Облученные нержавеющие стали
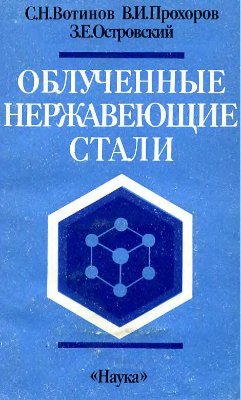
Вотинов С.Н., Прохоров В.И., Островский З.Е.
Наука, 1987 г.
ПОВЕДЕНИЕ ОБЛУЧЕННЫХ СТАЛЕЙ ПРИ ДЛИТЕЛЬНЫХ ИСПЫТАНИЯХ ПОД НАГРУЗКОЙ
Для прогнозирования работоспособности деталей конструкций активной зоны высокотемпературных энергетических реакторов, в частности оболочек ТВЭЛ быстрых реакторов, необходимы данные по влиянию облучения на сопротивление длительному разрушению и ползучести сталей и сплавов.
В работах [24—27] изучалось влияние облучения на длительную прочность и ползучесть нержавеющих сталей и высоконикелевых сплавов, ибо эти характеристики являются определяющими для материалов, работающих в температурной области выше 500° С. Послереакторные испытания на ползучесть, проведенные на сталях типа 18-10, 16-15, 16-35 и высоконикелевых сплавах, позволили установить характерные изменения на разных стадиях ползучести после различных режимов облучения. На рис. 26 представлены первичные кривые ползучести облученных и необлученных образцов сталей 06Х18Н10Т. Из данных следует, что время до разрушения и скорость ползучести образцов после облучения практически не изменились в сравнении с необлученными, отожженными по температурному режиму облучения. У сложно легированной стали 06Х15Н28В2М4Б не обнаружилось изменения 100-часовой длительной прочности при 650° С, однако скорость ползучести после облучения уменьшилась, что можно объяснить структурными изменениями, происходящими в облученном материале. Облучение привело к значительному снижению пластичности главным образом за счет сокращения или полного исключения III стадии ползучести. Сталь 06Х20Е35ВЗТ, у которой до облучения отсутствует явно выраженная III стадия ползучести, после облучения разрушается уже на II стадии. Предел длительной прочности на 100 ч снизился после облучения примерно в 2 раза вследствие охрупчивания, которое, как было показано, вызвано образованием после облучения сплошных стенок карбидов и интерметаллидов на границах зерен. Подобное значительное сокращение времени до разрушения у аустенитной нержавеющей стали наблюдали [23] и без облучения. И в этом
случае выделения по границам зерен образовывали сплошную стенку, а около границ существовала зона, свободная от выделений.
Влияние температуры облучения на характеристики ползучести прослежено [24] на примере стали 06Х16Н15МЗБР (рис. 27).
После облучения при 650° С и особенно при 500° С время до разрушения снижается, а скорость ползучести увеличивается у этой стали при одних и тех же напряжениях в большей степени, чем после облучения при 50—70° С. Разница между скоростью ползучести и временем до разрушения, определенных на образцах стали 06Х16Н15МЗБР до облучения и после него, уменьшается с ростом длительности испытания.
Испытания хромистой нержавеющей стали феррито-мартенситного класса 12Х13М2С2 [3] показали следующее: облучение при 70°С флюенсом 4*1021 нейтрон/см2 уменьшает время до разрушения примерно в 10 раз, а после облучения флюенсом 1-1022 нейтрон/см2 долговечность стали уменьшается на два порядка (рис. 28).
В работах [25, 26] была проведена оценка непосредственного влияния реакторного облучения на долговечность под нагрузкой оболочечных материалов тонкостенных труб диаметром 6—11 мм из сталей марок 06Х18Н10Т, 06Х16Н15МЗБ, 06Х16Н15МЗБР и сплава на основе никеля 02Х17Н77ТЮР двух состояний: с крупным и относительно мелким зерном в каналах реактора СМ-2 НИИАР им. В.И. Ленина с различной интенсивностью нейтронного потока. Испытания проводились на временной базе 200—1000 ч в диапазоне 600—700°С. Проводились также контрольные внереакторные испытания для непосредственного сравнения. Максимальное время до разрушения в реакторе для стали 06Х18Н10Т было 900 ч, флюенс 4*10 нейтрон/см2.
Кроме того, два образца стали были выдержаны в реакторе без разрушения в течение 2080 ч при 700°С и напряжении 40 МПа. Если желаемых температур не удавалось получить, то испытания проводили при температуре, максимально приближенной к необходимой. Эта разница температур обычно не превышала 10—30° С. Для пересчета полученного времени до разрушения использовали зависимость Ларсена—Миллера [23]. Коэффициент С принимали при этом равным 20.
