Новое в сварке чугуна
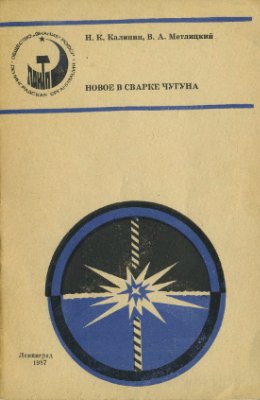
Калинин Н.К., Метлицкий В.А.
ЛДНТП, 1987 г.
ОСОБЕННОСТИ СВАРКИ ЧУГУНА
Чугун является плохо свариваемым материалом. Трудности при его сварке связаны прежде всего с образованием отбела в наплавленном металле и хрупкой мартенситной структуры в околошовной зоне.
В зависимости от требований сварка чугуна может производиться различными сварочными материалами. При сварке с использованием чугунных прутков необходимо обеспечить не только заданный состав наплавленного металла, но и определенную скорость охлаждения, чтобы избежать образования отбела и трещин.
При сварке чугуна сталью или цветными металлами науглероживание шва -крайне нежелательно, поскольку оно приводит к образованию в нем метастабильных структур, например, выделение цементита по границам зерен или распаду аустенита при охлаждении шва с мартенситным превращением. Это, в свою очередь, ведет к повышению твердости, резкому снижению пластичности металла шва и к образованию трещин.
В связи с этим принимаются специальные меры, способствующие получению качественных соединений чугуна: при горячей сварке — предварительный и сопутствующий подогрев, завершение эвтектического превращения, если нет особых требований к структуре соединения; медленное охлаждение наплавленного металла и по возможности уменьшение его усадки; при холодной сварке — получение пластичного металла шва и использование низких режимов сварки.
МАТЕРИАЛЫ ДЛЯ СВАРКИ ЧУГУНА
Прутки для газовой сварки. Для исправления литейных дефектов небольших и средних размеров, а также при ремонте деталей из чугуна широко применяется газовая сварка с присадкой из чугуна. При газовой сварке можно в некоторых пределах регулировать тепловое воздействие на сварочную ванну и основной металл, что создает необходимые условия для протекания процесса графитизации и уменьшает вероятность образования закалочных структур.
От прутков, рекомендуемых по ГОСТ 2671 —-70 (марки А и Б), они отличаются пониженным содержанием кремния и наличием добавок никеля, меди, титана и олова. При использовании указанных прутков получается плотный наплавленный металл со структурой и свойствами серого чугуна.
Для получения в наплавке чугуна с перлитной основой в состав прутков вводят редкоземельные металлы, стронций, цирконий. Например, предложен пруток следующего состава: 3,8—4,2 % С; 1,2—2,0 % Si; 0,2—0,6 % Μn; 0,03—0,30 % Zr; 0,01—0,25 % Sr; остальное Fe [11]. Наплавленный чугун имеет твердость НВ 180— 220 и поддается поверхностной закалке.
Весьма перспективной оказалась разработка составов прутков, обладающих самофлюсующимися свойствами. Эффект самофлюсования при сварке чугуна обеспечивают добавки бора, церия, иттрия. Состав такого прутка: 3,4—3,7 % С; 2,7—3,7 % Si; 0,4—0,7 % Μn; 0,1—0,6% Ni; 0,1—0,2% Ti; 0,01—2,50% Сu; 0,01—0,50 Sn; 0,05—0,2 % В; 0,05—0,25 % Се; 0,02—0,15 % V; остальное Fe [4]. Наиболее полно явление самофлюсования проявляется при сварке чугуна толщиной до 10 мм или заварке дефектов такой же глубины. При больших толщинах необходимо добавлять в сварочную ванну некоторое количество порошкообразного флюса. Установлено, что эффект самофлюсования повышается при дополнительном введении в состав прутка солей лития.
Для ацетилено-кислородной сварки чугуна с шаровидным графитом используются прутки, содержащие модифицирующие элементы: магний, кальций, редкоземельные металлы, иттрий.
