Молибден
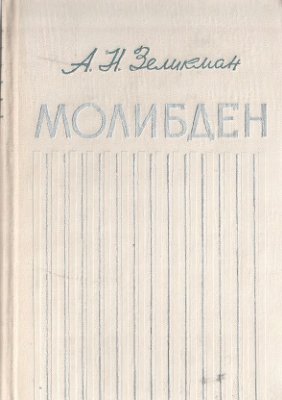
Зеликман А.Н.
Металлургия, 1970 г.
ПЛАВКА МОЛИБДЕНА
Для получения крупных заготовок молибдена массой 500— 2000 кг, необходимых для прокатки листов большого размера, вытяжки труб и других изделий, к началу 50-х годов была разработана и получила распространение в промышленной практике дуговая плавка молибдена с расходуемым электродом, и примерно 10 лет спустя — электронно-лучевая плавка.
Теория дуговой и электронно-лучевой плавок и конструктивные варианты плавильных агрегатов освещены в специальных монографиях [25, 36, 38].
ДУГОВАЯ ПЛАВКА
Конструкция печей и режимы плавки
В современных дуговых печах металл плавится в дуге, возникающей между верхним (расходуемым) электродом и нижним электродом — расплавленным металлом, находящимся в охлаждаемой медной изложнице (кристаллизаторе) (рис. 141). Вследствие высокой теплопроводности меди и быстрого отвода тепла водой, поступающей в рубашку кристаллизатора, жидкий металл, соприкасаясь со стенкой, быстро затвердевает и плавка фактически идет в гарниссаже из молибдена. Это исключает загрязнение молибдена медью. Плавку молибдена большей частью ведут на постоянном токе при полярности: расходуемый электрод — катод, расплав — анод. Для выпрямления тока служат мотор-генераторы или мощные селеновые, германиевые или кремниевые выпрямители. Обратная полярность (положительный верхний электрод) связана с большей вероятностью переброса дуги на стенку кристаллизатора. Это может вызвать прожог стенки или ее частичное разъедание.
Молибден можно плавить также и в дуге переменного тока. При работе на постоянном токе температура катода существенно не меняется во времени, что обеспечивает постоянство эмиссии электронов. Между тем из-за синусоидальной формы кривой переменного тока температура катода во времени изменяется. Однако при плавке наиболее тугоплавких металлов (W, Та, Мо) при определенной плотности тока дуга достаточно стабильна, что объясняется сохранением на электродах высокой температуры, необходимой для поддержания дугового разряда. [25, 40].
Наиболее распространены печи, в которых электрод предварительно изготовляют из спеченных молибденовых штабиков. Стыковой сваркой штабики соединяют в прутки длиной 1—2,5 м. Затем их связывают в пакет (4—16 прутков и больше в зависимости от сечения штабиков и диаметра кристаллизатора) [34; 29, с. 65].
Электроды могут быть также изготовлены спеканием спрессованных цилиндрических брикетов небольшой высоты в печах с использованием индукционного нагрева. Затем брикеты соединяют в электрод.
Расходуемый электрод перемещают при плавке и подводят к нему ток с помощью охлаждаемого штока, на конце* которого закреплен электрод (рис. 141), для подвода тока и перемещения электрода применяют также ролики (рис. 142).
Плавку ведут с глухим кристаллизатором (рис. 141) или с вытягиванием слитка, путем опускания поддона (рис. 142). Плавка с вытягиванием слитка обеспечивает лучшую откачку выделяющихся газов, так как зона дуги в этом случае все время находится в верхней части кристаллизатора, тогда как при плавке с глухим кристаллизатором газы откачиваются из глубокого кольцевого зазора между электродом и стенками кристаллизатора.
Перед плавкой на дно кристаллизатора кладут молибденовый диск. После создания в печи вакуума (10-3—10-4мм рт. ст.) электрод опускают для зажигания дуги.
В США в 1950 г. в результате работ, проводившихся с 1943 г., создана сложная плавильная установка, в которой электрод из молибденового порошка прессуют и спекают непосредственно в плавильной камере печи (рис. 143). Конструкция и работа установки УПСП детально описаны в работах [39, 41].
Электрод шестигранной формы прессуют слоями высотой от 6 до 30 мм с помощью гидравлической системы в пресс-форме сложной конструкции. Спрессованный электрод проходит между скользящими контактами (один из них расположен непосредственно под пресс-формой) и спекается прямым пропусканием тока, приобретая достаточную прочность, чтобы выдержать массу электрода длиной до 1,5 м.
Наиболее сложная часть установки — механизм формования электрода. Шестигранная пресс-форма состоит из шести пластин, из которых три могут реверсивно перемещаться в стальном блоке на расстояние до 1,5 мм, что регулируется горизонтальным гидравлическим цилиндром. Когда в процессе прессования давление в вертикальном цилиндре повышается (вследствие сопротивления прессуемого столбика) до заданного значения, давление в горизонтальном цилиндре снижается и брикет перемещается вниз до полного хода плунжера. Таким образом, скорость подачи электрода на плавление непосредственно связана с толщиной прессуемого брикета. Полный цикл прессования брикета длится 3 сек9 за минуту прессуется 20 брикетов.
Дуга установки УПСП работает на переменном токе. Для зажигания дуги на дно кристаллизатора укладывают в форме конуса молибденовую стружку. При соприкосновении электрода со стружкой возникает короткое замыкание, нагревающее верхний слой стружки и конец электрода до температуры плавления. В образующемся зазоре возникает дуга, которая далее горит непрерывно на протяжении всей плавки.
В плавильном агрегате подобного типа выплавляют слитки молибдена диаметром до 305 мм и массой 910 кгсо скоростью 7,3— 9,1 кг/мин.
Описанная установка весьма сложна, так как все ее части должны быть смонтированы в вакуумной камере и все операции (прессование, спекание, плавка) должны быть строго синхронизированы. Так как в УПСП предусмотрено движение электрода только вниз, подъем электрода, если дуга не загорелась, невозможен. Это требует сложной системы автоматического управления, обеспечивающей зажигание дуги и непрерывность ее горения в процессе плавки.