Новые стали и сплавы в машиностроении
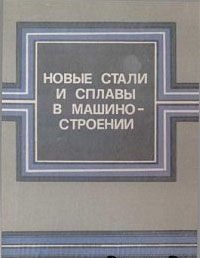
Лахтин Ю.М., Коган Я.Д. (ред.)
Машиностроение, 1976 г.
ЖАРОПРОЧНЫЕ СТАЛИ И СПЛАВЫ
ЖАРОПРОЧНЫЕ СТАЛИ И СПЛАВЫ В МАШИНОСТРОЕНИИ
Теплоэнергетика, стационарное, транспортное и авиационное турбостроение, ракетная техника, химическое и нефтехимическое аппаратостроение, промышленная теплотехника — далеко не полный перечень отраслей промышленности, использующих жаропрочные стали и сплавы.
Следует отметить, что в сравнении с низколегированными сталями конструктивная прочность жаропрочных сталей и сплавов определяется более широким комплексом свойств. К ним относятся кратковременные прочностные свойства, сопротивление ползучести н релаксации, длительная прочность, кратковременная и длительная пластичность, циклическая прочность (выносливость).
Помимо перечисленных характеристик, работоспособность жаропрочного сплава зависит от стабильности его структуры и механических свойств при изотермическом нагреве и в условиях термоциклирования (термостойкость), а также от коррозионной стойкости в газообразной среде при высоких температурах (жаростойкость, окалиностойкость).
Сплав должен быть технологичен, т. е. давать возможность массового производства изделий тем или иным методом (деформированием, отливкой, сваркой и т. д.). К сожалению, многие разработанные материалы, обладающие исключительно высокими характеристиками жаропрочности, недостаточно технологичны.
Многообразие предъявляемых требований вызывает и большое разнообразие жаропрочных материалов.
При сравнительно невысоких рабочих температурах 100— 400° С в качестве жаропрочных могут применяться конструкционные стали — углеродистые (до 350° С) и низколегированные, а также сплавы на основе меди, алюминия и титана. При температурах выше 400 С применяют низколегированные стали перлитного класса, жаропрочные до 550—580° С и коррозионностойкие стали мартенситного класса, жаропрочные до 600—620° С. Высоколегированные стали аустенитного класса находят применение в интервале температур 550—700° С, аустенитные сплавы па Fe—Ni—Сr основе (содержащие менее 50% Fe) — до 750° С Для рабочих температур 700—1000° С используют сложнолегированные сплавы на основах: Ni—Сr; Со—Сr; Ni—Сr—Со, а для еще более высоких температур (до 1400° С) — тугоплавкие металлы и их сплавы, металлокерамические и композитные материалы.
Мартенситные стали. Из сталей мартенситного класса в качестве жаропрочных нашли практическое применение стали с 11 — 13% (в среднем 12%) хрома, для повышения жаропрочных свойств стали дополнительно легируют молибденом, вольфрамом, ванадием и ниобием. Модифицированные хромистые стали в основном рассчитаны на применение в температурном интервале 560— 620° С, в котором жаропрочность и жаростойкость низколегированных сталей перлитного класса становится уже недостаточной, а использование аустенитных сталей экономически нецелесообразно.
Модифицированные 12%-ные хромистые стали имеют при обычном для них содержании углерода (0,10—0,20%) двухфазную феррито-аустенитную структуру, в которой содержание феррита составляет 15—25% (реже 30—35%). Количество последнего зависит от дополнительного легирования и в меньшей степени — от термической обработки. Выделению избыточного феррита способствуют сильные карбидообразующие элементы: ниобии, титан, ванадий. Закалка с весьма высокой температуры (1150—1200° С) вызывает, как правило, образование максимального количества феррит ной составляющей. Наличие избыточного феррита в мартенситной стали приводит к структурной нестабильности и, следовательно, ухудшает ее работоспособность [131.
Химический состав типичных жаропрочных сталей с 12% Сr приведен в табл. 39. Из них оптимальной жаропрочностью и в особенности релаксационной стойкостью обладает сталь 18Х12ВМБФР (ЭН-993) в результате введения ниобия и микролегирования бором.
