Основы фрезерного дела
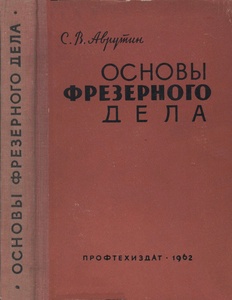
Аврутин С.В.
Профтехиздат, 1962 г.
§ 1. ОБЩИЕ ПОНЯТИЯ О ФРЕЗЕРОВАНИИ
Фрезерование является одним из способов обработки резанием. Оно осуществляется с помощью многолезвийного инструмента, называемого фрезой.
Фреза при вращении врезается зубьями в надвигающуюся на нее заготовку, закрепленную на столе станка, и срезает каждым своим зубом с ее поверхности стружку, придавая заготовке предусмотренные чертежом очертания и размеры.
В зависимости от расположения зубьев относительно обрабатываемой поверхности различают цилиндрические (рис. 1, а) и торцовые фрезы (рис. 1, б). Все другие виды фрез — дисковые пазовые (рис. 1, в), дисковые трехсторонние (рис. I, г), отрезные (рис. 1, д)и концевые (рис. 1, е)— можно условно рассматривать как одни из этих двух основных типов.
Вращение фрезы вокруг своей оси называют главным движением, а поступательное движение заготовки — движением подачи. Оба эти движения осуществляются фрезерным станком.
Главное движение, т. е. вращение фрезы, определяется числом оборотов шпинделя станка в минуту (об/мин) и характеризует скорость резания. Движение подачи характеризуется величиной минутного перемещения стола станка с закрепленной на нем заготовкой относительно фрезы. Эта величина выражается в миллиметрах в минуту (мм/мин).
Фрезерование является весьма производительным процессом механической обработки резанием, поэтому оно сравнительно быстро получило широкое применение.
Особенно большое распространение получило фрезерование с развитием крупносерийного и массового производства, так как оно позволяет обрабатывать в больших количествах одинаковые детали с заданной точностью при малых затратах рабочего времени.
Развитие фрезерного дела и широкое применение фрезерования вызвали в свою очередь ряд усовершенствований фрезерного инструмента и фрезерных станков, в результате чего непрерывно растет производительность труда и повышается качество выполняемых работ.
Нет ни одной отрасли машиностроения, начиная с производства точных приборов и кончая сооружением крупнейших гидравлических турбин, где бы для обработки деталей не применялось фрезерование.
Рис. 1. Основные виды фрез:
а — цилиндрическая; б — торцовая; в — пазовая; г — дисковая трехсторонняя; д — отрезная (шлицевая); е — концевая
Фрезерные станки выпускаются рядом отечественных предприятий: Горьковским, Одесским и Дмитровским заводами фрезерных станков, Ульяновским заводом тяжелого машинострое ния, заводом «Жальгирис» в г. Вильнюсе и др.
§ 2. КВАЛИФИКАЦИОННАЯ ХАРАКТЕРИСТИКА ФРЕЗЕРОВЩИКА
1-ГО РАЗРЯДА
Квалификационная характеристика фрезеровщика 1-го разряда по новому квалификационному справочнику соответствует 3-му разряду прежнего справочника; она приведена в программе
для индивидуальной и бригадной подготовки фрезеровщиков, изданной Трудрезервиздатом в 1959 г.
За время обучения фрезеровщик должен изучить также передовые приемы работы, а именно: методы скоростного фрезерования, работу с многоместными приспособлениями, со сборными и фасонными фрезами, методы многостаночного обслуживания и т. д.
Получив эти знания, фрезеровщик должен постоянно повышать свою квалификацию на производстве, тщательно изучая выполняемые работы и постоянно следя за технической литературой по фрезерному делу.
ФРЕЗЫ
§ 18. ОСНОВНЫЕ СВЕДЕНИЯ О РЕЖУЩЕМ ИНСТРУМЕНТЕ
Способы обработки. В машиностроении применяют много различных материалов: сплавы из черных и цветных металлов, пластмассы, дерево и т. д. Заготовкам из этих материалов в зависимости от их назначения необходимо придать требуемую форму и размеры, которые могут быть получены в процессе обработки. Различают два способа обработки:
а) обработку без снятия стружки: литье, ковку, горячую и холодную штамповку, прессование и т. д.;
б) обработку со снятием стружки, т. е. механическую обработку на токарных, фрезерных, строгальных, сверлильных и других станках.
Заготовка должна иметь припуск, т. е. слой материала, который срезают при механической обработке, чтобы получить требуемые форму и размеры детали, а равно качество ее поверхности.
При механической обработке резанием припуск с заготовки удаляют с помощью режущих инструментов. В зависимости от вида обработки режущие инструменты отличаются друг от друга по конструкции. Однако все эти многочисленные конструкции созданы на основе токарного или строгального резца обычной формы путем увеличения количества режущих граней, изменения его профиля или основных углов. Принцип работы для всех режущих инструментов совершенно одинаков.
Простейший резец и его работа. Режущая часть каждого режущего инструмента по форме представляет клин. Под действием приложенной к резцу силы острие клина углубляется в обрабатываемый материал, нарушает сцепление его частиц и сдвигает отделяемый слой в сторону.
На рис. 44, а показан простейший резец, врезающийся в заготовку для снятия припуска.
Чем острее клин, т. е. чем меньше угол, образованный его сторонами, тем меньшее усилие требуется для его внедрения в материал. Так, чем острее нож, тем легче он режет. Угол, образованный сторонами клина, называют углом заострения и обозначают греческой буквой (бета). Следовательно, чем меньше угол заострения β, тем легче резец проникает в материал, и, наоборот, чем больше угол заострения β, тем большую силу надо приложить для резания материала.
Следует считаться с тем, какой материал необходимо резать. Если резать твердый материал инструментом, имеющим малый угол заострения р, то тонкое лезвие не выдержит и выкрошится либо сломается. Поэтому в зависимости от твердости подлежащих резанию металлов назначают соответствующий угол заострения резца.
Под влиянием силы Р (рис. 44,6) передняя поверхность резца сожмет слой обрабатываемого материала и, преодолев внутренние силы сцепления частиц материала, надломит кусочек его, а затем отведет его вверх. Этот кусочек называют элементом стружки. Резец, продвигаясь дальше под действием приложенной силы, будет снова сжимать, а затем скалывать (надламывать) следующие элементы стружки и, таким образом, снимать слой материала, т. е. резать.