Нержавеющие стали
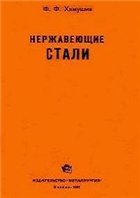
Химушин Ф.Ф.
Металлургия, 1967 г.
Горячая обработка давлением
Нержавеющие стали мартенситного, ферритного, полуферритного и аустенитного классов по-разному подвергают ковке и горячей прокатке.
Оборудование для горячей обработки давлением нержавеющих сталей в основном не отличается об оборудования, применяемого для обработки углеродистых и низколегированных сталей. В связи с тем, что нержавеющие стали, особенно аустенитные, имеют более высокие прочностные свойства при температурах горячей обработки, необходимо иметь более мощное оборудование, так как требуются большие затраты энергии при получении полуфабриката того же размера, чем при обработке углеродистой стали.
Многие нержавеющие стали обрабатывают в более узком интервале температур, поэтому важно иметь оборудование, обеспечивающее условия для сохранения тепла при переносе заготовок и горячей обработке давлением. Кроме того, чтобы после деформирования хорошо измельчилось зерно, требуются легкие удары в начале обработки и тяжелые в конце. Регулировка ударов важна также при изготовлении изделий более сложной формы. Следовательно, для ковочного и прессового инструмента следует применять более прочные и упругие штамповые стали [797, 798]. Для облегчения течения металла рекомендуется применять обильную смазку из графита (сухого), смешанного с маслом или водой, соляные растворы, стекло и др.
Использование менее окисляющих или контролируемых атмосфер при нагреве заготовок под ковку и прокатку уменьшает количество окалины и способствует меньшему износу инструмента. При горячей обработке давлением металл на первой стадии нагревают медленно до 820—870° С с выдержкой для прогрева при этих температурах, затем на второй стадии заготовки быстро нагревают до температур ковки или прокатки. Медленный нагрев и выдержка при указанных температурах сокращают время пребывания стали при высоких температурах, тем самым уменьшают окалинообразование и возможность растрескивания, которое может возникнуть вследствие большого температурного градиента, а для аустенитных сталей — еще высокого коэффициента линейного расширения.
Для уменьшения температурного градиента инструмент следует подогревать, что связано с применением более стойких против отпуска штамповых сталей.
Вследствие образования тугоплавких окислов хрома в трещинах и несплошностях нержавеющие стали не самосвариваются. Дефекты этого типа, образующиеся в металле при горячей обработке давлением, не завариваются, как в углеродистых сталях. Поэтому очень важно нагрев сталей на первой стадии вести тщательно с тем, чтобы металл хорошо был прогрет и в нем не образовались внутренние трещины. На второй стадии нагревают заготовку быстрее, так как этому способствует более высокая теплопроводность металла при высоких температурах. Слишком длительный нагрев заготовок приводит к пережогу, связанному с окислением и насыщением газов.
При определении способности стали к горячей обработке давлением и нахождения благоприятного температурного интервала часто определяют способность стали к пластической деформации скручиванием при высоких температурах. В работе [302] подробно исследованы свойства (δ, ψ, аk) сталей марок: 10, 45; ЭЯ1Т, ЭИ402, ЭИ439, ЭИ257, ЭИ448, ЭИ432 при 1000—1350° С (рис. 390), связанных с их сопротивлением деформации при высоких температурах. Одновременно проводилась опытная прошивка труб из указанных сталей. Чем выше сопротивление скручиванию (по числу скручиваний до разрушения), тем выше способность стали к горячей обработке давлением.
На диаграмме пластичность — температура у некоторых сталей можно отметить минимумы, максимумы и монотонное изменение пластичности с температурой, что зависит от неоднородности структуры аустенита или феррита или же от количества фаз в случае сталей переходного класса 17171.
Для стали 1Х18Н9Т сперва пластичность при температуре до 1200° С увеличивается, что связано с уменьшением количества δ-феррита, и далее резко падает с увеличением его количества. Полное падение пластичности (хрупкость) сталей наблюдается при температурах, приближающихся к температуре солидуса, однако это зависит от состояния границ зерен, температура плавления которых может наступать значительно раньше вследствие локального скопления легирующих элементов и различных примесей (Pb, Sn, Sи др.), понижающих температуры плавления [14, 718—720 ].
