Наладка и эксплуатация газоочистных сооружений в черной металлургии
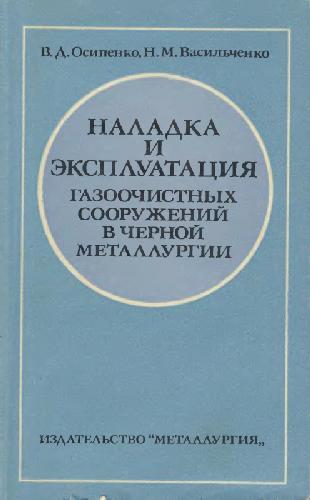
Осипенко В.Д., Васильченко Н.М.
Металлургия, 1983 г.
ИСТОЧНИКИ ОБРАЗОВАНИЯ ПЫЛЕГАЗОВЫХ ВЫБРОСОВ
Для предприятий черной металлургии характерным является многообразие качественного и количественного состава выбросов от основного и вспомогательного производств. Это обусловлено наличием в отрасли значительного количества основных и вспомогательных агрегатов, обслуживающих разные технологические процессы. К ним относятся коксовые батареи, башни мокрого тушения кокса, мартеновские, ферросплавные, электросталеплавильные печи, вагранки, конверторы, агломашины, травильные ванны, котлоагрегаты и промышленные печи, сжигающие природный газ и малосернистый мазут, сушильные барабаны, печи обжига извести и цемента, шихтовые отделения и т. д.
Все выбросы в зависимости от источника можно разделить на организованные и неорганизованные. Как правило, основное технологическое производство является источником организованных выбросов, а вспомогательное производство — неорганизованных.
Предприятия черной металлургии с полным замкнутым циклом производства включают агломерационное, доменное, сталеплавильное и прокатное производства. Кроме того, в состав таких предприятий в виде отдельных цехов могут входить коксохимическое, ферросплавное и огнеупорное производства. В связи с этим источники образования пылегазовых выбросов в черной металлургии удобно рассматривать по видам производств.
Агломерационное производство является одним из основных источников загрязнения воздушного бассейна. Организованные выбросы образуются в процессе спекания аглошихты, охлаждения агломерата и возврата его.
При спекании шихты необходимо просасывать через слой ее определенное количество воздуха для сжигания углерода и дожигания СО до СО2. Эти газы, проходя через слой шихты, насыщаются пылью и увлекают с собой сернистый ангидрид и недожженную окись углерода, попадают через коллектор в вакуум-камеру. Из последней газы поступают на очистку и выбрасываются через дымовую трубу в атмосферу.
Охлаждение агломерата производится путем просасывания через слой шихты атмосферного воздуха. При этом образуются газы, насыщенные пылью, которые также попадают в вакуум-камеру и после очистки выбрасываются через дымовую трубу в атмосферу.
В зависимости от технологии спекания и охлаждения агломерата возможны два варианта отсоса технологических газов от агломашины. Первый вариант заключается в отсосе газов одновременно из зоны спекания и охлаждения и подаче общего количества газов на очистку через общий коллектор. Второй вариант, характерный для агломашины с удлиненной зоной охлаждения, предусматривает раздельный отсос газов от зон спекания и охлаждения. Это обеспечивает более глубокое охлаждение агломерата. В этом случае две системы газоочистки работают раздельно-Большое количество запыленных газов образуется в местах разгрузки агломерата в хвостовой части агломашины. Как правило, отсос и очистка этих газов осуществляются в отдельно установленной аспирационной системе. В некоторых случаях эта система может быть включена в систему очистки газов зоны охлаждения.
Неорганизованные выбросы образуются в процессе транспортировки, выгрузки, загрузки и дробления шихтовых материалов (руды, извести, колошниковой пыли и т. д.). Источниками образования неорганизованных
п выбросов являются: корпус вагоноопрокидывания, рудный двор, места погрузки агломерата в вагоны и др.