На рис. 29,а—в представлены результаты испытаний в координатах lgσ3ΙΓΒ— lgσ для разных сталей при 650° С, а на рис. 30 для стали 07Х18Н10Т при 700°С. Из представленных зависимостей видно, что облучение мало влияет на длительную прочность стали названных марок при 650°С. Разница длительной прочности стали 07Х18Н10Т в реакторе и вне его при 700°С уменьшается с увеличением базы испытания, а при времени до разрушения 500 ч длительная прочность как в том, так и в другом случае одинакова н составляет 70—90 МПа. Подобная тенденция заметна и при 650°С. В этом случае длительная прочность в реакторе и вне его становится одинаковой при времени до разрушения около 10 тыс. ч.
Увеличение диаметра трубчатых образцов после испытания в реакторе составляло 0,5—1%, а после испытания вне реактора 0,5—3%.
Из двух сталей величина снижения длительной прочности под облучением меньше для стали с бором.
Испытания сплава на никелевой основе показали следующее [26]. При 700° С длительная прочность при реактивных испытаниях сплава 03Х17Н77ТЮР существенно (в 2 раза) ниже длительной прочности без облучения при времени до разрушения от 10 до 500 ч (рис. 31). Причем интересно, что за счет облучения длительная прочность примерно одинаково уменьшается для труб двух состояний, а деформация до разрушения не меняется, хотя в исходном состоянии пластичность труб состояния I равна 0,1—0,4%, а состояния II — 4—7%.
Приведенные результаты непосредственных испытаний в поле реакторного излучения сплава согласуются с установленным ранее значительным снижением длительной прочности материалов с неустойчивой структурой после облучения. Характер разрушения испытанных образцов сплава почти не меняется под действием облучения, о чем свидетельствует рис. 32,а—в. На разрушенном образце малопластичного сплава видна одна протяженная трещина, ориентированная вдоль оси образца. В то же время разрушение высокопластичного сплава (состояние II, величина зерна 15 мкм) происходит путем появления нескольких, не наблюдаемых при визуальном осмотре микротрещин в одном месте образца.
Металлографические исследования образцов малопластичного сплава подтверждают наличие единственной межзеренной трещины при отсутствии деформации зерен, т.е. характер разрушения этих образцов приближается к хрупкому с очень маленькой величиной деформации до разрушения (0,1—0,4%).
В образцах высокопластичного сплава (состояние II) большая величина деформации до разрушения (4—7%) является результатом сильно развитой пористости (рис. 33,α—в). Для этих образцов разрушение (потеря герметичности трубки) наступает тогда, когда поры объединяются в цепочки, распространяющиеся на всю толщину стенки трубы. Расположение пор свидетельствует о том, что вероятными зародышами их являются трещины в тройных точках зерен. Проведенные микроструктурные исследования позволяют заключить, что процесс разрушения вследствие зарождения и распространения микротрещин является совершенно различным для этих двух состояний сплава 03Х17Н77ТЮР.
В малопластичном крупнозернистом сплаве микротрещине трудно зародиться, однако после образования она легко распространяется на всю толщину стенки трубы. Для высокопластичного сравнительно мелкозернистого сплава зарождение микротрещины является, очевидно, более легким, чем ее рост, в результате этого зародившиеся трещины преобразуются в поры. Эффект значительного снижения длительной прочности вследствие облучения у такого типа сплавов подтверждается данными буквально всех исследователей. Причем подчеркивается, что это снижение всегда сопровождается очень существенным уменьшением пластичности (охрупчиванием). Высокая пластичность в процессе и после облучения, наблюдаемая у труб из сплава 03Х17Н77ТЮР одного из состояний, обнаружена впервые. Этот факт представляется очень интересным и прямым образом опровергает мнение, что причиной охрупчивания является гелий, так как в данном случае никакой разницы в содержании и в состоянии гелия в образцах нет.
Сравнивая кривые длительной прочности, полученные при 700°С для сталей 06Х15Н15МЗБ, 06Х18Н10Т и сплава 03Х17Н77ТЮР, можно заметить, что без облучения стали оказываются менее прочными, чем сплав при временах до разрушения, по крайней мере до 2000 тыс. ч. Однако под облучением более высокая длительная прочность сплава 03Х17Н77ТЮР сохраняется при времени до разрушения всего лишь около 200 ч, при более длительных временах до разрушения прочнее становится сталь 06Х18Н10Т. Эти данные говорят о нецелесообразности использования материалов с неустойчивой структурой при высоких температурах и длительных (более 200 ч) временах эксплуатации в реакторе. В этих условиях более прочной (долговечной) оказывается сталь с устойчивой структурой типа 18-10 или 16-15.