Непрерывный сталеплавильный процесс
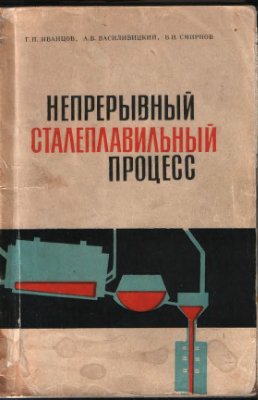
Иванцов Г.П., Василивицкий А.В., Смирнов В.И.
Металлургия, 1967 г.
АНАЛИЗ ОПУБЛИКОВАННЫХ СХЕМ НЕПРЕРЫВНЫХ СТАЛЕПЛАВИЛЬНЫХ ПРОЦЕССОВ
И АГРЕГАТОВ
В настоящей главе предпринята попытка оценить описанные схемы и варианты осуществления завершенных непрерывных процессов выплавки стали.
Многочисленность опубликованных схем не дает возможности остановиться подробно на каждой из них. Поэтому здесь рассмотрены, как правило, объединенные по основным нринцнпам технологические схемы процесса и конструктивного оформления агрегатов.
1. Технологические решения
Опубликованные схемы непрерывных сталеплавильных процессов в своем большинстве предполагают объединение всего комплекса реакций рафинирования металла в едином реакционном объеме, т. е. являются вариантами одностадийного совмещенного процесса.
Сторонников таких схем привлекает простота и дешевизна агрегата. Однако идея процесса вызывает серьезные возражения.
Как было указано выше, металл в ванне непрерывно действующего агрегата с нормальным перемешиванием по своему составу и температуре должен соответствовать конечному металлу в течение всего периода стабильной работы агрегата. Это определяет высокотемпературный характер процесса, проводимого в одном объеме, и чрезвычайно сложные и невыгодные требования к шлаковому режиму. В первую очередь имеется в виду проведение достаточно, глубокой десульфурации и дефосфорации металла.
Высокая температура, окислительный характер процесса (в то же время ограниченный необходимостью сохранить требуемое содержание углерода в стали) и высокое содержание кремнезема в шлаке, обусловленное полным окислением кремния, создают условия, принципиально противопоказанные для реакций серы и фосфора. Это неизбежно резко снижает термодинамический стимул перехода указанных примесей в шлак, и обеспечить высокий потенциал шлака в данных условиях весьма и весьма трудно, не выходя из границ реальных возможностей.
Известно, что при периодическом сталеплавильном процессе (в частности, в кислородно-конвертерном) для более или менее успешного удаления серы и фосфора из чугуна необходимо выполнение ряда условий — в первую очередь соблюдения определенных составов металлошихты и конечного шлака, ритма обезуглероживания и т. п. [44, 45].
Состав конечного шлака, необходимый для получения приемлемых содержаний фосфора и серы в стали, обычно удается обеспечить лишь путем скачивания первичного шлака и наводки нового. Иногда практикуется даже двукратное обновление шлака. Но и в этих условиях в конечный период плавки система близка к равновесию по указанным примесям, т. е. потенциал шлака в отношении серы и фосфора исчерпан.
Одностадийное рафинирование металла при непрерывном процессе в сочетании с обычным расходом реагентов создает условия, близкие в отношении состава шлака к условиям конвертерного или мартеновского процесса, проведенного без скачивания и обновления шлака. Очевидно, что такой шлак вообще не будет обладать потенциалом дефосфорации и десульфурации по отношению к конечным содержаниям фосфора и серы в металле, т. е. его термодинамические возможности будут существенно ниже, чем при периодическом процессе, где используется эффект обновления состава шлака, изменения температурных условий и т. п.
В то же время, как было показано в гл. III, специфика непрерывного процесса — протекание его на уровне конечных параметров системы — обусловливает необходимость значительного увеличения расхода реагентов даже в тех случаях, когда термодинамические условия в остальном совпадают с условиями периодического процесса. Следовательно, для проведения сколько-нибудь интенсивного непрерывного процесса необходимо существенно изменить состав шлака — так, чтобы значительно повысить его дефосфорирующий и десульфурирующий потенциал. Выполнение такого требования при любом разумном процессе, очевидно, невозможно, поскольку вызовет чрезмерный угар железа и расход флюсов. Принципиальная причина этого положения заключается в том, что невозможно обеспечить при совмещенном непрерывном процессе достаточно благоприятные условия протекания всех реакций рафинирования.
Попытаемся подтвердить это фактическими данными. К сожалению, описание лишь одной из одностадийных схем рафинирование в вертикальном вращающемся коническом сосуде (см. стр. 93—95)] содержит данные опробования. Анализ этих данных (если предположить, что отходящие из сосуда газы аналогичны конвертерным) показывает, что угар железа в описанном: случае опробования составил более 15% от веса чугуна, а шлак содержал более 60% окислов железа.
Условия службы футеровки при высокотемпературном режиме совмещенного процесса и наличии больших количеств активного шлака весьма тяжелы. Это снизит стойкость аппарата, т. е. вызовет большой расход огнеупоров и частые ремонты.
Особо следует остановиться на проблеме регулирования такого процесса. Наличие параллельно протекающих в одном объеме реакций, в том числе и конкурирующих между собой, резко уменьшает возможность поддерживать подвижное равновесие процесса на требуемом уровне. В динамическом равновесии находятся все массопотоки удаляемых примесей и тепловые эффекты реакций. При изменении какого-либо параметра исходного металла (содержания той или иной примеси, температуры или расхода), неминуемом в реальных условиях через какой-то интервал времени, потребуется корректировка процесса. Например, повышение исходного содержания какой-либо примеси потребует немедленной форсировки ее удаления со шлаком процесса. В противном случае возрастет ее содержание в конечном металле. Соответствующее изменение расхода реагентов и шлакового режима неминуемо нарушит массопотоки остальных примесей и общее равновесие процесса. В этих условиях характер работы автоматической управляющей системы будет весьма сложен.
В условиях большой металлургии такой процесс не сможет конкурировать с действующими периодическими процессами и потому эту идею для условий большой металлургии следует считать неприемлемой, несмотря на кажущуюся привлекательность из-за простоты конструктивного решения.
Однако в других условиях совмещенный процесс непрерывного рафинирования, по-видимому, перспективен и может быть реализован. Имеются в виду условия передела бессемеровского чугуна или работы агрегатов фасоннолитейных цехов, использующих малофосфористые чугуны и применяющих десульфурацию в вагранках с подогретым дутьем.
Во всех случаях, когда не требуется заметного удаления фосфора и серы, может быть реализован процесс типа непрерывного бессемерования в аппарате с кислой футеровкой при осуществлении операций раскисления и легирования в последующем сосуде. При таком процессе удаление кремния и марганца до необходимых содержаний в стали обеспечено при всех условиях и задача сводится к сохранению заданного содержания углерода в конечном металле. Таким образом, устранение операции удаления фосфора и серы снимает основные возражения против одностадийного варианта рафинирования.
Большинство двустадийных схем рафинирования построено по аналогии со схемой разделения основного кислородно-конвертерного процесса на два этапа, первый из которых соответствует периоду начала продувки вплоть до скачивания шлака, и второй — следующему, завершающему периоду.