Обработка давлением труднодеформируемых материалов
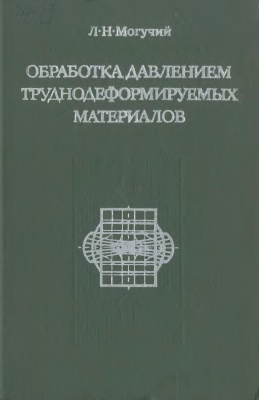
Могучий Л.Н.
Машиностроение, 1976 г.
ПРЕССОВАНИЕ СПЛАВА НИОБИЙ-ЦИРКОНИЙ В ОБОЛОЧКАХ
Для исследования применяли труднодеформируемый сплав ниобия с 27% циркония.
При разработке метода его прессования были использованы ранее выявленные закономерности по влиянию оболочек на процесс истечения металла через канал в матрице. Как было установлено, на уменьшение неоднородности распределения деформаций и неравномерности истечения, а также повышение пластичности заготовки оказывают влияние механические характеристики материала оболочки и ее толщина. Исходя из этого основным критерием при подборе материала оболочки являлось соблюдение установленного соотношения твердости обрабатываемого сплава к твердости материала оболочки (см. рис. 13).
Как уже отмечалось, увеличение толщины стенки оболочки благоприятно влияет на повышение пластичности и уменьшение усилия, потребного для прессования. Исходя из этого толщина оболочек со стороны боковой поверхности была принята равной 7 мм, а с торца — 15 мм.
Слитки из сплава ниобия с цирконием изготовляли на электроннолучевой установке с использованием металлов высокой чистоты. После обточки и торцовки их диаметр составлял 26 мм при длине 60—70 мм.
Исследование показало, что твердость по Викерсу сплава при комнатной температуре равна около 250 кгс мм2 и остается без изменения до 800 С, затем резко начинает падать и при 1000° С составляет примерно 100 кгс мм2.
Поэтому для оболочек целесообразно использовать сталь 12Х18Н9Т или сплав ХН78Т. В случае градиентного нагрева появляется возможность применять материалы с более низкими прочностными показателями: медь, низкоуглеродистую сталь и др. Причем оболочка должна иметь более низкую температуру, чем сплав для того, чтобы обеспечить необходимое соотношение механических характеристик.
Для предохранения от окисления и газонасыщения обрабатываемого сплава торцы образцов заклеивали стеклополотном. Прессование производили со смазкой, составленной из машинного масла и графита на гидравлическом прессе усилием 200 тс из нагретого до 400 С контейнера диаметром 42 мм. Так были получены прутки круглого сечения диаметром 20 мм со степенью деформации около 77°о. Качество прессованного материала контролировали просвечиванием лучами Рентгена, а также изготовлением макро- и микрошлифов.
Сплав в оболочках из стали 12Х18Н9Т прессовали при 1000 С. Однако благодаря недостаточной ее прочности в начальный момент и охлаждению в процессе обработки истечение носило неравномерный характер.
Применение оболочек из сплава ХН78Т потребовало нагрева заготовки до 1250 С и несколько повышенных давлений при прессовании. В связи с диффузией при высокой температуре в некоторых случаях происходило оплавление оболочки и образца.
Необходимость снизить давление истечения и температуру заставила применить комбинированные оболочки. Внутреннюю их часть изготовляли из сплава ХН78Т, а наружную — из низкоуглеродистой стали. Подобные оболочки дали возможность частично компенсировать действие неоднородного температурного поля. Заготовки перед прессованием этим методом нагревали вместе с оболочками до 1000—1100 С, давление при истечении составляло ПО—120 кгс мм2. Полученные прутки оказались вполне хорошего качества с достаточно равномерной толщиной оболочки.
Градиентный нагрев применяли с использованием оболочек из меди и низкоуглеродистой стали. Для устранения влияния внешней среды обрабатываемый сплав запаивали в кварцевые ампулы с остаточным давлением 1 • 10~3 мм рт. ст. Оболочки из стали нагревали в печи без защитной атмосферы до 600' С, а медные имели комнатную температуру. Ампулы, нагретые до 1100” С, выносили из печи, разбивали, а заготовки помещали в подготовленные оболочки. Затем всю систему помещали в контейнер и прессовали.
При контроле внутреннего строения прутков дефектов их материала не обнаружено, выявлена хорошая макро- и микроструктура. Однако медная оболочка более равномерно распределяется по поверхности прессованных прутков.
