Микроплазменная сварка
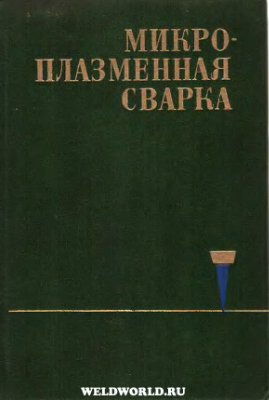
Патон Б.Е.
Наукова думка, 1979 г.
ПРИМЕНЕНИЕ МИКРОПЛАЗМЕННОЙ СВАРКИ
Микроплазменная сварка в непрерывном и импульсном режимах горения дуги нашла широкое применение во многих отраслях промышленности для изготовления различных изделий из черных и цветных металлов и сплавов малых толщин. Накоплен опыт использования данного способа при исправлении микродефектов в окончательно обработанных деталях из углеродистых и легированных сталей, а также из литейных алюминиевых сплавов. Ниже приведены характерные примеры применения микроплазменной сварки в приборостроительной, машиностроительной и электротехнической промышленности, в электронной и медицинской технике, химическом машиностроении и радиотехнике.
1. СВАРКА КОРПУСОВ ПРИБОРОВ
Наиболее распространена микроплазменная сварка при изготовлении тонкостенных корпусов приборов различного назначения. Это полупроводниковые элементы, конденсаторы, интегральные схемы, теплообменники, вакуумные датчики, реле, сопротивления, узлы электронных ламп, сильфонные узлы и фильтры. С помощью микроплазменной сварки изготовляют дроссели люминесцентных ламп, бытовые приборы, корпуса электрокофеварок и другие предметы народного потребления. Размеры изделий, свариваемых микроплазменным способом, находятся в пределах от 5—10 мм (рис. 121) до нескольких десятков метров при толщине металла 0,05—2,0 мм.
На рис. 122 приведен малогабаритный корпус теплообменника, состоящий из двух трубных досок размером 1*50*50 мм (сталь Х18Н10Т) и 36 капилляров диаметром 3 мм, длиной 65 мм и толщиной стенки 0,13 мм. Приварку капилляров к трубной доске выполняют от источника А-1255 горелкой ОБ-1115 на следующем режиме: Iсв=4,3 А; Iд.д=1,2 А; расход защитного газа (Аr+ 3% Н2) 3 л/мин; плазмообразующего (Аr) —0,25 л/мин. Как показал опыт, микроплазменная сварка в данном случае обеспечивает сохранение точных геометрических размеров корпусов теплообменников, высокую плотность сварных соединений и качественное формирование швов.
Освоена автоматическая микроплазменная сварка малогабаритных баллонов из тонколистовой стали (δ =0,5 мм) с продольными и кольцевыми швами. Применительно к изготовлению такого рода баллонов ручная газовая сварка вследствие низкой производительности, значительных деформаций и образования дефектов не удовлетворяла требованиям серийного производства. С целью использования микроплазменной сварки для данных изделий произведены конструктивные изменения в сопряжениях свариваемых элементов. В заготовке цилиндра баллона с двух сторон предусмотрены технологические припуски в виде усиков, что гарантирует необходимую точность стыковки деталей за счет увеличения времени на начало процесса сварки. Заварку кратера в конце шва также выполняют на технологическом усике. Сварку осуществляют специализированным автоматом на медной формирующей оправке с использованием пневмоклавишного прижима. Цилиндр фиксируют в таком положении, при котором его образующая совпадает с электродом сварочной горелки, установленной на подвижной каретке и перемещающейся по направляющей между двумя конечными выключателями.
Приварку крышки к цилиндру кольцевым швом производят на другой установке. Она состоит из двух основных узлов — вращающейся пневмоцанги и поворотной колонны с корректирующим устройством и горелкой. Конструктивно узел цанги решен так, что при зажатии медные вкладыши устанавливаются в одной плоскости со свариваемыми кромками деталей. Благодаря равномерному отбору тепла в процессе сварки удается избежать прожогов и других дефектов в швах.
В качестве источника питаниям данном случае применяют установки МПУ-М, работающие как в импульсном, так и в непрерывном режиме горения дуги. Оптимальные режимы механизированной микроплазменной сварки стали 08кп толщиной 0,5 мм приведены в табл. 29. При замене газовой сварки микроплазменной увеличилась производительность труда, улучшились его санитарно-гигиенические условия и повысилось качество сварных соединений.
Разработаны и внедрены в производство сварные трубчатые корпуса фильтров, служащих для получения чистого водорода методом диффузии водородсодержащего газа через ячейки с палладиевыми мембранами (рис. 123). В данном изделии мембраны, изготовленные из фольги толщиной 0,1 мм (80% Pd, 15% Ag, 5% Pt)» сваривают в самостоятельные ячейки, а затем несколько ячеек собирают в отдельный корпус. Микроплазменную сварку ячеек и корпусов выполняют в импульсном режиме горения дуги. Защитным газом служит аргоно-водородная смесь с 3% водорода. Сварные узлы водородных фильтров допускают надежную работу аппаратов при температурах до 650° С. Для сравнения отметим, что аналогичные паяные узлы при температурах свыше 500° С оказываются неработоспособными. Переход от пайки к микроплазменной сварке фильтров позволил увеличить производительность промышленных диффузионных установок и повысить их эксплуатационную надежность. Одновременно достигнута также значительная экономия благородных металлов.
Сварку узлов большинства электровакуумных приборов необходимо производить при пониженном давлении окружающей атмосферы, поскольку данные узлы после сварки подвергаются вакуумированию. Качество приборов такого типа в значительной мере зависит от постоянства давления среды внутри прибора в течение продолжительного промежутка времени. Если сварные швы насыщены газами или окислены, то в процессе эксплуатации давление внутри прибора увеличивается, что отрицательно сказывается на работоспособности изделия. Например, в вакуумных конденсаторах это приводит к снижению электрической прочности сварных соединений вплоть до выхода его из строя. Микроплазменная сварка при давлениях среды 10~2—10~3 мм рт. ст. обеспечивает высокое качество соединений. Чистота атмосферы, окружающей сварочную ванну, в этом случае определяется в основном чистотой плазмообразующего газа.
Характерным примером применения микроплазменной сварки в вакууме является использование ее при изготовлении вакуумных конденсаторов [77]. Схема соединения (рис. 124), предусматривающая сочетание наружных технологических колец с выступом и проточкой на массивном основании и втулке, обеспечила оптимальные условия нагрева соединений деталей, обладающих резко отличающимися теплофизическими свойствами. При этом технологическое кольцо служит одновременно и присадочным материалом, способствующим получению вакуумноплотных соединений. Сварку указанного корпуса производят специализированным источником питания ΙΟΧ-306 с плазмотроном А-1092К при преимущественном расплавлении технологического кольца из меди или бронзы.
Другим примером изделий, требующих вакуумирования в процессе сварки, являются стальные корпуса датчиков (рис. 125). Давление внутри корпуса должно составлять десятые доли миллиметра ртутного столба, что и предопределяет использование для герметизации узлов импульсной дуги низкого давления. Особенностью техники сварки такого рода изделий является применение дуги большой длины для обеспечения необходимого давления внутри корпуса. Последующие испытания сварных узлов и опыт их эксплуатации свидетельствуют о высоком качестве герметизации, удовлетворяющей техническим требованиям. Аналогичные результаты получены также при микроплазменной сварке в вакууме термостатов датчиков, корпусов электроннолучевых приборов и других изделий.