Кроме того, на многих аглофабриках имеются отделения для обжига известняка в машинах ОПР, БЦРМ и др., которые также являются источниками пылегазовых выбросов, содержащих известковую пыль, окись углерода'и сернистый ангидрид.
Все перечисленные источники пылеобразования, за исключением рудного двора и мест погрузки агломерата в вагоны, в настоящее время оборудуются системами аспирации с последующей очисткой газов в основном от пыли.
Коксохимическое производствохарактеризуется большим количеством выбросов, содержащих разнообразные химические вредности. Основными источниками выбросов являются цехи углеподготовки, коксовые, улавливания химических продуктов коксования, сероочистки, ректификации и смолопереработки.
Независимо от схемы подготовки угля источниками выбросов в цехах углеподготовки являются места выгрузки угля, углеприемные ямы, транспортеры, отделения предварительного дробления и дозирования шихты, угольные башни. В процессе подготовки угля в атмосферу выбрасывается в основном угольная пыль. Источниками выбросов в коксовом цехе являются отопительная система коксовых печей, системы загрузки угля и выдачи кокса, башни тушения кокса, коксовые рампы и коксо-сортировка, а ,в цехах улавливания продуктов коксования и цехов ректификации — различные неплотности в оборудовании и открытые емкости и отстойники. В цехах сероочистки и смолопереработки выбросы в атмосферу составляют газы, прошедшие специальную очистку, но содержащие остаточное количество вредных веществ.
Основными мероприятиями по сокращению выбросов от коксохимического производства являются: организация бездымной загрузки и выгрузки кокса; широкое внедрение установок сухого тушения кокса; максимальное уплотнение оборудования; высокая эффективность работы улавливающих и перерабатывающих установок.
Доменное производствоявляется источником организованных и неорганизованных выбросов.
Доменный газ содержит большое количество окиси углерода (до 30 %), что позволяет использовать его в качестве топлива. Вопросу очистки доменного газа посвящено много работ [3, 6 и 9], поэтому в данной книге ему не уделяется много внимания. Как правило, доменный газ проходит тонкую очистку перед подачей его потребителю.
Неорганизованные выбросы в доменном производстве образуются при загрузке сырья в доменную печь, транспортировке продуктов плавки. При разгрузке вагонов, перегрузке руды грейферами, подаче руды на бункерную эстакаду, разгрузке трансферкаров на бункерной эстакаде также образуется большое количество пыли, которая поступает в атмосферу. Указанные источники выбросов еще не везде оборудуются системами аспирации и очистки воздуха в связи со сложностью организации их улавливания. При работе грохотов, лебедок и других механизмов, а также при транспортировке материалов в доменную печь выделяется большое количество пыли. Эти источники пылеобразования оборудуются системами аспирации.
На литейном дворе при выпуске чугуна и шлака образуются выбросы, содержащие пыль, окись углерода, серы. При разливке чугуна на разливочных машинах также происходят выбросы, содержащие пыль и окись углерода. Сложность борьбы с неорганизованными выбросами на литейных дворах действующих доменных цехах заключается в отсутствие эффективных устройств для улавливания газов.
Для вновь строящихся доменных печей разработаны и успешно эксплуатируются системы аспирации литейного двора с отсосом газов от леток и желобов и очисткой этих газов от пыли- Например, такой системой аспирации была оборудована доменная печь № 9 на Криворожском металлургическом заводе, что позволило значительно улучшить санитарные условия на литейном дворе и резко сократить выбросы в атмосферу.
Снизить неорганизованные выбросы можно их локализацией путем устройства укрытий леток, желобов и участков слива чугуна и шлака.
При работе доменных печей с повышенным давлением газа под колошником из засыпного аппарата (межконусного пространства) периодически выбрасывается значительное количество пыли и окиси углерода. Институтом «ВНИПИчерметэнергоочистка» разработаны два способа борьбы с выбросами из межконусного пространства. Первый — это исключение перетока грязного газа из печи в период ссыпания материалов, второй — очистка этих газов в специально установленном аппарате.
