Ниобийсодержащие низколегированные стали
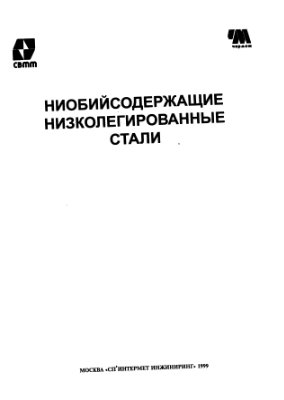
Хайстеркамп Ф., Хулка К., Матросов Ю.И., Морозов Ю.Д., Эфрон Л.И., Столяров В.И., Чевская О.Н.
Интермет Инжиниринг, 1999 г.
Глава 1. МИКРОЛЕГИРОВАННЫЕ СТАЛИ. ПОЧЕМУ НИОБИЙ, А НЕ ДРУГОЙ ЭЛЕМЕНТ?
Низколегированные стали — это низкоуглеродистые сплавы на основе железа. В их химический состав введены недорогие и недефицитные легирующие элементы в количестве, не превышающем 2,5 %. Эти стали обладают хорошей свариваемостью, повышенной прочностью и пониженной склонностью к хрупким разрушениям по сравнению с углеродистой сталью.
В качестве легирующих элементов используют такие недорогие и недефицитные элементы, как Si, Μn, Сr, иногда Сu, Мо, Νi·. Низколегированные стали применяются взамен углеродистых. Прочностные свойства низколегированных сталей выше, чем у углеродистых, в 1,3— 2,0 раза. Благодаря этому расход металла сокращается на 20—50 %. Но из-за расхода легирующих элементов и повышенной трудоемкости производства себестоимость низколегированных сталей выше, чем у углеродистых. Однако себестоимость проката из низколегированных сталей с ростом прочности увеличивается в меньшей степени, чем достигаемая экономия от уменьшения массы конструкций.
Наибольший эффект достигается при производстве низколегированных сталей, к которым относятся стали с пределом текучести большим 350 Н/мм2. При производстве таких сталей с целью снижения себестоимости применяют технологические приемы, направленные на повышение качественных характеристик, снижающие энергоемкость затрат (контролируемая прокатка, нормализующая прокатка, термомеханическая обработка, глубокая десульфурация, непрерывная разливка и т.д.), а с целью снижения расхода легирующих используют добавки микролегирующих элементов. Это малые добавки элементов, сотые доли которых оказывают на структуру и свойства стали существенное влияние. К таким элементам относятся ΑΙ, V, Nb, Ti, Zrи В, причем добавки бора составляют тысячные доли процента.
Наличие добавок микролегирующих элементов является важной характеристикой современных сталей и использование микролегированных сталей постоянно возрастает. Термин «микролегирование» означает, что содержание этих элементов невелико и обычно не превышает 10-1 %. Помимо очевидного различия в массовой доле, позволяющей отличать легирующие и микролегирующие элементы, также различен металловедческий механизм их влияния: легирующие элементы преимущественно воздействуют на матрицу стали, в то время как влияние микролегирующих элементов в значительной мере связано с выделением избыточных фаз. Дисперсные выделения фаз, которые формируются в структуре при распаде пересыщенных твердых растворов, препятствуют движению дислокаций, вызывая упрочнение матрицы, кроме того, частицы оказывают влияние на размер аустенитного и ферритного зерна, тип структурных составляющих, тип и характер распределения дефектов кристаллического строения.
Классическим примером использования микролегирования является алюминий, добавки которого широко применяют начиная с 1940-х годов для раскисления стали и измельчения зерна за счет образования нитридной фазы. С 1960-х годов нашли широкое использование для микролегирования элементы, расположенные в периодах от 4 до 6 и группах с IVaпо VIaПериодической таблицы элементов Д. И. Менделеева. Эти элементы имеют потенциал свободной энергии, необходимый для формирования нитридов и карбидов, который увеличивается от верхнего правого к нижнему левому углу приведенной части Периодической таблицы элементов Д. И. Менделеева (рис. 1.1). По сродству к углероду и устойчивости карбидов рассматриваемые металлы можно расположить в следующий ряд: Сг, Mo, W, V, Nb, Та, Ti, Zr, Hf. Склонность элементов к образованию нитридов выше, чем способность формировать карбиды [1].
