Оборудование прокатных цехов (эксплуатация, надежность)
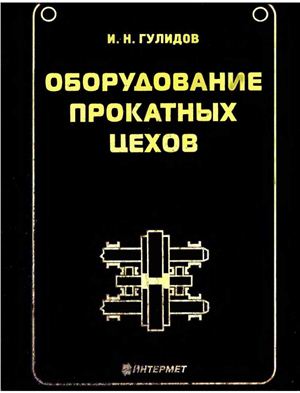
Гулидов И.Н.
Интермет Инжиниринг, 2004 г.
ПОВЫШЕНИЕ ИЗНОСОСТОЙКОСТИ ВАЛКОВ
Надежность и долговечность валков, зависящие от их стойкости, в значительной степени влияют на качество продукции, производительность и эффективность работы станов. Для достижения максимальной износостойкости необходимо обеспечить улучшение условий работы валков, правильный выбор материалов и способов упрочнения поверхности бочки.
При горячей прокатке существенно повышает износостойкость валков защита от воздействия высоких температур и правильный выбор системы их охлаждения. При охлаждении водой валки изнашиваются значительно быстрее, чем при воздушном охлаждении, хотя эффективность водяного охлаждения выше.
Износостойкость валков повышается с понижением запыленности воздуха в цехах (уменьшается абразивный износ) и поддержанием постоянной температуры зимой и летом.
К мероприятиям по улучшению условий работы валков относят также своевременное и правильное техническое обслуживание, повышение уровня специализации, рациональное планирование загрузки оборудования.
Износостойкость валков в значительной мере зависит от химического состава, структуры, физико-механических свойств поверхностных слоев. Повысить сопротивление износу можно, добиваясь оптимальной шероховатости валков, которую подбирают опытным путем. Значительное повышение износостойкости достигается при поверхностной закалке токами высокой частоты (до 500 кГц). Закалка ТВЧ позволяет получать валки с твердым износостойким покрытием и сравнительно вязкой и мягкой сердцевиной. Для высокочастотной закалки применяют индукторы различной конструкции.
К числу наиболее эффективных методов упрочнения и восстановления прокатных валков относят наплавку. Сущность процесса состоит в расплавлении присадочного металла теплом электрической дуги, газового пламени или других источников тепла и сплавлении его с материалом валков. Наиболее широко применяется электродуговая наплавка с использованием присадочного металла в виде электродов под слоем флюсов или в среде защитного газа. При механизированной наплавке валка под слоем флюса (рис. 1.9) электродная проволока 1 непрерывно подается к месту наплавки, подвод тока осуществляется через концентрично укрепленную втулку 2, возникающая дуга 3 вызывает расплавление электрода и металла валка 4. Расплавленный металл создает сварочную ванну 5. После кристаллизации образуется наплавленный валик 6, покрытый шлаковой коркой 7 и нерасплавившимся флюсом 8. Избыток флюса осыпается, а шлаковая корка удаляется. Для повышения качества наплавки ее ведут с предварительным подогревом валков.
В настоящее время получают распространение такие виды наплавки, как плазменная (рис. 1.10), автоматическая вибродуговая, наплавка электродами из спеченных материалов и др.
Для повышения стойкости валков многовалковых станов применяют высокотемпературную термомеханическую поверхностную обработку (ВТМПО), которая предусматривает совмещение операций нагрева, деформирования и охлаждения. Сущность ВТМПО применительно к валкам холодной прокатки заключается в нагреве поверхностного слоя определенной глубины до аустенитного состояния, пластическом деформировании поверхностных слоев роликами при температуре аустенитизации и резком немедленном охлаждении. Обработку выполняют так, чтобы после пластической деформации не успевали происходить процессы рекристаллизации. Структура и соответствующие свойства металла сердцевины валка формируются в результате предварительной термической обработки.
Правила учета и хранения прокатных валков
К каждому валку, поступающему в прокатный цех, должен быть приложен паспорт. В паспорте указывают данные, характеризующие условия изготовления, химический состав, металлографические исследования и механические свойства металла.
Прокатные валки необходимо хранить в закрытых помещениях, их укладывают отдельно и комплектно для каждого профиля, прокатываемого на стане. Торцы трефов с набитыми на них номерами должны быть чистыми. Непосредственно к стану валки нужно подавать только перед перевалкой.
Транспортировать обработанные прокатные валки из вальцетокарной (вальце-шлифовальной) мастерской в цех и обратно следует осторожно, соблюдая требования техники безопасности. При транспортировке нельзя ударять валок о валок или другое оборудование.
1.2.2. Подшипники прокатных валков
Подшипники прокатных валков являются ответственными узлами рабочей клети, от их конструкции и правильной эксплуатации зависит бесперебойная работа прокатного стана. Подшипники работают в очень тяжелых условиях -при высоких удельных нагрузках (в 4-10 раз превышающих нагрузку подшипниковых узлов тех же габаритов, установленных на машинах общего назначения); высокой температуре (до 300 °С и более) и при ограничительных габаритах (поэтому по внешнему виду они значительно отличаются от подшипников других машин).
Подшипники прокатных станов можно разделить на две группы: скольжения и качения. Подшипники скольжения конструктивно выполняют двух видов: открытые и закрытые. Подшипники качения применяют роликовые с коническими и реже со сферическими цилиндрическими роликами.
К подшипникам всех типов предъявляются жесткие требования по обеспечению длительного срока службы узлов трения при снижении расхода смазочных материалов и электроэнергии и по получению профиля проката высокой точности.
