Нитроцементация
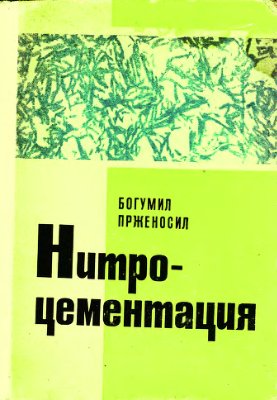
Прженосил Богумил
Машиностроение, 1969 г.
1.1. СУЩНОСТЬ НИТРОЦЕМЕНТАЦИИ
При нитроцементации поверхность стали насыщается в газовой атмосфере углеродом и азотом. Нитроцементованный слой образуется в результате одновременной диффузии углерода и азота в аустените.
Большинство деталей нитроцементуется при температурах выше 800° С, чаще всего при 840—860° С. Нитроцементованный слой, образующийся при этих температурах по существу аналогичен цементированному слою. Желательные механические свойства получаются за счет охлаждения его с температуры нитроцементации с такой скоростью, при которой достигается превращение углеродисто-азотистого аустенита в мартенсит.
Если нитроцементация проводится при температурах ниже 700° С, на поверхности нитроцементованного слоя образуется слой соединений железа с углеродом и азотом, обладающий большой стойкостью против задиров и износа.
В ближайшие годы можно ожидать, что нитроцементация получит применение при температурах порядка 700° С для деталей, подверженных износу и работающих в условиях полусухого и сухого трения.
Использование свойств поверхностного слоя, содержащего соединения железа с углеродом и азотом, до сих пор находится еще в зачаточном состоянии.
Главное экономическое значение в настоящее время имеет нитроцементация при температуре выше 800° С, применяемая наряду с цементацией для обработки сильно нагруженных деталей, особенно зубчатых колес.
1.2. ПРЕИМУЩЕСТВА НИТРОЦЕМЕНТАЦИИ
Присутствие азота в нитроцементованном слое обусловливает различия между нитроцементованным и цементованным слоями.
При одновременной диффузии углерода и азота в аустените ускоряется диффузия углерода. Скорость роста нитроцементованного слоя в случае малой его глубины (до 0,4 мм) при температуре 850—860° С приближается к скорости роста цементованного слоя.
Более низкая температура нитроцементации способствует уменьшению деформации, увеличивает долговечность печного оборудования и самое важное делает возможной закалку непосредственно после нитроцементации стали, имеющей в условиях цементации склонность к росту аустенитного зерна. В связи с более низкой температурой процесса нет необходимости при непосредственной закалке после нитроцементации применять подсту-живание детали до более низкой температуры.
Азот снижает температуру перекристаллизации аустенита. В процессе нитроцементации при температуре ниже точки А3границы аустенитной области сдвигаются в сторону меньшего содержания углерода. В результате этого облегчается диффузия углерода в сердцевину, не полностью перешедшую в аустенитное состояние. Поэтому при нитроцементации в отличие от цементации при температурах сердцевины ниже точки А3не происходит задержки в росте нитроцементованного слоя и образуется резкий переход от слоя к сердцевине.
Наличие азота в твердом растворе повышает устойчивость переохлажденного аустенита. В связи с этим нитроцементованные слои обладают более высокой прокаливаемостью, чем цементованные. Высокая прокаливае-мость слоя позволяет закаливать нитроцементованные детали из нелегированной стали в масле.
Азот повышает содержание остаточного аустенита в структуре закаленного нитроцементованного слоя. Остаточный аустенит снижает твердость слоя и содержание его ограничивается допустимой твердостью поверхности. Кроме того, остаточный аустенит в мартенситной структуре закаленного нитроцементованного слоя задерживает возникновение усталостных нарушений и повышает усталостную прочность нитроцементован-ных деталей.
Наличие остаточного аустенита в структуре слоя повышает также его пластичность, что ведет к повышению ударной вязкости и в меньшей мере к повышению прочности на изгиб у нитроцементованной стали. Повышенная пластичность нитроцементованного слоя обеспечивает достаточную вязкость и у деталей из стали с прочностью сердцевины 90—200 кГ/мм2. Применение такой стали открыло обширную область нитроцементации высоконагруженных зубчатых колес и валов. Большая прочность сердцевины дает возможность существенно уменьшить глубину слоя при равной выносливости и контактной прочности.
Так, например, для зубчатых колес производилась при прочности сердцевины 90—120 кГ/мм2цементация на глубину 0,8—0,9 мм, а при прочности сердцевины примерно 170 кГ/мм2достаточна глубина нитроцементованного слоя 0,25—0,30 мм, В этих случаях достигается сокращение производственного цикла нитроцементации по сравнению с цементацией на 60— 70%.
Нитроцементация зубчатых колес сопровождается значительно меньшей деформацией, чем цементация, что объясняется более низкой температурой процесса, меньшей глубиной слоя и более равномерным распределением внутренних напряжений первого рода в нитроцементованном слое. Сильно нагруженная нитроцементованная шестерня обладает также большим сопротивлением на истирание, что, по-видимому, связано со специфическим влиянием азота.
К недостаткам нитроцементации относится прежде всего необходимость строгого поддержания в нужных пределах науглероживающей и азотирующей способности газовой среды. Недостатком можно считать и то, что глубина слоя при нитроцементации практически ограничивается в пределах 0,7—0,8 мм вследствие дальнейшего снижения скорости роста диффузионного слоя.