Непрерывная разливка стали
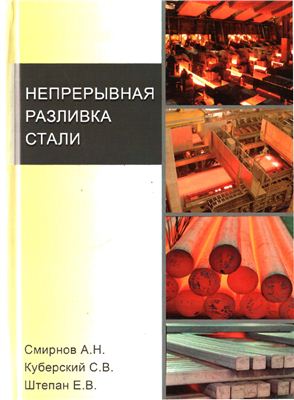
Смирнов А.Н., Куберский С.В., Штепан Е.В.
Донецк: ДонНТУ, 2011 г.
Разливка металла на тонкие слябы и литейно-прокатные модули
С начала 90-х годов прошлого века в практику создания эффективных технологических систем по производству плоского проката прочно вошло понятие литейно-прокатный модуль (ЛПМ), в котором органично совмещается процесс непрерывной разливки стали на заготовку и ее последующая, без охлаждения, горячая прокатка.
Принято считать, что первый промышленный ЛПМ был пущен в эксплуатацию в 1989 г. в г. Крофордсвилле (США): компания «Nucor» ввела в эксплуатацию завод, оснащенный электродуговыми печами и МНЛЗ для получения сляба толщиной 50 мм.
При этом слябы передавались непосредственно на стан горячей прокатки. Этот процесс получил название CSP {Compact Strip Production), а разработка была выполнена фирмой «Schloeman-Siamag» (Германия).
В целом технологическая система на базе ЛПМ может быть представлена следующим образом: выплавка стали в дуговой печи (или конвертере) —> доводка стали на установке «ковш-печь» —> (вакуумирование стали в ковше) —> разливка стали на сляб (толщина сляба 50-70 мм) и его горячая прокатка в технологической цепочке ЛПМ —> прокатка на станах холодной прокатки. При этом, как показала практика, для получения 1 тонны холоднокатаного листа достаточно 1,10-1,12 тонны жидкой стали, а значительный энергосберегающий эффект (рисунок 6.17) достигается, главным образом, за счет сокращения технологической цепочки и исключения дополнительных циклов охлаждения и нагрева заготовки.
Лидером в создании ЛПМ (по объему разработок и количеству реализованных агрегатов) является фирма «SMS-Demag» (Германия). Собственную концепцию ЛПМ разработала фирма «Mannesmann Demag» и дала ей название ISP (Inline Strip Production). Она реализована в 1992 г. на заводе в Кремоне фирмы Arvedi.
Глубокие научные и конструкторские разработки в этой области выполнены итальянской фирмой "Danieli". Фирма " Siemens-VAI" также рассматривает создание ЛПМ как перспективное направление. Однако их разработки базируются на получении сляба средней толщины (80-130 мм) и его последующей прокатке (например, металлургический завод в г. Острава, Чехия).
Схема расположения основных функциональных единиц ЛПМ (линейное расположение) представлена на рисунке 1.16. Современная практика применения ЛПМ показывает, что их разливочный модуль представляет собой, как правило, высоко функциональную одноручьевую МНЛЗ, в которой совмещены все основные достижения в области разливки стали. Прокатная часть ЛПМ может быть совмещена с одной или двумя МНЛЗ в зависимости от номинальной производительности цеха.
Основные решения, обеспечивающие совмещение технологии разливки на МНЛЗ тонких слябов и их прокатку, заключаются в следующем:
1. Сокращение до минимума числа промежуточных этапов технологического процесса (исключение промежуточных этапов охлаждения и нагрева заготовки и т.п.) за счет гармонизации процесса разливки стали и прокатки заготовки. Предполагается, что скорость вытяжки непрерывно-литой заготовки и ее последующей прокатки совпадают по величине (удельный расход металла). Стабильность работы литейной части модуля достигается за счет автоматизации работы всех его составных частей и механизмов.
2. Концепция ЛПМ не предусматривает промежуточный контроль качества заготовки и, тем более, ее сортировку и доводку. В таких условиях стабильность работы литейной части модуля достигается за счет жесткого обеспечения ряда показателей качества жидкой стали в ковше перед разливкой (включая температуру). Поэтому оптимальное сочетание технологических операций на стадии выплавки и ковшевой обработки в совокупности с техническими параметрами агрегатов имеет определяющее значение, как в отношении производительности, так и качества металлопродукции.
3. Создание системы сопряженных технических решений, обеспечивающих разливку с высокими скоростями на тонкий сляб. Основной задачей при этом является обеспечение стабильного подвода жидкой стали в вертикальный кристаллизатор и равномерное ее распределение по всей ширине сляба. С этой целью фирмой «SMS-Demag» запатентовано оригинальное решение для внутренней полости кристаллизатора, который в верхней части имеет воронкообразную форму, позволяющую беспрепятственно вводить погружной стакан (рисунок 6.18).
