Объемная штамповка. Атлас схем и типовых конструкций штампов
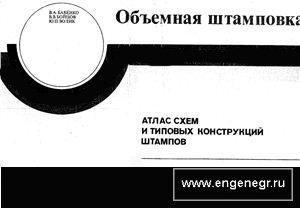
Бабенко В.А.
Машиностроение, 1982 г.
1 КЛАССИФИКАЦИЯ ШТАМПОВ
В отличие от универсального инструмента для ковки (бойков) штампы для объемной штамповки являются специальным инструментом, поскольку конструируются и изготовляются для серийного и массового производства поковок, как правило, одного наименования. В настоящее время в кузнечных цехах объемной штамповки применяют большое число самых разнообразных штампов, которые можно классифицировать по назначению, видам оборудования, количеству ручьев, конструктивному признаку и т. д.
Поназначению различают штампы. для собственно штамповки, обрезные, правочные и калибровочные. В качестве инструмента при штамповке используют также валки (секторы) — для прокатки и вальцовки, а также бойки — для ротационной ковки.
Повидамоборудования штампы можно разделить на две основные группы:
1) устанавливаемые на универсальном кузнечно-штамповочном оборудовании (молотах, ГШКП, винтовых и гидравлических прессах, ГКМ);
2) устанавливаемые на специализированном оборудовании (горизонтально-гибочных, раднально-ковочных, роташюпно-ковочных, вертикально-ковочных, злектроаьгсадочных, высокоскоростных машинах, гидравлических прессах для изотермической и многоплунжерной штамповки, вальцах и прокатных станах, инструмент для жидкой и сферодвижпой штамповки и др.).
Поколичествуручьев штампы подразделяются на одноручьевые и многоручьевые, Одноручьевые применяют для изготовления поковок простых по форме или предварительно подготовленных на других видах оборудования (ковкой, высадкой, вальцовкой), Многоручьевые штампы применяют для изготовления поковок сложной формы.
.Поконструктивномупризнаку различают штампы с одной или несколькими поверхностями разъема, с выталкивателями поковок и без них, цельные (монолитные) и сборные, со вставками различной формы. Штампы могут быть также открытыми—для штамповки с облоем и закрытыми — для безоблойной штамповки.
2. МАТЕРИАЛЫ, ПРИМЕНЯЕМЫЕ ДЛЯ ИЗГОТОВЛЕНИЯ ШТАМПОВ
Условия эксплуатации штампов для объемной штамповки, в особенности для горячего деформирования, очень тяжелые. Штампы подвергаются многократному воздействию высоких температур и значительных нагрузок. Интенсивное течение металла в процессе формообразования поковки вызывает истирание (абразивный износ) поверхности ручья. Штампы для горячего деформирования в течение каждого цикла штамповки испытывают резкие колебания температуры, особенно при использовании смазочно-охлаждающих жидкостей, что приводит к образованию на поверхности ручья разгарных трещин,
Штамповые стали должны обладать высокими механическими свойствами, сочетая прочность с ударной вязкостью, износостойкостью, разгаростойкостью, и сохранять эти свойства при повышенных температурах. Материалы штампов должны хорошо прокаливаться (при термической обработке), обрабатываться резанием и быть сравнительно дешевыми.
Выбор стали для штампа определяется условиями его эксплуатации (горячая или холодная штамповка, динамический или статический характер нагружения, способ смазки и охлаждения, величина удельных усилий штамповки, зависящая от сложности поковки и ее материала, схемы напряженного состояния в очаге деформации), габаритами штампа или вставки, серийностью производства и др. Поэтому для изготовления штампов применяют разнообразные по химическому составу и свойствам марки сталей. Однако их число стремятся свести на заводах к целесообразному минимуму, что облегчает заказ и получение штамповых материалов, изготовление штампов и их эксплуатацию.
Марки штамповых сталей и химический состав регламентируются ГОСТ 5950—73,
Для изготовления молотовых и прессовых штампов получили распространение стали 5ХНМ, 5ХНВ, 5ХНВС. 5XНГМ. Полноценным заменителем дефицитных хромоникелевых сталей 5ХНВ и 5ХНМ является безникелевая сталь 4ХСМФ. Дешевыми сталями для высадочных штампов являются марки 4ХВ2С, 5ХВ2С, 7X3, 8X3.