Электроды с чугунным стержнем. Отличительной чертой электродов, обеспечивающих получение в шве чугуна, близкого по химическому составу, структуре и свойствам основному металлу, является высокое содержание углерода и кремния в стержнях и компонентах покрытия для максимальной графитизации сварочной ванны. Примером может служить сплав состава [8]: 3,1—3,4 % С; 2,9—3,3 % Si; 0,3—0,7 % Μn; 3,0—4,5 % Ni; 2,5—5,0 % Си; 0,5— 2,0 % Sn; остальное Fe. Наличие никеля, меди и олова гарантирует получение перлитной металлической основы.
В качестве стержней электродов могут использоваться прутки, предназначенные для газовой сварки (см. табл. 1).
Близкий состав по основным элементам к указанным выше стержням имеет присадочный пруток для сварки неплавящимся электродом в среде инертного газа, содержащий 3,7—4,2 % С; 3,5—6,0% Si; Μn-0,5%; 1,0—3,0% Al; S<0,1; P<1,0; остальное Fe .
Электроды для сварки чугуна с шаровидным графитом содержат в стержнях и покрытии щелочноземельные или редкоземельные металлы, способствующие образованию в металле шва графита шаровидной формы. Так, предложены прутки следующего соства: 3,4—3,8 % С; 2,5—3,0 % Si; 0,6—0,8 % Μn; 0,04—0,10 % Mg; 0,05—0,10% Ni; 1,0—1,5% Си; 0,06—0,15% Sn; остальное Fe. Технологичность процесса сварки повышается при дополнительном введении в присадочный материал 2,5—4,0 % меди и 3,0—5,0 % алюминия. Добавка олова улучшает обрабатываемость соединения [7]. Есть, однако, данные, что олово и алюминий ухудшают форму графита. Для нейтрализации вредного действия антиглобуляризаторов в наплавленный металл рекомендуется вводить некоторое количество церия, тория или лантана [5].
Из предлагаемых составов электродных покрытий [5, 7] наиболее перспективными являются следующие: 20—30 % графита; 40—54 % лигатуры ЖКМК; 10 % криолита; 10 % плавикового шпата; 5 % древесного угля; 0,5—4,5 % карбонатов редкоземельных металлов; 0,001— 3,500 % V; 1—8 % Mg; 1—5 % Са; 0,001— 3,000 % Се; 10—15% мрамора; 5—10% графита; 1—15% Fe; остальное— плавиковый шпат.
Известно, что шаровидная форма графита в чугуне с заданной металлической основой может быть получена за счет добавок небольшого количества глобуляризаторов, причем наиболее надежным и эффективным глобуляризатором является Mg.
В связи с тем, что Се и Са при температурах сварки значительно меньше испаряются, чем Mg, для образования в наплавленном металле шаровидного графита в электроды надо вводить комплексный модификатор и в первую очередь Се, Са и Mg.
Электроды с чугунным стержнем, обеспечивающие получение однородного и равнопрочного соединения при сварке .чугунов с пластинчатым и шаровидным графитом, применяются в основном для заварки литейных дефектов. Рекомендуется следующий режим сварки серого чугуна электродом диаметром 8 мм: Iсв= = 500—700 А; VД=35—40 В; ток переменный или постоянный обратной полярности. Отливки предварительно нагреваются до температуры 500—700 °С (в зависимости от условий сварки) и, как правило, подвергаются последующей термической обработке. Сварку высокопрочного чугуна надо производить током прямой полярности или переменным током, что позволит снизить потери Mg.
Порошковые проволоки. Повысить производительность процесса и улучшить условия труда сварщиков возможно за счет механизации способов дуговой сварки чугуна. Весьма перспективна сварка порошковой проволокой, позволяющая изменять в широких пределах химический состав наплавленного металла, механизировать процесс, увеличить производительность, улучшить условия труда.