Правильная эксплуатация подшипников прокатных валков включает следующие операции: контроль состояния подшипниковых узлов и подготовка их к монтажу, монтаж и демонтаж подшипниковых узлов, уход и надзор за подшипниками во время работы, ремонт подшипников, хранение и учет подшипников.
Подшипники скольжения открытого типа
На станах горячей прокатки наибольшее распространение получили подшипники скольжения с текстолитовыми вкладышами. Подшипники этого типа стали применять несколько десятков лет назад, когда практически было обосновано, что текстолитовые вкладыши при обильной смазке водой выдерживают высокие удельные давления и могут вполне заменить дефицитные вкладыши из цветных металлов. Подшипники скольжения с бронзовыми (Бр.ОЦС6-6-3, Бр.АЖ-9-4) и латунными вкладышами (ЛАМЖЦ 66-6-3-2), а также из графитизированной стали и чугуна несовершенны, имеют высокий коэффициент трения и малый срок службы; их устанавливают на старых станах поштучной тонколистовой прокатки, шейки валков которых разогреваются до 300-400 °С.
Металлические вкладыши устанавливают в подшипниках только с одной стороны, в направлении которой действует усилие на подшипники (рис. 1.11). Неметаллические вкладыши применяют в подшипниках валков блюмингов, слябингов,толстолистовых, среднелистовых, рельсобалочных и сортовых станов. Наиболее распространенными материалами (кроме текстолита) можно считать лигнофоль, лигностон и др. Подшипники, изготовленные из текстолита, лигнофоля и других неметаллических материалов, обладают низкой теплопроводностью, поэтому в процессе работы их необходимо интенсивно охлаждать до t< 60—80 °С, так как при более высокой температуре начинается их интенсивное разбухание, а в дальнейшем и обугливание. В качестве смазывающей и охлаждающей жидкости используют воду или водную эмульсию.
Подшипники из текстолита характеризуются чрезвычайно малым коэффициентом трения (в 10-12 раз меньшим, чем для бронзовых), при больших скоростях вращения почти равным коэффициенту трения роликовых подшипников качения. Для сравнения приведем следующие значения коэффициента трения: 0,06-0,1 -для бронзовых; 0,002-0,005 - для роликовых; 0,004-0,006 - для текстолитовых подшипников.
Подшипники с цельнопрессованными текстолитовыми вкладышами, установленные на блюминге 1300 конструкции УЗТМ, показаны на рис. 1.12. Текстолитовые вкладыши 1 закреплены в кассете 2 планками и болтами. С наружной стороны вкладыши закрепляют металлическим кольцом. Текстолитовые фланцы 4, соприкасающиеся с валком (по шейке), изготовляют отдельно и закрепляют в специальных расточках кассеты со стороны бочки валка. Осевую регулировку валков и поджатие текстолитовых фланцев к торцу бочки валка осуществляют с помощью затяжки болтов 3. Подвеска 5 с помощью текстолитовых вкладышей б поддерживает верхний валок при холостом ходе стана. У подушки подшипника нижнего валка предусмотрена крышка 7 с небольшими текстолитовыми вкладышами. Сменные прокладки 8 служат для сохранения линии прокатки на одном уровне после переточки по отношению к роликам рольганга.
С помощью проушин 9 правая нижняя подушка соединена с левой и присоединена к механизму для вытаскивания комплекта валков. Верхняя подушка при смене валков остается подвешенной к пяте нажимного винта, а верхний валок со своей нижней подвеской 5 будет лежать на нижнем валке.
Подшипники скольжения закрытого типа
Подшипники скольжения закрытого типа, или жидкостного трения (ПЖТ), получили широкое распространение. При всех условиях работы (малые скорости вращения шейки валка в подшипнике, большие усилия) между телом шейки dmи материалом подшипников dnвсегда сохраняется масляная пленка, благодаря чему шейка валка как бы плавает в масляном слое подшипника. Состояние жидкостного трения обеспечивается герметичностью конструкции подшипникового узла с весьма тщательно обработанными (до зеркального блеска) поверхностями трущихся деталей. Коэффициент трения в этих подшипниках весьма мал (0,001-0,005), а износа трущихся поверхностей практически нет, срок эксплуатации ПЖТ - 10-20 лет. Указанные показатели значительно выше, чем для роликовых подшипников, кроме этого, подшипники жидкостного трения способны воспринимать большие удельные давления и сохранять высокую точность при высоких скоростях прокатки.
Рассмотрим основы теории гидродинамического эффекта (эффекта масляного клина), на котором основан принцип работы ПЖТ. Трение возникает при взаимном перемещении соприкасающихся тел в месте контакта и вызывает износ трущихся поверхностей. Различают три основных вида трения скольжения: сухое, жидкостное и граничное (полусухое). Сухое трение (рис. 1.13, а) возникает при зацеплении неровностей трущихся поверхностей при отсутствии смазки. При сухом трении наблюдается большой износ трущихся поверхностей. На основаниимногочисленных экспериментов установлено, что при сухом трении коэффициент трения μ = 0,2-0,4. Трение этого вида недопустимо в подшипниках.
Жидкостное трение (рис. 1.13, в) возникает при полном разделении трущихся поверхностей. Поверхности тщательно обрабатываются, смазка прилипает к ним и, скорость перемещения ее горизонтальных слоев будет переменной по толщине слоя смазки: наибольшая - у движущейся поверхности и равна нулю у неподвижной поверхности.
В реальных условиях, даже при самой тщательной (по 10-12 классу чистоты) обработке поверхностей, чтобы обеспечить жидкостное трение, толщина слоя смазки должна быть больше суммарной высоты шероховатостей трущихся поверхностей.