Металлургические шлаки
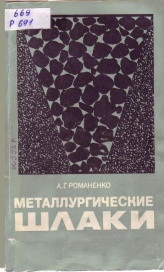
Романенко А.Г.
Металлургия, 1997 г.
СТАЛЕПЛАВИЛЬНЫЕ ШЛАКИ
Состав и свойства сталеплавильных шлаков определяются их ролью в процессах передела. Шлаки передают тепло от газовой фазы к металлической и питают ванну металла кислородом (регулируя ход процесса в сторону окисления или восстановления); защищают металл от поглощения азота и водорода и рафинируют его от вредных примесей (серы и фосфора); наконец, они должны сводить к минимуму угар и механические потери металла.
Формирование шлака и его конечный состав зависят от способа и характера передела (кислый или основной). Передел чугуна в сталь заключается в окислении содержащихся в нем примесей. При этом неизбежно окисляется и часть железа. Окислы элементов, флюсы и разрушающаяся футеровка печи, соединяясь между собою, образуют неметаллическую фазу —шлак.
В нем растворяются загрязняющие примеси шихты (песок, глина, ржавчина, доменный и миксерные шлаки).
В сталеплавильных шлаках всегда есть железо в виде окислов (до 24%) и в металлической форме (до 20%), а также МnО (до 11%). Наличие металла в шлаках не только снижает выход стали, но и заметно усложняет переработку шлаков.
В результате окисления и рафинирования металла, а также разъедания кладки в шлаках появляются окислы и сульфиды: SiO2, Al2O3, СаО, МgО, Cr2O3, Р2О5, FeО, МnО, FeS, MnS и др.
Использование сталеплавильных шлаков для получения строительных материалов и удобрений зависит от их химического и минералогического состава и физикомеханических свойств.
Мартеновские шлаки по характеру процесса (определяемого основной или кислой футеровкой пода печи) подразделяются на основные и кислые. Объем производства стали кислым процессом относительно невелик, поэтому в дальнейшем преимущественно будем рассматривать основные шлаки, Более чем наполовину эти шлаки состоят из основных окислов. СаО, МgО, FeО, МnО. Мартеновский шлак характеризуется основностью, т. е. отношением СаО: SiO2. Еcли СаО : SiO2<1, то шлаки считают низкоосновными. Шлаки средней основности имеют СаО : SiO2= 1,6-2,5. При СаО : SiO2>2,5 шлаки называют высокоосновными.
При переделе высокофосфористых чугунов в шлаках содержится повышенное количество Р2O5. В этом случае критерием основности шлака является отношение
СаO:(SiO2+P2O5).
Кислые шлаки состоят главным образом из SiO2 (50—65%) и некоторого количества таких основных окислов, как FеО (10—20%) и МnО (10—30%). Их кислотность выражается отношением SiO2 : (FеО+МnО). Если в кислых шлаках содержится 3—15% СаО, то их кислотность выражается отношением SiO2: (FеО+МnО+CaO). Мартеновские шлаки подразделяют на первичные и конечные (вторичные). Количество первичных шлаков колеблется от 50 до 70, вторичных — от 30 до 50%.
Мартеновские шлаки отличаются широким диапазоном колебаний состава в зависимости от марок стали и периодов плавки. Первичные шлаки имеют основность от 1 до 2 , конечные от 2 до 4.
Отличительная способность шлаков мартеновского производства —высокое содержание окислов железа (до 25%) и наличие (2—3%) Р2О5. Шлаки фосфористого передела завода «Азовсталь» содержат до 18—20% Р2О5. Наиболее характерные составы мартеновских шлаков представлены в табл. 4.
Минералогический состав мартеновских шлаков довольно сложен. Петрографический анализ мартеновских шлаков Ждановского завода имени Ильича, выполненный А. В. Запольский и А. М. Черезовой ДУралНИИЧМ), показал, что структура шлака неравномерно зернистая с размером зерен от 8 до 200 мкм. В шлаке преобладает мервинит в виде крупных призматических и чечевицеобразных зерен размерами 100—200 мкм (в количестве 42%).
Ферритная фаза представляет твердый раствор ферритной и алюмоферритной фаз, в которой наблюдаются вростки RО-фазы (твердых растворов свободных окислов МgО, МnО, FeО). Содержание ферритной фазы и RО-фазы составляет 29%. В исследуемой пробе наблюдались единичные выделения бурого цвета размером до 4 мкм с нечеткими размытыми краями — псевдоморфоза с включениями СаО. Включения, по-видимому, более высококоосновные, чем основная масса и представлены трехкальциевым cиликатом, алюмоферритной фазой и периклазом.