В дополнение к способности формировать нитриды и карбиды элементы группы IVaимеют высокое сродство к кислороду и сере (образуют оксиды и сульфиды). В то же время элементы группы Viaимеют более низкое сродство к неметаллам, чем элементы групп IVaи Va, кроме того, их карбиды имеют гексагональную кристаллическую решетку, которая в сравнении с гранецентрированной кубической решеткой карбидов элементов групп IVaи Vaхуже сопрягается с кубической матрицей стали.
Для того, чтобы сформировались частицы, которые могут эффективно воздействовать на микроструктуру стали в процессе горячей прокатки или термической обработки, микролегирующий элемент должен быть первоначально переведен в твердый раствор. Растворимость элемента в аустените связана с разностью размеров его атома и атома железа (таблица). Из сильных карбонитридообразующих элементов цирконий и гафний вследствие большой разницы атомных радиусов с железом практически нерастворимы в нем и, следовательно, не представляют в рассматриваемом случае практического значения.
Исходя из вышеизложенного видно, что имеется ряд химических и физических аргументов против использования элементов VIaгруппы, а также циркония и гафния в качестве эффективных карбонитридообразующих элементов. Кроме того, малая распространенность и высокая стоимость препятствуют широкому использованию тантала. В результате практическое применение в качестве карбонитридообразующих элементов в стали могут иметь только титан, ванадий и ниобий. Далее рассмотрим характерные особенности только этих элементов и их соединений.
Равновесие в системе "металл — неметалл", растворение и образование фаз описываются произведением растворимости. Как указывалось ранее, титан является элементом, имеющим сильную тенденцию к формированию оксидов и сульфидов, а не только нитридов и карбидов, как ванадий или ниобий. На рис. 1.2 приведены произведения растворимости всех этих соединений титана. Видно, что оксид формируется уже в жидком состоянии. Даже нитрид титана (имея в виду типичное для стали содержание азота) будет образовываться до или в процессе кристаллизации. Такие частицы, сформированные в жидком состоянии, могут быть удалены в шлак, либо их размер достаточно велик вследствие высокой температуры образования, поэтому их влияние на измельчение структуры слабое и они могут рассматриваться как включения, оказывающие неблагоприятное влияние на свойства стали. Однако определенное положительное влияние на свойства стали наблюдается при формировании таких частиц, как TiOи TiN, за счет уменьшения количества кислорода и азота в твердом растворе, которые отрицательно влияют на вязкость стали. Пониженное содержание азота, кислорода или титана, а также более низкая температура образования TiOи TiNприводят к формированию более мелких частиц. Мелкодисперсные и стабильные частицы подходят для контроля размера аустенитных зерен и этот эффект используется при нагреве под горячую прокатку и для измельчения крупнозернистой зоны термического влияния при сварке. После кристаллизации титан реагирует с серой с образованием сульфидов и карбосульфидов. Так как карбосульфид титана имеет более высокую твердость, чем сульфид марганца при температурах горячей деформации, это успешно использовалось для контроля формы сульфидов, когда стандартное содержание серы в сталях было высоким. Кроме того, в нижней температурной области существования аустенита или после γ— α-превращения возможно формирование карбида титана.
Свободные энергии формирования нитридов и карбидов титана, ванадия и ниобия приведены на рис. 1.3 [2, 3].
Из рисунка видны различные возможности, достигаемые с помощью этих соединений:
1. Так как нитрид титана формируется при довольно высоких температурах, он практически не может быть растворен в аустените при нагреве. Эффект таких стабильных частиц заключается в контроле размера зерна при высоких температурах.
2. Нитрид и карбид ванадия полностью растворяются в аустените и поэтому не оказывают практически никакого влияния на размер зерна аустенита при высокотемпературном нагреве. Эти фазы выделяются только в процессе или после γ—α-превращения. Частицы, сформировавшиеся при такой низкой температуре, имеют очень малые размеры и дают вклад в упрочнение стали по механизму дисперсионного твердения.
3. Произведения растворимости карбида титана, нитрида и карбида ниобия занимают промежуточное положение, что свидетельствует о возможности указанных соединений растворяться в верхней части аустенитной области и выделяться при низких температурах.
