Навивка пружин на автоматах
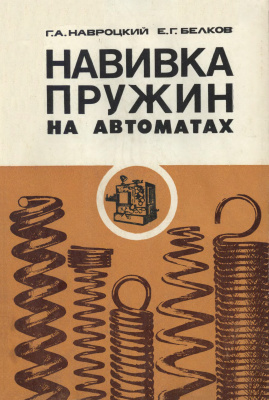
Навроцкий Г.А., Белков Е.Г.
Машиностроение, 1978 г.
3.МЕТОДЫ ИСПЫТАНИЯ ПРУЖИННОЙ ПРОВОЛОКИ
Значительная часть дефектов пружин возникает из-за плохого качества пружинной проволоки. Наиболее распространены следующие дефекты:
недопустимый разброс геометрических параметров при навивке вследствие неравномерности механических свойств проволоки по длине и при спутанной проволоке в бунте;
отклонение контрольной нагрузки от номинального значения вследствие несоответствия диаметра проволоки требованиям чертежа;
поломка проволоки при навивке или пружин при испытании из-за недостаточных пластических свойств проволоки, ее внутренних дефектов;
поверхностные дефекты витков, переходящие с проволоки на пружину и снижающие ее динамическую прочность;
значительная остаточная деформация пружины при контроле силовой характеристики и упругих свойств из-за пониженной прочности проволоки и большого обезуглероженного слоя и др.
В большинстве случаев такие дефекты неисправимы, поэтому проволоку перед навивкой следует подвергать контролю и испытаниям различных видов.
Измерение диаметра проволоки и контроль овальности необходимо выполнять измерительным прибором соответствующей точности в двух-трех местах по длине бунта (катушки). Овальность проволоки не должна превышать половины допуска по диаметру.
Поверхность проволоки осматривают невооруженным глазом, с применением лупы пятикратного увеличения, с зачисткой поверхности проволоки в сомнительных местах. Проволока должна иметь гладкую поверхность без трещин, плен, закатов, раковин и ржавчины. На поверхности проволоки допускаются следы волочения в виде рисок, а также омеднение и другие покрытия, применяемые в процессе волочения. Глубина допускаемых рисок не должна превышать половины допуска по диаметру. Глубина обезуглероживающего слоя определяется по ГОСТ 1763—68 и не должна превышать 1% фактического диаметра с каждой стороны. Наиболее распространенный метод определения глубины обезуглероженного слоя — металлографический. Образцы для изготовления шлифов вырезают поперек проволоки механическим способом, не вызывающим изменений в структуре металла. Травление шлифа, выполняемое в 2— 4% -ном растворе азотной или никриновой кислоты в этиловом спирте, должно гарантировать четкое выявление структурных составляющих. Общую глубину обезуглероженного слоя, включающего зоны полного (чистый феррит) и частичного (переходная структура) обезуглероживания, определяют под микроскопом. Измерять следует в месте наибольшей для данного образца глубины.
Микроструктура закаленной и отпущенной проволоки по ГОСТ 1071—67 должна состоят из сорбита или тростосорбита. Наличие в структуре игольчатой ориентировки и участков структурно-свободного феррита не допускается.
Для определения механических характеристик и проверки технологических свойств проводят четыре вида испытаний проволоки: на растяжение по ГОСТ 10446—63, на скручивание по ГОСТ 1545—63, на перегиб по ГОСТ 1579—63, на навивание по ГОСТ 10447—63.
Для неупрочненной проволоки необходимо также измерение твердости по ГОСТ 9012—59 и ГОСТ 9013—59.
Испытание упрочненной проволоки на растяжение является наиболее распространенным, его выполняют на образцах с расчетной длиной 100—200 мм на разрывной машине, максимальная нагрузка которой не превышает пятикратного разрывного усилия проволоки. Характеристика разрывной машины должна соответствовать ГОСТ 7855—74. Полная длина образца должна включать участки для закрепления в зажимах. Тонкая пружинная проволока, обладающая высокой прочностью, часто обрывается в универсальных зажимах, поэтому для ее испытаний применяют специальные зажимы (рис. 12), состоящие из двух пар щечек (гладких и с насечкой). Перед испытанием замеряют начальный диаметр проволоки do, в процессе испытания определяют максимальную силу при разрыве Ртах- Если разрушение произошло в зажимах разрывной машины, то испытание считают недействительным и повторяют его на другом образце. Предел прочности при растяжении определяют как отношение нагрузки к начальной площади поперечного сечения:
После испытаний измеряют минимальный диаметр шейки du и определяют относительное сужение ψ — отношение уменьшения площади поперечного сечения в месте разрыва к начальной площади:
Поскольку модуль упрочнения нагартованной, а также закаленной проволоки сравнительно мал и локализация деформации происходит без заметных остаточных удлинений проволоки, то относительное удлинение при разрыве не проверяют. Полученные при испытании пределы прочности должны соответствовать техническим требованиям. При испытании на разрыв с узлом, применяемым для тонкой проволоки вместо испытаний на перегиб, разрывающее усилие должно составлять не менее 50% разрывающего усилия той же проволоки при испытании ее без узла. Для определения предела пропорциональности и условного предела текучести применяют тензометры с ценой деления шкалы 0,002 мм. Метод определения механических характеристик при растяжении регламентирован ГОСТ 1497—73.
