Образование трещин при термической обработке стальных изделий
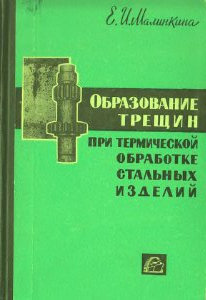
Малинкина Е.И.
Машиностроение, 1965 г.
Влияние технологических факторов
Температура нагрева. Температура может оказать влияние на образование трещин в процессе нагрева и охлаждения, а также после окончания термической обработки.
Сталь по чувствительности к трещинам с исходной структурой перлитного строения (пластинчатый перлит, зернистый перлит, сорбит) отличается от сталей с исходной структурой мартенсита.
Сталь со структурой перлитного типа при комнатной температуре обладает значительной пластичностью. При испытании, на растяжение углеродистая сталь У12 со структурой зернистый перлит при 20° С имеет следующие механические свойства: предел прочности 59 · 107н/м2(60 кГ/мм2), удлинение 24%, сужение поперечного сечения 40%. Хрупкое разрушение такой стали возможно при создании трехсторонних растягивающих напряжений. Поэтому необходимые условия для образования трещин при нагреве могут возникнуть в крупных заготовках, покрвках, прокате, слитках, поскольку в них возникает значительная разность температур по сечению, а в соответствии с этим и высокие временные внутренние растягивающие напряжения. Для предупреждения образования трещин ограничивают скорость нагрева. Допустимый перепад температур по сечению и скорость нагрева зависят от величины и формы нагреваемого тела и механических свойств стали. Слитки, благодаря пониженной пластичности стали, более подвержены образованию трещин, чем поковки, быстрорежущая сталь — более, чем углеродистая.
Подсчитано, что в процессе нагрева до 650° С слитков среднеуглеродистой конструкционной стали с исходной структурой перлит допустима разность температур по сечению до 230° С [47]. Поэтому скорость нагрева слитков регулируют менее интенсивным подводом тепла в первую (загрузочную) зону.
При температуре 600—650° С большинство сталей приобретает значительную пластичность; способность стали к удлинению при растяжении увеличивается в 2—2,5 раза. Например, при нагреве от 20 до 600° С удлинение углеродистой стали У12 возрастает от 24 до 56%, а быстрорежущей стали — от 14 до 28%. Для большинства крупных изделий из разных сталей скорость нагрева ограничивается только до температур 600—650° С.
Перед фазовыми превращениями слитки или поковки выдерживают с целью выравнивания температур по сечению для обеспечения одновременного превращения α-фазы в γ-фазу в объеме изделия. При большом перепаде температур по сечению превращение α>γΒ поверхностной части изделия, в связи с уменьшением удельного объема, вызовет растягивающие напряжения, обусловливающие образование трещин.
Предупредить трещины технически нетрудно, поскольку замедленный нагрев или выдержка легко осуществимы. Вопрос о допустимых скоростях нагрева имеет преимущественно экономическое значение как фактор, определяющий производительность.
Скорость нагрева изделий со структурой перлит ограничивается на практике только для слитков, крупных поковок, штампов; нагрев изделий среднего машиностроения ведется с достижимой скоростью в печах или соляных ваннах. Даже в изделиях из быстрорежущей стали при ускоренном нагреве в соляных ваннах с температурой 1280—1300° С трещин не бывает.
Ступенчатый нагрев, применяемый для инструментов, изготовленных из легированной и быстрорежущей стали со структурой перлитного строения, диктуется не столько предупреждением образования трещин в процессе нагрева, сколько другими технологическими соображениями. Предварительный подогрев перед окончательным нагревом сокращает время пребывания инструмента при высоких температурах и тем самым устраняет или уменьшает обезуглероживание режущих кромок инструмента. Он необходим также для полного и одновременного завершения структурных превращений по сечению в процессе кратковременного окончательного нагрева. Чем крупнее по габаритам инструмент, тем большее значение приобретает предварительный подогрев для уменьшения времени пребывания инструмента при высоких температурах. Неоднократно приходилось отмечать, что ступенчатый нагрев с достаточным временем выдержки имеет существенное значение для предупреждений трещин уже в процессе охлаждения крупногабаритного (диаметром 100—200 мм) сложного инструмента из быстрорежущей стали, особенно если охлаждение производится в масле, а не в расплавленной селитре.
Закаленная сталь менее теплопроводна и пластична по сравнению с отожженной. Эти особенности повышают чувствительность стали к трещинам при нагреве. В отличие от отожженной, в закаленной стали при нагреве до температуры Асх протекают процессы отпуска мартенсита. Суммарное изменение объема под влиянием расширения от воздействия температуры и сжатия в результате отпуска мартенсита зависит главным образом от содержания углерода в стали и степени развития процессов выделения углерода из мартенсита. При нагреве до температуры фазовых превращений на поверхности закаленных изделий могут быть не только сжимающие, но и растягивающие напряжения. Закаленные изделия в отличие от отожженных в процессе нагрева до 600—650° С подвержены образованию глубоких трещин первого типа.