На рис. 1.4 приведены изотермы растворимости NbC, TiCи VNв аустените для различных температур. Температура 900 °С соответствует нормализации или иной термической обработке стали, а изотерма при 1200 °С представляет состояние, типичное для нагрева под горячую деформацию [4, 5].
В типичной стали с содержанием углерода 0,15 %, подвергаемой нормализации при 900 °С, практически весь ниобий находится в виде частиц фазы NbC. Это же справедливо и для TiC, который имеет только немного большую растворимость в аустените по сравнению с NbC. Роль таких частиц заключается в закреплении границ аустенитных зерен, в результате чего после γ—α-превращения формируется мелкозернистая структура.
Изотермы при 1200 °С подтверждают, что в стали с содержанием углерода около 0,08 % (что типично для сталей, подвергаемых термомеханической обработке) может раствориться до 0,08 % Nbили 0,11 % Ti. Такое исходное содержание микролегирующих элементов в твердом растворе аустенита представляет собой основу для проведения термомеханической обработки путем торможения рекристаллизации в процессе прокатки.
Изотермы растворимости для VN(карбид имеет большую растворимость, чем нитрид) показывают, что любое количество ванадия будет полностью в твердом растворе даже при нагреве в нижнюю часть аустенитной области.
Состояние, близкое к описываемому произведением растворимости, достигается, например, при нагреве под горячую деформацию. Как и все другие элементы, микродобавки, находясь в твердом растворе замедляют процессы, контролируемые диффузией (рост зерна, рекристаллизацию). Это торможение возрастает с увеличением разницы размеров атома элемента по сравнению с атомом железа.
Другим контролируемым диффузией процессом является γ—α-превращение, которое замедляется микролегирующими элементами, находящимися в твердом растворе. Частицы кар-бонитридных фаз, выделившиеся до превращения, наоборот, ускоряют превращение.
Все нитриды и карбиды титана, ванадия и ниобия имеют гранецентрированную кубическую кристаллическую решетку и полностью растворимы друг в друге. Следовательно, эти кар-бонитриды могут существовать не только в чистом, но и в комплексном виде, что оказывает влияние на их свойства (растворимость и др.). Вопрос плотности карбонитридов не имеет особого значения для микролегированных сталей, если их формирование происходит в твердом состоянии. При больших количествах микролегирующих элементов (например, в инструментальных сталях) формирующиеся первичные карбиды могут быть распределены равномерно в металле только тогда, когда их плотность близка к плотности жидкого металла. В этом конкретном случае благоприятным оказалось совместное микролегирование ванадием и ниобием, обеспечивающее формирование комплексного карбида (Nb+ V) с плотностью около 7 г/см3.
Параметр решетки фазы влияет на возможное упрочнение путем дисперсионного твердения.
Упрочнение зависит от количества частиц и их размера [6, 7]. Очень эффективны для дисперсионного твердения частицы размером примерно от 1 до 2 нм.
Крупные частицы, образующиеся в процессе деформации в аустенитной области, также некогерентны с матрицей и мало влияют на дисперсионное твердение. Поэтому их основная роль — измельчение микроструктуры.
На рис. 1.5 обобщены данные по эффекту упрочнения феррита при микролегировании титаном, ванадием и ниобием [8—10], справедливые для широкого интервала содержания углерода. В связи с большой разницей параметров решетки между когерентными частицами и а-железом вокруг выделений карбонитридов возникают сильные поля напряжений. Исходя из этого, эффективность микролегирующих элементов должна быть связана с параметрами решетки их карбонитридов. В результате один и тот же эффект упрочнения достигается при использовании вдвое меньшего количества ниобия, чем ванадия. Но благоприятное влияние ниобия ограничивается его тенденцией образовывать выделения уже в аустенитной области, и эта тенденция усиливается деформацией. Следовательно, требуемый эффект дисперсионного упрочнения частицами фазы NbCможно ожидать и применять только в низкоуглеродистых сталях или после высокотемпературной горячей деформации. Соединения ванадия, легче растворимые в аустените, в большей степени пригодны для дисперсионного упрочнения в феррите.