Основы технологии получения поковок
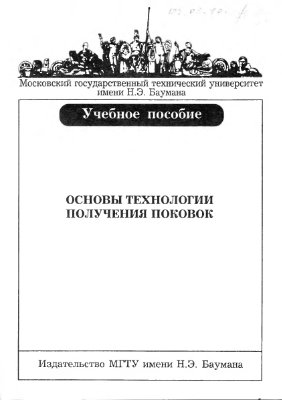
Евсюков С.А.
МГТУ им. Н. Э. Баумана, 2005 г.
ТЕХНОЛОГИЯ ПОЛУЧЕНИЯ ПОКОВКИ
1.1. Выбор способа получения поковки
Поковкой называют заготовку детали или деталь, полученную обработкой металлов давлением. Огромное разнообразие машиностроительных деталей и соответственно такое же разнообразие форм и размеров поковок, сплавов, характера производства обусловливает существование различных способов изготовления поковок.
Поковки машиностроительных деталей наиболее часто изготавливают ковкой, горячей объемной штамповкой (ГОШ) и холодной объемной штамповкой (ХОШ). Технологии получения поковки различают в зависимости от способа изготовления. Поэтому разработке технологического процесса получения поковки предшествует этап выбора рационального способа изготовления.
Во многих случаях точный выбор наиболее рационального способа получения поковки является довольно сложной задачей, так как часто сразу несколько способов обработки давлением могут надежно обеспечить выполнение технологических и эксплуатационных требований к детали. Целесообразность применения τογό или иного способа необходимо оценивать с учетом большого количества факторов, а также технико-экономических показателей (например, коэффициента использования метала - КИМ, себестоимости и т. д.), достигаемых при различных способах получения поковки. Поэтому на начальном этапе определения рационального способа получения поковки целесообразно учитывать лишь некоторые наиболее характерные критерии, влияющие на выбор способа получения поковки. Среди этих критериев выделим следующие:
- размер партии изготовляемых деталей (характер производства: единичное, мелкосерийное, крупносерийное и пр.);
- размеры и масса детали;
- материал, из которого изготовляется деталь;
- геометрия детали.
1.2. Размер партии деталей
Этот критерий может существенно повлиять на выбор рационального способа получения поковки. Так, в условиях единичного или мелкосерийного производства, при изготовлении небольших партий деталей, нецелесообразно применение специальной технологической оснастки (например, штампов), которая увеличивает себестоимость поковки. В этом случае наиболее оправданно применение ковки, причем неизбежны большие припуски и напуски, значительный объем последующей механической обработки резанием. Повышение точности размеров поковок и снижение припусков требуют применения дополнительной технологической оснастки (например, использования подкладных штампов), что при изготовлении небольших партий поковок существенно увеличивает затраты. В то же время при размере партии поковок N > 50 - 150 применение подкладных штампов может быть целесообразным.
В условиях серийного производства становятся рентабельными различные способы штамповки на молотах и прессах, а в условиях крупносерийного и массового производства рациональны способы штамповки на прессах в сочетании с выносом отдельных формоизменяющих операций на специализированное оборудование (например, ковочные вальцы).
1.3. Размер и масса поковки
Данный критерий при выборе способа получения поковки иногда играет решающую роль. Так, габаритные размеры поковок ограничены техническими возможностями применяемого оборудования и инструмента. Например, на существующем оборудовании для ГОШ не представляется возможным получение поковок массой более 1000 кг. В то же время особенности деформирования заготовки в процессе ковки (поковка деформируется последовательно по отдельным участкам при свободном течении металла, который не ограничен стенками инструмента) позволяют изготавливать крупногабаритные и массивные поковки массой до 250 т.
Масса и габариты детали чаще всего являются определяющими критериями при выборе температурного режима обработки давлением. При больших габаритах и массе детали предпочтительной становится деформация с нагревом, при которой меньше давление на инструмент и меньше сила, необходимая для деформирования. Поковки диаметром более 150...200 мм получают, как правило, горячим деформированием. При меньших размерах, если это возможно, предпочтительнее выбрать холодное деформирование, поскольку оно более экономично (меньше отходов, ниже энергозатраты и пр.). Следует отметить, что примерно 15...20 % всех производственных затрат связано с нагревом.
1.4. Технологические свойства материала
Чем ниже пластичность материала, тем сложнее получить качественную поковку и тем сложнее технологический процесс. Так, при изготовлении поковок из труднодеформируемых сплавов с пониженной пластичностью предпочтение следует отдавать способам, обеспечивающим схему нагружения, близкую к трехосному неравномерному сжатию (штамповку в закрытых штампах, выдавливанием и т. п.). Сопротивление металла деформированию также является важным фактором, который обусловливает нагрузки, возникающие на инструменте. Поэтому при деформировании прочных материалов следует выбирать схемы штамповки с меньшими силами деформирования.
Сказанное выше следует учитывать при выборе того или иного способа холодной объемной штамповки, при которой особенно жесткие требования предъявляют к технологической пластичности и сопротивлению деформированию штампуемых материалов. Особенностью этих процессов являются очень высокие давления пластического течения металла, достигающие пяти-шести пределов текучести (для алюминиевых сплавов - до 1200 МПа и до 3000 МПа - для сталей) и низкая пластичность в холодном состоянии. Поэтому для ХОШ применяют материалы, имеющие показатель пластичности не менее 20...30 % и напряжение текучести στ < 600 МПа, при этом следует также учитывать масштабный фактор (массу поковки) и схему деформирования.
При объемной штамповке чаще всего используют заготовки из низко- и среднеуглеродистых сталей, некоторых низколегированных сталей, пластичных
(предназначенных для обработки давлением) алюминиевых и медных сплавов.
1.5. Геометрия детали
Этот фактор в ряде случаев достаточно точно предопределяет выбор рационального способа получения поковки. Поковки, получаемые ГОШ, классифицируют по соотношению линейных размеров в плане (круглые в плане и близкие к кругу по форме, с удлиненной осью, с изогнутой осью и т. п.), по наличию сквозных или глухих полостей и т. д. В соответствии с этой классификацией поковки можно разделить на пять групп (табл. 1). Из этой таблицы ясно, что, например, для деталей, близких по форме к поковкам группы 1, рациональным способом штамповки является штамповка в открытых штампах на молоте, так как при молотовой штамповке можно использовать многоручьевые штампы с широким набором заготовительных ручьев. При достаточно больших партиях поковок (крупносерийное и массовое производство) эффективным может быть применение штамповки на прессе с выносом заготовительных, профилирующих переходов на отдельное оборудование.