Наиболее высокой пластичностью обладает чисто ферритная сталь Х25Т, меньшей пластичностью — сталь Х25Ю5 и углеродистые стали 10 и 45. Аустенитные стали обладают значительноменьшей пластичностью, чем ферритные (рис. 391). В ряде случаев добавки редкоземельных элементов (Са, Ва, La, Zr, Се) улучшают пластичность нержавеющих сталей в горячем состоянии и длительную прочность [14, 718].
Температурные режимы нагрева нержавеющих сталей по данным отечественной и зарубежной практики различны по маркам и классам (табл. 225, 226). Эта разница относится главным образом к максимальным температурам нагрева и объясняется тем, что в зарубежной практике нагрев заготовок перед горячей обработкой давлением более кратковременный [773]. Как правило, заготовки не оставляют в сварочном пространстве длительное время, если почему-либо наступает перерыв при прокатке или ковке.
Горячую обработку давлением нержавеющих сталей различных классов ведут по-разному, учитывая их особенности,
Хромистые стали мартенситного класса
Вследствие малой теплопроводности сталей при умеренных Температурах нагрев под горячую обработку давлением сначала ведут медленно, а затем по мере прогрева и повышения температуры несколько быстрее. При быстром нагреве разница в температуре поверхности и сердцевины большая; возникающие огромные напряжения приводят к разрыву в середине и к образованию так называемых скворечников.
Первые удары молота должны быть осторожными во избежание появления трещин по границам первичных зерен, а затем более энергичными. Температура конца ковки сталей мартенситного класса должна быть не ниже 850° С и охлаждать металл после ковки следует медленно в колодцах, в золе или в подогретом песке.
Хромистые полуферритные и ферритные стали
Горячая обработка сталей этого типа должна заканчиваться при более низких температурах (700—800° С), но с повышенными степенями деформации в конце ковки или прокатки. Стали ферритного класса, имея большую склонность к росту зерен при температурах выше 800° С, благодаря рекристаллизации становятся крупнозернистыми, если ковка заканчивается при более высокой температуре.
Аустенитные стали менее склонны к росту зерна, но деформация, так же как и полуферритных и ферритных сталей, в конце прокатки должна быть достаточной, а температура не ниже 850— 900° С.
Крупнозернистость сталей, ковка или прокатка которых заканчивалась при высокой температуре, не может быть исправлена последующей термической обработкой.
В работе [49] приведены диаграммы рекристаллизации сталей полуферритного и ферритного классов, показывающие, что с повышением температуры у сталей аустенитного класса наблюдается меньшая склонность к укрупнению зерна, чем у сталей ферритного.
Свойства сталей (механические и коррозионные) достигаются в том случае, если в процессе горячей обработки давлением строго выполняются температурные условия и степень деформации.
Хромоникелевые стали при умеренных температурах (600— 800° С) имеют пониженные пластические свойства вследствие образования карбидов, поэтому эти стали нельзя подвергать горячей деформации при пониженных температурах, т. е. ниже температур конца ковки, указанных в табл. 225, 226.
Вследствие понижения пластичности в стали возможна склонность к растрескиванию. Повышение температуры нагрева выше установленной ведет к резкому увеличению зерна и к разрушению границ зерен, что ведет к растрескиванию или потере механичен ских и коррозионных свойств металла.
После горячей деформации в изделиях появляются остаточные напряжения вследствие одновременного действия самой деформации и температуры, при которой происходит образование и выделение избыточных карбидов. Эти напряжения снимаются и пониженная коррозионная стойкость восстанавливается термической обработкой, которая для аустенитных сталей состоит из нагрева стали до высоких температур (1000—1150° С) — аусте-низации и быстрого охлаждения, что подробно рассматривается при описании соответствующей стали, и в главе о коррозионном растрескивании нержавеющих сталей под напряжением.