В нашей стране и за рубежом находят применение разработанные в Институте электросварки им. Е. О. Патона порошковые проволоки типа ППЧ со стальной оболочкой [1]. Производительность процесса при использовании порошковой проволоки диаметром 3 мм составляет б—10 кг/ч (в зависимости от режима),
С целью повышения производительности наплавки разработаны два новых метода сварки порошковой проволокой. Первый из них предусматривает одновременную подачу в сварочную ванну трех проволок диаметром 3 мм. Для этого разработан специальный полуавтомат А-1072С, рассчитанный на работу на токах до 2000 А. Производительность наплавки достигает 17—19 .кг/ч. Другой путь — разработка состава порошковой проволоки диаметром 5,0—5,5 мм. Конструкция проволоки двухслойная, что повышает ее жесткость и электропроводность в условиях сварки. Металл, наплавленный порошковой проволокой ППЧ-ЗМ, представляет собой чугун с пластинчатым графитом и преимущественно перлитной матрицей. Отдельную группу составляют порошковые проволоки, дающие однородное соединение при сварке чугуна с шаровидным графитом. Технология сварки порошковой проволокой марки ПП-АНЧ-5 обеспечивает получение однородных и равнопрочных соединений из высокопрочного чугуна. Металл шва и зоны термического влияния представляют собой чугун с шаровидным графитом, химический состав и структура которого близки основному металлу.
Последующими исследованиями установлено, что эффективными модификаторами при сварке чугуна являются иттрий и скандий. Оптимальное содержание этих элементов в порошковой проволоке составляет, соответственно, 0,4—0,6% и 0,2—0,5% . Выпускаются и другие порошковые проволоки для сварки ВЧ: ППСВ-7 и ППВЧ-1.
Порошковые проволоки с модификаторами применяют для заварки дефектов литья, нанесения износостойких и жаростойких слоев и для ремонтных целей. Для исключения отбела в шве и зоне термического влияния производится предварительный подогрев изделий до. температуры 400—700 °С и, как правило, последующая термическая обработка.
Способ сварки чугуна стальной проволокой с присадкой керамических стержней получил дальнейшее развитие при замене проволоки сплошного сечения на порошковую. Керамические стержни марки СКЧ-3 в сочетании с порошковыми проволоками ППЧ-ЗМ или ПП-АНЧ-2 дают в наплавке серый чугун с пластинчатым графитом, а стержни марки СКВЧ-1 в сочетании с проволоками тех же марок — чугун с шаровидным графитом. В состав керамических стержней входят следующие компоненты: графит, карбид кремния, ферромарганец, алюминиевый порошок, плавиковый шпат, железный или чугунный порошок, модификаторы, жидкое стекло и др. [4, 6, 10].
Электроды для сварки без подогрева. При сварке чугуна стальным электродом происходит науглероживание шва за счет перехода углерода из основного металла. В результате ускоренного охлаждения в структуре шва образуются цементит и мартенсит, что приводит к повышению твердости, снижению пластичности и образованию трещин в сварном соединении. В зоне неполного расплавления, обедненной углеродом, образуются хрупкие структуры.
Технологические приемы сварки чугуна сталью — применение электродов малого диаметра; уменьшение плотности тока; обеспечение минимальной глубины проплавления чугуна — направлены на снижение твердости и склонности к образованию трещин в зоне сплавления и в первом слое наплавленного металла.
Большинство из предлагаемых стальных электродов имеют стержень из нелегированной стали, а компоненты покрытия предназначены для улучшения качества соединения, уменьшения отбела в шве и зоне термического влияния, что повышает обрабатываемость соединения и стойкость его к образованию трещин. Значительно реже для исправления небольших дефектов применяются электроды со стержнями из легированных и в первую очередь хромоникелевых сталей.
Наибольшее распространение получили электроды марки ЦЧ-4, которые дают возможность получить ферритный шов с мелкодисперсными карбидами ванадия. Электроды ЦЧ-ft состоят из стального стержня Ή покрытия, включающего феррованадий, ферросилиций, плавиковый шпат, мрамор, поташ и жидкое стекло. Наплавленный металл содержит [81: 0,8—1,2 % С; 0,8 % Si; 1,0 % Μn; 9,5 % V; 0,04 % Ρ; 0.04 % S; остальное Fe. Твердость металла шва k(HB) составляет 170—200, а зоны сплавления до НВ = 500. Электроды ЦЧ-4 используют при исправлении дефектов небольших и средних размеров на отливках, прошедших механическую обработку, а также для сварки с применением шпилек. Рекомендуемые режимы приведены в табл. 2. При однослойной сварке без подогрева в зоне сплавления образуется большое количество ледебурита и мартенсита, поэтому возникает опасность образования трещин. При многослойной сварке твердость несколько снижается. С помощью предварительного подогрева изделия можно получить твердость зоны .сплавления порядка НВ=350.