Основы порошковой металлургии. Свойства и применение порошковых материалов
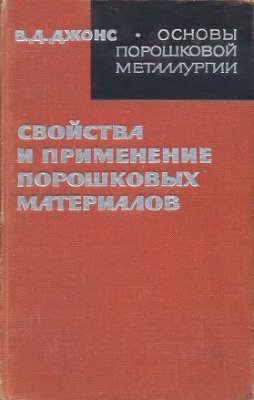
Джонс В.Д.
Мир, 1965 г.
Примеси в магнитных материалах
Немагнитные или слабо магнитные включения и поры могут вызывать значительные местные изменения магнитостатической энергии [130]. Количественное влияние примесей было определено в работах [130, 131]. Неель [132] отметил, что при наличии в ферромагнитной матрице немагнитного включения возникают неоднородности внутреннего намагничивания; они приводят к образованию свободных магнитных полюсов вокруг этого включения. Добавочная магнитостатическая энергия, возникающая в этом случае, может быть сведена к минимуму за счет образования вторичной доменной структуры. Такая «шлейфовая структура» была впервые сфотографирована Уильямсом [133]; хорошим примером ее является фотография на фиг. 31, на которой видны два шлейфовых домена по обе стороны от 180°-ной доменной стенки, проходящей по середине фотографии.
Насколько вредно влияние примесей при производстве магнитномягких материалов? Примеси вредно влияют на свойства литых, прокованных и прокатанных материалов [135, 136]. В тонких лентах железоникелевых сплавов магнитная проницаемость имеет более низкие значения у поверхности ленты по сравнению с серединой. В результате стравливания поверхностных слоев у мягкого железа, железоникелевых сплавов или хромистых пермаллоев у этих материалов повышается магнитная проницаемость и снижаются потери на гистерезис [137]. Поверхностные слои материалов, полученных прокаткой, характеризуются более низкими значениями магнитной проницаемости и более высокими потерями на гистерезис.
Для получения качественной тонкой магнитной ленты необходимо прокатывать относительно толстые ленты и удалять поверхностные слои электрополировкой или травлением [138].
Хорошо известно, что значение магнитной проницаемости для разных образцов одного и того же материала может колебаться в широких пределах. Например, начальная магнитная проницаемость пермаллоевой ленты толщиной 50 мк может меняться от 40000 до 2000 [139]. Подобное явление наблюдается и для ленты толщиной 125 мк после выдержки в течение 4 лет [140].
При микроскопическом исследовании литых и катаных сплавов такого типа обнаружено, что в слоях, примыкающих к поверхности, размер включений и зерен значительно меньше, чем во внутренних слоях (фиг. 34).
Весьма вероятно, что это явление определяется внутренним окислением. Магнитная проницаемость лент, отожженных в очень чистом сухом водороде, намного выше, чем у лент, отожженных во влажном водороде [136]. Для получения наилучших свойств необходимо, чтобы точка росы защитных газов была не выше —60° С. Вероятно, этот эффект вызывается диффузией кислорода из атмосферы отжига через решетку металла и последующим взаимодействием со следами Mg, А1 или Si, которые применялись в качестве раскислителей при плавке магнитных материалов. Следовательно, высококачественные литые материалы могут быть получены только при очень тщательном контроле, позволяющем избежать загрязнения элементами с более высокой энергией образования окислов, чем железо, или при достижении полной их гомогенности благодаря применению дорогостоящей холодной обработки и продолжительного отжига в очень сухом водороде.
В этом отношении весьма полезным может оказаться использование технологии порошковой металлургии, которая позволяет получать порошки Ni, Fe, Mo и Сu с очень низким содержанием вредных примесей. При этом могут быть использованы обычные методы порошковой металлургии (прокатка порошков или спеченных заготовок) без применения очень чистого водорода. Необходимо только следить, чтобы загрязнения не попали в материал в процессе производства (например, кремний, восстанавливаемый из футеровки печи). У изделий из железоникелевых сплавов, полученных методами порошковой металлургии, значительно более высокая магнитная проницаемость, чем у изделий, полученных из литых и прокатанных сплавов [141]. Более того, при спекании таких материалов можно применять при отжиге водород с точкой росы 20° без ухудшения магнитных свойств. Полученные при этом значения магнитной проницаемости для ленты из сплава Ni — Fe приведены в табл. 5.
Можно ли получить у порошковых материалов более высокие магнитные свойства, чем у обычных сплавов, пока не ясно. В работе [136] указано, что производство спеченной ленты пока находится в стадии лабораторных исследований. Если принять во внимание, что ленту прокатывали из заготовок, спеченных из карбонильных порошков никеля и железа, то замечание авторов о высокой стоимости процесса следует, вероятно, признать справедливым. Однако, применяя прокатку более дешевых, но таких же чистых порошков (например, никель, восстановленный водородом из растворов, и электролитическое железо), можно, по-видимому, добиться, что стоимость спеченной ленты будет ниже стоимости ленты, полученной из компактных металлов.
Кристаллографическая анизотропия
Железо и сплавы железа магнитно анизотропны, т. е. обладают различными магнитными свойствами по разным кристаллографическим направлениям кристаллической решетки. В сплавах, богатых железом, наибольшая проницаемость и наименьшие потери, а также наименьшая энергия намагничивания наблюдаются по направлениям [100], совпадающий с ребрами кубической решетки.
