Металлургия титана
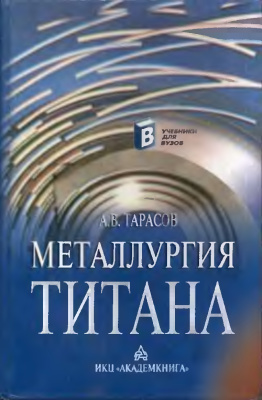
Тарасов А.В.
Академкнига, 2003 г.
ПЛАВКА И ЛИТЬЕ ТИТАНА И СПЛАВОВ НА ЕГО ОСНОВЕ
Общие сведения
Высокая реакционная способность, склонность к активному химическому взаимодействию с кислородом, азотом, углеродом и другими элементами не позволяют плавить титан и его сплавы в обычных металлургических печах. Плавку титана необходимо производить в условиях, предохраняющих жидкий металл от насыщения газами и другими вредными примесями. Технически чистый титан имеет сравнительно низкую прочность, поэтому в промышленности используют главным образом сплавы титана.
Высокая температура плавления титана (~ 1670 °С) в сочетании с высокой химической активностью создает большие трудности при плавке и литье сплавов на основе титана. Чтобы титан не стал хрупким в результате загрязнения газами, плавку и литье проводят в высоком вакууме или н атмосфере инертного газа высокой чистоты, а также не допускают соприкосновения металла с огнеупорными материалами. В настоящее время разработано несколько методов получения титана, предотвращающих загрязнение металла газами или огнеупорными материалами: 1) вакуумная дуговая плавка; 2) плавка в печи с гарниссажем; 3) плавка в электрошлаковой печи; 4) плазменно-дуговая плавка; 5) индукционная плавка в графитовом тигле. Для всех видов плавок, за исключением индукционной, при плавлении титана применяют для формирования слитка медный водохлаждасмый кристаллизатор, а при гарниссажной плавке — также графитовый тигель. Вакуумная дуговая плавка в настоящее время является основным методом получения титана.
В электрошлаковой плавке источником нагрева служит джоулево тепло, выделяющееся при прохождении тока через слой флюса (фторида кальция), который является элементом сопротивления. Процесс осуществляется по схеме расходуемого электрода. При этой плавке параметры плавления легко регулируются, поверхность слитков получается такой, что их можно использовать для дальнейших переделов без обточки. Кроме того, можно получать слитки плоского и квадратного сечения, что очень удобно для прокатки.
Способ плазменно-луговой плавки позволяет переплавить сыпучую шихту с добавкой любого количества отходов. Источником тепла в этом процессе служит поток ионизированного газа-плазмы, подаваемого в зону плавки специальными устройствами — плазмотронами. При плазменной плавке, которая может осуществляться также и по схеме расходуемого электрода, повышается безопасность процесса, поверхность слитков лучше, чем при дуговой плавке.
Способ индукционной плавки предусматривает использование главным образом графитового тигля, при этом весь переплавляемый металл находится в расплавленном виде в отличие, например, от вакуумно-дуговой плавки, когда формирование слитка из жидкой ванны металла в медном водоохлаждаемом кристаллизаторе идет постепенно.
Плотный графит является одним из тех немногих веществ, которые выдерживают действие жидкого титана. В результате реакций между графитом и расплавленным титаном на поверхности графита образуется слой стойкого карбида титана, который предотвращает непосредственное соприкосновение расплавленного металла с графитом. Поскольку углерод переходит в титан только в результате диффузии через слой карбида, растворение углерода в расплавленном титане происходит медленно. При использовании в качестве тигля огнеупорных материалов титан сильно ими загрязняется.
Способ гарниссажной плавки позволяет наплавлять жидкий металл сразу на весь слиток, фасонную отливку или заготовку, например расходуемый электрод для второго переплава. Эта плавка характеризуется наличием на внутренней поверхности плавильного тигля слоя твердого гитана или «г арниссажа», с которым соприкасается расплавленный металл. При плавке весь металл расплавляется электрической дугой в металлическом или графитном тигле с титановым «гарниссажем», откуда жидкий титан сливается в форму, а парниссаж либо отделяют от металлического тигля и используют как расходуемый электрод при последующей плавке, либо оставляют (например, в графитовом тигле) для защиты от загрязнения углеродом очередных плавок титана. Способ гарниссажной плавки позволяет переплавлять любое количество отходов, получаемый металл имеет высокую однородность, тугоплавкие включения «вмерзают» в гарниссаж и не переходят в слиток.
Кроме перечисленных, испытаны и находятся в разработке новые методы плавки, которые рассмотрены ниже.
Плавка в вакуумно-дуговых печах
Наибольшее распространение получила технология производства слитков, включающая приготовление шихты, прессование расходуемого электрода, первую вакуумно-дуговую плавку в водоохлаждаемом кристаллизаторе, вторую вакуумно-дуговую плавку в кристаллизаторе большего диаметра, механическую обработку слитков, контроль химического состава, механических свойств и наличия внутренних дефектов.
Шихта (смесь титановой губки, легирующих компонентов и оборотных отходов в заданных количествах) после усреднения формируется в расходуемые электроды на специальных прессах горизонтального или вертикального типа. Наилучшие результаты дает непрерывный метод прессования на вертикальных прессах, который обеспечивает получение более однородного в поперечном сечении и достаточно длинного электрода. Возможно получение расходуемых электродов диаметром 350-650 мм.