• При испытании проволоки на скручивание выявляются пластические свойства металла. Один из захватов прибора для испытания на кручение должен вращаться, не перемещаясь вдоль осевой линии, другой должен иметь только продольное перемещение для нагружения осевой силой, не превышающей 2% разрывного усилия Ртах- Образец должен быть зажат в захватах так, чтобы в процессе испытания он не проворачивался. Скручивание образца должно проводиться до его разрушения без остановки, с равномерной частотой вращения, не превышающей: 90 об/мин для проволоки диаметром d< 1,5 мм, 60 об/мин для 1,5-3,0 мм, 30 об/мин для r = 3 мм и более.
Расчетную длину образца устанавливают равной 100 d, но не менее 50 мм и не более 500 мм.
Испытание считается недействительным и должно быть повторено на другом образце, если разрушение его произошло в захватах машины или вблизи захватов (на расстоянии менее 5 мм) и образец при этом не выдержал число скручиваний, установленное стандартом или техническими условиями на проволоку. В соответствии с требованиями стандартов и технических условий может проводиться испытание на скручивание с переменой направления кручения.
При испытании на перегиб образец зажимают в губках тисков и с помощью рычага и поводка подвергают знакопеременному изгибу на ±90° через валики. Диаметры валиков, параметры прибора и его конструкция приведены в ГОСТ 1579—63. Последний перегиб, на котором произошло разрушение образца, в расчет не принимают.
При испытании проволоки на навивание используют оборудование, обеспечивающее возможность закрепления и вращение стержня необходимого диаметра с равномерной частотой вращения, не превышающей 60 об/мин. Проволока для пружин ответственного назначения по ГОСТ 1071—67 диаметром <4 мм не должна расслаиваться и ломаться при навивке пяти витков на стержень, равный диаметру проволоки. Проволока по ГОСТ 9389—75 по требованию потребителя не должна ломаться или растрескиваться после навивки пяти витков вокруг стержня, диаметр которого равен тройному диаметру испытуемой проволоки — для проволоки диаметром d>6 мм, двойному диаметру испытуемой проволоки — для d = 4,0—6,0 мм, диаметру испытуемой проволоки—для d<4,0 мм.
4. КОНТРОЛЬ ПРУЖИН
Контроль и испытание пружин является заключительной, операцией их изготовления. Объем испытаний и их виды должны быть указаны в чертеже или технических условиях. Основные требования к готовым цилиндрическим пружинам сжатия и растяжения регламентированы ГОСТ 16118—70.
Наиболее распространенными видами контроля и испытаний пружин холодной навивки являются следующие: наружный осмотр, дефектоскопия; контроль геометрических параметров силовой характеристики и упругих свойств при обычной и повышенной температурах; заневоливание; динамические испытания.
На практике применяют и другие виды контроля и испытаний пружин, например монтажные испытания, испытания коррозионной стойкости пружин после гальванического покрытия контроль интенсивности наклепа при дробеметной обработке (технологический), контроль химического состава материала структуры, глубины обезуглероженного слоя и др.
Предъявленные к приемке пружины подвергают визуальному контролю снаружи, иногда с применением лупы пятикратного увеличения. На поверхности витков не допускаются трещины, волосовины, раковины, расслоения, закаты, ржавчина, а также местная скрученность. Допускаются без зачистки мелкие забоины, морщины, отдельные царапины и риски, а также следы от навивочных оправок и роликов, если они распространены не глубже, чем наполовину поля допуска на диаметр проволоки. В сомнительных случаях глубину дефектов определяют контрольной пологой зачисткой.
Для выявления дефектов (трещин, расслоений) ответственных пружин применяют метод магнитной дефектоскопии. Намагниченные пружины погружают в суспензию магнитного порошка в масле. Благодаря резкому изменению характера магнитного поля в местах нарушения сплошности металла магнитный порошок оседает вдоль трещин в виде черных линий и пятен. Контроль методом дефектоскопии оговаривается в чертеже пружины. Наружный осмотр проводят до и после контрольных испытаний.
