Обработка металлов без снятия стружки
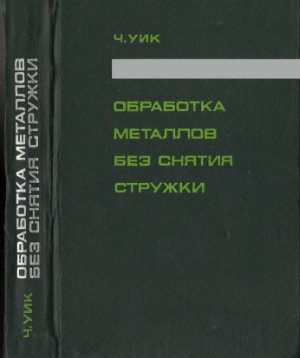
Уик Ч.
Мир, 1965 г.
КАКИЕ ПРОЦЕССЫ ОТНОСЯТСЯ К ОБРАБОТКЕ МЕТАЛЛОВ БЕЗ СНЯТИЯ СТРУЖКИ
В тех случаях, когда литейные процессы (литье в землю, центробежное литье, литье в постоянные формы, литье под давлением, литье в гипсовые формы, литье по выплавляемым моделям, в оболочковые формы и т. д.) и процессы горячего пластического деформирования (выдавливание, штамповка, высадка, гибка, вытяжка и т. д.) обеспечивают получение изделий требуемой формы, они могут быть также отнесены к процессам металлообработки без снятия стружки. Однако эти процессы давно известны и 'поэтому в книге не (рассматриваются.
Горячая обработка металлов давлением находит широкое применение благодаря тому, что для нее требуется минимальное количество энергии, идущей на формообразование изделий, и она позволяет осуществить наибольшее преобразование формы заготовки. Однако горячая обработка имеет тот недостаток, что в процессе ее происходит окисление поверхности или образование окалины, что снижает качество поверхности и размерную точность изделия. Кроме того, тепло от заготовки передается на инструмент, что сокращает срок службы последнего. Одним из решений этих проблем является применение импульсных методов обработки, позволяющих до минимума сократить время образования окалины и передачи тепла инструменту (см. гл. 16).
В книге рассматриваются в основном методы холодной обработки стали и главным образом новые процессы, которые могут быть использованы для изготовления изделий вместо процессов резания. Поэтому здесь совсем не рассматривается обработка листового материала: вытяжка, штамповка резиной, гибка и другие операции, применяемые при холодной листовой штамповке.
Не рассматриваются также процессы холодного волочения, предназначенные для обработки горячетянутых стальных прутков, труб, проволоки или полос различного сечения посредством протягивания их через фильеры или между валками. Эти процессы не рассматриваются еще и потому, что они в основном предназначены для получения полуфабрикатов, а не готовых изделий и осуществляются они на металлургических заводах. Не рассматривается здесь также изготовление бесшовных труб прокаткой на конической оправке, носящей название процесса «Рокрайт», разработанного фирмой «Тыоб редьюсинг корпорейшен», и метод «Флотружен», разработанный фирмой «Флотружен» и заключающийся в протягивании труб при помощи фасонной оправки для получения изделия со стенками переменной толщины. Не рассматривается применение многороликовых и регулируемых вытяжных головок для изготовления квадратных, прямоугольных и фасонных прутков, так как это тоже является одним из основных процессов, выполняемых на металлургических заводах.
Из новейших процессов в книге детально разбираются следующие: накатка шлицевых валов и шестерен, ротационное выдавливание, внутреннее профилирование ротационной ковкой, радиальная ковка, холодное прессование многоступенчатых валов, холодное выдавливание и импульсная, или высокоэнергетическая штамповка, включая обработку взрывом. Отдельные главы посвящены также хорошо известным процессам холодной высадки, накатки резьбы и ротационной ковки, имеющим немаловажное значение в современной практике обработки металлов без снятия стружки.
ДРУГИЕ ПРОЦЕССЫ ОБРАБОТКИ
Чтобы сконцентрировать внимание только на производственных процессах обработки без снятия стружки и не увеличивать объем книги, в ней лишь упоминается о таких методах обработки, как электроискровая, электролитическое шлифование, ультразвуковой метод и химическое фрезерование, в результате которых образуется своеобразная «стружка».
При электроискровой обработке пульсирующие разряды переходят от профильного электрода через диэлектрическую жидкую среду к обрабатываемому изделию, поверхность которого постепенно эродирует. Этот процесс .пригоден в основном для образования полостей заданной формы в очень твердых материалах. Недостаток метода заключается в его низкой производительности, нежелательном и даже вредном образовании высокой температуры на поверхности изделия, а также в необходимости частой замены быстро изнашивающихся электродов.