ПРЕССОВАНИЕ НЕКОТОРЫХ ТРУДНОДЕФОРМИРУЕМЫХ СПЛАВОВ НА ОСНОВЕ ТУГОПЛАВКИХ МЕТАЛЛОВ И ИНТЕРМЕТАЛЛИЧЕСКИХ СОЕДИНЕНИЙ
Прессование сплавов на основе вольфрама. Сплавы вольфрама с ниобием, танталом, а также с другими металлами, карбидами и окислами обладают очень высокой жаропрочностью, вследствие чего чрезвычайно трудно обрабатываются давлением. Для их деформирования необходимо применять высокие температуры и напряжения, предохранять от окисления и диффузии в них газов, а также защищать от охлаждения в процессе обработки. Однако исследования, проведенные в лабораторных условиях и на крупных слитках в полупромышленном масштабе, показали, что сплавы вольфрама с молибденом обладают достаточно высокой пластичностью и могут прессоваться по режиму, принятому для чистого вольфрама, а в оболочках из низкоуглеродистой стали — методами низкотемпературного прессования.
При легировании вольфрама или его сплава ниобием, а также танталом значительно повышается жаропрочность и одновременно хрупкость. Высоколегированные сплавы подобного типа теряют способность подвергаться обработке давлением обычными методами [62, 911. С целью изучения влияния степени легирования вольфрама на его технологические характеристики было проведено исследование по прессованию слитков различного размера на прессах усилием 300 и 600 тс с контейнерами диаметром 52 и 75 мм.
Металл получили в вакуумной дуговой печи по обычной технологии в медные кристаллизаторы, причем он имел пониженное содержание ниобия и тантала (в сумме около 1,0%). Слитки имели крупное кристаллическое строение. При их обточке происходило выкрашивание зерен с образованием неровной боковой поверхности.
Предварительные эксперименты с применением различных термомеханических режимов и методов прессования, а также анализ прочностных характеристик сплавов показали необходимость при обработке их давлением использовать оболочки и градиентный нагрев. В связи с этим оболочки нагревали до 700° С в силитовой печи без защитной атмосферы, а слитки — в водородной печи до 1600—1700;> С.
Оболочки изготавливали в виде стаканов из стали СтЗ с толщиной боковой стенки около 8% от диаметра контейнера.
Для уменьшения теплопередачи оболочки изнутри покрывали слоем асбеста толщиной 1,5 мм. В качестве смазки применяли аквадаг, кроме того, на матрицу клали шайбу, приготовленную из серебристого (чешуйчатого) графита с жидким стеклом и водой.
Прессовали со степенью деформации е = 75%. Прутки остывали в коробе с сухой окисью магния, предварительно нагретой до 600° С. Визуальный осмотр поверхности прутков не выявил каких-либо дефектов. Однако после разрезки на части, обточки и травления в реактиве, составленном из 15 г красной кровяной соли и 7 г едкого натра в 100 г воды, были обнаружены на некоторых из них очень тонкие, паутинообразные трещинки. Причина образования последних — остаточные и термические напряжения, вызванные изменением температуры материала в процессе его нагревания и охлаждения. На возникновение трещин оказывает влияние и упрочнение (нагартовывание) материала, сопровождающееся значительным увеличением хрупкости.
Очевидно, что с целью оптимизации технологии прессования следует создать условия для более полного протекания процесса релаксации напряжений. Исходя из этого было проведено прессование этих же сплавов с соблюдением тех же, что и в первом случае, условий, но с нагревом слитков в индукционной вакуумной установке до 1800 С. При этом, как и предполагалось, были получены изделия вполне хорошего качества.
Исследования показали, что дальнейшее снижение степени легирования рассматриваемых сплавов, особенно ниобием, увеличивает их пластичность и уменьшает давление истечения при прессовании. Таким образом, эту группу материалов можно прессовать в оболочках при температурах, достигаемых в водородных печах, т. е. при 1600—1650' С.
Особо важное значение имеет решение вопроса деформирования более легированных сплавов вольфрама, которые при температурах 1600—1700° С не давали положиельных результатов, так как имели низкую пластичность и высо- кое сопротивление деформированию.
Опыты проводили на слитках, отлитых гарниссажным методом. Часть слитков содержала до 8% Та, а остальные еще значительное количество молибдена. Металлографическое исследование слитков показало, что они имеют мелкокристаллическое строение без посторонних включений и трещин. Эго доказывает целесообразность применения данного метода литья. Материал оболочек выбирали на основании графика рис. 136, построенного по результатам измерения твердости при различных температурах в условиях вакуума и ранее приведенного на рис. 13. В связи со значительной разницей в прочностных характеристиках основного металла и оболочек оказалось необходимым использовать градиентный нагрев и теплоизоляцию.