Неоднородность и работоспособность стали
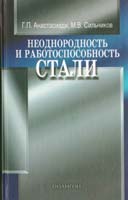
Анастасиади Г.П., Сильников М.В.
Полигон, 2002 г.
ХРУПКИЕ РАЗРУШЕНИЯ СТАЛИ В ВЫСОКОПРОЧНОМ СТРУКТУРНОМ СОСТОЯНИИ
Высокопрочное состояние среднелегированных сталей с содержанием углерода 0,10... 1,0 % по массе можно создать путем закалки, последующий отпуск снижает прочность, но повышает пластичность. Поскольку углеродистый мартенсит имеет высокие внутренние напряжения и малую способность их релаксации в процессе выдержки при комнатной температуре, в свежезакаленной стали могут возникать «холодные» трещины. Аналогичные явления происходят в процессе сварки конструкций из листовых или сортовых заготовок сталей повышенной прочности.
Фактически зона сварного шва имеет структуру литой стали, а зона термического влияния включает область закаленной стали возможным самоотпуском, если сварка производилась с подогревом. Отпуск для снятия термических и фазовых напряжений после сварки является сложной технологической операцией и для крупногабаритных конструкций, например для корпусов транспортных бронированных машин производится местным нагревом при слаборегулируемомрежиме. В высокопрочных сталяхпадение разрушающего напряжения в свежезакаленном состоянии может достигать 80 % при малом времени выдержки и снижаться до 20 % при большом времени выдержки.
Типичные кривые замедленного разрушения, заимствованные из работы [72], приведены на рис. 8.13. Для среднеуглеродистой низколегированной стали марок 30ХНЗА и 35ХГ2 перлитного класса отдых в течение 66 часов и отпуск при 100 "С приводит сталь в работоспособное состояние. Высоколегированная сталь марки 30X13 мартенситного класса склонна к замедленному разрушению: в закаленном без отпуска состоянии она разрушается при напряжениях σ < 0,2σΒ; после отпуска при 200 "С разрушающие напряжения составляют σ < 0,3σ,; только после отпуска при 300 "С сталь марки 30X13 приобретает работоспособное состояние.
Следует обратить внимание на то, что нормативные документы, в том числе ГОСТ 5949, рекомендуют для стали марки 30X13 режим термической обработки, включающий закалку и низкий отпуск при 200...300 X. Однако приведенные выше исследования замедленного разрушения свидетельствуют о нестабильности работоспособности сталей мартенситного класса в низкоотпущенном состоянии. Опыт работы свидетельствует о реальной вероятности выхода из строя деталей из сталей со структурой отпущенного мартенсита (мартенситного и мартенситно-ферритного класса), включая сталь марки 09Х16Н4БЛ в закаленном и отпущенном при 300 °С состоянии при рабочих напряжениях. Экспертиза таких разрушений устанавливала хрупкое разрушение отрывом, которое должно быть исключено в конструкционной стали.
Стали повышенной прочности в значительном объеме применяются для сварных конструкций. Процесс электродуговой сварки «стирает» структуру и механические свойства стали, термически обработанной на определенную категорию прочности, и соответствующие характеристики пластичности. Режим предварительной окончательной термообработки заготовок оказывается подавленным мощным источником тепла, стимулирующим нагрев стали до температуры 1300 "С со скоростью нагрева и охлаждения в несколько градусов (или десятков градусов) в секунду. Высокая скорость нагрева определяет неоднородный состав по углероду и другим элементам аустенита, образовавшегося из ферритно-цементитной смеси (для среднелегированных сталей) или ферритно-карбидной смеси (для сталей с высоким содержанием карбидообразующих элементов). Поскольку выдержка при температуре аустенизации составляет минуты, последующей при охлаждении закалке подвергается неоднородный аустенит, и в зоне термического влияния образуется весь набор возможных продуктов распада от мартенсита до перлита. Область мартенсита, прилегающая к сварному шву, составляет половину зоны термического влияния — около 5 мм. С точки зрения работоспособности это достаточно широкая самостоятельная в механическом отношении зона свежезакаленного мартенсита. В монографии [72] проведен анализ структуры зоны термического влияния 25 среднелегированных марок сталей в зависимости от параметров сварки, показано, что зона термического влияния независимо от начального структурного состояния включает смесь мартенсита, бейнита и перлита в различных соотношениях. В любом случае стали повышенной прочности после сварки подвержены разрушению при напряжениях σ < 0,5σΒ. Обычно рассматриваются два механизма задержанного разрушения [72, 110]:
— проскальзывание атомных плоскостей в приграничных областях, приводящее при комнатной температуре к образованию и быстрому распространению трещин, при этом рекомендуется предварительная обработка холодом с целью исключения разрушения;
— вакансионное течение при наличии высокого уровня внутренних напряжений, приводящее к образованию микрополостей, являющихся зародышами трещин и трактами для их движения.
К ним можно добавить формирование микронеоднородности распределения примесей внедрения (сегрегации) на границах зерен в соответствии с кинетикой диффузионного «дрейфа» в поле напряжений, возникающих в приграничных областях различных структурных составляющих. Этот механизм описан в главе 6. Экспериментальные данные, которые могут быть использованы для обоснования этого механизма, показаны на рис. 6.13,6.14. Распределение углерода определялось в композиционном материале, состоящем из стали 40Г13 и стали 40Х2СМФ, полученном методом экструзии распыленных порошков. Структура композиционного материала состоит из включений аустенита стали 40Г13 при любом режиме охлаждения и мартенсита (после закалки) или мартенсита отпуска (после закалки с низким отпуском). Распределение углерода после закалки характеризуется наличием ярко выраженных обогащений на границе аустенита и мартенсита, связанных, очевидно, с высоким уровнем напряжений на границе мартенсита и аустенита. После отпуска обогащения на границах мартенсита слабовыражены.