Первый и второй переплавы осуществляются в одинаковых по конструкции печах, различающихся только размерами кристаллизатора и источниками тока. Применяемые по настояшее премя в промышленности печи позволяют получать слитки первого переплава диаметром 560— 850 мм. длиной 2000-2600 мм и массой 2500-5000 кг. Диаметр слитков второго переплава — 650—950 мм, масса — 2500—10000 кг: Для первого переплава используют источники с силой тока 25 кА, для второго — 37 кА. Тенденция развития плавильною производства заключается п увеличении массы слитков до 5—8 т. Существенный недостаток этой технологии
ограниченная возможность ввода титановых сплавов в шихту (~30%). Вовлечение отходов в большем объеме уменьшает прочность расходуемых электродов и создает опасность их разрушения при транспортировке и плавке. Некоторые печные агрегаты позволяют при планке с расходуемым электродом периодически добавлять кусковые отходы из бункера.
Высокая активноесть титана по отношению к кислороду и азоту воздуха, а также практически ко всем огнеупорным материалам, обусловила создание специальной вакуумной плавки для получения слитков.
Наиболее приемлемой оказалась плавка дугой в металлической охлаждаемой форме — кристаллизаторе. В процессе плавления на поверхности кристаллизатора образуется слой твердого металла, который не взаимодействует с материалом формы. Довольно широкое распространение получила дуговая вакуумная плавка с нерасходуемым электродом. В качестве последнего использовали вольфрам или графит. Однако и этот способ плавки оказался непригоден вследствие загрязнения переплавляемого металла материалом электрода. Тогда начали применять расходуемый электрод из титановой губки.
Современная технологическая схема производства слитков титановых сплавов включает следующие основные операции: подготовку шихты, прессование расходуемых электродов, первый переплав, обработку слитков первого переплава, второй переплав, механическую обработку слитков, контроль их качества.
Шихта для плавки слитков состоит из губчатого титана, лигатур и легирующих элементов в чистом виде, отходов. Свойства губчатого титана подробно рассмотрены в предыдущих главах.
Введение легирующих элементов в чистом виде или в виде лигатур определяется, в основном, возможностью их растворения в металле в процессе плавки. Лигатуры выбирают так, чтобы их температура плавления и плотность в наибольшей степени были близки к этим показателям титана.
В чистом виде применяют следующие легирующие компоненты титановых сплавов: алюминий, марганеп, цирконий, железо, кремний, иногда хром. Ванадий, молибден вводят в виде лигатур с апюминием. Применяют также комплексные лигатуры, например, для выплавки сплава ВТЗ-1. который содержит в соответствующей пропорции и другие легирующие элементы (Cr. Fe и лр.). Эти лигатуры получают алюминотермическим способом. Олово вводят в виде лигатуры Al-Sn, которую изготовляют сплавлением чистых компонентов в индукционных печах.
Перел использованием в шихте легирующие компоненты измельчают. хрупкие металлы и лигатуры (Сr-Мn, Al-Mo, A1-V и др.) дробя г на щековых или молотковых дробилках. Слитки (чушки) алюминия и лигатуры Al-Sn переводят стружку на строгальных станках.
В шихте используют следующие виды отходов: листовую обрезь, кусковые отходы от копаных или прессованных изделий, стружку. Предварительно отходы необходимо измельчить и удалить с их поверхности слой, содержащий повышенное количество газовых примесей. Для этого листовые отходы предварительно травят, измельчают на механических ножницах и эксцентриковых прессах до размеров 60x50 мм и затем обезжиривают. Кусковые отходы куют и рубят в нагретом состоянии на куски размером не более 60x60x80 мм, а затем очищают в галтовочных барабанах для удаления слоя оксидов.
При плавке используют стружку без видимых цветов побежалости. Стружку дробят до размеров <70 мм и подвергают магнитной сепарации для удаления осколков твердосплавных резцов, которые попадают в стружку при токарной обработке титановых сплавов и, не расплавившись, могут образовать в слитке инородные включения.
При шихтовке сплавов рассчитывают навески легирующих компонентов и необходимую твердость губчатого титана, обеспечивающую требуемую прочность сплава. Расчет навесок легирующих компонентой, в соответствии с их содержанием в сплавах, производят с учетом их поступления из отходов и угара при плавке.
Для получения расходуемых электродов применяют порционное прессование в проходную коническую матрицу круглого сечении. Прессование ведут на мощных горизонтальных или вершкальных гидравлических прессах. Применение вертикальных прессов предпочтительнее, так как в этом случае распределение компонентов шихты по горизонтальному и вертикальному сечению электродов более равномерное. Шихту засыпают из бункера по шихтопроволу в лоток-приемник шихты. Пресс-штемпель (пуансон) посредством пресс-шайбы (надставки) толкает шихту в конусную матрицу, которая установлена в направляющей втулке. Порция шихты спрессовывается, пресс-штемпель отводят в исходное положение, и загружают очередную порцию шихты. Для уменьшения усилий прессования матрица подогревается до 250—300 °С. Для того, чтобы порции шихты в электроде соединялись между собой, предусмотрена фигурная поверхность торца пресс-шайбы.
Одно из основных условий получения прочного электрода — достижение достаточною удельного давления прессования — 29,4-34.3 кН/см2, а в конце цикла прессования — не менее 13.7 кН/см2.
Состав каждой порции прессования по соотношению компонентов должен соответствовать расчетному составу шихты. Размер порции определяется диаметром прессуемою электрода. Расчетами и на практике установлено, что масса порции не должна быть больше 1/2 массы ванны жидкого металла при плавке слитка первого переплава.