В качестве примеров можно привести случаи образования трещин первого типа в инструменте из быстрорежущей стали, когда после обработки холодом при —80° С его вновь нагревают для отпуска в электропечи с температурой 560° С. Во избежание трещин при отпуске после обработки холодом инструмент диаметром 40—50 мм из холодильника выгружают на пол (или в тару), выдерживают до температуры окружающего воздуха в цехе и после этого загружают для отпуска в печь, нагретую до 500—600° С. Наблюдается также появление трещин в крупногабаритном сложном инструменте из быстрорежущей стали после закалки и отпуска при нагреве его в соляных ваннах с температурой 560° С для цианирования. Во избежание трещин крупногабаритный инструмент необходимо подогревать до 200— 300° С перед загрузкой в цианистую ванну.
Как правило, закаленные изделия нагреваются для отпуска до температуры 200—680° С, поэтому скорость нагрева, достижимая в печах и соляных ваннах, небольшая. Практически для закаленных изделий малых размеров, отпускаемых при 200— 680° С, скорость нагрева не оговаривается. Исключение составляет закаленный инструмент из быстрорежущей стали.
В процессе охлаждения и после его окончания при закалке склонность стали к образованию трещин определяется температурой нагрева. В противоположность операции нагрева, при охлаждении трещины могут появляться на изделиях весьма малого размера. Это объясняется прежде всего тем, что закалка изделий, как правило, предусматривает большие скорости охлаждения, вызывающие значительный перепад температур по сечению и высокие внутренние напряжения. Кроме того, сталь с мартенситной структурой малопластична. Высокоуглеродистая сталь, закаленная на мартенсит, при испытании растяжением разрушается хрупко без заметной макроскопической деформации. Трещины в такой стали могут возникать даже при одноосном напряженном состоянии и при очень малых деформациях растяжения, не выводящих сталь из упругой области деформирования.
Внутренние напряжения (временные и остаточные), создаваемые закалкой, даже в образцах и изделиях сечением в несколько миллиметров бывают достаточными для хрупкого разрушения закаленной стали.
Вместе с тем влияние температуры нагрева на образование трещин находится в зависимости от размера изделий, их прокаливаемое™ и формы. Поэтому влияние температуры нагрева целесообразно рассмотреть отдельно.
Образование продольных трещин (первого типа) наглядно характеризуется диаграммами, приведенными на фиг. 14 и 16, на которых отмечены температуры, ограничивающие область образования трещин. Температура, предопределяющая появление продольных трещин, зависит от размера закаливаемых образцов, причем она понижается с увеличением сечения вплоть до размеров критического образца, а затем вновь повышается. Объяснение этой зависимости будет дано позднее, а в данном случае отметим, что температурная область образования трещин первого типа ограничивается только снизу, так как с повышением температуры нагрева склонность стали к растрескиванию увеличивается.
Однако эта хорошо известная зависимость образования трещин от перегрева характерна только для определенной группы сталей.
Группа сталей Х05, XI2М (и другие этого типа), 90Х2Н4 (фиг. 39) характеризуется замкнутой областью образования трещин первого типа с ограничительной линией сверху. При нагреве образцов стали до температуры, лежащей выше верхней ограничительной линии, трещин не возникает. Здесь нарушается установленная зависимость влияния перегрева на образование трещин для сталей первой группы, и вместо повышения склонности к трещинам происходит ее снижение и даже потеря способности к трещинообразованию. Зависимость трещинообразования от температуры нагрева на первый взгляд кажется необычной, но тем не менее она существует и характерна для сталей, в которых сохраняется значительная доля остаточного аустенита после закалки. Применительно к высокоуглеродистой стали количество остаточного аустенита должно превышать 25—35%.
Все высокоуглеродистые стали, в которых после закалки с перегревом до любой температуры сохраняется остаточного аустенита менее 25—35%, характеризуются диаграммами с открытой областью образования трещин первого типа, а стали, способные сохранять остаточный аустенит в большем количестве,— диаграммами с закрытой областью.
Для удобства рассмотрения закономерности образования трещин первого типа разделим область образования трещин на часть, относящуюся к образцам размером меньше критического, и часть, характеризующую образование трещин на образцах размером больше критического.
Склонность к образованию трещин образцов размером меньше критического, относящихся к диаграммам с открытой областью трещин, можно представить ρ виде кривых, показы-