4. Конструкция кристаллизатора тонкослябовой МНЛЗ (рисунок 6.19) предусматривает возможность изменения ширины сляба непосредственно в процессе разливки (максимальное изменение ширины, как правило, составляет не более двух раз). Длина кристаллизатора составляет 0,9-1,0 м. Скорость вытяжки сляба в таких МНЛЗ составляет 5-10 м/мин.
5. Применение системы электромагнитного торможения потока металла, подаваемого в кристаллизатор (ЕМВг). Электромагнитный тормоз создает в верхней части кристаллизатора регулируемое по напряжению электромагнитное поле. Втекающая в него сталь пересекает это поле и в ней наводятся напряжения и токи, которые закорачиваются в жидкой стали. Вызываемые этим процессом силы тормозят потоки стали и обеспечивают равномерно распределенное движение металла вниз и по сечению сляба.
6. Механизм качания кристаллизатора выполняется с гидравлическим приводом, позволяющим обеспечить свободный выбор амплитуды и частоты колебаний в процессе разливки и корректировать эти параметры при изменении скорости вытяжки заготовки. С целью минимизации глубины следов качания и расхода ШОС, например, амплитуда качаний кристаллизатора увеличивается, а частота качаний уменьшается по мере увеличения скорости разливки. Закон качания кристаллизатора - несинусоидальный.
7. Обеспечение вертикального участка МНЛЗ в ЗВО на всей протяженности затвердевания тонкого сляба и последующий его загиб с выходом на горизонтальную плоскость (рисунок 6.20).
8. Реализация технологии разливки с дополнительным многоточечным обжатием заготовки с жидкой сердцевиной непосредственно под кристаллизатором в ЗВО (до толщины 35-40 мм) (рисунки 6.21, 6.22). На современных тонкослябовых МНЛЗ, которые имеют высокий уровень автоматизации, это достигается посредством непрерывного определения конфигурации жидкой лунки с соответствующей коррекцией начала и окончания обжатия. Общая величина такого обжатия для тонкослябовых МНЛЗ достигает 20-30 мм. При этом меньшая толщина сляба позволяет добиться большей производительности при прокатке его в тонкий лист.
9. Установка устройства для удаления окалины с поверхности сляба перед ножницами для порезки заготовки на мерные длины.
10. Использование туннельной печи для выравнивающего подогрева заготовки (непосредственно после порезки и без дополнительного охлаждения).
Длительность пребывания тонкого сляба в печи обеспечивает практически полную равномерность распределения температуры по ширине, толщине и длине сляба. Точность выравнивания температуры ± 10°С. Поэтому последующие операции (прокатку и охлаждение) ведут при постоянной скорости.
11. Прокатка тонкого сляба в группе черновых и чистовых клетей с целью получения проката в рулонах (толщина листа до 1-1,2 мм). Для этих целей применяются две различные схемы: система непрерывной прокатки (рис. 1.16) и система прокатки на стане Стеккеля (рисунок 6.23).
12. Общая система автоматического управления ЛПМ, обеспечивающая переработку больших объемов информации и выполнение скоростных операций, что необходимо для производства высококачественной продукции на стане горячей прокатки.
В целом же все ведущие фирмы, производящие металлургическое оборудование, занимаются разработкой литейно-прокатных агрегатов, обеспечивающих разливку на тонкий или средний сляб, совмещенную с прокаткой на тонкий лист (таблица 6.3).
Так, фирмой «Маннесман Демаг Хюттентехник» разработан процесс ISP, который во многом аналогичен процессу CSP. Тонкий сляб толщиной 60 мм выходит из кристаллизатора с еще жидкой сердцевиной и на участке опорных роликов подвергается мягкому обжатию до толщины 45 мм. Затем после полного затвердевания сляб прокатывается в трехклетьевой группе на полосу толщиной 15-20 мм. После индукционного промежуточного подогрева и прокатки полоса подвергается смотке в рулон. На установке 1SP фирмы «Арведи» (Италия) можно получать полосу толщиной 1,1 мм и более.
В целом совмещенные литейно-прокатные модули представляют собой высокоэффективные агрегаты для получения тонкого листа, которые весьма успешно вписываются в современные конвертерные и электросталеплавильные цехи, что обеспечивает им высокую конкурентоспособность. За годы промышленной эксплуатации ЛПМ показали себя как надежная система технологий со стабильными показателями, удовлетворяющими требованиям мировых стандартов.
Внедрение процесса совмещенного литья тонких слябов и горячей прокатки полосы в черной металлургии в странах с традиционной металлургией идет более медленными темпами, чем в других регионах мира. Это объясняется в основном высоким уровнем развития традиционной технологии производства плоского проката и возможностью удовлетворения всех рыночных нужд.
Следует ожидать, что в обозримом будущем технология ЛПМ получит еще большее распространение на действующих металлургических заводах Европы, и в частности, Украины и России.