Геометрические параметры пружин проверяют как универсальным измерительным инструментом (штангенциркуль, микрометр, угломер), так и специальными калибрами, применяемыми в серийном и массовом производстве. При использовании универсального инструмента наружный диаметр пружины измеряют не менее чем в трех местах во взаимно перпендикулярных направлениях. При контроле калибрами пружина должна свободно проходить через проходную гильзу-калибр, длина рабочей части которой должна быть не меньше утроенного шага пружины. Если пружина предназначена для эксплуатации в ограниченном пространстве, то ее наружный диаметр следует проверять в предельно сжатом состоянии с помощью гильзы. Длина гильзы должна быть на 10% меньше длины сжатой пружины. Пружину при контроле помещают внутрь гильзы и сжимают до соприкосновения витков, при этом необходимо, чтобы гильза свободно перемещалась вдоль пружины. Если в чертеже указан контроль внутреннего диаметра пружины, то проходной контрольный стержень-калибр должен проходить через полость не- нагруженной пружины. Одновременное задание размеров с отклонениями на внутренний и наружный диаметры не допускается. При единичном и мелкосерийном производстве обычно установочным диаметром назначают наружный.
При холодной називке на автоматах наблюдается отклонение пружины от цилиндрической формы, связанное с изменением шага навивки (поджатые торцы и др.). В зависимости от индекса и схемы навивки (сжатие + изгиб, растяжение + изгиб) появляется бочкообразность или корсетность пружины, так как при изменении угла подъема винтовой линии изменяется кривизна и упругая отдача после разгрузки. Кроме того, при без- оправочной навивке (сжатие + изгиб) в моменты реза и начала подачи происходит отклонение от окружности первого витка (преимущественно в сторону увеличения диаметра) вследствие разновидности трения скольжения и трения покоя и от действия усилия реза и усилия внедрения шагового клина. Поэтому при холодной навивке пружин сжатия на автоматах (крупносерийное производство) наиболее удобный способ технологического контроля диаметра при навивке — назначение предельных отклонений на внутренний диаметр и указание максимально допустимого наружного диаметра пружины в свободном состоянии. В этом случае для технологического контроля пружины применяют совмещенные калибры, состоящие из проходного и непроходного стержней-калибров и проходной гильзы.
Проходной стержень-калибр выполняют по высоте равным длине пружины в свободном состоянии, а выступ на торце равен допуску по длине. Высота непроходного стержня-калибра и гильзы должна быть больше половины длины пружины. Калибр окончательного контроля изготовляют для размеров, указанных в чертеже, от технологического он отличается на величину изменения геометрических параметров пружины после отпуска, шлифования торцов и других технологических операций.
У пружин растяжения установочным диаметром является наружный. Полный допуск (поле допуска) диаметра пружин в зависимости от индекса пружины и группы точности выбирают по ГОСТ 16118—70. Точность по геометрическим параметрам: пружин из проволоки d< 1,4 мм, а также пружин, подвергающихся технологической осадке и упрочнению дробью, должна быть не выше II группы.
Длину пружины контролируют с помощью универсального инструмента или при измерении силовых параметров на динамометрических весах.
ТЕХНОЛОГИЯ НАВИВКИ. КОНСТРУКЦИЯ АВТОМАТОВ
1. СПОСОБЫ НАВИВКИ ПРУЖИН
Все существующие методы навивки винтовых пружин можно разделить на две принципиально различные схемы: навивка на оправку по схеме растяжение+изгиб и навивка с помощью подающих роликов на упорные штифты по схеме сжатие+изгиб. Если при навивке по схеме сжатие +изгиб установлен один упорный штифт и необходима оправка для перегиба через нее (или через кромку направляющей планки), то схема докритическая, если же установлены два упорных штифта и перегиб через оправку не требуется, то схема закритическая. Большая часть современных пружинонавивочных автоматов работает по схеме сжатие + изгиб, наиболее применяемые из них двухштифтовые автоматы.
На рис. 37 представлена классификация схем холодной навивки винтовых пружин.
Навивка на вращающуюся оправку — наиболее простой способ, его применяют в единичном и мелкосерийном производстве при ручной навивке на приспособлениях, при механизированной навивке, например с помощью токарного станка. В серийном и массовом производстве применяют специализированные автоматы с вращающейся оправкой (шенкельного типа). На рис. 38, а показана схема навивки пружины на вращающуюся оправку с разводом витков. Развод витков может быть осуществлен или смещением вращающейся справки вдоль оси, или соответствующим смещением направляющей втулки. При навивке пружин без развода витков направляющая втулка приспособления для натяжения проволоки может быть расположена на значительном расстоянии или смещена вдоль оправки с шагом, равным диаметру проволоки. Навивка с отгибом проволоки заключается в том, что проволока подается к оправке под углом 90° — а, причем отгиб происходите сторону навитой части пружины. При такой навивке витки плотно прилегают друг к другу с межвитковым давлением.
Если при навивке на оправку обеспечить скручивание проволоки в направлении к навитой части пружины (рис. 38, б), то в полученной пружине возникает межвитковое давление (предварительная нагрузка). Большее межвитковое давление получается при навивке с отгибом и обкаткой роликом (рис. 38, в). Навиваемая проволока проходит под углом 90° — а к оправке в пазу направляющей колодки 5, по винтовой линии предварительной навивки огибает уже навитую часть пружины 1 и с помощью ролика 2 прижимается к оправке 4 между навитой частью и упором 3.