Соответствующей прокаткой и отжигом можно добиться создания текстуры в листовом металле. Например, в кремнистых сталях можно достичь значительного изменения магнитных свойств в зависимости от направления последних проходов прокатки. Если нарезать образцы так, чтобы магнитный поток был почти параллелен направлению прокатки, проницаемость может быть больше на 20—30%, а потери в сердечнике меньше на 10—15% по сравнению с материалом, структура которого состоит из случайно ориентированных зерен. Свойства в других направлениях могут быть лучше или, наоборот, хуже, чем в материале со случайно ориентированными зернами. Это объясняется тем, что прокаткой можно добиться создания такой текстуры, при которой направление [001] будет параллельно направлению прокатки, а плоскость (100) — совпадать с плоскостью листа.
Вследствие хорошей проницаемости и высокого электросопротивления тысячи тонн мат риала с ориентированной структурой используются для производства мощных электромоторов, работающих на токах низкой частоты. Еще более благоприятные магнитные свойства обнаруживают листы с так называемой кубической текстурой, при которой направления [001] совпадают с направлением прокатки и с перпендикулярным направлением.
Безуспешные ранние попытки получить такую кубическую текстуру в сплавах с объемноцентрированной кубической решеткой (например, Fe — Si) привели к общему мнению, что по крайней мере в промышленном масштабе ее получить невозможно. Однако в 1957 г. была получена листовая кремнистая сталь (3% Si) с кубической текстурой [139], а в 1958 г. две американские фирмы почти одновременно сообщили о получении листовой трансформаторной стали этого типа [140, 141]. Такие же листы с кубической текстурой толщиной до 2,5 мм были изготовлены из сплавов железо — алюминий [147] и молибден — железо.
Магнитные испытания образцов в виде отдельных полос при постоянном и переменном токе частотой 60 гц показали почти одинаковые магнитные свойства в направлении прокатки и перпендикулярно к нему, совпадающие со свойствами, измеренными на материале с зернами, ориентированными по направлению только одного ребра решетки. Эти результаты имеют большое практическое значение. Например, потери энергии в сердечнике трансформатора, изготовленного из материала с кубической текстурой, при всех значениях индукции значительно меньше. Потери в таком сердечнике при индукции в 17 000 гс составляют около 60% потерь в сердечнике из обычного материала, в котором зерна ориентированы только в направлении ребра; для возбуждения указанной индукции в материале с кубической текстурой требовался вдвое меньший ток по сравнению с материалом с ребровой текстурой.
В настоящее время такие материалы с кубической текстурой, по-видимому, еще не получают методами порошковой металлургии, хотя нет принципиальных причин, которые бы сделали это невозможным. Выше уже отмечалось, что достигнут значительный успех в получении вольфрамовых нитей с нужной ориентацией кристаллов за счет применения летучих и нелетучих присадок. Для успешного экспериментирования в том же направлении с кремнистыми сталями имеются хорошие предпосылки; особенно после того, как было показано, что предпочтительную текстуру вторичной рекристаллизации можно получить, вводя в слитки вакуумного кремнистого железа по 0,05—0,1% марганца и серы [148]. Кроме того, по-видимому, возможно механически или магнитным путем ориентировать частицы (монокристаллы) порошка при подаче его в пресс-форму или на прокатку. Следует помнить, что состав обычной (компактной) листовой кремнистой стали ограничен 4% Si (уже при таком его содержании материал слишком хрупок для прокатки), тогда как путем прокатки порошков возможно, по-видимому, получать тонкие листы с более высоким содержанием кремния.
Прокаткой и отжигом спеченных штабиков сплава Fe — 3,25% Si с 0,025% Si02 в качестве диспергированной фазы, необходимой для вторичной рекристаллизации, удалось получить текстуру по направлению [001] в плоскости (ПО) [149]. Включения двуокиси кремния не были видны под микроскопом. В сплав ее специально не вводили; она образовывалась за счет окисления частиц кремния при спекании штабиков сплава. Этот процесс контролировался при спекании по точке росы. Если точка росы была слишком высокой или слишком низкой, то образования требуемой структуры не наблюдалось. Чем выше температура спекания, тем выше должна быть точка росы.
Процесс состоял из следующей типичной последовательности операций. Смесь порошков кремния и карбонильного железа прессовали под давлением 40 кг/мм2 и подвергали предварительному спеканию для раскисления порошка никеля при 300° в водороде (точка росы —65°). Спекание продолжалось до тех пор, пока влажность газа, поступающего в печь и выходящего из нее, не становилась одинаковой. Затем температуру повышали до 1050—1200° и точку росы контролировали по ранее установленным данным. Спекание продолжалось в течение 12 час, после чего Этот материал прокатывали в полосы по следующей схеме: 1) прокатка до 3,175 мм; 2) отжиг в водороде при 1050° в течение 12 час (точка росы —65°); 3) прокатка до 0,5 мм; 4) отжиг в водороде при 800° в течение 1 час (точка росы —65°); 5) прокатка до 0,33 мм; 6) отжиг в водороде при 1350° в течение 12 час (точка росы —40°); 7) прокатка до 0,10 мм; 8) отжиг по такому же режиму, как (6).
Точка росы операций отжига 4), 6) и 8) не оказывала влияния на конечные свойства полосы. Такие же хорошие результаты были получены при использовании водорода, насыщенного парами воды.