При ультразвуковой обработке жидкость, содержащая абразивные частицы, протекает между быстро колеблющимися инструментом и изделием, снимая с поверхности последнего частицы металла в соответствии с формой инструмента. Специальный .преобразователь трансформирует электрическую энергию в механическое движение инструмента, совершающего 30 000 колебаний в секунду. Этот процесс, подобно электроискровому методу, может быть использован для сверления, нат резки внутренней резьбы и прошивания отверстий сложной формы. Однако он относительно мало производителен и не так пригоден для обработки очень твердых материалов, как электроискровой, хотя и не вызывает образования внутренних напряжений и коробления изделия.
При химическом фрезеровании изделие погружают в резервуар с химическим раствором, вытравливающим с него излишек металла на тех участках, где это необходимо, и с нужной скоростью. Поверхность изделия, 'не подлежащая обработке раствором, защищается нейтральной легко снимаемой пленкой из неопрена или винила. Процесс особенно удобен для уменьшения веса крупных деталей, когда толщина снимаемого слоя материала должна быть небольшой. Применение его ограничивается тем, что раствор стравливает металл не только в незащищенных местах, но и частично подтравливает под нейтральной пленкой.
При электролитическом шлифовании металл удаляется электрохимическим путем и переходит в раствор, где образует металлические соли. Процесс .подобен гальваническому, но изделие в этом случае является анодом. Обычные шлифовальные станки с абразивными кругами на металлической связке могут быть приспособлены для электролитического шлифования и заточки режущего инструмента, если станок соединить с источником постоянного тока и подводить электроэнергию при низком напряжении к шпинделю шлифовального круга и к затачиваемому инструменту или к приспособлению, в котором закреплен инструмент или изделие.
Специальный, не вызывающий коррозии, соляной раствор служит как охлаждающая жидкость и как электролит для прохождения тока между абразивным кругом и изделием. Этот метод обработки может быть также применен для прошивания отверстий и снятия металла при образовании полостей.
ОБРАЗОВАНИЕ ПОЛОСТЕЙ В МАТРИЦАХ ВДАВЛИВАНИЕМ
Хотя вдавливание и является хорошим примером холодного пластического деформирования стали, оно в данной книге не рассматривается, так как представляет собой метод образования полостей в прессформах и кокилях, высадочных и ковочных штампах.
При осуществлении операции вдавливания закаленный и хорошо отполированный пуансон, представляющий собой форму получаемой полости, вдавливается под большим давлением в стальную заготовку, изготовленную из специальной или простой углеродистой стали. При вдавливании иногда требуется периодический отжиг заготовки. По окончании вдавливания изделие подвергается цементации, закалке или хромированию.
ПОЛИРОВАНИЕ
Еще один процесс пластического деформирования металлов— полирование обкаткой, здесь также не рассматривается, так как он служит для повышения чистоты поверхности или точности изделия без изменения его формы. К разновидностям полирования относятся: полирование роликами, протягивание шаровыми протяжками и др.
Внутренние и наружные цилиндрические поверхности (отверстия цилиндров двигателей внутреннего сгорания, галтелей валов, подвергаемых кручению и изгибу, и несущих поверхностей осей железнодорожного подвижного состава) окончательно обрабатываются накаткой роликами, прижимаемыми к вращающимся деталям. Такая обработка увеличивает усталостную прочность сильно нагруженных деталей, твердость и износостойкость несущих поверхностей.
Для полирования отверстий малых диаметров применяется метод, основанный «а использовании вращающейся много-роликовой головки. В головке размещены по периферии центральной оправки ή а равных расстояниях друг от друга колусные ролики, оси которых для обеспечения эффекта самоподачи слегка наклонены к оси головки. Оправка имеет конусность, обратную конусности роликов. Это позволяет раздвигать ролики в радиальном направлении для получения заданного диаметра отверстия.
Протягивание шаровой протяжкой применяется для крепления втулок в зубчатых колесах или в других деталях без использования шпонок, шпилек и шлицев. Этим методом в отверстии детали при помощи пластического деформирования образуются продольные канавки, отделенные друг от друга невысокими гребнями. При запрессовке втулки в протянутое отверстие гребни смещают более мягкий материал втулки в канавки отверстия, образуя их соединение.