Важной характеристикой мартеновских шлаков является их вязкость. При температуре 1600° С вязкость жидких шлаков составляет 0,2—0,4 П, густых — выше 2 П. Повышение степени перегрева шлаков повышает его жидкотекучесть. Вязкость шлака возрастает с повышением его основности. Минимальную вязкость мартеновский шлак имеет при основности 2,1—2,3. Вязкость шлака зависит также от содержания Сr2O3, МgО и А12O3. Большая вязкость шлаков, содержащих Сr2O3, объясняется образованием в них хромитов железа Fe(Сr2O3)2, имеющих температуру плавления 1900—2000° С. Присутствие малорастворимой в шлаке МgО повышает гетерогенность шлака и, следовательно, увеличивает его вязкость. А12O3 заметно понижает вязкость. Для разжижения основных шлаков в них добавляют боксит, содержащий 40—60% А12O3; бой шамотного кирпича, содержащий 36—42% А12O3 и 55—60% SiO2; плавиковый шпат; в некоторых случаях — песок, содержащий до 98% SiO2.
Мартеновские шлаки, как правило, устойчивы против силикатного распада. Однако в высокоосновных мартеновских шлаках встречаются модификации γ-ортосиликата кальция и свободная известь, которые вызывают их растрескивание и самораспад. Эти явления особенно опасны при использовании щебня из мартеновских шлаков в бетонах и асфальтобетонах. Локализация разрушающего действия этих соединений достигается обработкой шлака паром в закрытых емкостях в течение 2—3 ч или длительной выдержкой шлака на воздухе — в течение не менее двух месяцев.
Конверторные шлаки по химическому составу близки к мартеновским шлакам, отличаясь несколько большей степенью основности. Удельный выход конверторных шлаков на 1 т стали колеблется в широком диапазоне (50—245 кг/т). В среднем по СССР удельный выход шлака конверторной плавки составляет 149— 150 кг/т.
При содержании в чугуне до 0,15% Р конверторную плавку ведут с одним шлаком и при содержании Р от 0,15 до 0,30% работают с двумя шлаками, т. е. с промежуточным сливом шлака в процессе продувки.
В кислородном конверторе интенсивно окисляются примеси чугуна. Образующееся окислы с известью и другими сыпучими материалами, загружаемыми в конвертор, формируют шлак. К концу продувки отношение СаО:5Ю2 в шлаке > 2,5.
При выпуске стали в сталеразливочный ковш сливают также небольшое количество шлака, предохраняющего металл от охлаждения. Оставшийся шлак сливают через горловину конвертора в шлаковую чашу.
Минералогический состав конверторных шлаков значительно различается в зависимости от характера процесса. Бессемеровские шлаки состоят главным образом из β-кристобаллита и бурого стекла, встречается родонит МnSiO3. Томасовские шлаки включают силикокарнотит, томасит, нагельшмитит, стэдит, шпинель и двухкальциевый феррит.
Шлаки кислородно-конверторной плавки представляют сложный многокомпонентный сплав, минералогический состав которого определяется маркой выплавляемой стали и, следовательно, химическим составом шлака, а также особенностями технологического процесса.
А. В. Запольской и А. М. Черезовой выполнено петрографическое исследование конверторных шлаков завода имени Ильича, имеющих отношение СаО:$Ю2= =8,3. Структура шлака равномерно зернистая. Выделившиеся в первую очередь призматические зерна трех- кальциевого силиката размером до 400 мкм по краям окружены двухкальциевым силикатом в виде призматических полисинтетически сдвойниковакных зерен размером до 100 мкм. К зернам двухкальциевого силиката примыкают округлые зерна периклаза. Промежутки между зернами периклаза, трех- и двухкальциевого силиката заполнены ферритной фазой.
Конверторные шлаки НЛМЗ содержат 75—80% ортосиликата кальция, КО-фазы и ферритной фазы. В шлаках с высоким содержанием СаО встречаются трехкальциевый силикат и свободная известь.
Составы электросталеплавильных шлаков более разнообразны в сравнении с мартеновскими и конверторными шлаками, В процессе плавки в электропечи окисляются составляющие шихты, происходит формирование шлака и переход в него фосфора. Наряду с окислами (FeO, МnО, SiO2) в шлак переходит известь, загружаемая в электропечь в несколько приемов. В шлаке образуется окисел фосфора - продукт дефосфорации металла. К концу периода плавления шихты в электропечи шлаки имеют следующим состав, %: 32-44 CaO, 16—25 SiO2, 8—14 МgO, 6—10 МnО, 10—14 FeО и 0,6—1,2 Р2О5. Во избежание обратного перехода фосфора из шлака в металл больше половины шлака сливают и затем наводят новый шлак, загружая известь и, при необходимости, плавиковый шпат и бой шамотного кирпича.