Вредные выбросы образуются также при переработке и грануляции шлака (содержат вредные сернистые компоненты) , а также в помещениях глиномялки и при разгрузке пылеуловителей.
Сталеплавильное производство имеет в своем составе мартеновские печи, двухванные сталеплавильные агрегаты, дуговые электросталеплавильные печи и конверторы. Несмотря на различную технологию выплавки стали в перечисленных агрегатах, им присущи общие источники выбросов: шихтовые отделения, отделения подготовки изложниц, миксеры и выбросы, образующиеся в процессе транспортировки готового продукта. Выбросы, образующиеся в результате протекания технологического процесса в этих агрегатах, различаются по количеству и качеству.
Газы, образующиеся в мартеновских печах и двухванных сталеплавильных агрегатах, имеют в своем составе пыль и такие химические компоненты, как окислы углерода, серы и азота. В основном все мартеновские печи и двухванные сталеплавильные агрегаты оборудованы системами очистки газов. После очистки технологические газы выбрасываются через дымовую трубу в атмосферу. В некоторых случаях, особенно при продувке мартеновских печей кислородом, часть технологических выбросов поступает в помещение цеха через завалочные окна и выбрасывается через фонарные проемы в атмосферу. Это связано как с недостаточной мощностью тягодутьевых машин газоочистных сооружений, так и технологией производства. В силу специфики выплавки стали в двухванных сталеплавильных агрегатах количество выбросов от этих агрегатов еще больше- Вопросы снижения технологических выбросов от двухванных сталеплавильных агрегатов должны решаться путем не только увеличения производительности тягодутьевых машин газоочистиых сооружений, но и разработки мероприятий по уплотнению завалочных окон (например, аэрозавесами) и газового тракта, а также внедрения рационального режима ведения плавки в агрегате.
Электросталеплавильные печи характеризуются большим количеством технологических выбросов. Особенностью плавки в дуговых электросталеплавильных печах является применение электрической дуги, которая производит местный нагрев металла до высоких температур с образованием большого количества пыли. Кроме пыли, образуются и выбрасываются с технологическими газами такие химические вредности, как окислы углерода и азота. В последнее время для получения стали высокого качества используются индукционные печи и печи электрошлакового переплава (ЭШП). Эти агрегаты также являются источниками пылевых и химически вредных выбросов в виде окиси углерода, фтористых соединений и др.
Местами технологических выбросов из дуговой электросталеплавильной печи являются завалочное окно, электродные зазоры и фурменные отверстия в своде, неплотности песчаных затворов сводового кольца, сливной носок и др. При сливе металла, механизированной заправке подины и особенно при завалке промасленной стружки в печь образуется большое количество неорганизованных выбросов, которые через фонарные проемы выбрасываются в атмосферу без очистки.
Количество вредных выбросов в электросталеплавильном производстве можно снизить существенно путем правильной организации отсоса газов из печи, устройства надежно работающих уплотнителей электродных зазоров и фурменных отверстий, оптимального ведения технологического процесса, выбора рационального способа подачи кислорода в печь и т. д. [4, 5].
Конверторное производство стали характеризуется высокой интенсивностью протекания технологического процесса и высокой производительностью агрегата. Жидкий чугун, заливаемый в конвертор, продувают кислородом. Большой удельный расход кислорода (до 5— 6 м3/мин) обусловливает высокую . скорость окисления углерода. При этом образуются пылегазовые потоки, которые через горловину конвертора отсасываются в газоочистительную установку.
В настоящее время существует три способа отвода газов от конверторов: с полным дожиганием, частичным дожиганием и без дожигания окиси углерода. При отводе газов без дожигания окиси углерода количество их перед газоочисткой в несколько раз ниже, чем при отводе газов с полным и частичным дожиганием. С целью сокращения выбросов окиси углерода в атмосферу при отводе газов без дожигания их после очистки от пыли направляют либо в специальное устройство для дожигания
СО, либо в газгольдеры для последующего использования в качестве топлива.