При штамповке труднодеформируемых сплавов применяют высоколегированные стали 4ХЗВМФ, 4Х5В2ФС, 4Х5МФС, 4Х4ВМФС, 6ХЗВЗМФС, 5Х2ВМНФ и др. Эти же стали целесообразно применять для изготовления высоконагруженных детален штампов при выездке и выдавливании на ГКМ, ГШКП, горячевысадочных автоматах, высокоскоростных машинах.
Для повышения износостойкости и теплостойкости штамповых вставок, пуансонов и матриц широко применяют химико-термическую обработку поверхности ручья. Например, очень эффективно азотирование сравнительно небольших по габаритам вставок штампов ГШКП.
Рабочие элементы обрезных штампов изготовляют из хромистых сталей типа 7X3, 6X3. Реже применяют стали 5ХНВ, 5ХГМ1,
4ХВ2С. Часто режущие кромки деталей штампа, выполненных и. стали 45, наплавляют твердым сплавом.
Блоки для молотовых вставок, матриц для высадки изготовляю из сталей 40ХЛ, 40Л,
При жидкой штамповке для инструмента используют стали 4Х5В2ФС, 4Х5ЭДФС, ЗХ2В8Ф; для изотермической штамповки титановых сплавов и сталей применяют жаропрочные сплавы на никелевой основе типа ЖС6К, ЖС6У, керамические и металлокерамические сплавы, сплавы на основе молибдена.
Весьма перспективно при горячей объемной штамповке применение литых штампов, изготовляемых вместе с ручьями. Для литых штампов используют стали, в основном, подобные по составу сталям для ковочных штампов. Применение литых штампов повышает стойкость инструмента, снижает трудоемкость изготовления штамповой оснастки, позволяет более экономно расходовать стали за счет многократного переплава изношенного штампа и др.
Детали штампов для холодного объемного деформирования изготовляют из высокоуглеродистых (У10А), среднелегированных (9ХС, ХВГ) и высоколегированных (Х12М, Х12Ф1, Х6ВФ, Р18 и др.) сталей. Стали У10А, 9ХС, ХВГ обладают сравнительно невысокой прочностью, поэтому их используют в основном для малонагруженных элементов штампа (выталкивателей, опорных прокладок и т. п.). Высоколегированные стали после термической обработки приобретают высокие показатели твердости, прочности и вязкости.
Рекомендации по выбору штамповых материалов, а также термической и химико-термической обработки штампов приведены в справочной и специальной [6, 24, 21]литературе.
3. ПРАВИЛА КОНСТРУИРОВАНИЯ И ОФОРМЛЕНИЯ ЧЕРТЕЖА ШТАМПА
Габаритные размеры и размеры крепежных элементов штампов должны Сыть строго согласованы с соответствующими параметрами оборудования, на котором их устанавливают. При этом необходимо учитывать размеры рабочего пространства машины, величину хода бабы молота, ползуна пресса, главного и бокового ползунов ГКМ, ход и размеры толкателя пресса и выталкивателя пакета, регулировочный ход закрытой высоты и размеры стола ГШКП, способы крепления штампов и др.
При конструировании штампов следует правильно компоновать штамповочные и заготовительные ручьи, ножи, выемки под клеш, обрезные и отрезные ручьи ГКМ и др., учитывая допустимые расстояния между ручьями и до края штампа, удобство укладки нагретой заготовки в первый ручей и последующей перекладки в другой, площадь зеркала штампа.
В целях экономии штамповой стали следует по возможности шире применять конструкции штампов со вставками, предусматривая при этом надежное крепление вставок и удобную их замену. При конструировании штампов, устанавливаемых па автоматизированных ГШКП или ГКМ, а также на высадочных автоматах, необходимо учитывать специфику автоматизированной штамповки поковок.
Ниже приводятся основные правила оформления чертежа штампа.
1. Чертеж штампа выполняется, как правило, в натуральную величину. Уменьшенный масштаб допускается для крупных и простых штампов.