание азота в стали, возможность использования значительного количества скрапа (до 20–23 % вместо ∼3 %) глубокая дефосфорация, происходящая с самого начала процесса (в бессемеровском конвертере дефосфорация не происходит). Вследствие этих преимуществ кислородно-конвертерный процесс начал быстро распространяться в промышленно развитых странах, и уже к 70-му году в Японии, ФРГ, США на его долю приходилось 50–80 % всей выплавки стали. Вскоре он занял доминирующее положение в мировом производстве стали.
Интенсивное развитие кислородно-конвертерного процесса стимулировало развитие электросталеплавильного производства. Это было вызвано тем, что в шихте кислородных конвертеров можно использовать лишь до 23–25 % скрапа, и в этом он не мог заменить мартеновский процесс, где доля лома в шихте достигала 80 % и более. Поэтому применение для производства стали, взамен мартеновских печей, только конвертеров не могло обеспечить полное использование образующегося металлического лома. Плавка стали в ДСП, работающей на 100 % скрапа, явилась хорошей альтернативой плавке в кислородных конвертерах.
Успешному развитию производства стали в дуговых печах способствовали коренные изменения мощности печного трансформатора, конструкций дуговых печей и технологии плавки, которые произошли в начале 60-х годов и затем быстро распространились. Мощность печного трансформатора увеличилась с бывших к тому времени 200–250 кВ·А/т до 500–600, а затем до 800–1000 кВ·А/т. В сверхмощных ДСП в значительной части стен и свода футеровка заменена водоохлаждаемыми панелями. Ввиду того, что мощность трансформатора в полной мере используется лишь при плавлении и интенсивном кипении ванны в окислительный период, от восстановительного периода отказались. Рафинирование стали перенесли в ковш. В результате этих мероприятий продолжительность плавки, например в ДСП емкостью 100 т, сократилась с 4–5 ч до 50–60 мин. Расход электроэнергии уменьшился с 650–700 до 300–400 кВт·ч/т. Плавка стали в дуговых печах получила ряд преимуществ по сравнению с плавкой в мартеновских печах: более высокая производительность, меньше капитальные затраты и расходы на проведение процесса. Стало экономически выгодным производство в дуговых печах рядовой углеродистой стали.
Существенное повышение технико-экономических показателей кислородно-конвертерного и электросталеплавильного производств явилось, в значительной мере, следствием применения и интенсивного развития с начала 60-х годов внепечной обработки, которая стала непременной частью современной металлургии стали. Применение внепечной обработки привело к тому, что кислородный конвертер и дуговая печь превратились в агрегаты, предназначенные лишь для получения жидкого полупродукта, имеющего заданное, не всегда в узких пределах, содержание углерода, определенную минимально допустимую температуру и обычно ограниченное содержание фосфора. Значительная же часть операций рафинирования жидкой стали перенесена в ковш. Возникла, как называют в англоязычной технической литературе, «вторичная» или «ковшовая» металлургия, совершившая количественный и качественный скачок в развитии сталеплавильного производства.
Перенос ряда процессов рафинирования в ковш привело к повышению производительности сталеплавильных агрегатов, особенно дуговых печей, при плавке в которых отказались от восстановительного периода. Еще большее значение имело то, что применение разных методов внепечной обработки привело к значительному улучшению качества стали. Это явилось следствием повышения степени ее чистоты по неметаллическим включениям, понижения содержания в ней серы и газов, гомогенизации металла с выравниванием состава и температуры во всей массе в ковше, возможности получения содержания в стали элементов в весьма узких пределах. Оказалось возможным получение металла с ультранизким (≤ 0,0030 %) содержанием углерода, что стало основой производства стали нового класса с принципиально отличными свойствами.
Применение внепечной обработки привело к тому, что сталь одинакового качества стало возможным выплавлять как в кислородных конвертерах, так и в дуговых печах. Это дало мощный импульс разработке новых прогрессивных технологий выплавки стали в этих агрегатах и ее последующей внепечной обработки.
Имея явные преимущества в производительности, капитальных затратах, гибкости, возможности автоматизации, легкости обслуживания, кислородно-конвертерный процесс и плавка в ДСП по существу вытеснили и продолжают окончательно вытеснять мартеновский и томасовский процессы. В результате, во второй половине XX столетия структура мирового производства стали существенно изменилась (рис. 1). Мартеновское производство практически исчезло, его доля в общей выплавке стали уменьшилась до 4 %. При этом доля конвертерного производства увеличилась до 62 %, а плавка в ДСП до 30 %. В России на долю кислородно-конвертерного процесса приходится 59 % общего производства, плавки в ДСП – 15 %, мартеновского производства – 26 %.
Учитывая малую долю мартеновского процесса в производстве стали и явную тенденцию к его полному исчезновению, в настоящем курсе рассматриваются и сопоставляются только основы производства стали в кислородных конвертерах и в дуговых печах. Знание этих основ позволит без труда освоить и технологию мартеновского производства в случае такой необходимости.