Неорганизованные выбросы пыли и газов при конверторном производстве стали образуются в разливочном пролете, в пролетах сушки и ремонта конверторов, миксерном отделении и на дворе изложниц; они удаляются в атмосферу через аспирационные и вентиляционные системы.
Прокатное производство также характеризуется организованными и неорганизованными вредными выбросами. К источникам организованных выбросов относятся нагревательные колодцы и печи, закрытые колпаковые и отжиговые печи, машины огневой зачистки слябов. Источниками неорганизованных выбросов являются нагревательные колодцы во время открывания крышек, рабочие клети, ножницы для резки металла, огневая и механическая зачистка заготовок, травильные ванны и т. д.
Резкое уменьшение выбросов от прокатного производства может быть обеспечено путем сокращения времени открывания нагревательных колодцев и печей, применения малосернистого топлива, более полного сжигания окиси углерода, уплотнения и укрывания машин огневой зачистки и травильных ванн.
Ферросплавное производство характеризуется высокой температурой протекания технологического процесса и выделением большого количества пыли и газов. По методу получения готового продукта и характеристике выбросов все ферросплавы можно подразделить на три основные группы [6]:1) ферросплавы, выплавляемые в рудовосстановительных электропечах (ферросилиций, ферромарганец, феррохром и т. д.); 2) ферросплавы, выплавляемые в рафинировочных печах (малоуглеродистый и безуглеродистый ферромарганец, феррохром и т.д.); 3) ферросплавы, получаемые алюмосиликотермическим способом в плавильных шахтах (феррохром, ферротитан и др.).
Открытые и закрытые рудовосстановительные печи имеют существенное различие по составу и количеству технологических выбросов. Закрытые печи имеют зонт и вытяжку для удаления продуктов сгорания. Как правило, все печи этого типа оборудуются газоочистками, поэтому поступление выбросов в атмосферу от этих печей ограниченно. Открытые печи оборудуются вытяжными шахтами, через которые продукты сгорания как с предварительной очисткой, так и без нее выбрасываются в атмосферу. В зависимости от этого шахты работают с естественной и принудительной вытяжкой.
Рафинировочные трехфазные печи (рафинировочные и восстановительные) имеют специальные шторы, уменьшающие подсос атмосферного воздуха, а следовательно, и объем отсасываемых газов. Плавильные шахты оборудованы вытяжками, через которые удаляются технологические газы.
В ферросплавном производстве источниками неорганизованных выбросов являются места слива готового продукта в ковши, разливочные машины, шихтовые отделения, дробилки, питатели, транспортеры. Эти источники выбросов оборудуются системами вытяжной вентиляции с очисткой газов от пыли.
Огнеупорное производство относится к производству, выделяющему большое количество пыли. Значительная доля технологических выбросов происходит при обжиге глины, магнезита, доломита во вращающихся печах и сушке глины в сушильных барабанах. Сушильные барабаны и вращающиеся печи оборудованы системами отсоса газов с их очисткой перед выбросом в атмосферу, плавленый магнезит получают в трехэлектродных дубовых открытых печах. В зависимости от режима работы печи (с подсосом или без подсоса воздуха) количество выбросов при производстве плавленого магнезита значительно колеблется. Вредные выбросы происходят также при обжиге огнеупорных изделий и при сушке огнеупорных материалов в печных агрегатах. Источниками неорганизованных выбросов являются в основном процессы транспортировки и переработки исходного материала.
Для снижения технологических выбросов в огнеупорном производстве необходимо поддерживать оптимальный тепловой режим работы печей, поддерживать оптимальные скорости газов в рабочем пространстве сушильных барабанов, применять бессернистое топливо, создавать системы с рециркуляцией технологических газов, обеспечивать максимальное уплотнение печей.