Жаропрочные хромистые стали производят в виде сортового проката, поковок и отливок. Из сортового металла изготовляют главным образом лопатки и крепежные детали для паровых турбин (13]. Крупные поковки используют при производстве турбинных дисков и роторов [271, мелкие — для различной арматуры. Путем отливки из 12%-ных хромистых сталей изготовляют цилиндры турбин . Жаропрочные стали мартенситного класса также начинают применяться в котлостроенин для паропроводных труб.
Фсрритные стали. Наряду с широко применяемыми жаростойкими сталями с 18—32% Сг разрабатываются принципиально новые фсрритные жаропрочные стали, упрочненные частицами интерметалл идныχ фаз типа АВ, (фазы Лавеса). Известно, что эти фазы, например, Fc,Wи Fe, (W, Mo) обладают большой термической устойчивостью в течение длительного времени и высокой жаропрочностью при температурах до 700° С. В качестве примера можно привести сталь состава: 0,08—0,12% С, 2,5% Сг, 8% W, 0,75% Nb, 0.20% V [291.
Длительная прочность этой стали приближается к прочности аустенитных хромойнкелевых сталей, составляя при температурах 650, 675° С и сроке службы 100000 ч 12 и 10 кгс/мм2 соответственно. Предел ползучести при тех же температурах равен 8 и 6 кгс/мм2.
Эксплуатационное опробование пароперегревательных труб, изготовленных нз новой стали, в течение двух лет дало удовлетворительные результаты.
Аустенитные стали. Из всех жаропрочных сталей наибольшее распространен не получили аустенитные хромоникелевые стали. На концентрационном треугольнике системы Fe—Сr—Ni(рис. 66) отмечены области промышленного применении с млей и сплавов, относящихся к данной системе.
Число марок жаропрочных аустенитных сталей в СССР и в зарубежных странах весьма велико — отчасти потому, что марки различных стран полностью или с самыми незначительными отклонениями дублируют друг друга. За последнее десятилетие состав практически применяемых аустенитных сталей стабилизировался.
Следует отметить, что зарубежные аустенитные стали дополнительно легированы молибденом и лишь отдельные из них содержат вольфрам: отечественные же марки преимущественно легированы вольфрамом. При этом аустенитные стали, легированные вольфрамом, часто превосходят по жаропрочности аналогичные композиции с молибденом.
Аустенитные стали удобно различать по виду упрочнения, обеспечивающего после соответствующей термической обработки различный уровень механических свойств: Аустенитные стали с интерметаллидным упрочнением отличаются более высокой структурной стабильностью и жаропрочностью, чем с карбидным упрочнением. Разработаны также аустенитные стали со смешанным (карбидно-интерметаллидным) упрочнением.
Соединение Ni,Ti— основная упрочняюшая фаза в аустенитных сталях с интерметаллидным и смешанным упрочнением. Фаза Ni,Tiс гранецентрированной кубической решеткой при температуре 750° С и выше способна переходить в фазу того же состава с гексагональной решеткой
Для образования интерметаллида Ni,Tiаустенитные стали легируют титаном в количестве 1,5—3,0% при минимальном содержании углерода (не более 0,08%). В табл. 40 приведены аустенитные стали с интерметаллидным упрочнением.
Один из путей дальнейшего повышения жаропрочности аустенитной стали — это микролегирование бором и редкоземельными элементами (чаще всего церием).
Как показал опыт применения отечественных марок сталей (например, 09X14Н19В2БР) микродобавки бора приводят к повышению сопротивления ползучести, а также релаксации напряжении при температурах до 700° С.
В отдельных случаях бор вводится в аустенитную сталь в значительных количествах, превышающих расчетные добавки, обычно применяемые при микролегировании. В аустенитной структуре такой стали образуются изолированные боридные фазы. Химический состав ряда борсодержащих хромоникелевых сталей приведен в табл. 41. Содержание в них бора составляет 0,2—0,7%.
Борсодержащне аустенитные стали отличаются повышенной стойкостью против локального разрушения в сварных швах и околошовной зоне, вследствие чего они рекомендуются для сварных конструкций.