Основы порошковой металлургии
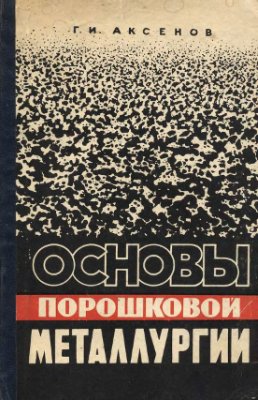
Аксенов Г.И.
Куйбышев, 1962 г.
ВВЕДЕНИЕ
Порошковой металлургией называется отрасль техники, занимающаяся получением металлических порошков и изготовлением из них полуфабрикатов или готовых изделий. По мере развития техники получения металлических порошков, особенно тугоплавких металлов, их производство включалось в систему предприятий цветной или черной металлургии. По существу, технология производства металлических порошков цветных металлов представляет собой один из методов получения металлов из руд путем сложной химико-металлургической переработки. Лишь металлы из окислов в силу своей простоты с помощью различных восстановителей получаются на предприятиях собственно порошковой металлургии с замкнутым циклом производства.
В настоящее время ряд металлов в чистом виде может быть получен только в виде порошка. К ним относятся: железо, никель, медь, титан, вольфрам, молибден, хром, тантал, цирконий, ниобий и др. В технике чистые металлы применяются в виде стержней, прутков, полосок, из которых делаются детали (например, для электровакуумных приборов). Поэтому порошок чистого металла должен быть превращен в указанные профили. Этим и занимается порошковая металлургия.
Чистый вольфрам получается в виде порошка. Из порошка прессуют штабики, которые после нагрева до температуры около 3000° делаются достаточно прочными и пригодными для дальнейшей ковки и протяжки в тонкую проволоку. Так готовят в настоящее время вольфрамовую проволоку для нитей электрических. ламп, а также
для нитей накала усилительных и генераторных ламп, применяемых в радиотехнике.
Современное силовое и скоростное резание металлов производится резцами с наплавленными пластинками из твердых сплавов типа «победит». Эти пластинки представляют собой спеченную смесь порошков карбида, вольфрама и титана с порошком чистого кобальта. У нас и за границей такие пластинки выпускают специальные заводы.
Прерыватели магнето в двигателях внутреннего сгорания, обеспечивающие образование искры в цилиндре, контакты в слаботочной технике (телефонии), в контакторах для пуска и остановки электромоторов изготовляются из порошков вольфрама, серебра, меди, никеля и некоторых окислов.
Электротехническая промышленность, являющаяся основным потребителем всевозможных видов контактов, в настоящее время имеет в г. Кинешме свое предприятие по изготовлению контактных материалов. Щетки электродвигателей и электрогенераторов делаются из смеси порошкообразных графита и меди также на специализированном предприятии.
Современная электроника своими успехами во многом обязана разработке новых, магнитных материалов, которые имеют общее название — ферриты. Кроме того, большое количество постоянных магнитов с различными характеристиками, так же как и ферриты, получаются только' методами порошковой металлургии.
Эти примеры показывают, что порошковая металлургия является поставщиком таких новых видов материалов, которые другими методами не могут быть получены-
Порошковая металлургия располагает средствами для получения не только порошков чистых металлов, но и сплавов, что позволяет экономить дорогие и дефицитные легирующие элементы.
Из порошка можно прессовать деталь заданных размеров и после спекания получить ее готовую для дальнейших доводочный операций. При этом химический состав детали остается неизменным. Таким образом экономится большое количество металла, ибо стружки почти нет. Вместе с тем значительно снижается трудоемкость изготовления.
Из железных порошков с добавками других порошков (меди, графита и т. д.) можно делать втулки для подшипников скольжения вместо бронзовых; поршневые кольца для двигателей внутреннего сгорания взамен чугунных; шестерни для насосов, подающих масло или охлаждающую эмульсию, взамен изготовляемых из литого металла (с отходом в стружку до 80%).
Для получения железного порошка в качестве исходного продукта берутся или отходы производства (окалина, пылевидная руда), или чистая руда. После восстановления одним из многих методов (к настоящему времени насчитывается около 70 методов восстановления окислов железа до чистого металла) получается железная губка, которая подвергается размолу в порошок и рассеву по фракциям.
Полученный порошок сначала подготовляется (смешивается с другими порошками), а затем прессуется в специальных пресс-формах гидравлическими или механическими прессами. В пресс-форме порошок принимает форму детали, которая оказывается достаточно прочной, чтобы ее можно было удалить из пресс-формы и транспортировать на следующие операции. Прочность прессовки повышается спеканием. Оно заключается в нагреве детали до температуры выше порога рекристаллизации, но ниже температуры плавления металла. Во время спекания происходит образование металлического контакта между отдельными частицами порошка, и механическая прочность прессовки возрастает. Для улучшения образования металлического контакта спекание ведется обязательно в восстановительной атмосфере (водород, окись углерода и пр.).
После спекания прессовка подвергается дополнительной обработке (калибровка, пропитка маслом, чистовая проточка и т. п.) и делается вполне готовой для установки в механизм. Здесь можно отметить, что качество изделия зависит от свойств исходного порошка, от условий прессования и режима спекания. Однако все этапы технологического процесса получения детали из порошка в одинаковой мере влияют на качество готового изделия.
Теперь уже совершенно очевидно, что механические свойства прессовки из любого порошка зависят от состояния, исходного порошка, режимов прессования и спекания. Эти этапы следует рассматривать во взаимной связи друг с другом. Поэтому правильнее будет изложение основ порошковой металлургии начинать с описания физической природы частиц порошков, полученных разными методами. Затем изложить макро- и микроявления, происходящие при прессовании, и, наконец, завершить это современным состоянием вопроса о теории спекания и дать в первом приближении механизм спекания одно- и многокомпонентных систем.
В настоящее время машиностроительная промышленность при обработке превращает в стружку около 25—30% металла. Ее брикетируют, пакетируют и отправляют на металлургические заводы в мартеновские печи. Нетрудно подсчитать, сколько тонн металла в виде отходов возвращается обратно на переплавку. С такой технологией сжились и считают ее нормальной: металлурги плавят и прокатывают, транспортники перевозят, а у машиностроителей по-прежнему значительная часть металла уходит в стружку. А ведь ее можно превратить в железный или стальной порошок, из которого можно путем прессования и спекания изготовлять разные детали или изделия. В этом направлении сделано очень мало и можно .назвать лишь одну работу, в которой показана принципиальная возможность превращения стальной стружки в порошок.