Наладка и эксплуатация газоочистных сооружений в черной металлургии
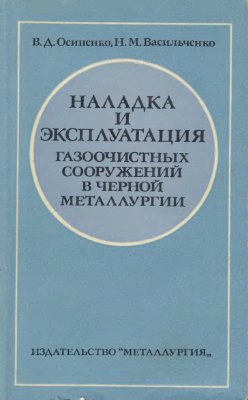
Осипиенко В.Д., Васильченко Н.М.
Металлургия, 1983 г.
ТИПЫ АППАРАТОВ СУХОЙ ОЧИСТКИ ГАЗОВ
ГРАВИТАЦИОННЫЕ И ИНЕРЦИОННЫЕ ПЫЛЕУЛОВИТЕЛИ
Аппараты сухой очистки газов, применяемые в черной металлургии, предназначены для очистки технологических и аспирационных газов только от пыли. По принципу действия они разделяются на гравитационные, инерционные, центробежные, электрические и фильтрующие.
В зависимости от требований, предъявляемых к степени очистки газов, свойств и дисперсного состава пыли аппараты сухой очистки газов могут применяться как самостоятельно, так и в сочетании с другими газоочистными аппаратами.
К гравитационным аппаратам относятся пылевые камеры, которые имеют различные конструктивные модификации. Осаждение пыли в гравитационных пылеуловителях происходит под действием силы тяжести на частицу. На нее оказывает влияние и сила взаимодействия с несущим потоком газа. В гравитационных пылеуловителях создаются такие условия, при которых сила тяжести преобладает над силой взаимодействия частицы пыли с потоком газа вследствие резкого снижения скорости газа в сечении пылевых камер. Как правило, гравитационные пылеуловители применяются в качестве первой ступени очистки газов — грубой и позволяют улавливать пыль с размером частиц более 100 мкм. Для улавливания более мелких частиц пыли гравитационные пылеуловители не применяются.
ЦЕНТРОБЕЖНЫЕ ПЫЛЕУЛОВИТЕЛИ
Центробежные пылеуловители являются наиболее распространенными аппаратами для сухой очистки газов; конструктивно эти аппараты выполнены в виде циклонов. Принцип работы их основан на использовании центробежных сил, возникающих при вращательно-поступательном движении газового потока в корпусе циклона. Такое движение обеспечивается путем тангенциального ввода газа в циклон под углом наклона входного патрубка к горизонтали. При этом под действием центробежных сил частицы пыли отбрасываются к стенке корпуса циклона и с частью газов поступают в бункер. В бункере происходит отделение пыли от газа, который затем через центральный газоотводящий патрубок выходит с основной массой газов. Из бункера пыль выводится через затворный аппарат типа мигалка.
Для очистки газов в больших объемах, например агломерационных, возможно применение батарейных циклонов.
Батарейный циклон состоит из большого количества циклонов небольших размеров, объединенные в одном корпусе и имеющих общий подвод и отвод газов. Целесообразность применения батарейных циклоном обусловлена, как правило, местными условиями компоновки газоочистных сооружений. С точки зрения эффективности очистки газов следует отдать предпочтение групповым циклонам.
К инерционным пылеуловителям относятся вихревые аппараты, которые в настоящее время находят широкое применение для высокоэффективной сухой очистки газов. Вихревой пылеуловитель, разработанный институтом ВНИПИчерметэнергоочистка» работает по следующему принципу. Запыленный газ поступает в аппарат снизу через лопаточный завихритель; при этом создаются центробежные силы, которые отбрасывают пыль к стенкам корпуса аппарата. В предварительно закрученный поток подают через специальные сопла, тангенциально установленные под углом к вертикали, вторичный воздух. Запыленный поток получает дополнительное вращательное движение, что усиливает влияние центробежных сил и обеспечивает отвод скопившейся у стенок корпуса аппарата пыли в бункер-накопитель. Отвод очищенных газов осуществляется через регулирующую диафрагму, закрывающую корпус аппарата.
При прочих равных условиях вихревой пылеуловители по сравнению с аппаратами инерционного типа и обычными циклонами имеет значительно большую эффективность улавливания мелкодисперсной пыли (до 50 мкм).
Приняты следующие эффективные диаметры вихревых аппаратов: 200, 300, 500, 600, 1350 мм. Средняя скорость газа по сечению рабочей полости аппарата не должна превышать 7,2 м/с. Скорость истечения газа из сопла с завихрителем не должна быть меньше 50—70 м/с; расход вторичного воздуха (или очищенного газа) составляет 20—25 %. Угол наклона сопел вторичного дутья выбирается из условий необходимой эффективности очистки газов и колеблется в пределах 12—24°. Применение вторичной подачи воздуха увеличивает коэффициент очистки газов примерно на 18 % [13].
Вихревые аппараты характеризуются компактностью] и высокой надежностью в эксплуатации; могут применяться в агломерационном, доменном, огнеупорном и других производствах.
Очистка газов методом фильтрации производится а фильтрах тканевых и с пористой перегородкой. Наиболее распространенными тканевыми фильтрами являются pyкавные. На рис. 7 показана принципиальная схема работы таких фильтров. Конструктивно фильтр выполнен и виде герметичного корпуса, разделенного на несколько камер, в которых размещены рукава из ткани. Камеры имеют коллекторы загрязненного и очищенного газа. Коллектор загрязненного газа снабжен бункером для пыли. Газ из этого коллектора поступает внутрь рукава! где фильтруется и откуда выходит в коллектор очищенного газа. Частицы пыли, осаждающиеся на поверхности ткани, накапливаются, что приводит к повышению гидравлического сопротивления рукава. По достижении οпределенного перепада давления производится регенерация рукавов. Для выполнения операции регенерации камера отключается от коллектора загрязненного газа. Таким образом, камеры фильтра работают поочередно, в результате чего количество работающих камер на одну меньше общего их количества.
АППАРАТЫ И СХЕМЫ МОКРОЙ ОЧИСТКИ ГАЗОВ
ПОЛЫЕ СКРУББЕРЫ
Аппараты для мокрой очистки технологических выбросов широко распространены в металлургии. Они имеют ряд достоинств, которые определяют их преимущество в некоторых случаях перед аппаратами сухой очистки газов. К этим достоинствам следует отнести низкие капитальные затраты при строительстве без систем очистки и возврата воды, высокая степень очистки газов от мелкодисперсной пыли, возможность очистки высокотемпературных газов и улавливания химических вредностей, простота в эксплуатации.
Наряду с этим аппараты мокрой очистки газов имеют и недостатки: необходимость обработки сточных вод, которые получаются в результате очистки газов мокрым способом; высокие эксплуатационные затраты по сравнению с затратами по сухим аппаратам; износ основных элементов газоочисток, связанный с коррозией металлов под воздействием сточных вод, насыщенных кислотными или щелочными компонентами.
Наиболее распространенными аппаратами мокрой очистки газов в металлургии, которые различаются принципом действия и способом диспергирования жидкости являются: полые форсуночные и насадочные скрубберы, аппараты ударно-инерционного действия, аппараты центробежного действия, скрубберы Вентури. Барботажные и пенные аппараты, а также динамические газопромыватели различных конструкций менее распространены в черной металлургии из-за низкой эффективности улавливания мелкодисперсных частиц пыли (пенные и барботажные аппараты) и значительных энергетических затрат при эксплуатации (динамические газопромыватели). Такие типы аппаратов могут быть применены для очистки небольшого количества технологических и аспирационных выбросов.