Настройка, стабилизация и контроль процесса тонколистовой прокатки
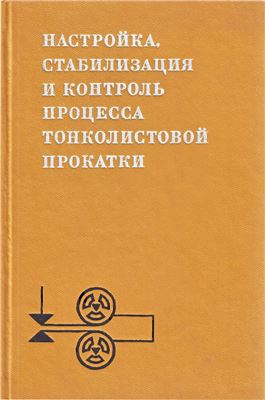
Григорян Г.Г., Железнов Ю.Д., Черный В.А., Кузнецов Л.А., Журавский А.Г.
Металлургия, 1975 г.
РАСЧЕТЫ ОСНОВНЫХ ПАРАМЕТРОВ НАСТРОЙКИ ТОНКОЛИСТОВЫХ СТАНОВ
1. РАСЧЕТ РЕЖИМА ПРОКАТКИ С УЧЕТОМ ЭНЕРГОСИЛОВЫХ И ПРОЧНОСТНЫХ ХАРАКТЕРИСТИК ОБОРУДОВАНИЯ И ОСОБЕННОСТЕЙ ТЕХНОЛОГИИ
В настоящее время не существует единой методики выбора режима прокатки на непрерывном стане, которая была бы в достаточной мере формализована. Необходимость более или менее строгого определения требований к режиму прокатки и последовательности операций для его выбора возникла лишь в последнее время в связи с возможностью применения вычислительной техники для решения задач настройки. В ряде случаев наблюдается различие в выборе режима обжатий на аналогичных станах при сходном сортаменте. Так, например, 9татистический анализ режимов обжатий по математическому ожиданию и среднеквадратичному отклонению величины ε,./εΣ (ε. — обжатие в клети, εΣ — суммарное обжатие), проведенный для десяти различных типоразмеров, прокатываемых на станах холодной прокатки 1700 Череповецкого и Ждановского металлургических заводов, показал (рис. 82), что, во-первых, на станах Череповецкого металлургического завода обжатия распределены по клетям более равномерно, чем на станах Ждановского завода, где проявляется ярко выраженный по всем типоразмерам пик обжатий во второй клети; во-вторых, малость среднеквадратичных отклонений конкретных значений обжатий от их математического ожидания указывает на стабильность распределения обжатий по клетям стана, которое практически не зависит от типоразмера. Диапазон среднеквадратичных отклонений показан на графиках пунктирной линией.
За последние годы выполнен ряд теоретических и экспериментальных работ по тонколистовой прокатке , которые могут служить основой для разработки рекомендаций по выбору режимов прокатки. Нашей задачей является формулирование основных принципов разработки режима прокатки и определение на этой основе достаточно простого, приемлемого для инженерной практики, алгоритма расчета.
При выборе режимов прокатки необходимо учитывать как энергоснловые, так и предъявляемые технологические требования и ограничения.
К энергосиловым ограничениям следует отнести ограничения по максимальному усилию прокатки, ограниченному прочностью механического оборудования клети, и по моменту или мощности двигателя. Причем на скоростях ниже номинальной ограничение целесообразно накладывать по мощности, а на скоростях, выше номинальной — по моменту. Имея в виду необходимость регулирования толщины н планшетности полосы в процессе прокатки, при выборе режима прокатки следует оставлять некоторый запас как по усилию, так и по моменту (мощности). Действительно, если это условие не выполнять, то любое перемещение винтов или изменение натяжений, используемое, например, в системе регулирования толщины [51], приведет к выходу за прочностные или за энергетические ограничения.
Технологические требования могут накладывать жесткие ограничения на режим обжатий. Так, например, необходимость обеспечения требуемой температуры конца прокатки и степени деформации в последней клети ограничивает выбор возможных режимов горячей прокатки. Учет технологических ограничений позволяет выбрать среди возможных режимов тот, который определяется лучшим соответствием данному ограничению. Так, например, при холодной прокатке режим обжатий можно рассматривать с точки зрения явления самовыравнивания поперечной и продольной разнотолщинности. Экспериментальные и теоретические исследования коэффициента самовыравнивания продольной разнотолщинности [57, 148] в статике показали, что наиболее значителен эффект самовыравнивания в первых клетях, в которых полоса наклепана незначительно. Отсюда можно сделать вывод о целесообразности снижения обжатий в первых клетях стана с целью максимизации самовыравнивания продольной разнотолщинности.
Однако с точки зрения энергетической загрузки оборудования это означает разгрузку привода первой клети, а так как она разгружается по моменту за счет переднего натяжения, то мощность привода первой клети будет фактически недоиспользована. Целесообразным, по-видимому, является выбор режимов, максимизирующих использование оборудования и с этой точки зрения обжатия в первой клети должны быть значительными. Регулировку толщины и устранение разнотолщинности следует осуществлять с помощью САРТ. Рассмотрим кратко влияние распределения обжатий по ширине полосы по клетям стана. Эффект самовыравнивания вытяжек по ширине возрастает с увеличением жесткости полос и удельных давлений металла на валки. Он максимален в последних клетях стана, и, исходя из этого, для повышения самовыравнивания последние клети также целесообразно нагружать по обжатию.
Однако большинство из технологических ограничений снимается, если ставится задача максимизации производительности стана за счет увеличения скорости прокатки при ограниченных энергетических ресурсах стана, т. е. если мощность электрооборудования стана выбрана без существенного запаса по всем прокатываемым профилям. В этом случае для получения максимума производительности потребуется нагрузить до пределов все клети, оставив запас лишь на последующее регулирование процесса. При этом регулировка толщины, а также планшетности должна обеспечиваться соответствующими системами автоматического регулирования.
Таким образом, при выборе режима прокатки возможны различные постановки задач. Можно говорить о выборе режима максимизирующего самовыравнивания продольной или поперечной разнотолщинности, однако при этом будут недоиспользованы резервы стана по производительности. За основной критерий оптимальности можно принять производительность оборудования, т. е. выбирать режимы, позволяющие загрузить его максимально. В этом случае возможно определить:
1) максимально допустимые толщины подката при заданных характеристиках стана и конечной толщине готовой полосы;
2) режим прокатки, максимизирующего скорость при заданных параметрах подката и готовой полосы.