Основы литейного производства
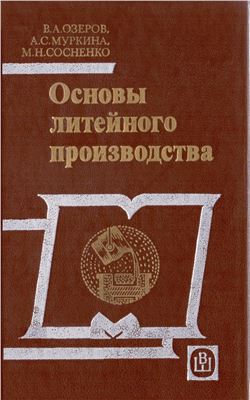
Озеров В.А., Муркина А.С., Сосненко М.Н.
Высшая школа, 1987 г.
5.5. ЛИТЕЙНЫЕ СТАЛИ
К литейным сталям относят железоуглеродистые сплавы, содержащие до 2,14% С и другие элементы (Мn, Si, Ρ, S, Cr, Ni, W, Mo, V и т. д.), попавшие в сталь из шихтовых материалов либо специально введенные в нее в определенных количествах для придания сплаву необходимых эксплуатационных и технологических свойств.
В настоящее время стальные отливки используют во всех отраслях машиностроения; по объему производства они занимают второе место после чугунов. Из сталей отливают обычно детали, κ которым предъявляют повышенные требования по прочности, пластичности, надежности и долговечности в процессе эксплуатации. Литейные стали классифицируют в основном по способу выплавки, химическому составу, структуре, назначению. По химическому составу литейные стали разделяют на углеродистые, а также низко-, средне- и высоколегированные.
По структуре углеродистые стали могут быть ферритными или перлитными, а легированные—ферритными, мартенситно-ферритными, мартенситными, аустенитно-мартенситными, аустенитно-ферритными и аустенитными. Так как стальные отливки обычно подвергают термической обработке, стали классифицируют также по структуре в термически обработанном состоянии. Так, для термически обработанных углеродистых и многих низко- либо среднелегированных сталей характерна перлитная структура, а для высоколегированных жаропрочных и жаростойких сталей, так же как и для износостойкой высокомарганцовистой стали 110Г13Л,— аустенитная. Структура отливок из высоколегированных сталей в основном определяется природой и количеством легирующих элементов, содержанием углерода, режимом термической обработки, поэтому приведенная выше классификация этих структур условна. В зависимости от скорости охлаждения, например, у сталей мартенситного класса можно получить перлитную структуру и наоборот.
В зависимости от назначения литой детали и требований к ней конструкционные нелегированные и легированные стали разделены (согласно ГОСТ 977—75) на три группы: для изготовления отливок общего назначения, ответственного назначения и особо ответственного назначения. Для каждой группы отливок установлены показатели контроля. Для отливок I группы допускается содержание в стали 0,С5—0,06% S и 0,05—0,087% Р; для отливок II группы —0,045—0,06% S и 0,04—0,07% Р; для отливок III группы — 0,045—0,05% S и 0,04— 0,05% Р. Содержание других элементов одинаково для сталей всех групп отливок.
По способу выплавки различают стали, выплавленные в печах с кислой и основной футеровкой, так как состав футеровки оказывает существенное влияние на ход процесса плавки и свойства готового сплава. В печах с кислой футеровкой, главной составляющей которой является кремнезем S1O2, выплавляются обычно углеродистые и многие низколегированные конструкционные стали. В печах с основной футеровкой (магнезитовой, магнезитохромитовой, хромомагнезитовой) выплавляют преимущественно средне- и высоколегированные стали.
Большую часть фасонных отливок (около 65%) изготовляют из углеродистых конструкционных сталей (ГОСТ 977—75) следующих марок 15Л, 20Л, 26Л, ЗОЛ, 35Л, 40Л, 45Л) 50Л, 55Л. В обозначении марки число означает среднее содержание углерода в сотых долях процента (например, для марки 25Л—0,25% С), а буква «Л» указывает, что сталь предназначена для литья (табл. 5.5.). Как видно из приведенных в таблице данных, с увеличением содержания углерода повышается прочность и снижаются пластические свойства сталей.
5.5. Свойства некоторых углеродистых конструкционных литейных сталей
Сталь | Состав, % (Fe-основа) | Механические свойства (после нормализации), не менее | Температура заливки, °с | |||||
С | Μη | σв | στ | 6 | ψ | КСU | ||
МП а | % | Мдж/ м2 | ||||||
15Л | 0,12—0,2 | 0,3—0,9 | 400 | 200 | 24 | 35 | 0,5 | 1560—1630 |
20Л | 0,17—0,25 | 0,35—0,9 | 420 | 220 | 22 | 35 | 0,5 | 1560—1630 |
25Л | 0,22—0,3 | 0,35—0,9 | 450 | 240 | 19 | 30 | 0,4 | 1500—1580 |
45Л | 0,42—0,5 | 0,4—0,9 | 550 | 320 | 12 | 20 | 0,3 | 1460—1560 |
55Л | 0,52—0,6 | 0,4—0,9 | 600 | 350 | 10 | 18 | 0,25 | 1460—1560 |
Одновременно улучшается жидкотекучесть их и уменьшается усадка. Важное значение имеют требования, указанные в примечаниях в отношении содержания вредных примесей — серы и фосфора. Сера вызывает склонность сталей к образованию горячих трещин, а фосфор — хрупкость при обычных и низких температурах.
В ГОСТ 977—75 (СТ СЭВ 4459—84, СТ СЭВ 4561— 84) предусмотрено также сорок пять марок легированной (Сг, Ni, Μη, Mo, V, Си и др.) конструкционной стaли с содержанием каждого из легирующих элементов не более 2% (масс).
На отливки из высоколегированных сталей со специальными свойствами установлен ГОСТ 2176—77. Стандартом установлено 30 марок высоколегированных сталей указанного назначения. Марки включают буквенное обозначение легирующих элементов и следующие за ним числа, указывающие на среднее содержание этого элемента в массовых процентах. Числа в начале наименования марки характеризует среднее содержание углерода в процентах, а буква «Л» в конце показывает, что сталь предназначена для фасонного литья. Так, широко используемая в машиностроении коррозионно-стойкая (нержавеющая) сталь аустенитного класса 10Х18Н9ТЛ содержит не более 0,12% углерода, 17— 20% хрома, 8—11% никеля и до 0,6°/0 титана, а отличающаяся высокой износостойкостью высокомарганцовистая сталь 110Г13Л, идущая, например, на отливку звеньев гусениц тракторов и других гусеничных машин, содержит 0,9—1,3% углерода и 11,5—14,5% марганца. Для большинства рассматриваемых легированных сталей строго ограничивается содержание вредных примесей (до 0,03—0,035% серы и до 0,035—0,С4% фосфора). Буквенные обозначения легирующих элементов приняты теми же, что и в марках легированных чугунов (см. примечание к табл. 6.3), а других: Φ — ванадий, В — вольфрам, Б — ниобий, Ρ — бор.
ГОСТ 21357—75 установлен на отливки из хладно-стойкой и износостойкой стали для деталей машин и металлоконструкций, эксплуатируемых при температурах до —60°С. К числу этих сталей относят углеродистые и легированные конструкционные (например, 15ЛС, 35МЛС, 30ХМЛС, 35ХГСМЛС), а также высоколегированные со специальными свойствами 10Х18Н9МЛС и 110Г13МЛС. Буква «С» в конце марки указывает, что эта сталь предназначена для работы при температурах до —60°С. В рассматриваемых сталях хладностойкость и повышенная износостойкость обеспечиваются низким содержанием вредных примесей — серы и фосфора (не более 0,02% каждой), а также обработкой этих сталей при плавке комплексными раскислителями и лигатурами редкоземельных и других металлов в сочетании со специальными режимами термической обработки готовых отливок.